A very important part of the finishing process is the drying of the materials. About drying in ambient air we have already talked about. But in large factories (and not only) there are installations for the forced drying of finishing materials, generically called dryers. They reduce drying time and thus increase productivity. They are usually inserted in finishing lines, following the natural flow of the technological flow, but they can also be separated for hand-finished parts or to serve several finishing lines. A little about these dryers in the next material.
But first I want to tell you that, depending on how the film is formed, there are 3 types of drying:
- Physical drying - the products dry due to solvent evaporation. After drying, these materials can be dissolved again in the same solvent (reversible process). The time for physical drying can be significantly reduced by increasing the temperature. This is the case for nitrocellulose products
- Chemical drying - drying of two-component materials. In reality, it is the chemical reaction between the two liquid components that results in a third product, the varnish film, which is solid. This is how polyurethane, polyester and polyacrylic products dry. The drying of single-component products, such as water-dilutable products (acrylic dispersions), can also be considered as chemical drying. In this case, the chemical reaction is triggered when the molecules come very close together as a result of the evaporation of water. Unlike nitrocellulose lacquer, in this case the process is irreversible, i.e. the film does not become liquid if water is added.
- Oxidative drying - is the drying and curing of synthetic alkyd resins. In this case drying is the result of evaporation of solvents and a reaction between the resin and oxygen in the air. It is the type of drying that is not greatly influenced by temperature rise.
Back to dryers used in industry. The most common are:
Convection dryers. Such a dryer has 3 distinct portions: the de-drying space, the actual drying space and the cooling space. The de-aeration zone is immediately after the application of the finishing material and is necessary for the varnish film to set as well as possible. The temperature in this zone is close to room temperature. In the drying zone the temperature rises up to 45-50 grd.C. This is where drying and hardening of the film takes place. In the cooling zone the objects are brought to room temperature before being removed from the dryer. Cooling the objects is very important because most coatings are thermoplastic, which means that they are soft at high temperatures. Air exchange in the cooling zone must be intense.
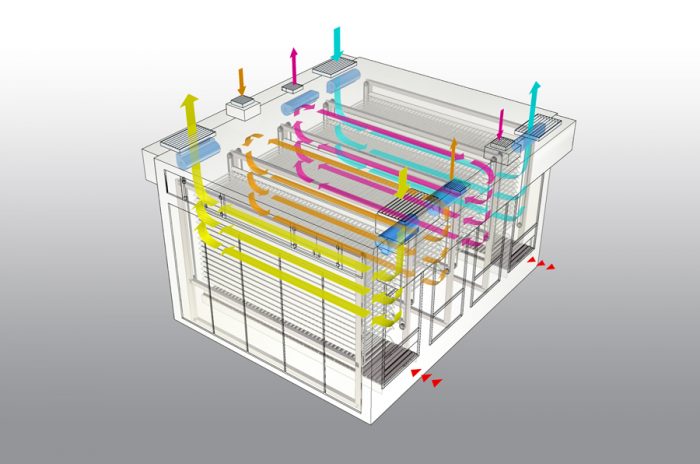
photo source: ceflafinishing.com
These dryers are most commonly used and they can be built vertically or horizontally. The materials are moved inside them by means of rising and lowering turntables in the case of vertical dryers, or conveyor belts or chains (chains) in the case of horizontal dryers. The speed of movement is calculated in such a way that the material is dry when it leaves the tunnel.
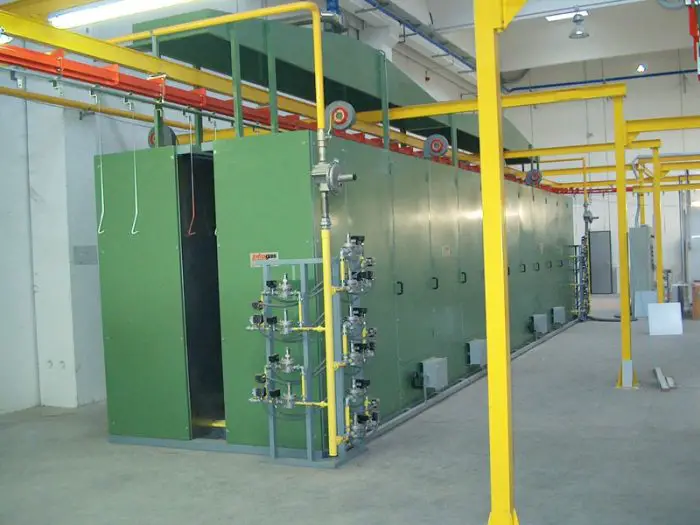
photo source: infragasnova.com
IR infrared dryers. In such dryers the heating power of IR radiation is used. Electromagnetic radiation with a wavelength of 0.76 µm - 1 mm is called infrared. Depending on the wavelength of the radiation there can be IRS dryers (short IR radiation), IRM dryers (medium radiation) and IRL dryers (long radiation). IR dryers are often combined with convectional dryers.
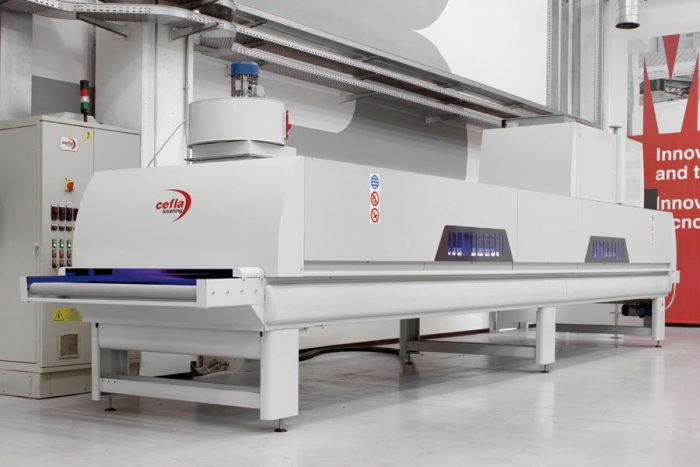
photo source: directindustry.com
IR dryers are more energy-efficient than convectional dryers.
Ultraviolet UV dryers. In these dryers the material is cured by UV radiation. Varnishes and paints specially formulated for this type of drying (acrylic, polyester, combination) are used. Curing takes place very quickly (5-15 sec).
Two types of radiation sources are used: gallium (Ga) lamps and mercury (Hg) lamps. Gallium lamps have a wavelength longer than 420 nm and a lifetime of about 2000 hours. They are used to harden pigmented varnishes and are often combined with mercury lamps. Mercury lamps have a wavelength of 200-380 nm and last for about 3000 hours. They are used for curing clear lacquers. UV lamps need to be checked regularly because their power decreases over time. Energy consumption is significantly lower than with convectional drying.
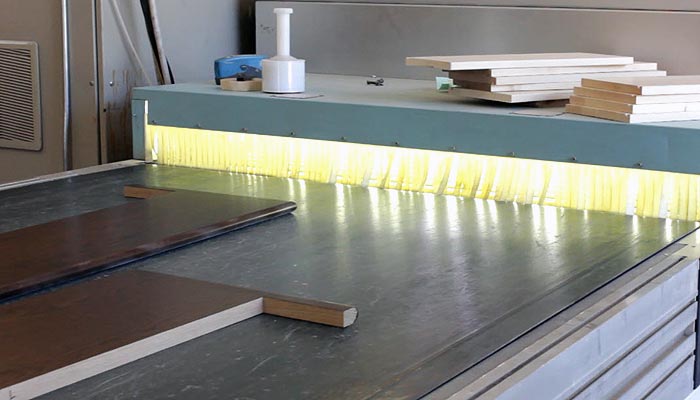
photo source: uptownfloors.com
On UV curing the solvent must be removed until the product comes under the lamp. The remaining traces of solvent make the film opalescent. This is why there is a convectional or IR drying tunnel in front of the lamps to help remove the solvent. The length of this tunnel depends on how quickly the solvent can be removed. For drying water soluble products the tunnel is longer. The tunnel can only be missing for waved products with body 100%.
For pigmented finishing, dual-cure products can be used, i.e. products that have a combined UV + chemical cure. Such products are mixed with hardeners and as they pass through the lamps the curing takes place superficially, but not in the depth of the coating. The film hardening process is continued after the objects come out from under the lamps thanks to the added catalyst. This is necessary because, due to the pigment, UV radiation cannot penetrate the film to harden it instantly. So why not use normal curing without the hassle of UV? Instant surface drying when passing through lamps means that the film no longer traps atmospheric dust when placed on the squeegee for total drying, thus increasing the quality of the film (especially glossy films).
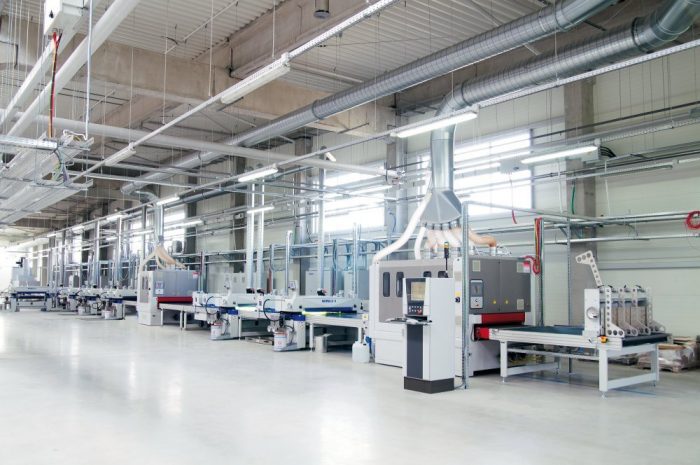
photo source: mpsmachine.co.uk
Drying time is a very important element in working technology as well as in the economics of the production process, especially when large volumes of identical products are involved. A dryer greatly shortens drying time while increasing productivity. But if your field of activity involves artistic, unique, labor-intensive products that add value, a high-performance dryer is not the best investment.
Add comment