Sometimes, cracks can appear on the surface of painted or varnished solid wood, which can lead you to think that there may be a problem with the finishing materials. But if you look closely, you realize that all those cracks follow the grain of the wood. By analyzing them with a strong magnifying glass or sanding along the crack until you get to the wood, you will find the same cracks in the wood. Because of the large difference between the moisture content of the wood and that of the environment, or improper drying, stresses build up in the wood which lead to cracks. As I have just come across such a defect, I thought it would be useful to revisit the discussion of wood drying and reaching equilibrium moisture content.
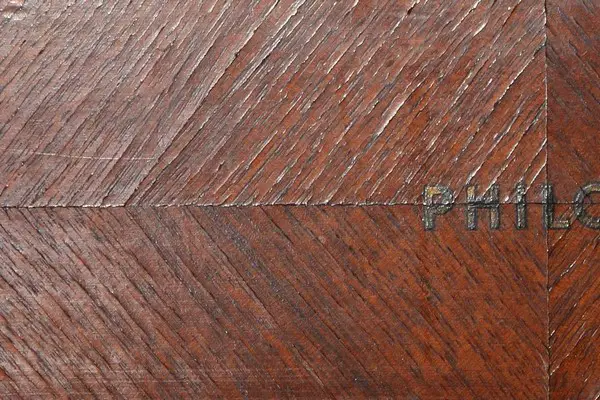
The drying of wood depends on several factors and can be done naturally, in stacks, or forcibly, in special dryers. Factors influencing drying are:
- species and type of wood
- plank thickness
- initial humidity
- final humidity
If we talk about natural drying of wood as a diy process, when the man cuts his own tree and takes care of drying the wood, then it is good to consider the following:
- It is best to cut the tree when the tree is at its least active, i.e. November-December. During this period the humidity of the wood is at its lowest and drying is easier, without major splitting problems.
- cutting into planks should be done as soon as possible after cutting to avoid cracking;
- The thickness of the planks depends on what you want to do with them. There is no standard size. But you should be aware that for every 2.5 cm of thickness, it takes about a year to dry. In general, the drying time in years is calculated using the formula: plank thickness (cm):2.5 cm + 1.
- it's good to keep the peel as it prevents water from draining out quickly and causing tension.
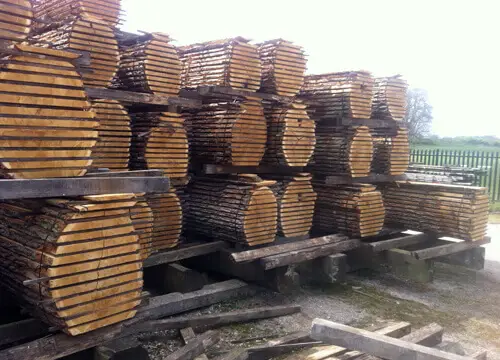
Drying wood for use in industry or for sale to processors, however, is forced. Forced drying has many advantages as well as disadvantages. The most important advantages are:
- much reduced duration of the process
- highly efficient and accurate control throughout the drying period
- achieving uniform humidity over the entire plank surface
- any final humidity can be achieved
Disadvantages include:
- high energy consumption
- investment costs - special drying rooms are needed
- qualified personnel to work with such drying chambers
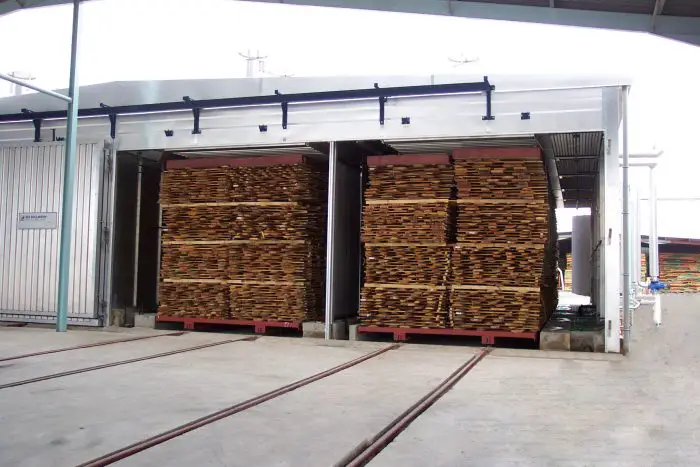
Forced drying can be done in several ways depending on the mode of heat transmission. The most commonly used are:
- conventional drying - is the most commonly used and is based on the principle of removing the air saturated in moisture and replacing it with air of normal humidity. Using this method it takes 1-7 days to dry resinous species and 10-30 days to dry hard species. If the drying of the resinous species goes smoothly, the method does not work very well with hard species, as the percentage of cracking is quite high.
- condensation drying - is based on removing moisture from the air in the dryer by condensation. It is a longer cycle because it requires heating the air after it has been cooled for the vapors to condense, but the drying quality is better on hard essences. The main disadvantage is the possibility of discoloration and mildew due to the longer dwell time in the dryer.
- vacuum drying - Vacuum dryers are smaller in size and can be a good option for small and medium-sized factories. The drying time is short and the quality good. Very suitable for hardwood with evenly distributed pores (e.g. beech).
- high temperature drying - is based on the addition of superheated vapors. The drying time is reduced by half compared with conventional drying. During drying, the temperature reaches up to 230 grd.C, which leads to a change in the color of the wood (darker wood). However, it has the advantage of much greater dimensional stability and increased resistance to insect attack. It is preferred for drying wood used in construction.
- CIF high frequency current drying - is an expensive, but time-saving method (up to 70%). It is combined with vacuum drying and is used for drying valuable species. The drying quality is very good in both softwoods and hardwoods because of the low temperatures and short drying time. For these reasons there is no discoloration or mildew.
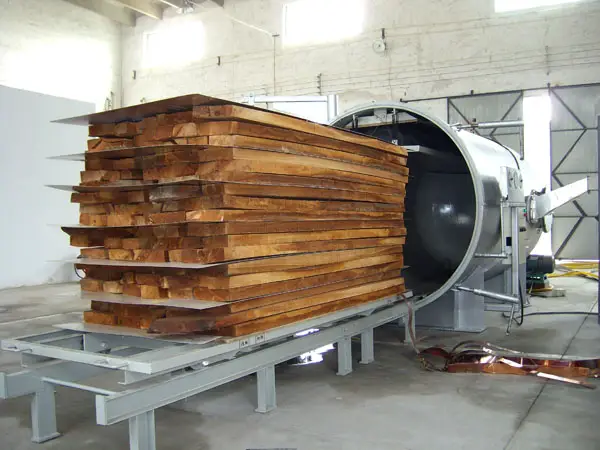
Drying aims to achieve equilibrium humidity of wood when it is most dimensionally stable and the probability of cracking is very low. Wood is considered 'green' if its moisture content is greater than 35%. Dry wood has different moisture contents depending on the area where it is to be used:
- in construction 12-20%,
- exteri0r 15-17%,
- for burning 20%,
- for furniture 8-12%
- on acoustic musical instruments 6-8%
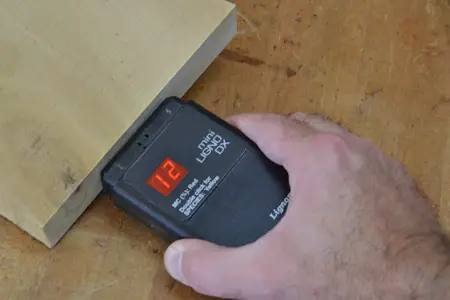
Even when wood has reached equilibrium, it continues to exchange moisture with the environment. Therefore the final moisture content should also be chosen according to the area or place where it will be used. It is good to know that a 4% change in ambient humidity leads to a 1% dimensional change in solid wood furniture. Therefore, construction solutions must take these changes into account and leave room for the wood to be able to "move". If it is clamped very rigidly tensions can occur leading to cracking.
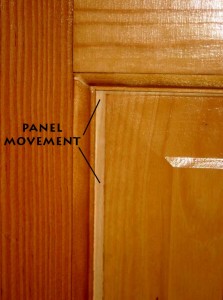
There is a very close link between the humidity of the environment and that of the wood. Specialists have come up with the following relationship between the two humidity levels:
- 25% medium - 5% wood
- 50% medium - 9% wood
- 75% medium - 14% wood
- 99% medium - 23-30% wood
Therefore, when furniture or objects made of solid wood have to go to other deographic zones than the one where they are produced, it is good to know the humidity in those areas in order to avoid problems. We are talking here about those who export processed and finished wood in various forms. For example, a piece of furniture made of wood with 9% humidity at 9% humidity, taken to an environment with 75% humidity, will change dimensionally by more than 1% because the wood has to reach 14% humidity.
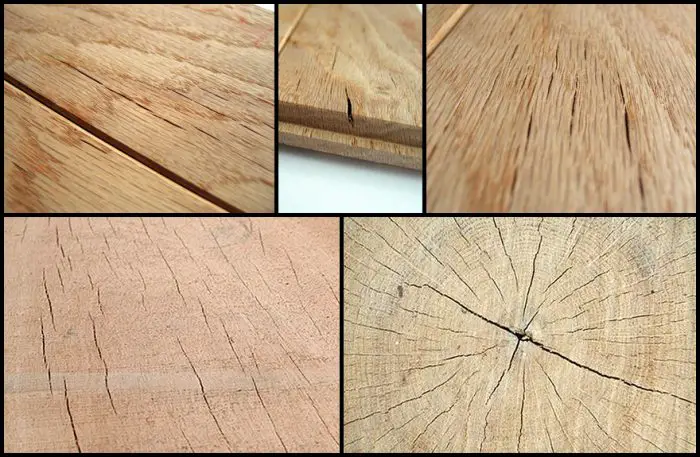
Much can be said about wood drying, which is the most important step in solid wood processing. But it is better to stop here, and I will come back with more details on other occasions. For more information on natural drying you can also read the article on natural drying of walnut wood.
I saved two 40×40 hair logs from the fire. how to dry it? leave it in the stump or cut it?
I saved two 40×40 hair logs from the fire. how to dry it? I leave it in the stump or cut it? back to wrong email address
Hello,
They need to be cut as soon as possible to avoid cracks. Cut them into "slices" and place the shingles in the covered stack. They should not stand directly in the sun. In the root the tensions are even greater than in the trunk.
All the best!
"[...] when furniture or objects made of solid wood have to reach areas other than the production area [...]'" ... all due respect to the intention but let's be serious.... not all furniture reaches other areas? :)) AND how many times has a customer come in knowing what percentage of humidity the room they are going to put their furniture in has? Let's get back to practice, as in theory...
Hello,
Indeed, the wording was ambiguous. I was referring to geographical areas other than those where furniture is produced, i.e. export. I have had such experiences with solid wood furniture made for the USA.
I also made the clarification in the text. Thank you.
All the best!
From the point of view of endurance for woodwind musical instruments (flute) how would the following be ordered according to their endurance over time: hazel, elder, ash, plum, cherry?
Thank you.
Hello, the technical veneer for the manufacture of elastic beech slats, what humidity should it have?
Good evening.
From what I learned many-many years ago, it should have between 6 and 8% if it is to be sealed with water-based adhesive and 10-12% (some data say 10-15%) if sealed with adhesive film.
Hello
In order to obtain a drying with as little cracked material as possible, should the lumber be put in the kiln immediately or should it be left for a while in natural ventilation (outside)?
Thank you
Hello.
The sooner it gets in the dryer the better. Natural drying cannot be controlled so the moisture exchange with the environment is based on the humidity of the environment at that moment and does not take into account the humidity of the wood or other factors such as thickness, species, etc. There are special programs in the dryers and the air humidity and moisture exchange with the wood is controlled. You should know that there is a certain percentage of cracked wood in the kiln as well.
All the best!
Hello. I ordered some interior doors in Spain, veneered with cherry. Yesterday I received them and was shocked to see that the door leaves and the frame (12 cm) have a certain colour (light brown, honey), and the frame extensions (the thickness of the walls where the doors will be mounted is about 30 cm) have a much, much lighter colour (the colour of the unfinished shingle). The manufacturer says that in time they will darken in colour. That they have been wet-processed and that over time they will dry and darken to about the colour of the door leaves and door frames. I don't know what to do, whether to believe them and keep the doors or send them back. Please help me with some advice. pircalab_a@yahoo.com Thank you.
Good evening.
From what you tell me it is cherry veneered doors (at least that's what I understood from the translation). The cherry darkens over time, the colour fading starting immediately after cutting. However, the difference seems far too great. It could be that the veneer on the doors also darken and the difference remains. You should ask for guarantees from the manufacturer that if the colour doesn't come close in a month you can return them. If you don't like them the way they are now it's not worth the risk. I would talk to the manufacturer.
All the best!
Hello. Thank you for your comment, I have contacted the manufacturer and asked them to confirm in writing that those holster extensions will close in time (a few months said the manufacturer). And that otherwise they send the goods back and refund my money or replace the goods. He said to do a test, namely to expose the extensions to natural light (sunlight) for a few days, after previously sticking a sticker on them. After a few days the manufacturer says I will notice the difference. I am very curious. I will keep you informed. Thanks again for your help. Good luck.
Good evening!
Glad I could be of help.
I'm waiting for news about the colour change.
All the best!
My name is stefan and I asked if I put a beam in the dryer what size should I cut it to be 15 × 22? Thank you
Ok ! I have understood what and how, what I didn't understand is which is the better , , , healthier , , method for drying , the artificial or the natural one , I have some pieces of Osage wood from which I want to make bows and arrows , I cut it in December , I split the wood to avoid tensions , how long do I have to leave it before I can start , , , carving , , at the moment it is stored at a temperature of 10 degrees
Good evening!
The thickness of the piece of wood and the air circulation in the space where it is stored are important. From what I've read (I've never seen such a wood) I understand that it is a very hard wood in which high stresses can occur when drying. With such wood drying to equilibrium moisture (12% in the area where Osange grows) can take many years. In theory it takes 1 year for every inch (some sources say every centimetre) of thickness of the plank (pieces of wood) + 1 more year. But, as I said, air circulation is also important. With good ventilation the time decreases. Very good is that the wood was cut in December, when it is with very low water content inside (if in the northern hemisphere).
If the pieces are small, you have in the link below some ways to speed up drying and stabilize it.
All the best!
https://revistadinlemn.ro/2018/06/13/stabilizarea-lemnului-verde-pentru-evitarea-craparii/
Hello,
I'm looking for 4 wooden cabinets 200X200x2500 some information?
Good evening, I have purchased 70 linear metres of planed planking and it is slightly damp from pine. The wood is naturally dried and has a moisture content of 20-25%. My question is:
I can move on to putting up the fence and treating the wood with primer, varnish etc.
Thank you in advance
Good evening!
The humidity is a bit high, it should be somewhere between 14 and 16% to avoid dimensional variations and significant wood movement. It is good to check the humidity, if you can, inside the wood. There are those moisture meters with 2 thick needles that stick into the wood. Sometimes the surface moisture is higher than the interior moisture that really matters.
The wood should be allowed to dry a little longer. By fastening the planks with nails, dowels or screw-bolts, you limit the movement of the wood. Tensions occur that lead to cracks or warping. Especially in winter, when the outside humidity drops very low and causes the wood to shrink.
You should let the wood dry in a ventilated and covered space (attic, shed). Make a stack at least 30 cm from the ground, with space between the planks (wooden sticks between them to avoid contact and allow air to circulate). If you don't have room in the shelter, you can also make a stack outside and cover the last layer with board. You must bear in mind that air must circulate between the planks, it is essential for drying.
All the best!
Hello! I am able to buy kiln dried lumber for an outdoor project with resinous lumber. From what I understand the advantage would be that the wood is more stable: it will crack less and warp less.
Is it possible for it to work again when exposed to outside humidity?
Hello!
Correctly dried wood is certainly more stable and will vary less dimensionally with the variation of humidity in the environment in which it is exposed (indoor or outdoor). The level of deformation also depends on the way it has been cut.
If it is not completely insulated with finishing products, so that it is no longer in contact with outside moisture, the wood will not work. It is almost impossible to achieve this performance because there are many wooden elements in a project and it is difficult to insulate them all very well on all sides. So the wood will work, but the dimensional variation will be much less if it is properly dried. In our country's conditions, the moisture content of wood used indoors should be 8-12% and that of wood used outdoors 14-16%.
My recommendation is to use the correct dry wood on any project. You will avoid many problems.
All the best!
What is the percentage of loss during drying in the dryer, if we turn 100 m3 how much is the result?
It depends on the initial moisture content of the wood and the one you want to reach. For example, if the initial moisture content is 30% and you reach 12%, the theoretical loss per 100 m3 is 18 m3. This is a purely theoretical calculation because, in volume terms, things are more nuanced because of internal changes in the wood due to water loss. In terms of weight, the loss is just over 18 kg because the water also carries other salts or colouring substances out of the wood.
Good evening, I happened to find the wood magazine. From the previous comments I understand what dry wood means and for that I thank you. As another follower I want to know how I can dry wood for making bows without waiting a few years for natural drying. Given that the pieces of wood needed are long, it remains to be seen how I will manage to make a 2m microwave. If somehow you can suggest another option...I am indebted to you. Have a good evening.
Hello!
The safest solution would be to treat in a dryer. Try to find someone in your area who has such dryers. Profile groups are a good place to start looking. There are carpenters who have made very efficient natural dryers and they also dry small amounts of wood of different species.
All the best!