The high gloss of furniture, flooring, musical instruments and other such examples of finished wood is hard to achieve. It requires a lot of work and following certain rules. If with a matt finish some faults can be overlooked and are invisible to the vast majority of those who look at it, with a gloss finish the defects are very visible. The gloss highlights all the flaws, making them visible even to the uninitiated.
It is not enough to use a good quality gloss varnish to achieve the gloss. If certain requirements are not met in terms of working technology, product preparation and working space conditions, no matter how good the varnish is, it will not work wonders. This is why I will present you with what I think are the conditions that must be respected to obtain a high quality gloss.
Perfectly flat surface, without bumps and roughness
The gloss of a finish expresses the extent to which a finished surface reflects light. At high brightness the percentage of light reflected approaches 100%. For this, the surface should be as flat as possible, without bumps or roughness. Obtaining this surface starts with the white sanding of the wood, which is done with sandpaper with successive grits, starting at 80-100 and going up to 180-240. There is no need to sand with each individual grit level. It is sufficient if 3 different grits are used (see also here). Also, the sandpaper should be replaced after the recommended time of use or if it is heavily clogged.
The primer applied must be full-bodied, hard and in sufficient quantity to allow very good sanding. Sanding removes roughness and orange peel appearance, ensuring a perfect surface for applying gloss varnish. The most suitable primers are polyester, polyurethane or UV-curing primers (polyester, acrylic, polyacrylic, etc.).
The sanding of the primer should not be done with a grain size less than 400. Because of the gloss, fine curls that occur after sanding with smaller grit paper will become very visible.
Thinner is very important
The varnish must have time to spread very well before it starts to dry. This is why a slower, good quality thinner should be used, regardless of the season. If it is not very well laid and the surface has orange peel, it must be made polishing. Polishing or buffing is a more advanced polishing, which is carried out with very fine-grained abrasive materials up to 4000.
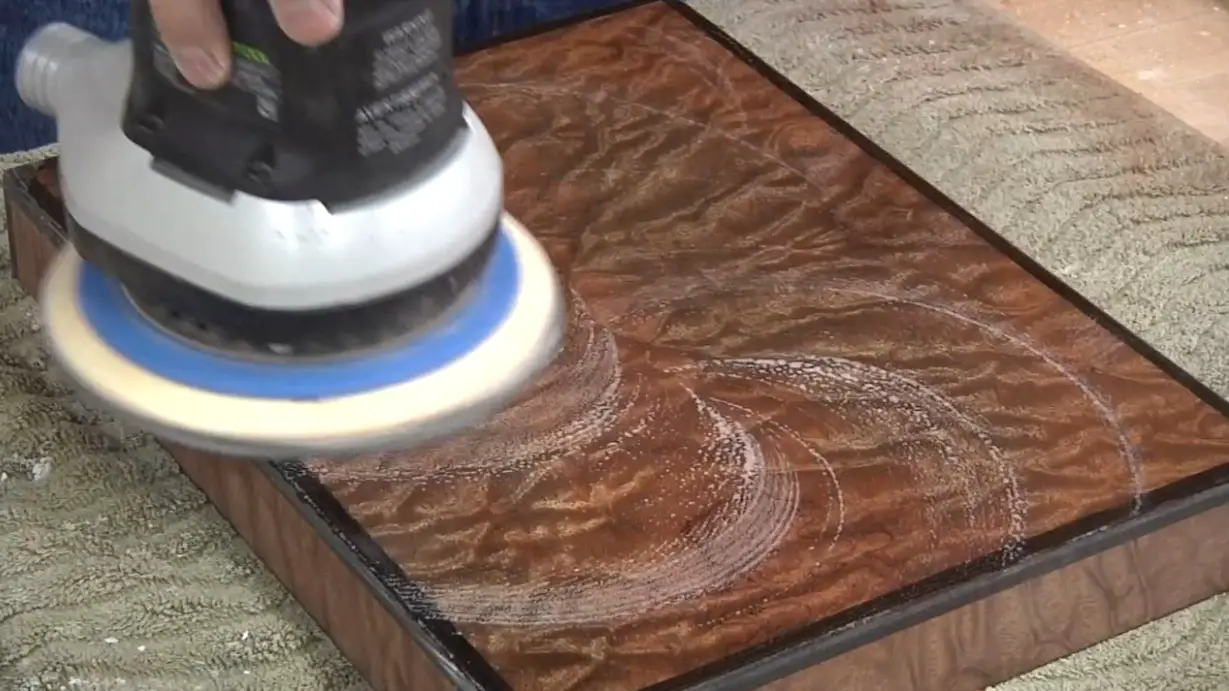
Clean, dust-free space
There must be no dust and impurities in the air in the area where the varnish is applied and dried. The varnish has a longer drying time and so impurities can be more easily absorbed into the film, becoming very visible because of the gloss. It is very difficult to get a correct gloss finish in a normal spray booth finishing area without polishing. No matter how clean the environment is there will always be impurities in the air. Pressurised spray booths or capped and pressurised finishing lines can be used to reduce them as much as possible. Even so, impurities can sometimes occur, which are also removed by polishing.
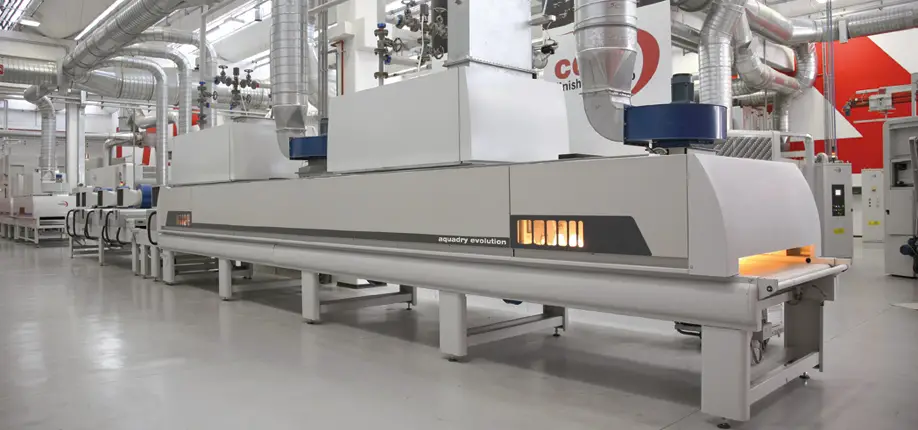
Good quality varnishes
The gloss varnish used must be of good quality, spread well and if it is a hardener varnish, it should not be fast. At the time of application it should be at approximately the same temperature as the wood substrate and the environment. The recommended temperature is between 18 and 20°C. Slight variations from this range are acceptable but the greater the distance from this range, the lower the chances of achieving a quality finish.
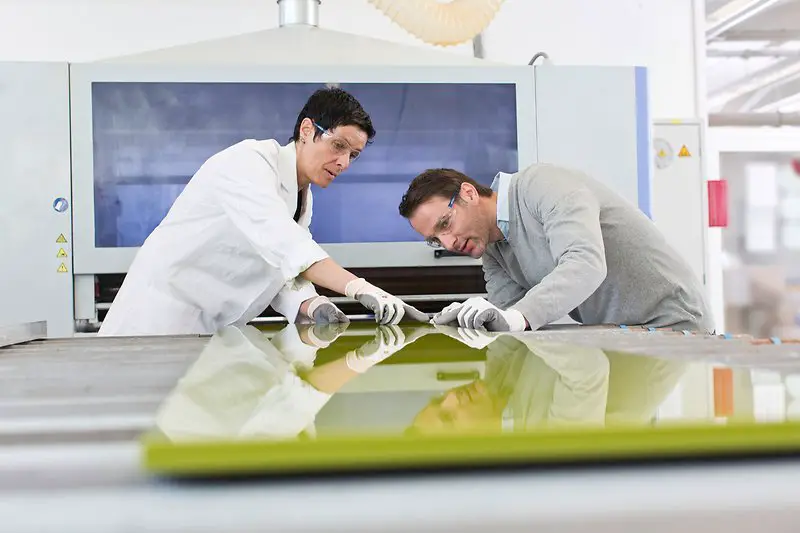
The above recommendations apply regardless of the nature of the finishing materials, technology or machinery used. If they are followed, quality finishes can be achieved. Omitting them leads to finishing defectsand repair means additional consumption of materials and workmanship and therefore additional costs.
Add comment