The term fondo-finitura is imported from Italy. It is formed from the word fondo, which means primer, and finitura, which means varnish. So, in translation, primer-lacquer. The Romanian term for such a product is universal lakeBut the Italian version has caught on so well that there's hardly anyone in the industry who's heard of universal varnish.
As the name suggests, a primer-finish is a product used to finish wood as both a primer and a varnish. It sounds like a miracle product that, when applied layer upon layer, solves problems without having to keep changing the products you're working with. It's the way finishing is done for DIY projects, where a single product is applied in multiple coats to protect and varnish the desired object. So why don't they just use only such products in the industry as well, and continue using different materials? Why would people want to complicate their lives? I set out to answer these questions in the following.
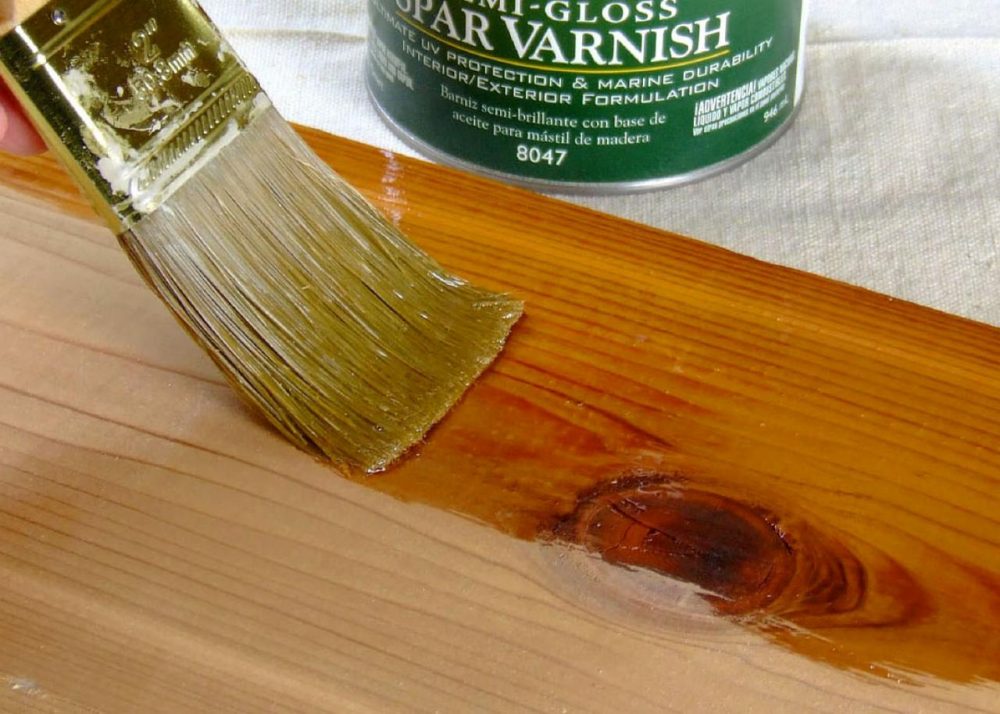
Why a universal varnish was needed
Bottom-coating products have emerged from the need for simpler technologies without having to constantly change materials in spray guns, pumps and other equipment. They can work up to the finished product by applying successive layers of material. They can be of any type, nitrocellulose, polyurethane, acrylic, solvent-based or waterborne. They are used both as a primer and as a varnish, being basically a hydrid product which takes on the properties of both materials.
To better understand where problems can arise when using such a material, let me remind you what primer and varnish are used for. The primer is used so that the varnish film will grip very well to the wood substrate and provide a consistent surface that can be sanded to remove roughness and provide a perfect support for the final varnish. The varnish is applied on top of the primer and gives the varnish, in addition to a nice look and feel, resistance to scratching, mechanical shocks and staining.
The plusses and minuses of the universal varnish
For a filler to be used as a primer, it must be easily sandable. This means that its resistance to scratching and mechanical shock must not be very high. As it is also used as a varnish, it must have scratch resistance, which will make it more difficult to sand as a primer. This is also where the 'weaknesses' of the material come in: it is harder to sand as a primer and less scratch-resistant as a varnish.
In DIY projects, the person who starts "tinkering" with something has the time to work on the object until the desired result is achieved. The resulting object does not have to be handled by several people, packed, shipped, transported, kept in warehouses until it reaches the customer, so the risk of scratches and bumps on the film is reduced. In industry, however, technologies have timescales that have to be respected and products have to meet certain quality requirements. They are handled several times, packed and transported to different customers, where they are handled and stored again. The journey to the end customer is long and the risks of damage to surfaces are higher.
I do not want you to understand that this is a recommendation not to use such products. Because, as I have already said, they have their advantages. Their use on specialized equipment is simpler, they reduce the losses caused by changes of material from one stage to another, they eliminate mistakes caused by confusion. You just have to weigh up the advantages and disadvantages of using them and make an informed choice.
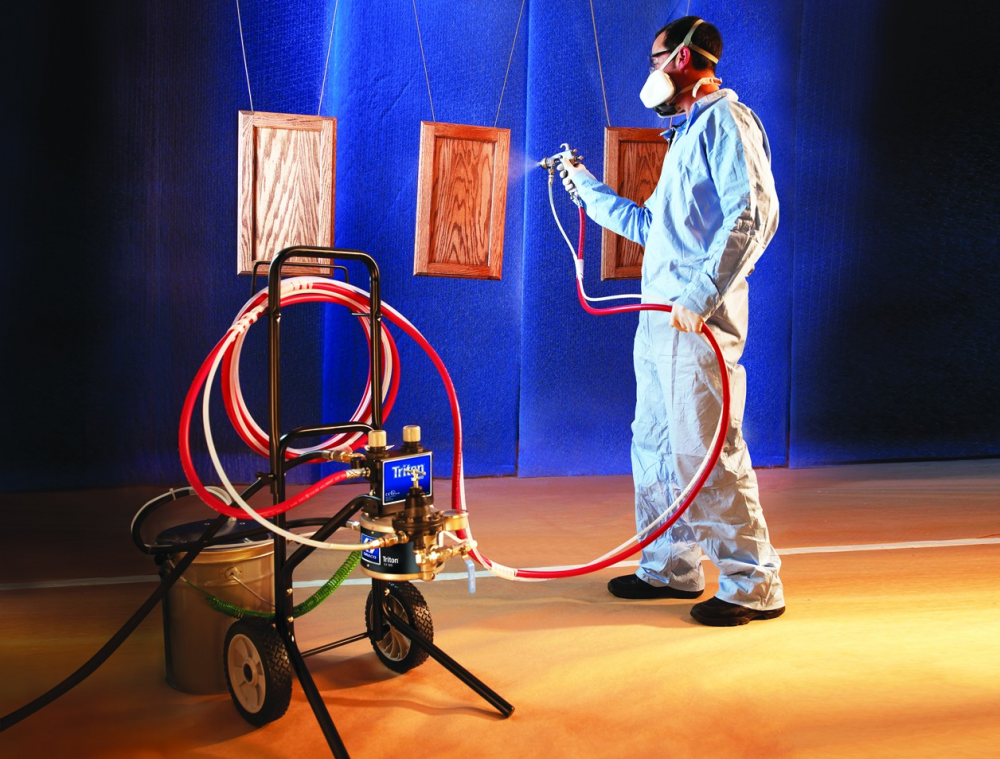
I hope you find the above information useful. As always, additions are welcome. And if you have any questions or queries, please leave them below in the space provided. I will be sure to reply.
Don't ever stop doing that.