Objects made of wood or derived materials often need finishing. In other words sanding, coloring - if necessary - and final protection with different materials. The choice of materials is made according to aesthetic and resistance requirements. Use oil or wax, for a natural look or varnishes and paints when film resistances, appearance with mirror gloss or other special effects are important. Whatever material you choose, the final look depends on its application. This can be achieved if the right technologies are used, and the right workspace and equipment are used. Without minimum application conditions, no matter how good the products are, they will fail to make perfect surfaces. In this case, it is better to turn to companies specializing in industrial painting, which have good conditions and high-performance equipment. The fashion for high-gloss finishes has led to the emergence of such a business, but there is still plenty of room for those interested.
Wood varnishing and painting - a business in itself
The idea of making wood varnishing or painting a business in itself is not new. It is a specialization that guarantees a very high quality finished product. Well-known companies have been finishing furniture of very high quality for many years and exporting it to countries in Europe, the USA and the Middle East. But the wooden pieces are made by other manufacturers, only up to the finishing stage. The furniture is bought "blank", i.e. unfinished. The finishing is done by the furniture exporter, who has control over the final quality of the products.
But painting can also be done as a service for the furniture manufacturer. In this case, the furniture or just component parts are taken to the industrial paint factory, which does the finishing in the best possible conditions and then hands the pieces over to the manufacturer. This is a service that has been available for some time and is used by many of those who make mirror-finish MDF furniture, which is a demanding finish that requires special conditions. It is similar to car refinishers, where the investment in equipment is very high.
Requirements for a perfect finish
But why is a quality finish so hard to achieve? What conditions must be met for the varnished or painted surface to look great? The most commonly used way of applying products is by spraying, so I'll cover the necessary conditions for this below.
Praful is the finish's number one enemy. Generally, the materials used are liquid at the time of application. By the time they dry, the dust and fine varnish particles that constitute the overspray fall onto the finished surface and remain in the film. The result is a rough finish with an altered gloss, which is very unpleasant to the eye. To avoid such problems, there must be a very good exhaustion system and other dust-attracting arrangements (water curtains, water baths in the floor).
Temperature and humidity in the workspace influence the appearance of the film. The recommendation from varnish and paint manufacturers is that products should be applied at 18-20°C. If it is too cold, the varnish will not spread well. If it is too warm, the viscosity decreases and the product may leak. High humidity in the workshop can lead to opalescent surfaces or affect drying time.
Equipment with which the spraying is done is also important. In order to obtain a quality film, the lacquer must lay down evenly, not be cloudy, and there must not be a large amount of overspray. Quality spray guns must be used for such a result.
Exhaust quality. The exhaustion process removes the stale air (with dust and varnish vapors) from the enclosure and introduces clean air into the enclosure. The sooner the varnish dust is removed, the less likely it is to reach the film. The air circulation must be calculated in such a way that no "waves" are created on the varnished surface.
How to get the right finishing conditions
The simplest is to have a spray booth which removes stale air with a fan. The air is passed through filters that trap dust and fine varnish particles. The filters can be dry or wet. A dry filter is an agglomeration of fibers through which air is forced to pass. Some of the dry lacquer particles and dust will be trapped by these fibers. Until it is released into the atmosphere, the air can pass through several such filters, becoming cleaner and cleaner. A water filter is actually a water curtain. Stale air is absorbed through the water curtain, impurities remain in the water.
The best conditions for quality spraying are in pressurised spray booths. A pressurized cabin is a closed enclosure in which a slight overpressure is created by introducing more air than is being exhausted. As a result, dust from the outside no longer gets inside. For the overpressure to persist, the cabin must be very well sealed. The cabin is also equipped with devices to maintain constant temperature and humidity.
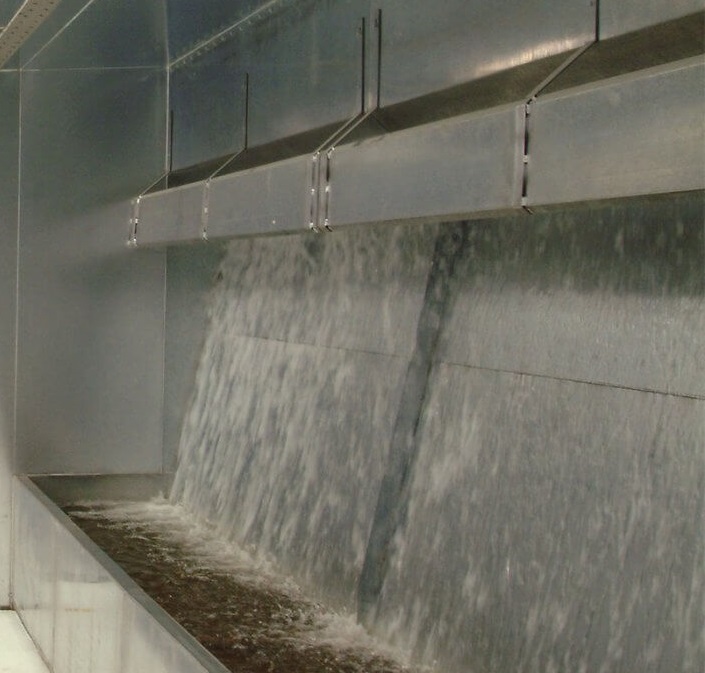
source: airblast.co.uk
Spray guns play an important role in achieving quality surfaces
Spray guns can influence the final quality of the film. How surface material transfer is better, the better the film looks. Low transfer means high losses, i.e. varnish dust which negatively influences the quality of the film. The types of spray guns with the lowest losses are:
- HVLP
- electrostatic guns
- airless guns
HVLP guns are modified so that the material can be sprayed at low pressure. Only low viscosity materials can be applied in this way. Productivity is low, however, making it a gun suitable for occasional finishing and low volume work.
When applying with electrostatic guns consumption is reduced by 50 to 80% compared to conventional spraying. Due to the electric charge, particles are attracted to the object to be finished and only a small amount ends up being lost.
Airless guns use high pressure to make quality applications. The jet of material is forced through a special nozzle that atomizes the slurry which then comes out unmixed with air. It is a good material transfer system, very suitable for viscous materials.
Guns that combine reduced wastage with very good surface quality are those that use spray systems of medium pressure. Airmix is one such system, trademarked Sames Kremlin. The concept is a successful one, turning a common technology into a global industry standard.
When the object of activity is industrial painting, the choice of spray gun is linked to the workload and the type of materials applied. As spraying is supposed to be done at least 8 hours/day and different materials can be applied, a reliable, resistant, flexible and low-loss gun must be chosen. Flexibility helps to ensure that switching from a less viscous to a more viscous material is not a problem. If both solvent-based and water-based products are being applied, it is advisable to use dedicated guns for each category to avoid high solvent consumption and defects that arise from mixing the two types of materials.
You can turn painting into a business. It is not simple, but there are many who are looking for such a service and in the end it can be a good business.
Add comment