Suppliers of products and services are the ones who usually give gifts to customers. It is a classic way of rewarding loyalty, encouraging the purchase of new products and, of course, a marketing and advertising activity. That's why when you see a customer so satisfied with the seller's performance that they feel the need to reward them, it's bound to get your attention. Such a reward the other way around caught my attention the other day. Two young entrepreneurs from Bucharest thanked the firm Danibrum for their help and the thank you note was accompanied by a bottle of whisky. I wanted to know what prompted this gesture so I contacted them and spoke to Angelo, one of the two friends.
Memory lost due to power fluctuation recovered by IT specialist Danibrum
It all started with a large voltage fluctuation that completely wiped the memory of the CNC in the machine. Angelo Èšuchiu and Sorin Ionita started their business 4 years ago. They met by chance and soon became good friends. The business started with a photo studio, Sorin being a photographer. They needed different sets for the studio and thought of buying a CNC to make them. They didn't have the money for a new one so they got one from a friend who closed his business. The CNC, a SERON bought a few years ago from Danibrum, did its job well. Gradually they realized that they could make a business in creating sets for other studios. The business grew, the passion for wood grew and other projects started to appear. Thus was born Kasa Concept, a company that makes wooden serving platters, lichen blanks, lighting fixtures and furniture pieces.
Everything was going well, they even made a website with an online shop, until one day, following a voltage fluctuation, the entire CNC memory was erased. Basically, all the operating parameters no longer existed in the mind The CNC became impossible to use. After the first moments of panic, they wondered what can they do? They thought of trying to contact the seller - Danibrum - but their hopes were slim because the CNC was long out of warranty.
"I called Reception, said I was having problems with a CNC and asked if someone could help me. I was immediately put through to Service. Here I spoke to the person in charge of the mechanical side who explained that it was not up to him and put me through to the IT and programming specialist. That's how I met Beni (Beniamin Brumă). And here's the best part. Although I didn't have a warranty, Beni helped me fix the problem and did it for free. And it wasn't simple at all because the SERON CNC model I had is no longer being manufactured, and the manufacturing company, which Beni contacted, couldn't help with a backup. I was on the phone with Beni for 3-4 hours, sent I think about 20-30 messages on WhatsApp, at some point I was embarrassed. Beni spent practically all that day with me, redoing the settings step by step, until he solved the problem.
What impressed me that I felt the need to make that gesture of thanks was that willingness to help the customer solve the problem. Unfortunately, you find that less and less. At the end of the day, you may find machine options elsewhere, but the service, the way you talk to people and help them, that's what matters. Thanks again to Danibrum and I would highly recommend them.", Angelo said.
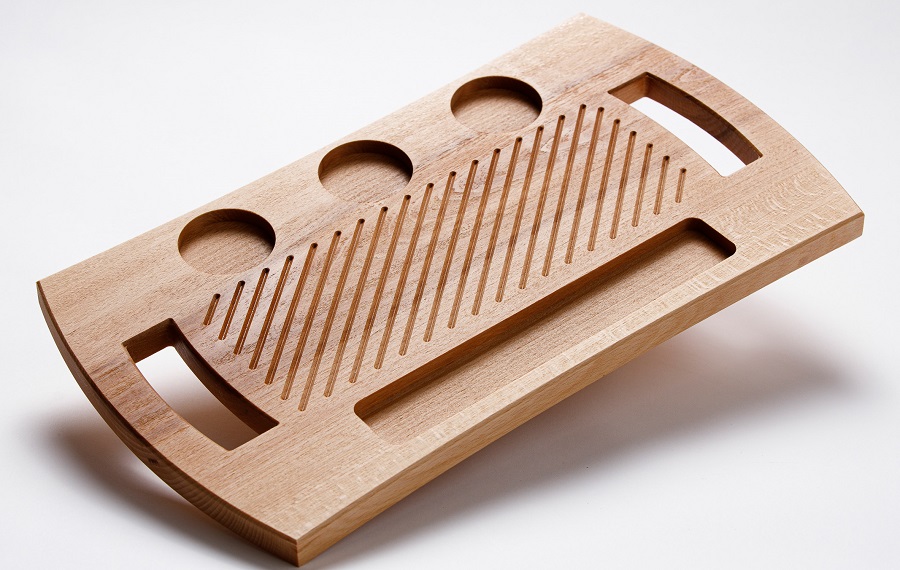
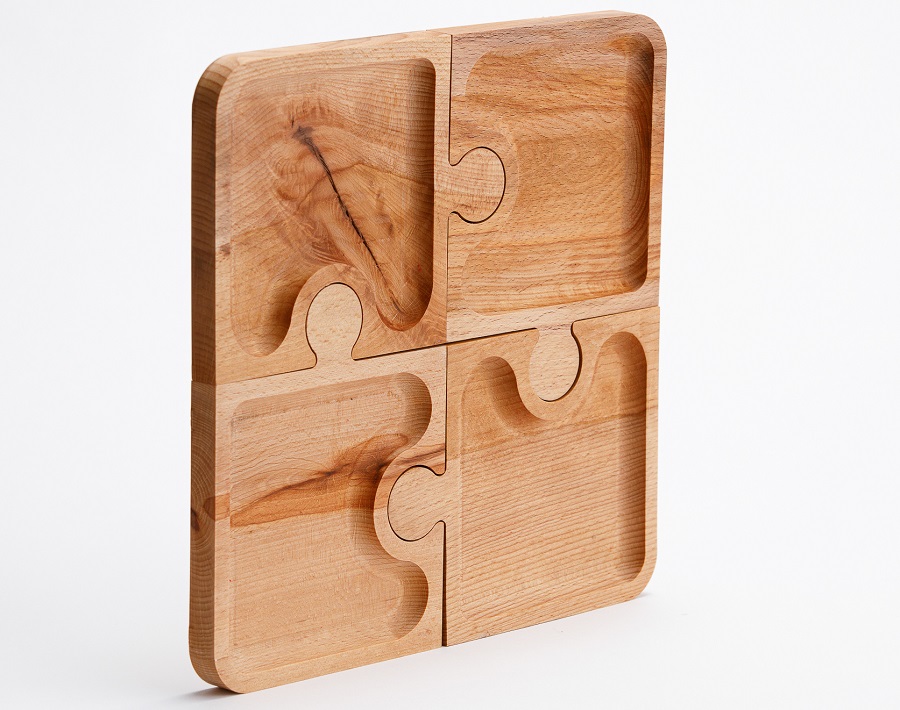
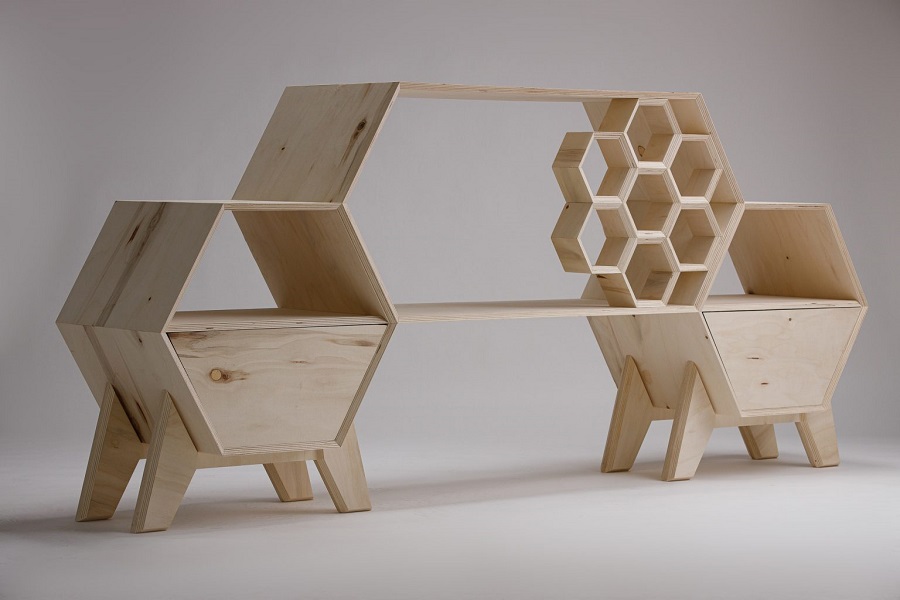
A simple, intuitive and cost-effective software
Because Angelo was so pleased with the service, I wanted to meet Beni. I've been to Danibrum many times. Mihai Vatavu, on Robert ColpoÈ™, on IonuÈ› Soroceanubut I never talked to Beni. So I called him. Modestly and without seeming at all to have made such an important gesture for the customer, Beni told me how he had to re-enter all the settings by calculating the steps for each pulse with an engineer from the manufacturer because he couldn't help him with a backup, the model being old and out of production for some years.
Beni is part of the Danibrum service team, responsible for IT and programming. He supports customers, especially online, helping them to solve problems quickly.
"People are in the factory, in the workshop, and they see that their machines won't start. They have orders and they're in a hurry and they need help as quickly as possible. Sometimes the problems are simple and can be solved immediately. I once had someone whose starter button wouldn't work. It was dust buildup. Other times they are more difficult and people can't tell me exactly what it is. The transition from traditional to computer-aided processing is not easy and some people find it harder to adapt. I tell them to send me pictures of what the display is showing or what is happening. Once I'm clear, I tell them step by step what to do and the problems are solved. People are happy that they are solved quickly."
Beni is very satisfied with the ASPIRE and V CARVE programs with which Danibrum CNCs operate. In his opinion they have the best quality/price ratio on the market. The software imports 2D and 3D drawings transforming each dimension into G-code (machine code) for CNC. The difference between the two softwares is that ASPIRE draws in 3D (after import, the drawing can be seen in 3D on the equipment display).
"The program is very user friendly, very intuitive, easy and simple to work with. It has a very large library of patterns included. To learn there are thousands of tutorials in English on the net. For our customers we also made tutorials in Romanian. They include people who don't know English and we want to help them."
Beni speaks passionately about what he does, about the team he is part of, he is very proud of it. All this passion and pride in being part of a high-performing team makes him happy, a happiness that he returns to the client. And from this comes referrals, new clients and friendships.
Add comment