Avec leurs formes fluides, les bateaux ont toujours séduit. Un bateau est une source de beauté, mais s'il est construit de vos propres mains, et surtout s'il est en bois, les choses peuvent devenir incontrôlables et entrer dans le domaine de l'addiction et de l'extase. Pour ceux qui sont prêts à prendre le risque, je vais vous montrer comment construire un bateau de A à Z. Étant donné que pour la plupart des Roumains, les eaux sont loin, j'ai choisi une construction légère, moins de 20 kilogrammes, un canoë qui peut être facilement transporté sur les barres d'une voiture jusqu'à la rivière ou au lac le plus proche. Un bateau est une chose délicate et spéciale, c'est pourquoi il ne faut pas s'étonner si le coût des matériaux s'élève à environ 1 000 lei.
Il existe plusieurs méthodes de construction de bateaux légers, mais en raison de sa simplicité, j'ai opté pour celle connue sous le nom de "stitch&glue". Cette méthode peut être abordée même par un constructeur débutant et s'apparente à de la couture. Le matériau nécessaire est le contreplaqué, dans lequel les pièces sont découpées, cousues avec de la saumure, collées le long des coutures et renforcées avec de la fibre de verre.
La première étape consiste à trouver un modèle. Il existe des sites web proposant différents plans à des prix abordables ou même gratuitement, mais pour les débutants, je recommande les plans simples de Michael Storer (https://www.storerboatplans.com/design/boatplans/) Le canoë que je présente est le Kymi River 16 (https://www.woodenboat.com/boat-plans-kits/kymi-river-16), une construction plus élaborée que j'ai choisie pour sa belle forme.
Une fois que nous avons le dessin, nous devons nous procurer nos matériaux. Pour la Kymi River, nous avons besoin de deux feuilles de contreplaqué de 4 mm d'épaisseur, d'une surface de 1220/2500 cm, et si nous parlons de bateaux, nous parlons automatiquement de contreplaqué nautique. Le contreplaqué nautique a la qualité de ne pas s'écailler sous l'action de l'eau ou de l'humidité, tant en raison de l'essence de bois (okoumé) que de la colle avec laquelle les feuilles de placage ont été collées. En Roumanie, le placage d'okoumé peut être acheté chez Holver à un prix d'environ 120lei le litre. Nous avons également besoin de fibre de verre et de résines époxy (époxy, pas polyester !) pour imprégner le tissu de fibre de verre. La fibre de verre est vendue sous forme de tissu d'un mètre de large. Elle est tissée en différentes épaisseurs et son poids spécifique permet de la différencier. Pour les canoës, nous avons besoin de fibre de verre pesant 160 grammes par mètre carré ou, si nous ne la trouvons pas, un maximum de 200 grammes par mètre carré, 15 mètres linéaires.
La résine époxy est un composé chimique à deux composants (la résine elle-même et le "durcisseur"). La résine est préparée pour l'imprégnation peu avant l'utilisation en mélangeant les deux composants dans les proportions indiquées dans la fiche technique du produit (EPIPHEN RE 4020 + CATALYST DE 4020), environ 5 litres étant nécessaires pour un bateau léger. Le tissu de fibres de verre et la résine époxy peuvent être achetés chez Polydis. Un mètre linéaire de fibre de verre coûte environ 10 lei et un kit de 5 litres de résine + durcisseur coûte environ 600 lei. Nous avons également besoin de 15 mètres de fil de cuivre d'une section de 1,5 millimètre carré (disponible dans les magasins d'électricité en tant que conducteur isolé Fy 1,5, qui peut être désisolé à la maison à l'aide d'un cutter), de papier de verre de différents grains et de quelques lattes de bois à acheter en cours de route.
Avec ces matériaux, nous pouvons nous occuper des outils. Pour couper le contreplaqué, nous avons besoin d'une scie pendulaire, et pour le reste, nous avons besoin des outils habituels : une défonceuse, une scie à main, une scie égoïne, un brevet, une perceuse, etc. Nous avons également besoin d'un espace couvert de 6x3m, à l'abri des intempéries. Comme la résine époxy ne polymérise qu'à des températures supérieures à 20°C, si nous voulons construire pendant la saison froide, nous devons avoir accès à un atelier chauffé (garage), alors que si nous construisons pendant les mois d'été, un hangar suffit.
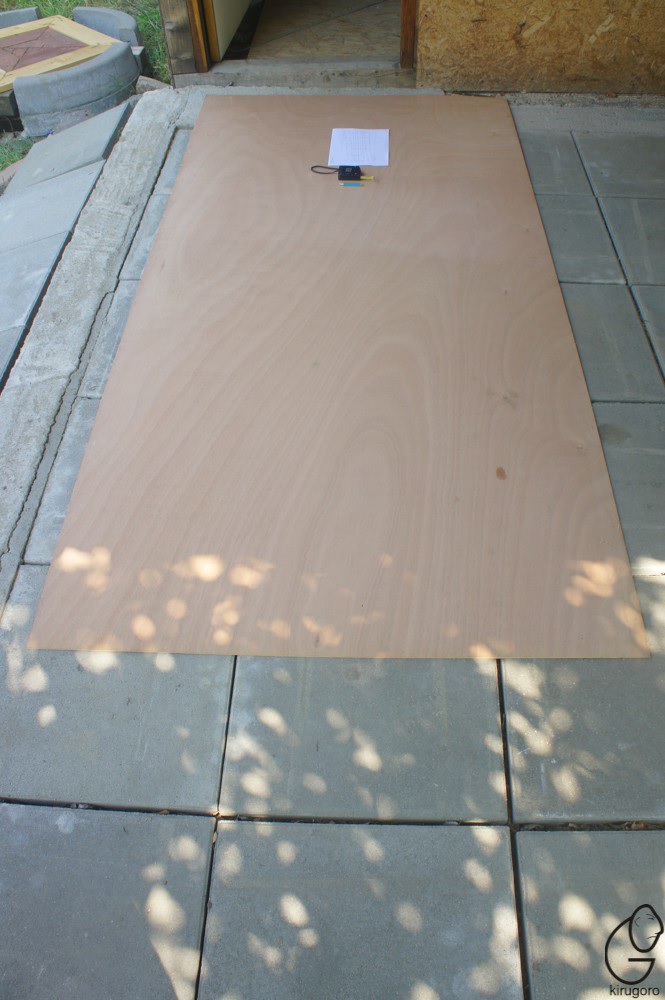
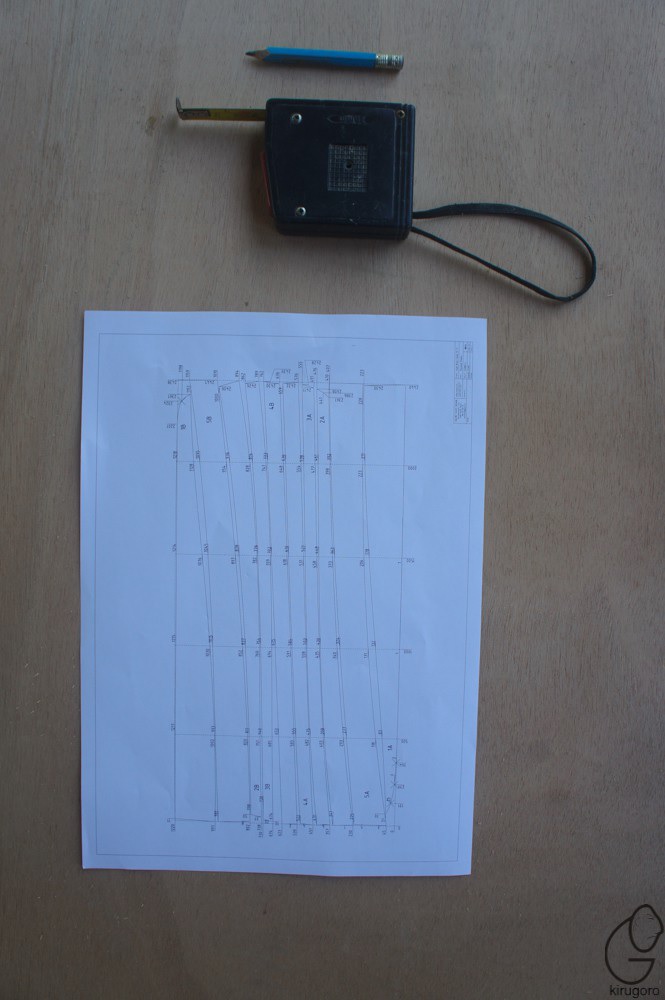
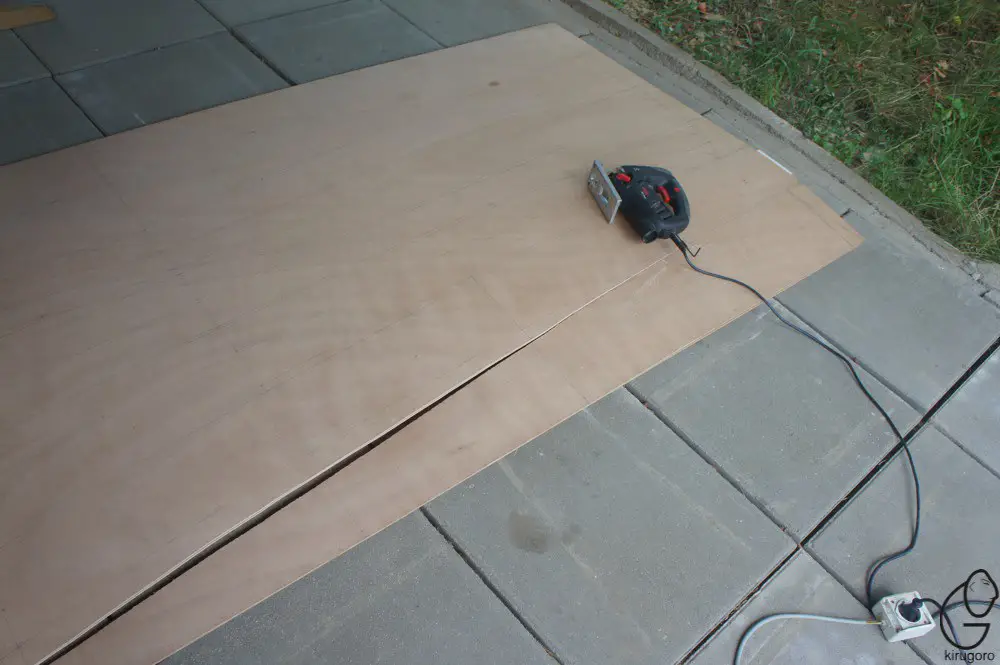
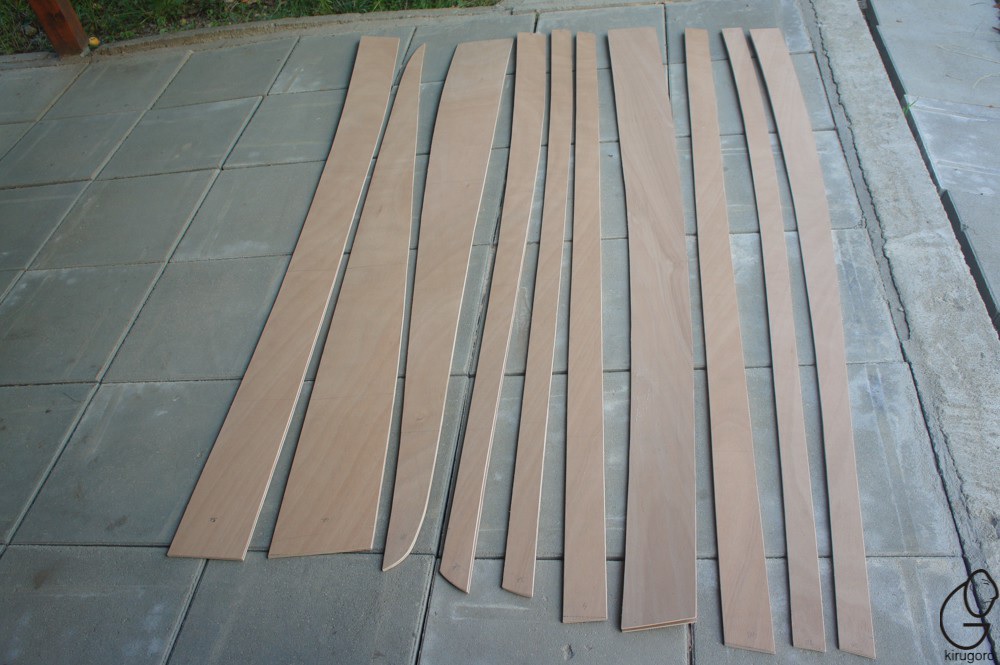
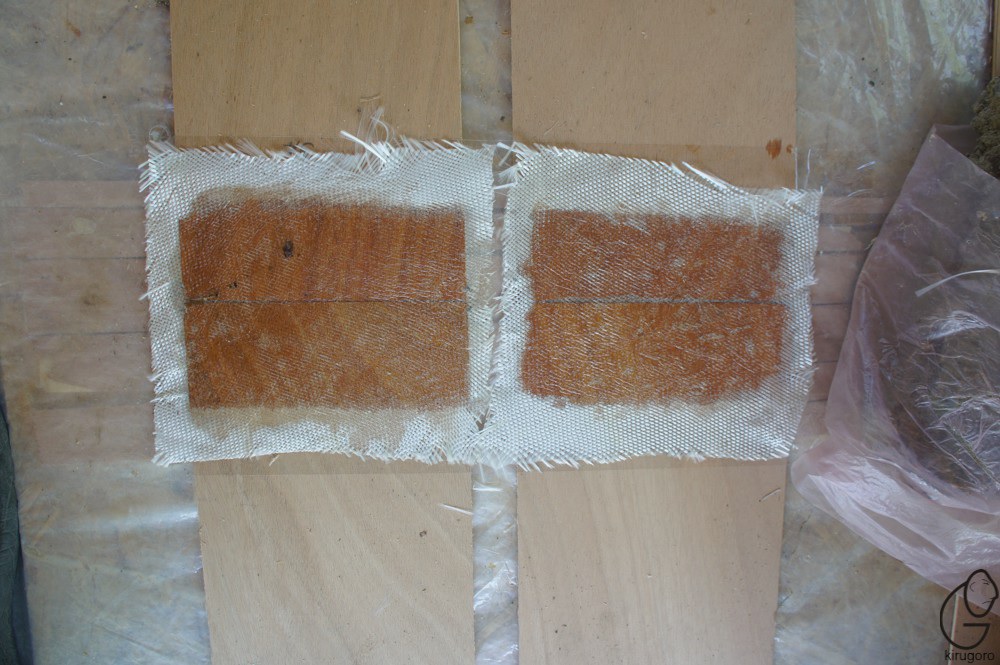
La première opération consiste à tracer les éléments du bateau sur le contreplaqué. Il y a plusieurs façons de procéder, mais les plans du Kymi River 16 sont décrits par un ensemble de coordonnées X-Y indiquées dans un plan. En transposant ces points sur le contreplaqué par des mesures à la règle, on obtient un ensemble de points que l'on relie ensuite par des lignes droites. Comme le bateau est symétrique, il n'est pas nécessaire de tracer les marques pour les côtés gauche et droit du bateau, mais nous tracerons une seule feuille de contreplaqué que nous superposerons et collerons à la seconde avec du ruban adhésif double face et nous découperons les deux feuilles en même temps.
A la fin de l'opération de découpe, on obtient des bandes courbes appelées filets. Comme le canoë mesure 5 m de long et que le contreplaqué ne mesure que 2,5 m, il faudra coller deux filets bout à bout, l'un dans l'axe de l'autre. L'opération se fait avec de la résine époxy et pour plus de solidité, le collage est "renforcé" par des bandes de fibre de verre, à l'avant et à l'arrière.
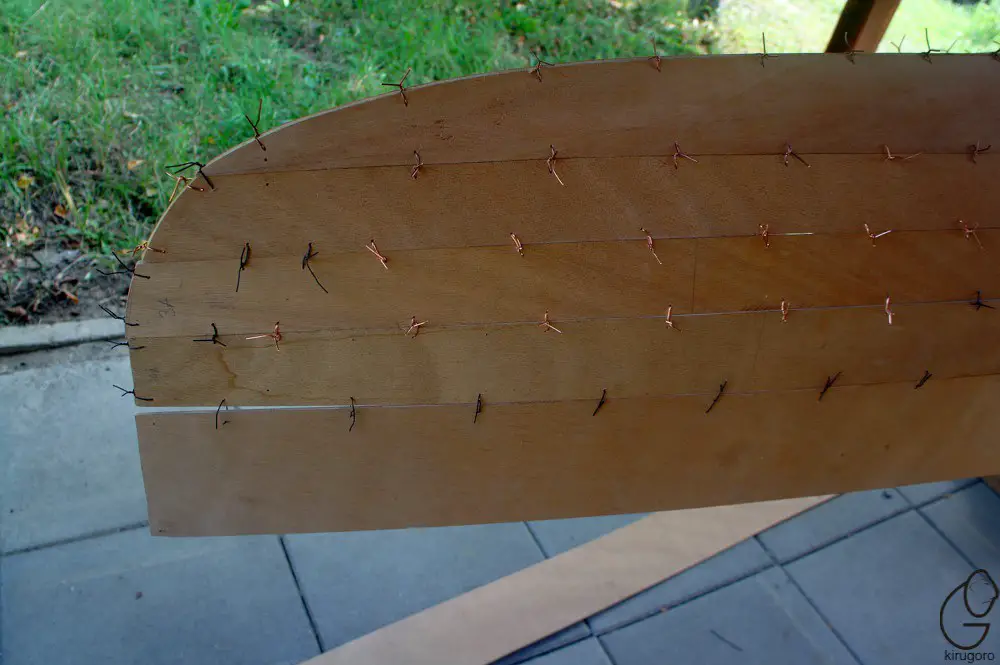
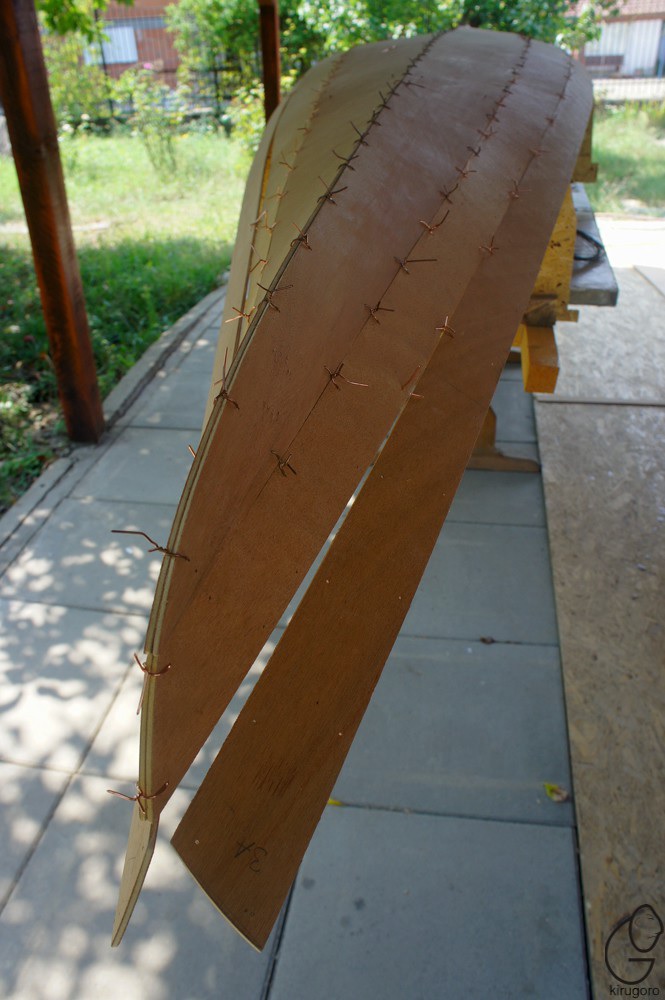
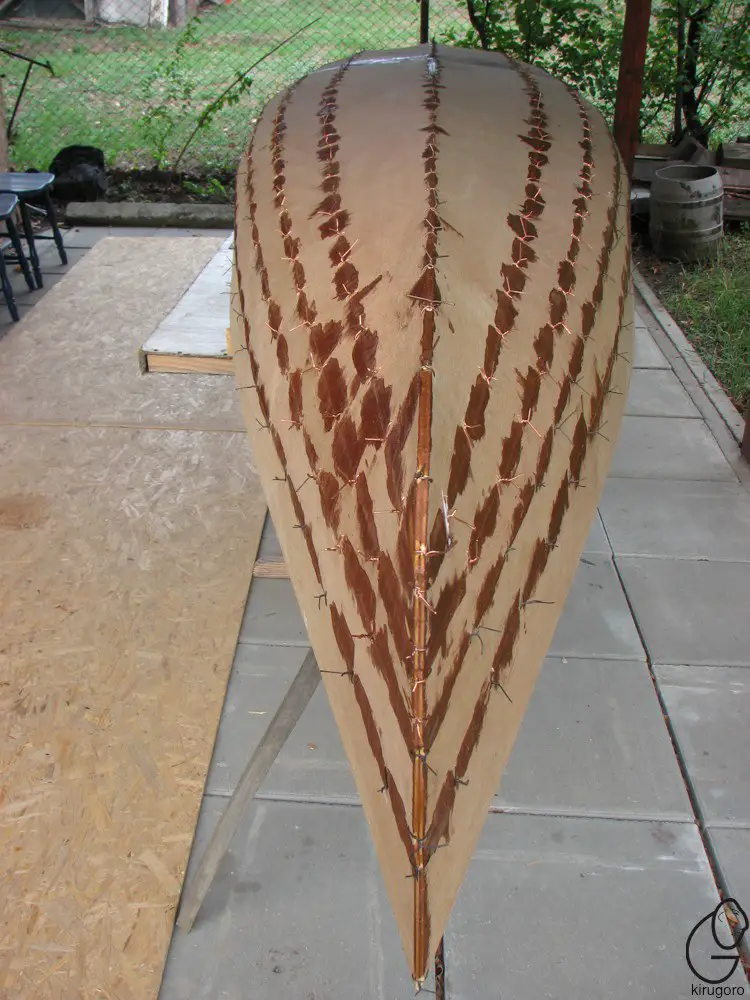
Pour passer à la forme 3D du bateau, il faut coudre le périmètre des filets de contreplaqué avec du fil de cuivre. La préparation se fait en faisant des trous équidistants (tous les 15 cm) dans le contour des filets, qui sont cousus par paires, deux par deux, avec des boucles de fil de cuivre torsadées ensemble. À la fin de ce travail, nous pourrons voir le bateau pour la première fois dans sa taille réelle et nous imaginer en train de nous y promener, ce qui soutiendra notre enthousiasme et nous incitera à continuer. Les fils sont un accessoire temporaire dont nous nous passerons une fois que nous aurons collé tous les filets au contour avec des cordons de résine époxy épaissie à la farine de bois (sciure fine).
Une fois que vous vous êtes débarrassé des fils, vous pouvez dire que vous avez votre bateau, mais il doit être renforcé par l'ajout d'une couche de fibre de verre, appelée "stratification".
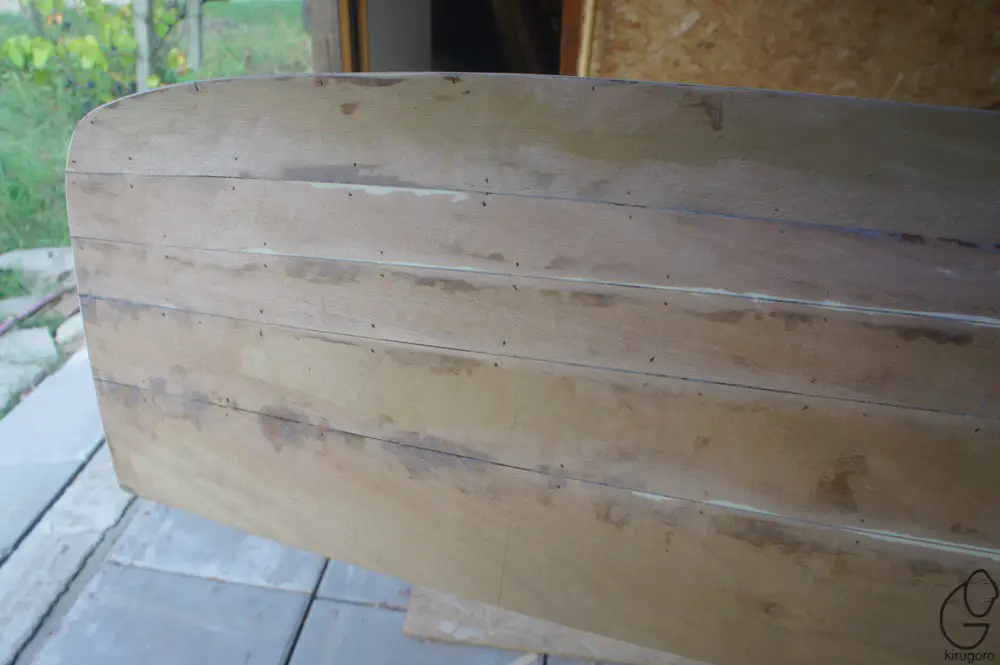
Poser le tissu de fibre de verre sur le corps en contreplaqué et le sécher à l'aide d'une brosse jusqu'à ce qu'il soit parfaitement plat et sans plis, puis verser le mélange de résine et de durcisseur dessus, en l'étalant uniformément sur toute la surface à l'aide d'une raclette, d'une brosse ou d'un trafalquet. La résine devenant visqueuse au bout de quelques minutes de mélange, préparer des doses successives, suffisamment petites pour avoir le temps de s'étaler avant de durcir. Lorsque toute la surface du canoë est recouverte de résine, attendez environ 10 heures et appliquez la couche suivante, en répétant l'opération.
3 à 5 fois (ou autant de fois que nécessaire, jusqu'à couverture totale).
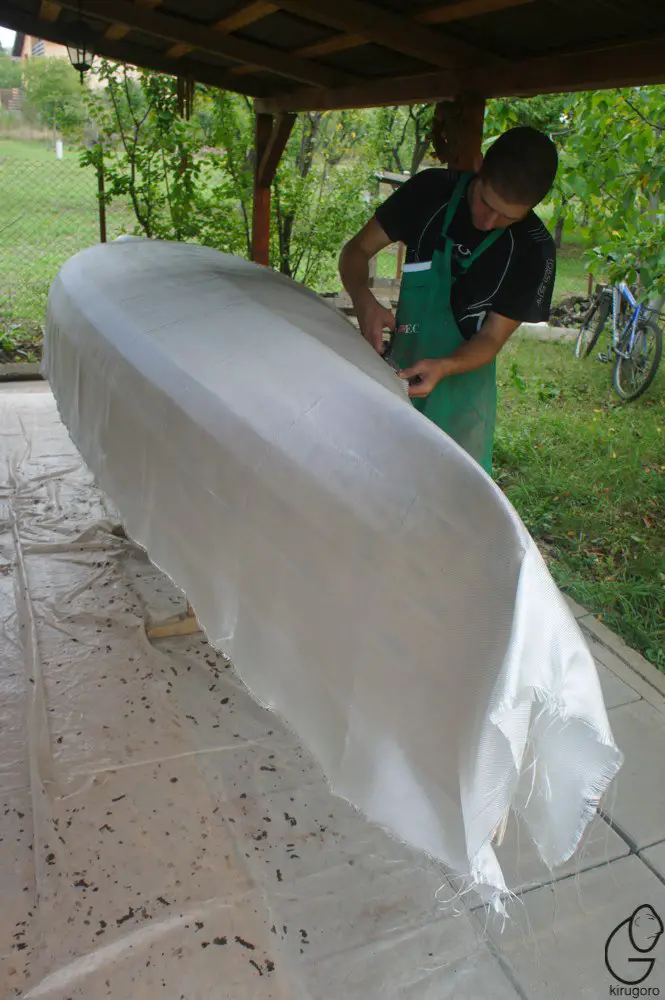
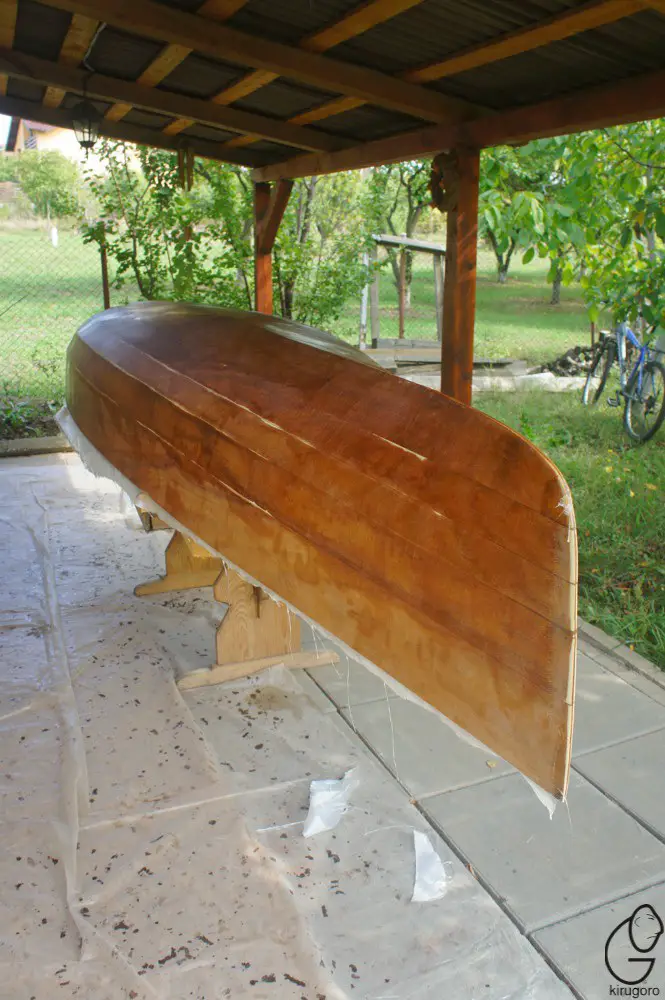
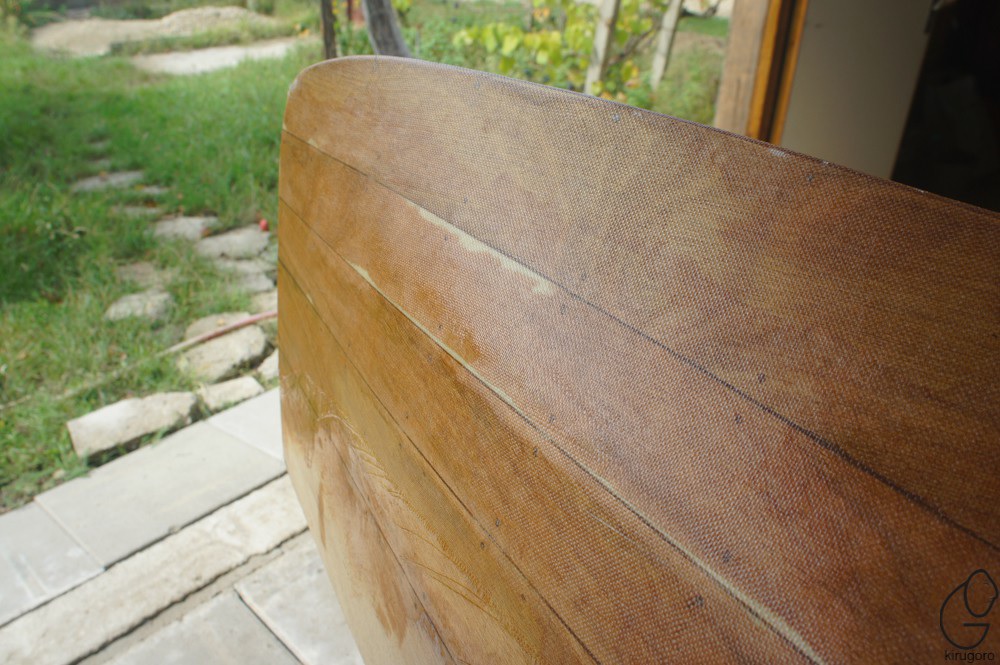
Une fois imprégné, le tissu de fibre de verre devient parfaitement transparent, de sorte que le bateau ressemble à du bois verni. Si vous souhaitez le colorer, il vous suffit de mélanger des pigments de peinture (poudre) à la résine.
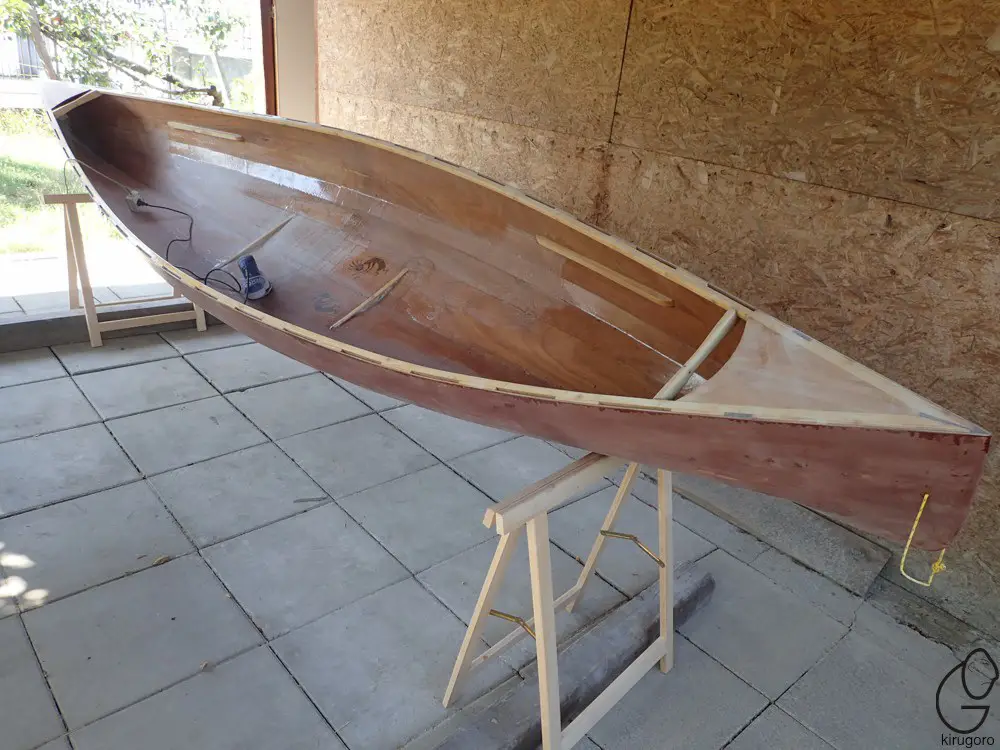
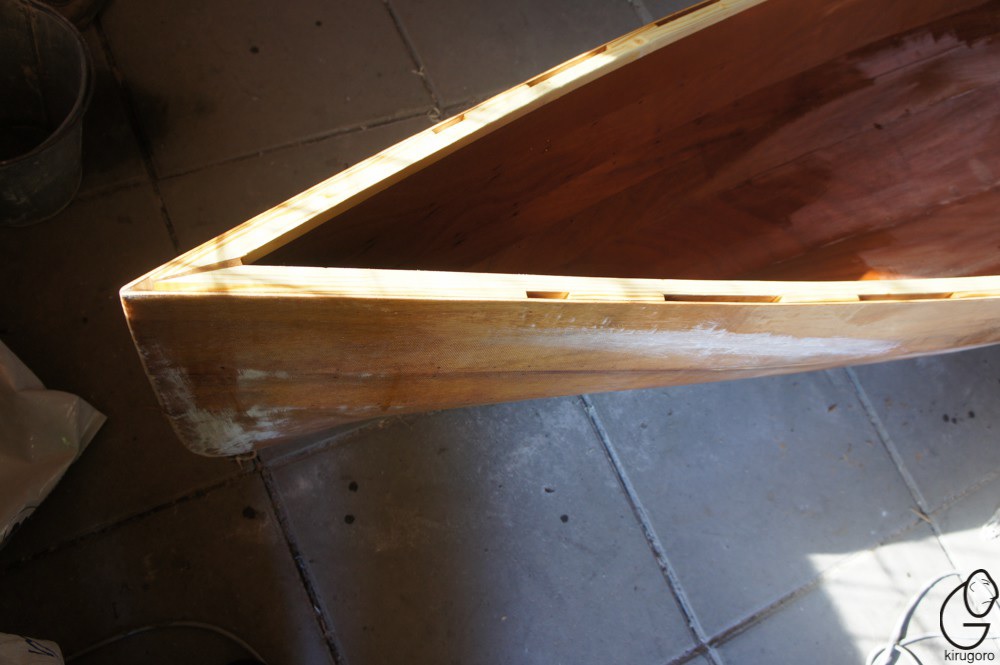
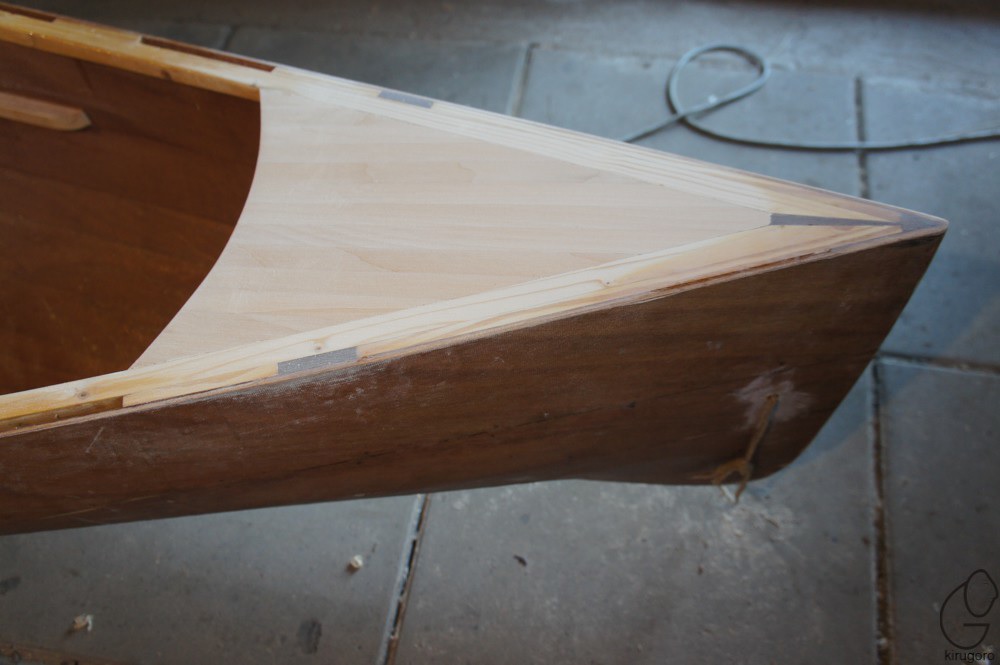
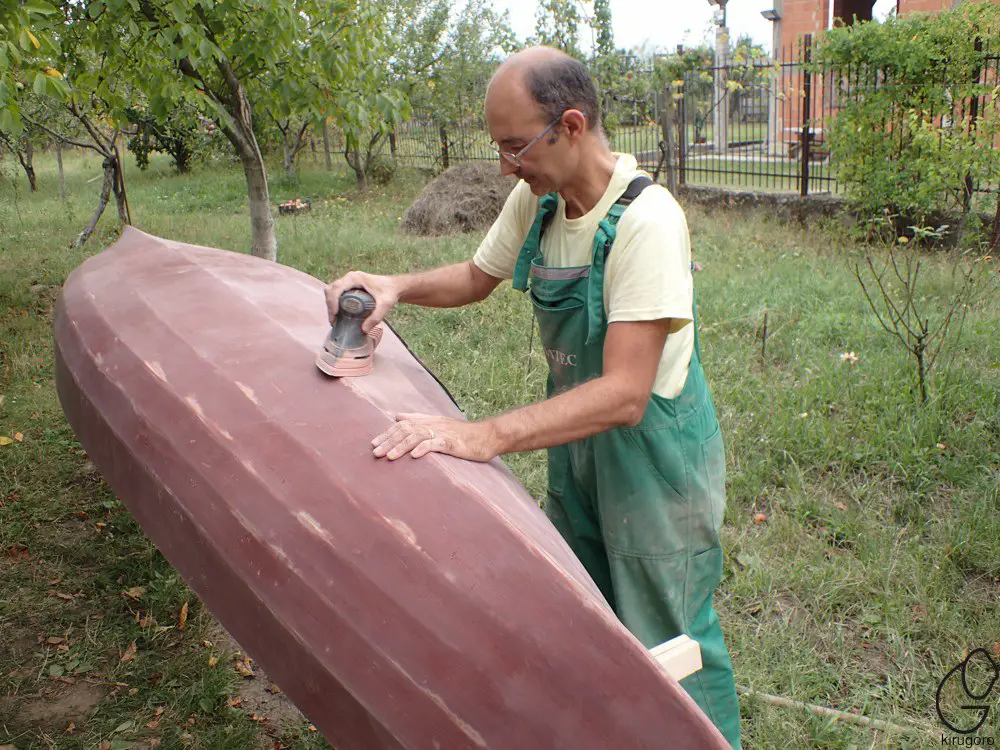
Deux jours après la dernière application, la résine est suffisamment polymérisée pour continuer le travail et on peut procéder au renforcement des bords en collant des lattes de bois de 25x25mm appelées margelles le long des bords, et des ponts triangulaires peuvent être réalisés à l'avant et à l'arrière à partir de lattes ou de planches de bois. Après cela, il ne reste plus qu'à finir la coque du bateau avec du papier de verre à grain de plus en plus fin et une dernière couche de vernis de yacht protégé contre les UV.
Le canoë est terminé et prêt à être mis à l'eau, mais pour une première pagaie, nous avons encore besoin de sièges pour les pagayeurs et, bien sûr, de rames. Traditionnellement, les sièges sont fabriqués sous forme de cadres en bois à l'intérieur desquels le siège est tissé avec un fil synthétique non extensible. Comme le sapin ou le pin n'offrent pas la résistance nécessaire, on utilise des bois durs, de préférence du frêne.
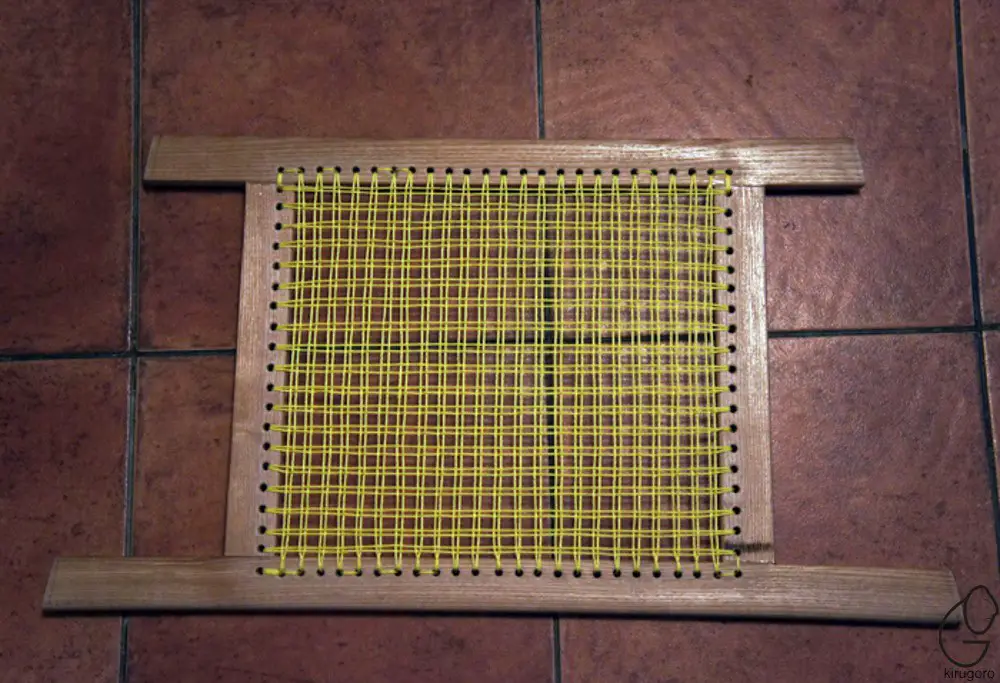
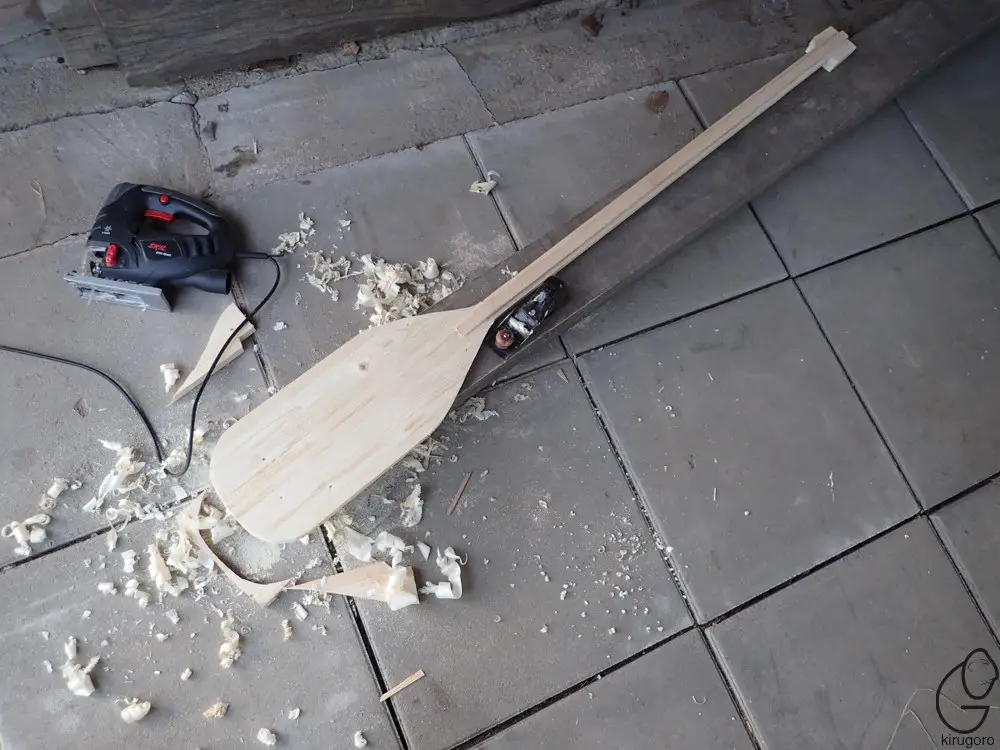
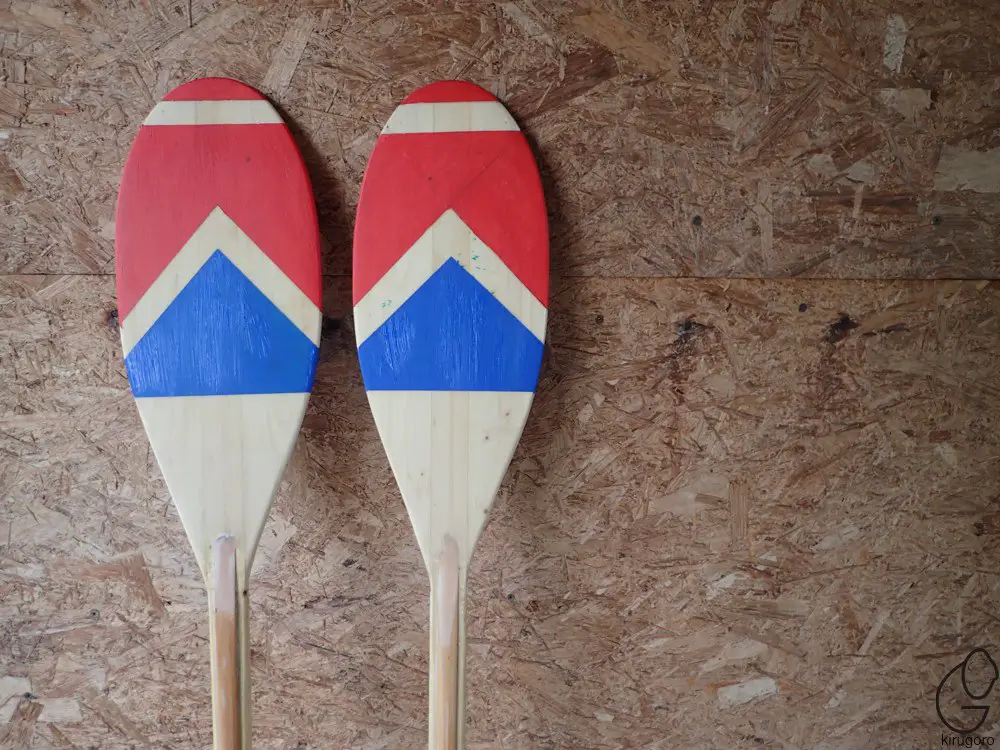
Les pagaies sont constituées de lattes de pin collées en forme de panneau, puis moulées avec du papier de verre et du moulage au papier de verre. Pour protéger le bois de l'eau, les pagaies sont entièrement laminées avec de la fibre de verre et recouvertes de résine époxy comme le corps du canoë. Si vous n'êtes pas trop pressé d'aller sur l'eau, il est possible de faire des dessins avant d'appliquer de la fibre de verre sur les plumes des avirons, qui seront envoyés au constructeur.
Voilà, c'est fait. Nous sommes les heureux propriétaires d'un bateau de plaisance qui nous a donné satisfaction et nous a permis d'améliorer notre estime de soi. J'ai dit au début de l'article qu'un bateau en bois fait à la main crée une dépendance : dans la plupart des cas, le premier bateau construit n'est pas le dernier. La plupart des marins s'arrêtent lorsqu'ils n'ont plus de place pour stocker leurs bateaux, mais il y a eu de nombreux cas où de beaux bateaux ont été vendus pour rien, juste pour libérer de l'espace.
Ajouter un commentaire