How to apply varnishes recommended in the product datasheets reminded me of an application method that is unfairly treated with less confidence than other application methods. I am talking about pouring, a method much used in the past and much less so now, although its use does come with some advantages.
The main advantage of mold application is the reduction of material loss. The most commonly used application method is spraying, but the amount of material lost varies from 20-25% for whole panels to 60-100% for more complicated objects. This loss is substantially reduced in molding.
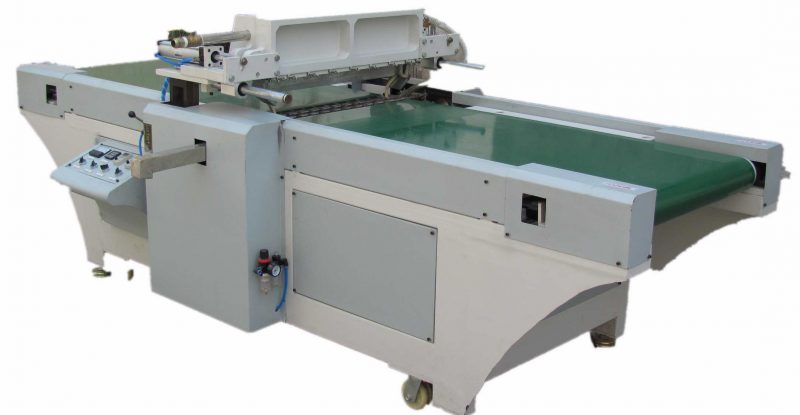
photo source szjxuv.com
The molding is done by a molding machine, which is generally clamped in a more complex finishing line, but can also operate with only 2 conveyor belts. The principle of the machine is to apply the lacquer or primer in the form of a curtain. The main parts of the machine are the conveyor belt and the varnish pouring heads. Very little material is wasted because everything that does not fall on the finished object is recovered and reused.
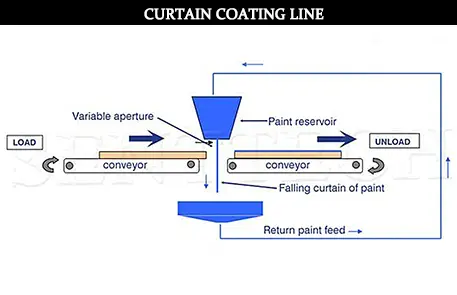
photo source: infrared-dryer.com
Depending on the design, the machines may have one or more molding heads. For example, multi-head machines are used for the application of mixtures that have a short pot-life, such as polyester products.
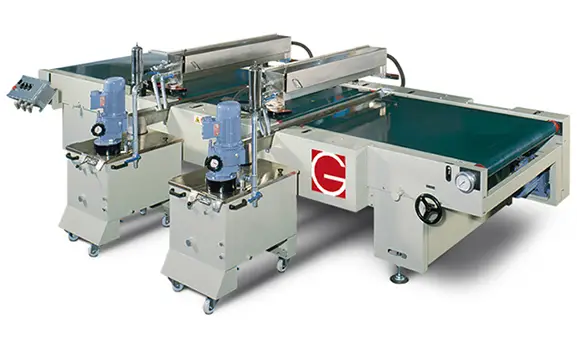
photo source: giardina group.com
Heads can be fixed or removable. The advantage of the latter is that they are easy to clean.
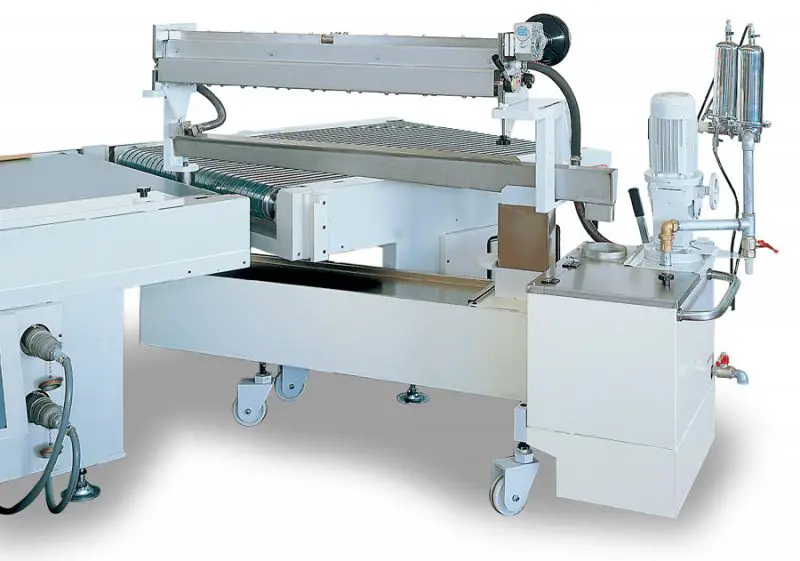
photo source: ceflafinishing.com
The material in the mold heads can be entrained by gravity or pressure. With gravity machines, the material simply "falls" into the head and forms the varnish curtain, all due to the force of gravity. In pressure machines, of course, pressure is used to get the material into the molding heads.
Casting, like Valuationare used for flat surfaces. This is also their main disadvantage. But, in contrast to leveling, if the objects to be finished are placed at a certain angle on the conveyor belt, edges and certain surface patterns (door planks, branch patterns, etc.) can also be finished.
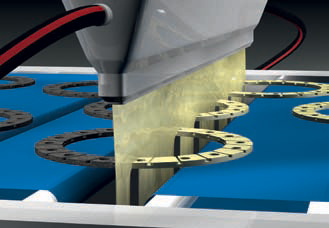
photo source: burkleamerica.com
The molding machines are highly productive, with conveyor belt speeds up to 150 m/min. By modifying the slit through which the material falls, the consumption can be adjusted between 60 and 450 g/mpm. Nitrocellulose, hydrodilutable, polyurethane, acrylic, acid-hardening, polyurethane, acrylic, etc
Another disadvantage of the molding machine is the sensitivity of the varnish curtain. It can "break" if there is a draught in the room or if, in an attempt to greatly reduce consumption, the slit is opened very slightly. When the curtain breaks, the lacquer is no longer applied to some of the parts, the more so the higher the speed of the belt. This is why the machine should be placed in areas without current and once the slit opening is fixed, it should not be changed during application.
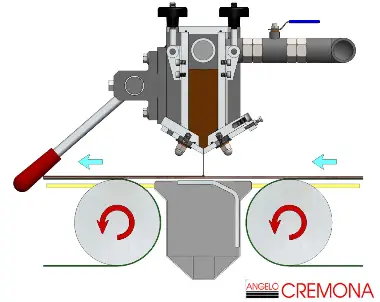
photo source: angelocremona.it
When solvent-based products are applied, their viscosity increases during application due to faster solvent evaporation. Therefore the viscosity is checked more often and adjusted if necessary by adding thinner. The viscosity in pouring is higher than in spraying, reaching 16-28 seconds.
Indeed, the molding machine is not an option when we have to finish wooden chairs or balusters, but it can be a good choice when finishing doors, flat elements, frames and other such wooden objects. You can also consider it if there are many small flat elements in your production profile, especially since there are machines of various sizes, even the laboratory version.
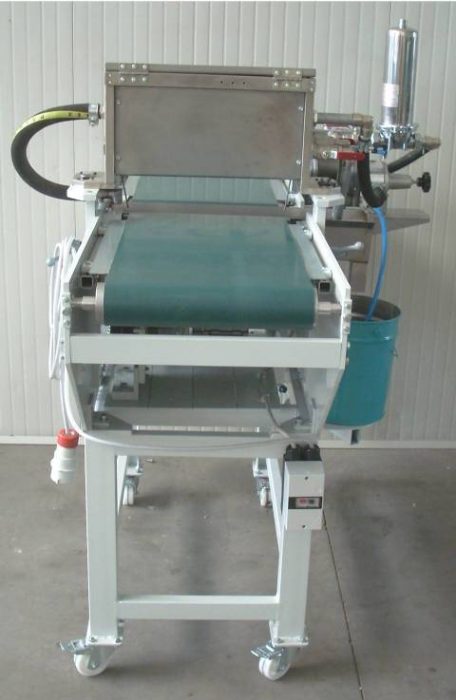
photo source: venetafinishing.it
Add comment