When it comes to high-gloss, mirror or high gloss finish as they call it, I always tell you that it's very hard to achieve, and for that you need special workspace facilities. Dust, uneven varnish, orange peel, cause the light not to be perfectly reflected and the gloss not to be as desired. However, there is a method where you can achieve the mirror shine even if the varnish application and working conditions have not been perfect. This is polishing.
In short, the technology to achieve mirror gloss is as follows:
- preparing the wood support by calibrating and sanding;
- application of primer coats (min.2). The primer must be as hard as possible so that sanding between layers that it can be done as well as possible;
- sanding the primer coats. Sanding of the primer may be done after each coat applied and thoroughly dried or, if the application is wet/wet, after all coats have been applied and properly dried. Sanding for gloss should be done with sandpaper with a minimum grit size of 400;
- applying the final coat of gloss varnish.
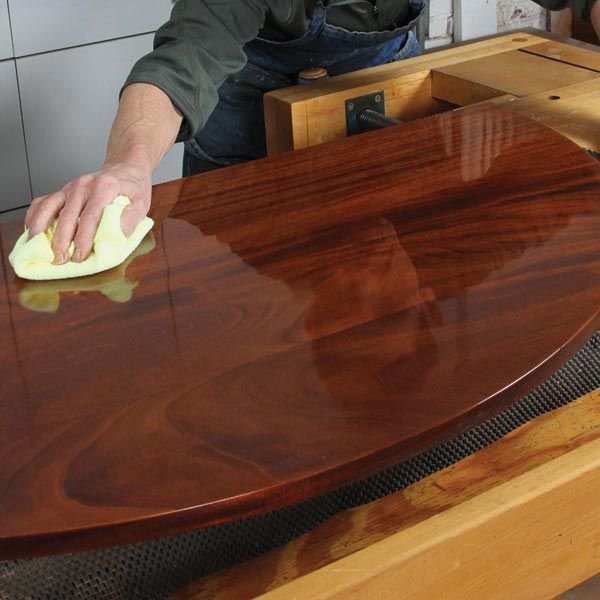
With the same technology, both transparent and opaque coatings can be obtained, and the substrate can be wood or MDF. To achieve the perfect gloss, the atmosphere in the workspace must be dust-free and the lacquer must be very smooth, even, smooth and not orange peel. Because of the sheen, dust and trash trapped in the film show up much better on the finished surface, and their presence is even exaggerated. Film defects prevent light from reflecting 100%, resulting in a lower gloss. To eliminate problems, you need a clean atmosphere provided by high-performance exhaust systems, and the varnish should be applied in pressurized booths. The varnish must be of high quality, the drying times must be respected and the thinner used, also of high quality, must ensure that the varnish is perfectly spread and perfectly even before drying.
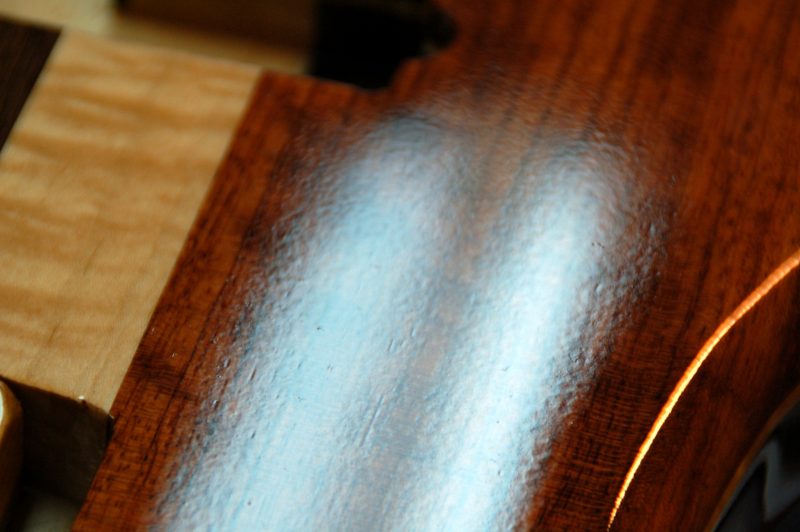
photo source: wordpress.com
As you can see there are many "musts" to be able to get that mirror sheen. You can remove some of them with polishing. But what is polishing? It's a finer sanding, a polishing, which is done with abrasive pastes and leaves behind a very smooth film. It can be done just to remove dust and dirt trapped in the film, but it can also be used to remove a thin layer of varnish, getting rid of the orange peel.
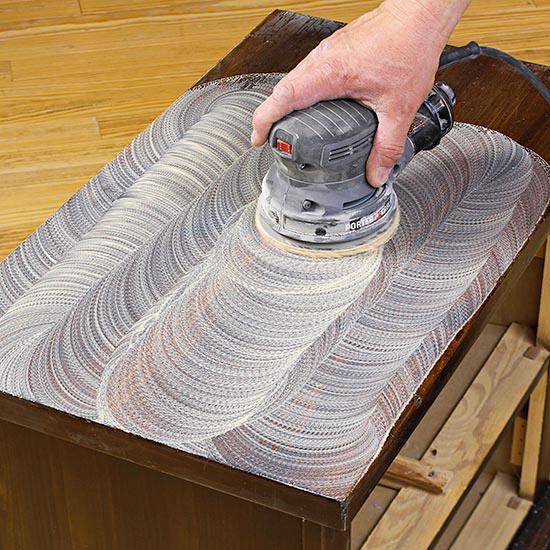
In order to get rid of the haze, the polishing process starts with sanding with lower grit sandpaper (400, 600, 800) and continues with abrasive pastes, also progressively, from 1000 to 3000 and even more. The higher these numbers are, the finer the material used for sanding, the more and smaller the abrasive particles contained.
Polishing can be done both by hand and by machine. Because it is labor-intensive and physically demanding, hand polishing is effective for polishing small surfaces and removing minor defects.
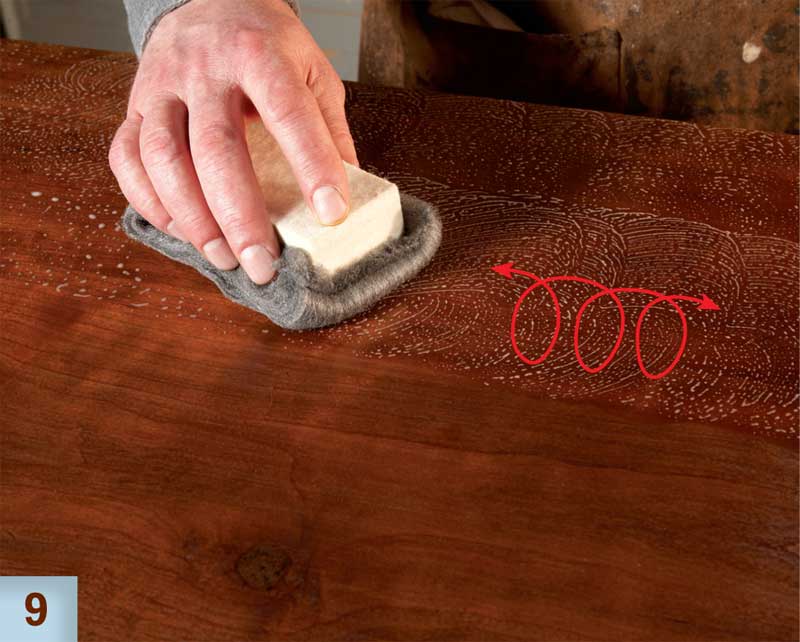
If the surfaces are large, polishing machines (basically rotating sanding machines) are needed. There are both small, manual polishing machines and industrial machines. The manual ones have a rotating drum at the center of the machine, onto which you attach a disk of felt or other very fine, soft materials (cotton, felt, steel wool).
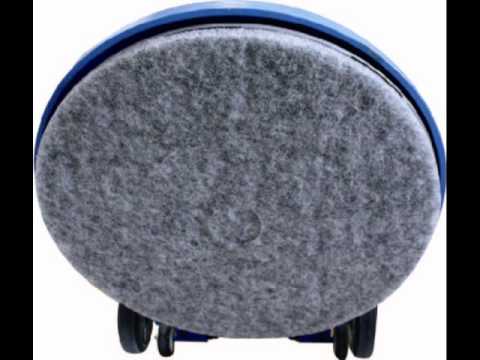
photo source: alibaba.com
To polish, a small amount of abrasive paste is applied to the surface and then the surface is rubbed in a rotating motion with the polishing machine. The fine felt disks help the paste to spread well to work where it is needed, but without scratching or damaging the film. As I said, you start with 1000-grit paste, then continue with 2000 and 3000. The polishing is done over the entire surface to obtain a uniform gloss. If the polishing is done only locally, it is possible that there will be a more glossy area compared to the rest of the surface. At the end the dust particles are removed and the surface remains glossy without the need to apply varnish or any other product on top.
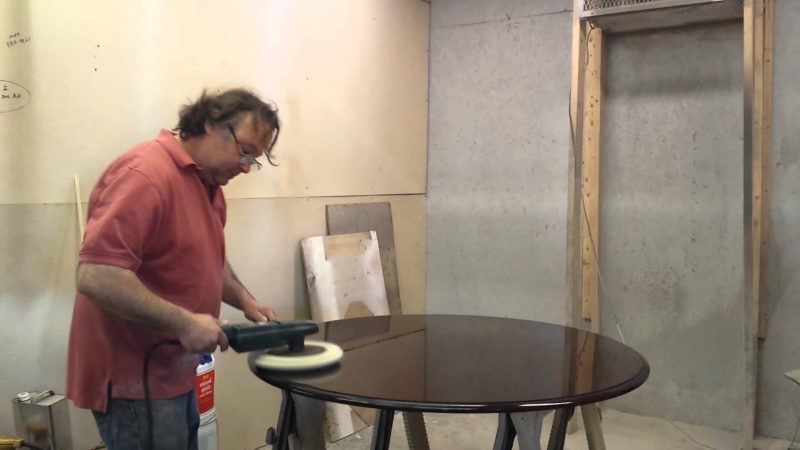
In the case of manual polishers, as well as larger machines such as floor polishers, the object is static and it is the machine that is moved over the surface.
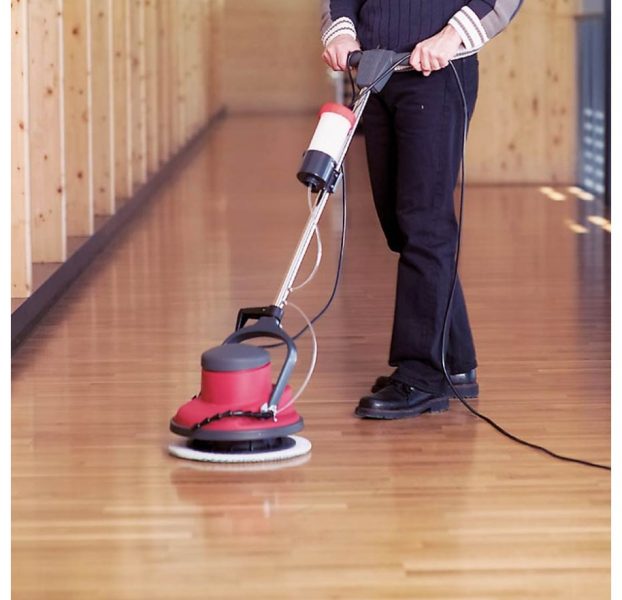
With industrial machines it's the other way around, the machine is stationary and the objects pass through the belts, on which the felt is applied, to be polished. I had the opportunity to see how musical instruments are polished in one of the factories in Romania. It is impressive how skillfully and quickly large instruments (such as double basses) are moved by a polishing machine with a vertically rotating belt. The movement is repetitive, at one point even hypnotic. And at the end you get the feeling that the instrument is perfectly polished.
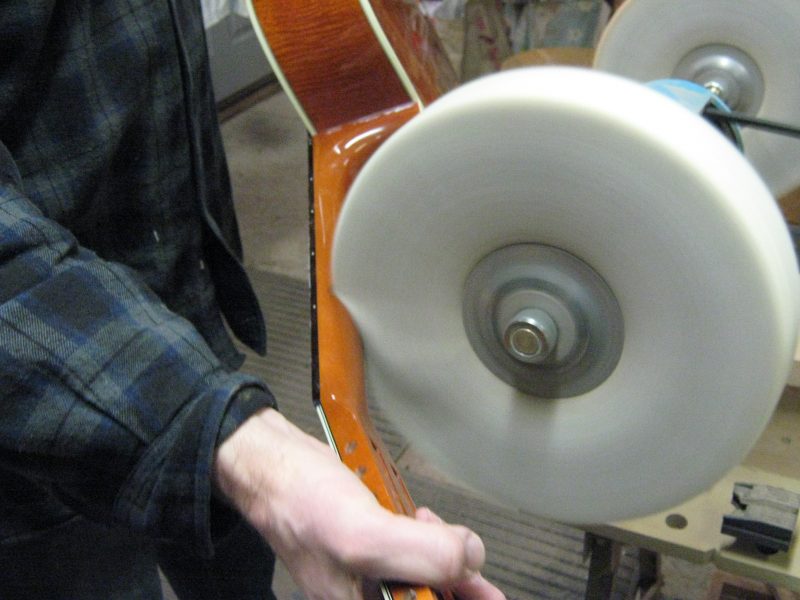
Being musical instruments, polishing machines are of a more specialized construction, as the objects have different and sometimes difficult shapes. However, there are also polishing machines that can be integrated into modern finishing lines, polishing parts without human intervention. They are perfect for parts with less complicated shapes and mass production.
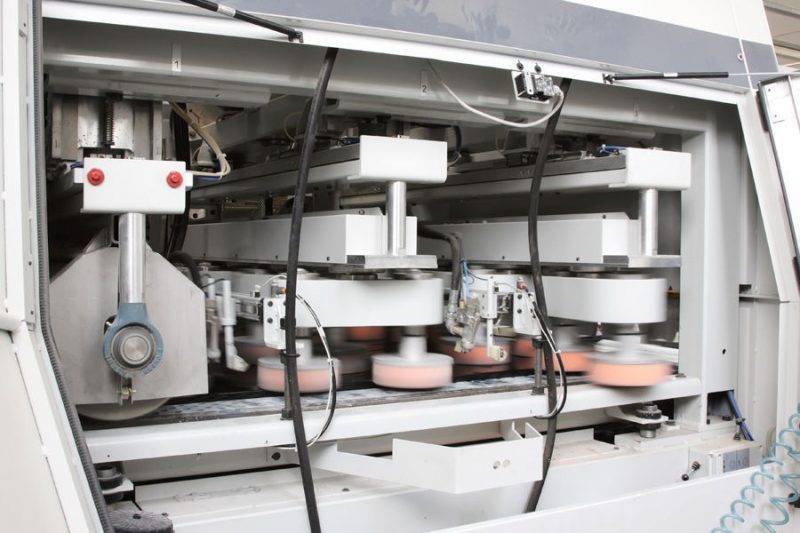
But you should know that not all varnishes can be polished. There are some that, due to the heat released during polishing, lose their sheen and even become slightly opalescent. It's a good idea to ask your refinish supplier if the varnish you are using is polishable. This avoids potential problems.
Polishing is not a simple operation, but it is not impossible to do. You can try it even if you are not a professional woodworker. If you've used a drill once, you'll certainly be able to use a polishing machine. The important thing is to get started and have the right materials.
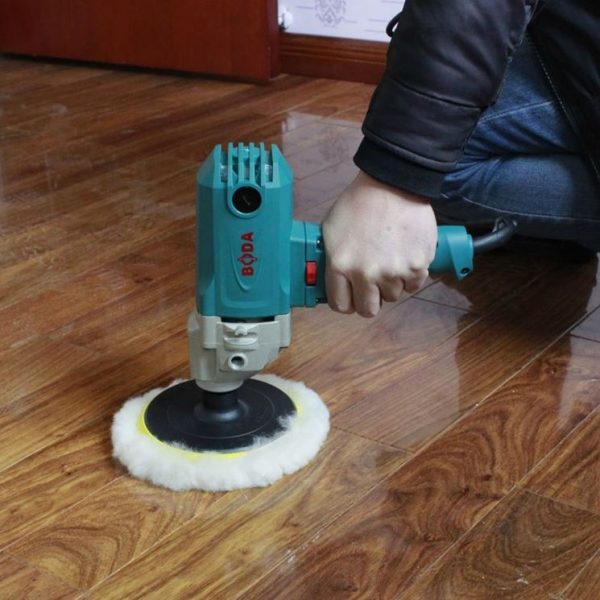
Very good tips,you save time and money in the process of putting out a good product!!!
Hello
I would like to know where to find wood polish abrasive paste and possibly a product code. Everywhere I find only for cars and I suspect it is not suitable. Thanks
Hello.
Most companies that have abrasive products for wood also have abrasive pastes (3M, Klingspor, Mirka, Carbochim). Preferably use wood products, but I've also seen glossy MDF polished with automotive pastes and it looks good. In this case use products recommended for many types of surfaces (they are less aggressive) and the lacquer applied should be as scratch resistant as possible. Make successive sandings with smaller and smaller grit sizes (600, 800) and then use pastes (1000, 2000, 3000).
All the best!
Hello. Can you recommend me some wood varnishes. Which would be the best? Thank you very much for your answer.
Good evening!
Lacquers come in many varieties and you should know what you want to use them for: indoor or outdoor, furniture, table tops or flooring, bathroom or kitchen furniture.
If you work with wood as a craft, my recommendation is to use professional varnishes. There are many good brands on the market: Sayerlack, Sirca, Renner, Ica, Milesi, Remmer, etc. Distributors of these brands also have trained technicians and can recommend the right product.
If you work with wood as a hobby, use products from DIY stores. The important thing is to follow the manufacturer's instructions. Very often, the difference between a good finish and a poor one is down to the way the materials have been applied.