I recently had a very interesting discussion with Jean-Michel Jeanselme from Sames Kremlin and Gabriel Mănoiu from Falk Consulting, the company that represents them in Romania, about the application of electrostatic varnishes. Sames Kremlin, part of the EXEL group, is a French manufacturer of professional spray guns and equipment. Our meeting was a follow-up to the discussion about electrostatic systems with Gabi Manoiu last year at BIFE SIM, where we talked about their efficiency and safety in operation, as well as their use by both large and small manufacturers.
The other day Jean-Michel Jeanselme, Director of Development in the Europe-Middle East-Africa (EMEA) region and a very good specialist in electrostatic field application, was on a business visit in Romania. Gabi remembered our discussion and suggested a meeting to find out more about this way of applying varnishes on wood, for some seemingly impossible given the insulating properties of wood.
The principle of electrostatic field application has been discussed extensively in article dedicated to this type of varnishing. It is based on the movement of varnish particles along the lines of an electromagnetic field formed between a negatively charged gun (or bell) and a positively charged object. The electrically charged particles are attracted to the object, give up their electric charge and are retained on its surface. This results in a very good application efficiency, as the material also settles on the back of the object to be finished, even if the application is only from the front. And all that material that goes on the back of the object is actually the overspray, i.e. the material that would be lost in a normal spraying. The application is done with an electrostatic gun or a system called a bell, and there are differences in performance, quality and maintenance between the two types of application.
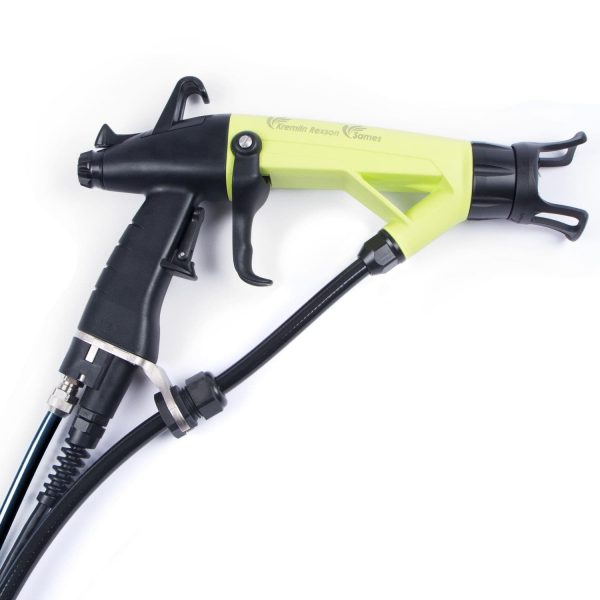
photo source: directindustry.com
As I have said, the yield of such an application is very good, which also prompted me to write this article. Electrostatic field application has come a long way and has become very safe. They are talking about yields of 95% and the application of waterborne products in complete safety, which is almost unbelievable in the idea that it is water and electricity taken together.
For electrostatic application certain conditions must be met:
- Wood moisture content should be between 6 and 10-12%;
- the viscosity of the products to be applied must be 70 sec Ford 4 cup for spray application and 50 sec Ford 4 cup for bell application;
- the installation must have a grounding system;
- the installation must be kept continuously clean.
Using electrostatic systems it is possible to apply 1000 cc product/min, if the application is made with a spray gun, and 500 cc/min, if the application is made with a bell system. The quality of the film is better with bell application, but the operator must be trained, have a thorough knowledge of the field and maintenance must be continually maintained. Material transfer efficiency is 95% with the bell and 80-85% with the gun.
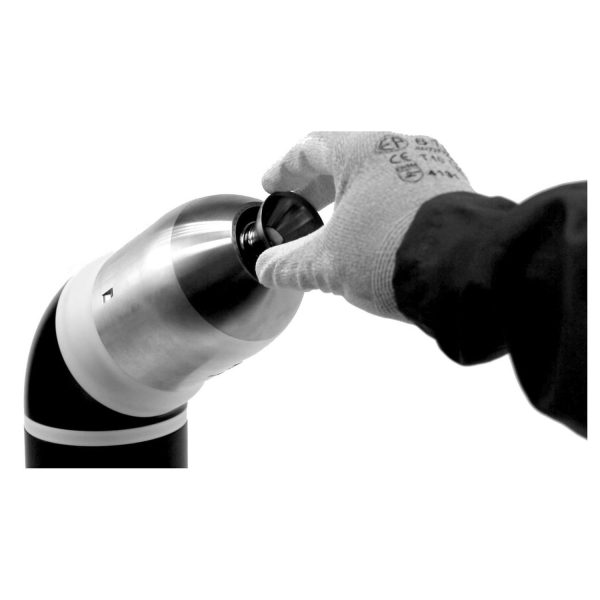
photo source; directindustry.com
There are also options for small manufacturers for whom large, sophisticated installations are not an option. Basically, application systems fall into 3 categories:
- simple pistols - application is done by a person handling the pistol;
- reciprocating - application is done by a robot with a vertical translation movement;
- anthropomorphic robots - the application is done by a robot that copies the movements of the human hand, applying the material from any angle and can be programmed to repeatedly apply the material to any shape.
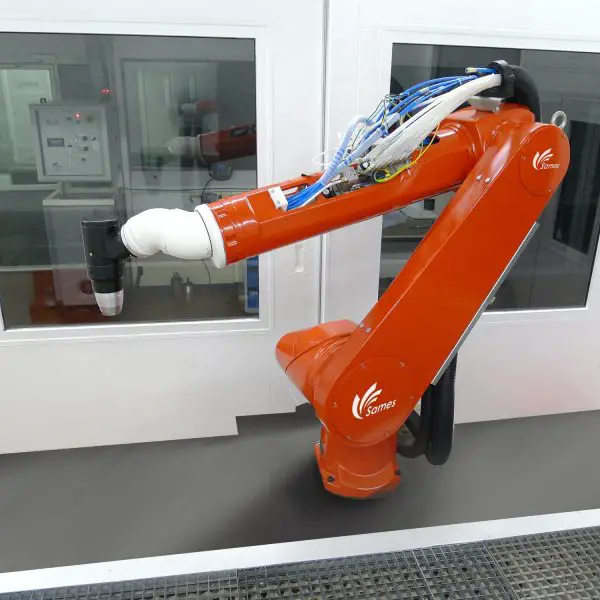
For all these categories of equipment there is an electrostatic field version. So it is possible that a small manufacturer, who spray finishes complicated shaped objects with very high material losses, may buy a gun with electrostatic application.
The number one priority of these systems is safety first. When applying solvent-based products, the electrical charging of the material takes place only at the tip of the gun, virtually only 5 cc of product contains electric current. The whole thing is full of sensors, and at the slightest change in voltage a signal is immediately sent that stops the entire installation, so that the next 5 cc of material will no longer be electrically charged. The message is sent in nanoseconds.
In waterborne products the material is fully charged with electricity, the water carrying the electric current. For this reason the safety systems are much more numerous and often duplicate each other for added safety. Again, at the slightest change in voltage, the generator is shut down in nanoseconds. The application system and the material container are insulated with grids. There are electrical discharge modes in all areas of the installation. The folks at Sames Kremlin are very proud of their coaxial cable that both conducts and discharges electricity. With its help the material left in the path when the generator is switched off can also be electrically discharged.
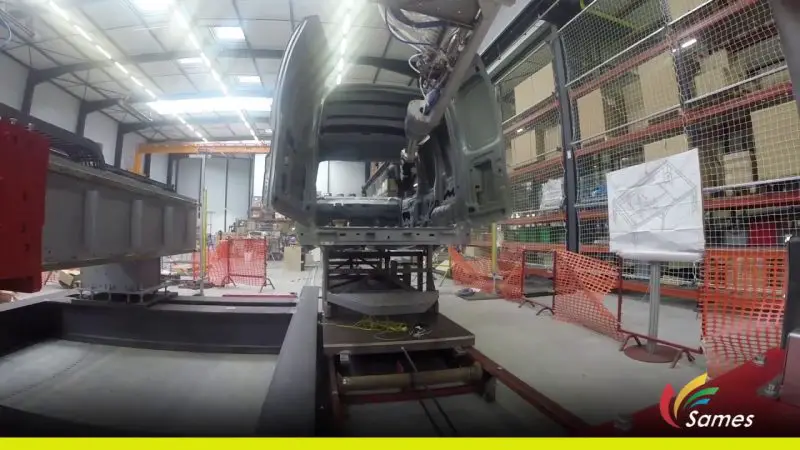
Such application systems are the norm in fields such as automotive where metal and plastic have been painted like this for years. I asked Jean-Michel how much of their production goes to the furniture industry worldwide and the answer was 30-35%. I find that an impressive percentage, which says everything about how safe the equipment is. He told me that they have not had a single case of injury or death due to the current in these systems.
Because I am convinced that no matter how many words I say and no matter how many arguments I invoke, they do not make a picture or a movie, I leave here a video taken during the commissioning of such equipment at a factory in Romania. You will see how, at a certain point, the mist produced by the pulverized lake disappears, settling down on the part. At about 35 seconds. Enjoy.
For programming the robot arm to
a car painting booth is possible?
Thank you!
Hello! This kind of technology is frequently used in the automotive industry. I recommend you to talk directly to Falk Consulting representatives. You can find the link to their website in the article.
All the best!