There are situations when it is necessary or desirable to reduce the amount of solvent-based products used. Protecting the environment demands it (reduction of VOC emissions), the increased risk of fire is also to be taken into account, improving working conditions is also a plus. But how do you do that when you already have contracts signed on models you can't change? How to do it "on the fly", while maintaining the quality of the products and the original look of the finish? Combination finishing, using both water-based and solvent-based materials, seems to be the answer.
If the furniture is colored but transparent, stains are used for staining. With simple solvent-based stains, the amount of VOCs is very high, above 90%. Replacing them with water-based stains is a solution. After complete drying, they can be coated with solvent-based products without any incompatibility between coats.
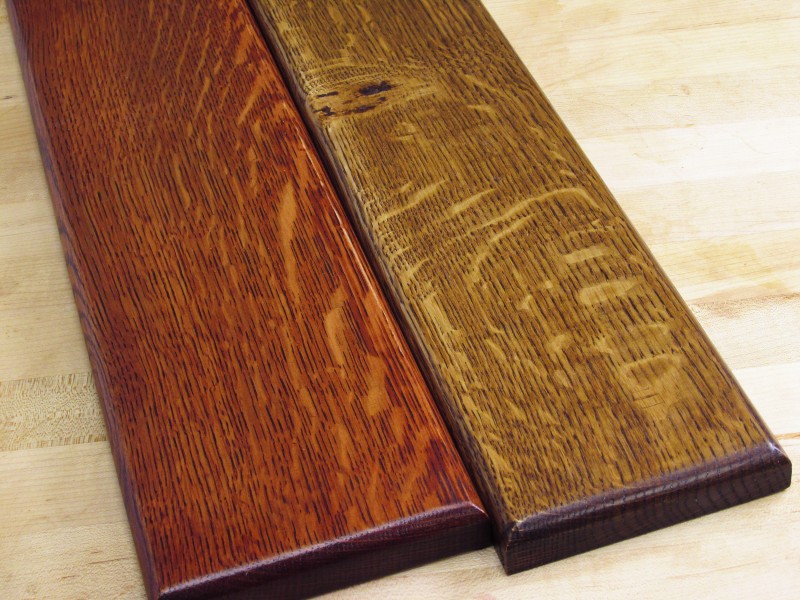
But there are drawbacks. One of them is deep absorption, which leads to a more pronounced lifting of the wood grain, making sanding between coats more difficult. Deep absorption can also lead to more intense staining or stains. Another drawback is a longer drying time. All these disadvantages can be overcome by using a mixture of water and products specially formulated to reduce absorption and speed up drying. The price of the bath will increase compared to using only water as a solvent, but will be offset by the reduced cost of repairing the defects.
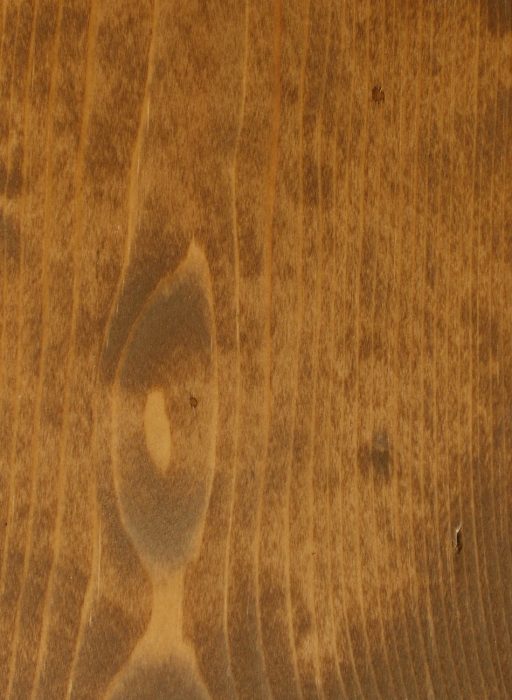
By far the easiest way to reduce solvent emissions and therefore the amount of solvent used in production is to change the bath to solvent. Indeed, color copying may take some time, but it is not impossible to do. The other options, i.e. replacing the primer or varnish, can cause much bigger problems. The waterborne primer changes the color of the bath a bit, so the bath will have to be changed as well. In addition, some components of the stain may also be soluble in water, leading to "bleeding", i.e. the water in the stain dissolves the stain and causes it to migrate.
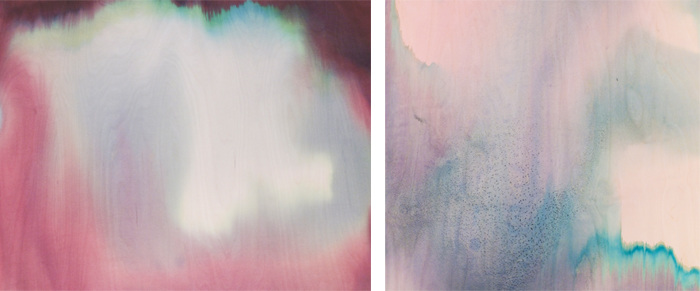
Changing the varnish can also create problems, even if the same gloss is maintained. Sometimes water-based varnishes don't have the same transparency as solvent-based ones, and the stain may be different.
Combination finishing can also be used for an opaque finish. In this case it is easiest to change the solvent-based primer for a water-based one. Solvent-based varnish can be used over waterborne finishes, provided the primer is properly sanded before application. Replacing the primer makes it important to reduce the consumption of solventborne products, as it is normally the primer that is used in larger quantities, with the lacquer being applied only at the end.
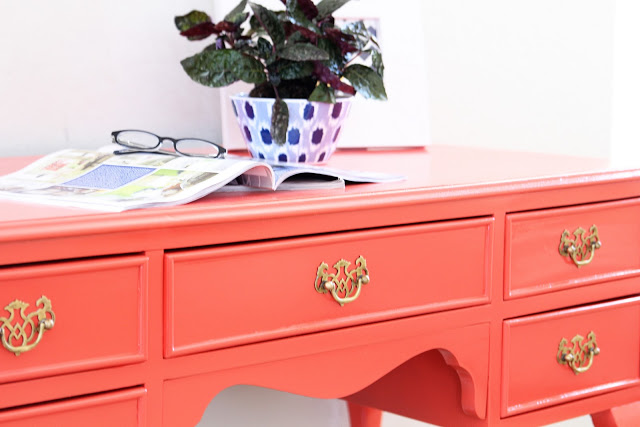
If the solvent-based primer is curing it is best to use a similar waterborne primer. For example, a tinted opaque finish can be done using catalyzed white waterborne primer, 2-3 coats, followed by the usual solvent-based tinted clearcoat. The appearance will remain unchanged and you have achieved a significant reduction in emissions.
Another example might be the antiqued matte finish. One finish that I recently reproduced, precisely because of the desire to reduce solvent-based products, was originally done with white primer, patina and clear varnish, all solvent-based. White primer was replaced with white waterborne primer, leaving the rest of the finish unchanged. Acrylic varnish on solvent, used to protect the effect from yellowing over time, applied at the end, kept the appearance of the finish unchanged.
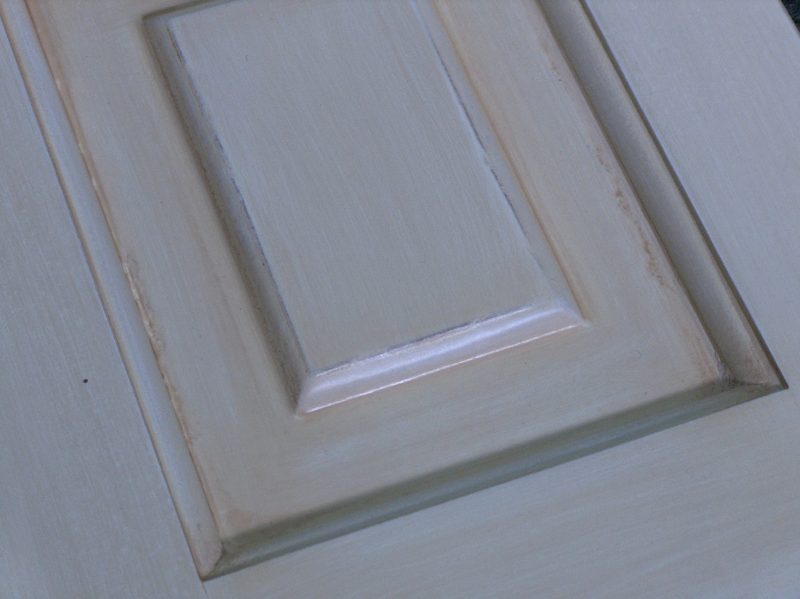
These are just a few examples of combination finishes that can help you reduce the amount of solvent-based materials used without changing the appearance of the finish. It is always a good idea to ask your finishing material supplier about material compatibility whenever you want to make such changes, so there are no surprises.
Add comment