Dust and chips resulting from processing of wood and wood-based panels have always been a problem. Whether it's a factory or a small workshop, the result of machining is sawdust and dust that has to be got rid of. So, willy-nilly, everyone installs filter exhaust systems. There was a time when I used to drive around the country looking for customers for lakes, and I'd see wood-processing factories far and wide looking for exhausters. All these systems are energy-intensive, and there is even a theory that the energy required to evacuate the waste from milling or drilling is equal to the energy required to drill or mill. If not discharged, the waste can damage tools during machining. As, like any process, evacuation also has a specific output, the machine has to be stopped from time to time so that it can be cleaned. The question is: are there smart tools that can increase the efficiency of dust removal and thus reduce energy consumption? It turns out yes.
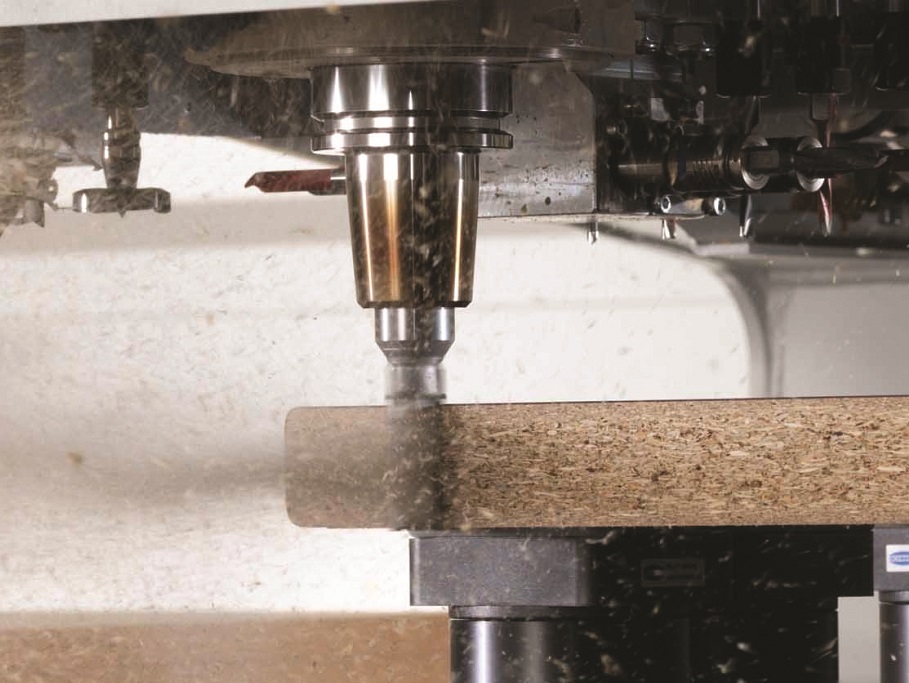
By chance, I happened to see a data sheet of such a tool. As technical information was quite scarce, I started to do some research. I may not be a "minitehnicus", but I've always been technically inclined (I was going to say that I'm an engineer, but that's not really relevant now 🙂 ) So I didn't give up until I found information that would help me understand how the process was designed and how the part works.
This is a chuck coupled with a suction system capable of sucking up to 90% of the chips and dust formed. This turbine attached to the chuck controls the flow of dust and chips resulting from milling and using the energy of the flow - the chips come out at speed when milling - it removes them from the chipping tool, channeling them to the suction system.
This seemingly simple idea comes with a number of advantages:
- energy saving - The exhaust air flow no longer has to capture the chips, but only transports them. This reduces the airflow, which is very noticeable in winter when the warm air is no longer exhausted, and heating costs are considerably reduced;
- increased productivity - The machine no longer has to stop occasionally to be cleaned, with increased productivity resulting in effectively more working time;
- reduced maintenance costs - Splinters are abrasive materials, and removing them quickly increases the life of drills and bits.
The system is called "Dust Flow Control" DFC and belongs to the group Leitz. But in addition to this system, the chuck has a number of other advantages:
- the material it is made of is very hard, with high resistance to the very high frictional forces that develop during milling or drilling;
- thermal clamping/clamping of the cutting tool which gives maximum stability and rigidity, optimizing the process. Basically the mill or drill becomes one with the chuck. This is another clever system. To get an idea you can see the video below;
- The tool is clamped with an eccentricity of 0.01 mm and is perfectly balanced up to 24,000 rpm.
If you want to find out more about this chuck, by its baptismal name "Shrink-fit chuck ThermoGrip® with DFC® Turbine" you can enter here.
My final point is that if someone says that using one system or another will save you money, you should test that system to see for yourself. And if so, then use it. I'm not saying that you should immediately replace the parts you're working with now with other parts. But if you cut costs, you make the system more efficient and more profitable. My opinion! 🙂
Add comment