Pallet production combines both simplicity and complexity, and more than any other type of woodworking relies on the business skills of company owners and the reliability of equipment.
"It is an extremely competitive environment," says the co-owner of DECO TIMBER, Mr. Ovidiu Stăncălie from Ionești. "Now, the European market is full of pallet products from Ukraine and Poland, and we have to work more efficiently to maintain our share in this market."
DECO TIMBER has been in existence for many years, but its current owners recently bought the company and decided to start in a new direction - the production of pallets for export to Italy.
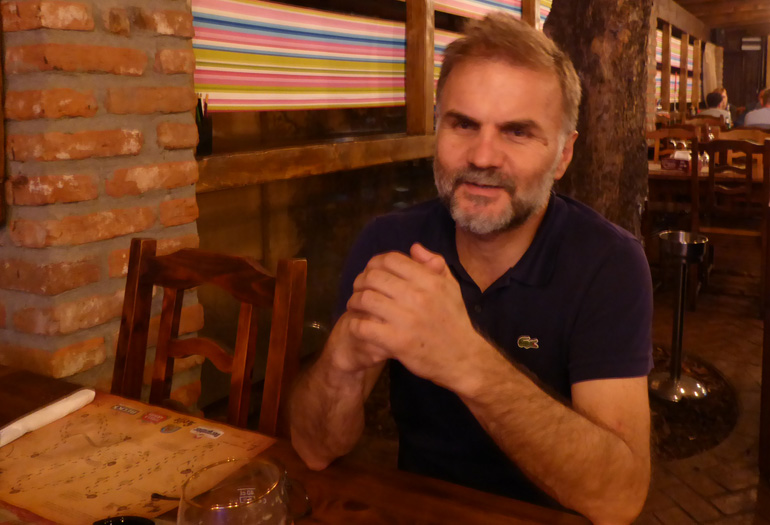
optimal pallet production technology at his company
Mr. Ovidiu Stănсălie, a mechanical engineer with 20 years of experience in wood processing, talks about the key elements of pallet technology.
"Our task is to cut a three-sided prism with a width of 100-145 mm into 22 mm thick planks with high precision and productivity. This operation requires multi-headed horizontal rip saws."
Mr. Stănсălie considered from the very beginning that thin-cut technology was the most suitable and efficient method for pallet production.
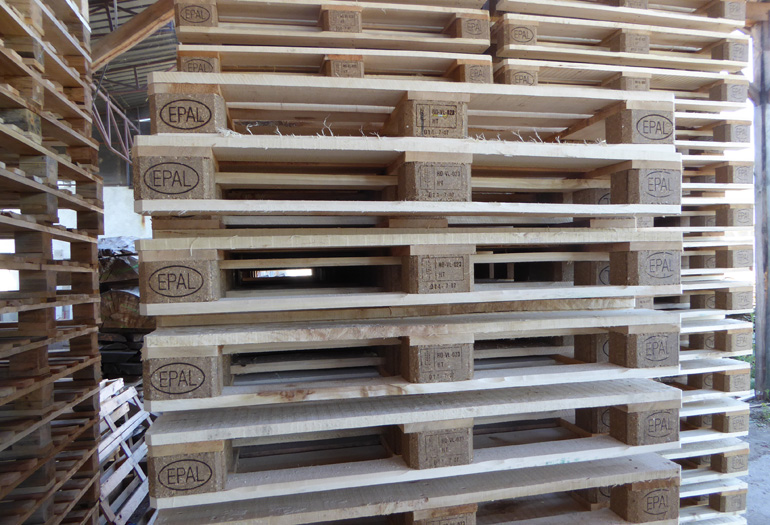
"I wasn't familiar with this technology, but now the Internet offers the possibility of continuous learning, so I carefully researched and studied all possible variants of multi-head horizontal band saws on YouTube," says engineer Stănсălie, who eventually opted for a four-head HR700 model from Wood-Mizer.
"In fact, it was the only option that suited us perfectly," he explains, "First of all, the price was right, and secondly, I found out that this machine had already been produced by Wood-Mizer for several years and that there are many machines like this in operation in Europe. I didn't want to take a risk and buy new, untested technology."
"Plus, the name Wood-Mizer means a lot. Once it's Wood-Mizer - it must be a reliable piece of equipment."
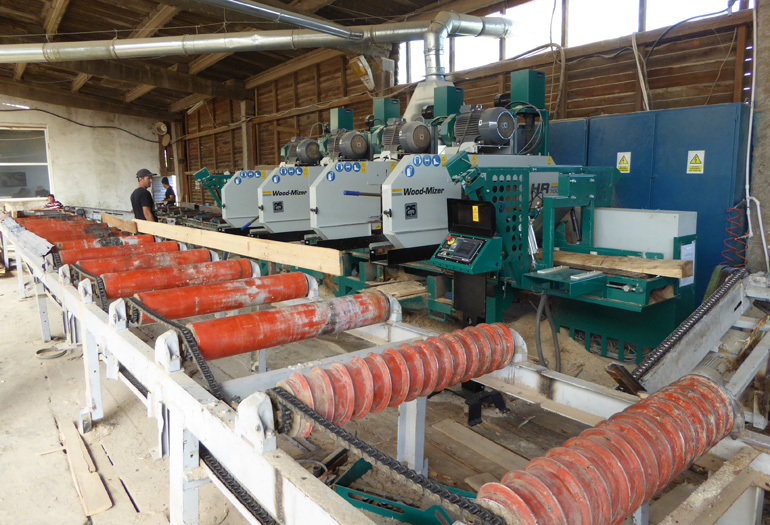
key to the pallet line
"When Mr. Stănсălie called our office, we understood from his questions that we were dealing with a specialist," says Adrian Echert, director of the Romanian subsidiary Wood-Mizer RO. "He inquired about HR700 very carefully and competently."
Mr. Stănсălie has been familiar with the Wood-Mizer equipment for more than 15 years, he has seen these ribbon saws several times at exhibitions, but for the first time he came in contact with the multi-head horizontal ribbon saws.
The new HR700 machine has arrived in DECO TIMBER production straight from the show in Bucharest.
Processing three-sided wooden prisms for pallets
The design of this machine is special: it consists of modules; each module has 2 cutting heads. With four cutting heads, the HR700 cuts a three-sided prism into four pallets, plus a square in one pass.
Each cutting head is equipped with a 15 kW electric motor. A separate console holds all cutting controls. Electric up/down controls adjust the heads to produce different sized timber. Centralized blade tensioning for each two-head module makes the blade change process much faster.
The prism is fed into the cutting mechanism on the double steel belt conveyor at a variable speed of up to 20 m/min. Strong, heavy-duty rollers stabilize and feed the prisms through the heads during cutting. This facilitates the processing of short prisms. A pneumatic sensor automatically lifts the rollers to contain incoming prisms. The speed of the roller is synchronized with the speed of the conveyor belt, providing a more precise cut, especially for thin boards.
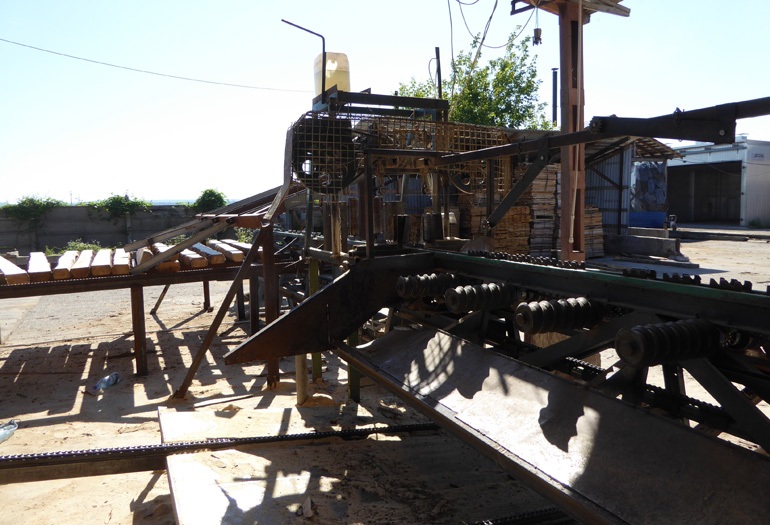
"The HR700 equipment has proven to be extremely reliable, especially the mechanical and electronic parts.This machine needs minimal maintenance and is not sensitive to the qualifications of the personnel. It is very easy for people to learn how to work with the HR700" says Mr. Stănсălie.
"The HR700 machine is running about 90% during the shift and we still have capacity, because we are now cutting at a speed of 8 m/min," explains engineer Stănсălie.
Primary processing of logs
The primary cutting of logs is done on a vertical bandsaw with a double wide double band produced by the South African company MultiSaw. Recently, Wood-Mizer acquired the intellectual property for this equipment and, starting in 2017, began producing these ribbon saws under the brand name TITAN. They were presented for the first time at LIGNA 2017 in Hannover.
At DECO TIMBER mainly small logs of local wood - poplar, pine or spruce up to 35 cm in diameter - are processed. The logs are stored on an open surface and fed to the bandsaw, one by one, through the chain log loader. The operator sits in the operator's seat at an overhead control station on the side of the bandsaw, giving him a clear view of the entire process. He controls all functions of the bandsaw with the lever arms.
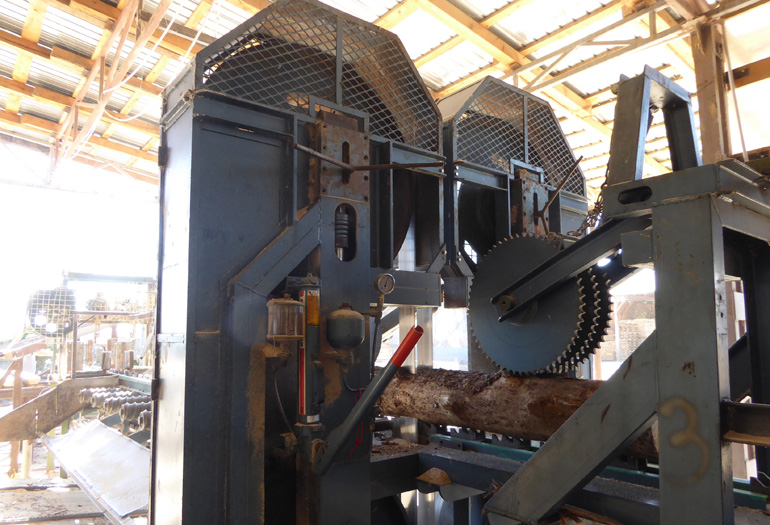
A log loader at the start of the line loads and rotates the log into the correct position for cutting before it is fed into the vertical conveyor. The spiked infeed/outfeed system sends the logs through the 150 mm wide double blades, resulting in a double-sided, double-width prism. Mechanized support rollers hold the logs securely on the spiked chain during cutting.
After the cutting ends, the billets are lowered down onto the cross conveyor which transfers the billets to the horizontal ribbon saw - another element of the TITAN line. Here the sawdust is transformed into several additional planks.
The two-sided prism is passed through another horizontal cross-cutting bandsaw and turned into a three-sided prism with a width of 100 mm or 145 mm, after which it is cut on the HR700 four-head machine into 22 mm thick pallets.
"It's a step forward that Wood-Mizer has started to produce TITAN wide-web band saws, while Romania already has experience in using these saws, and the experience is very promising," says Adrian Echert, director Wood-Mizer RO. "The TITAN range of saws consists of primary and secondary saws, a multi-rip saw and two circular edging saws, plus all the material handling equipment needed to automate the wood transfer from start to finish, as well as waste removal. The productivity of the TITAN line can reach up to 150m3 per day."
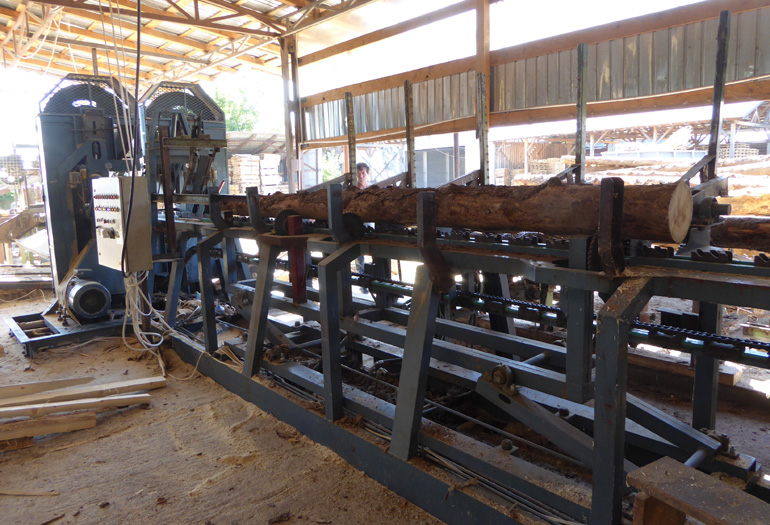
manufactured by Wood-Mizer under the TITAN brand
"Look at the kind of mechanization that goes on at DECO TIMBER," continues Adrian Echert, "It's amazing. All the equipment is completely linked in one technological line where the machines are connected by chain conveyors. This is the development of engineer Stănсălie".
"In my practice, I have often worked with used machines," explains Mr. Stănсălie. "It's not the best choice, but sometimes we have to do it, and in order for used equipment to work well, you have to be fully involved in the process: understanding which units are vulnerable, which functions need to be specially controlled, how to fix them."
"The wide-web ribbon saws didn't come new to us, but I'm completely satisfied with the way they work. It's a simple piece of equipment, all the mechanical components are very reliable and virtually no electronics. And we have a large reserve of production capacity, but it's important to note that we have experience in maintaining the wide-ribbon web. As you know, 70% of your woodworking success depends on the blades you use and how they are sharpened and prepared for the job."
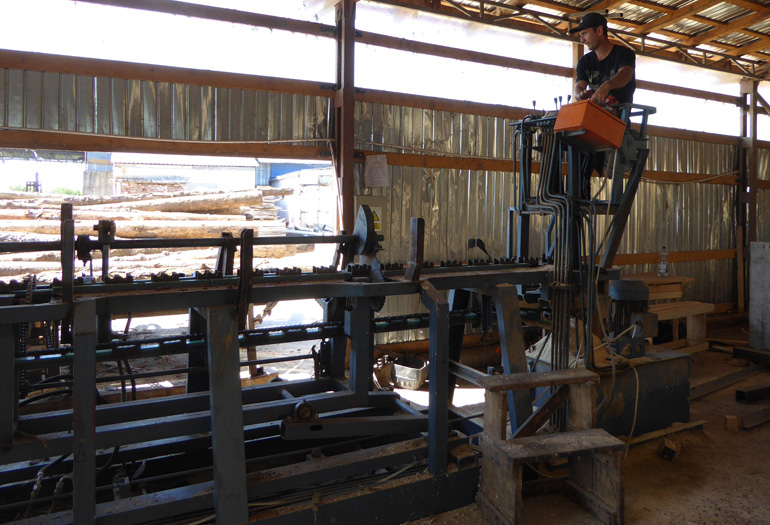
"Another important issue in pallet production is the thickness of the cut. When you are cutting planks only 22 mm thick, the thickness of the cut is the key factor, it has to be minimal. The Wood-Mizer technology is known for its cut thickness, a thickness of about 2 mm, which increases product recovery and decreases the amount of sawdust", - shares engineer Stănсălie.
With a focus on pallet quality
Due to the fact that the poplar will twist during drying, the pallets are assembled from green planks. They are made on the special Wektor production line capable of producing up to 170 pallets per hour. Already assembled, the pallets are loaded into a specially designed drying oven.
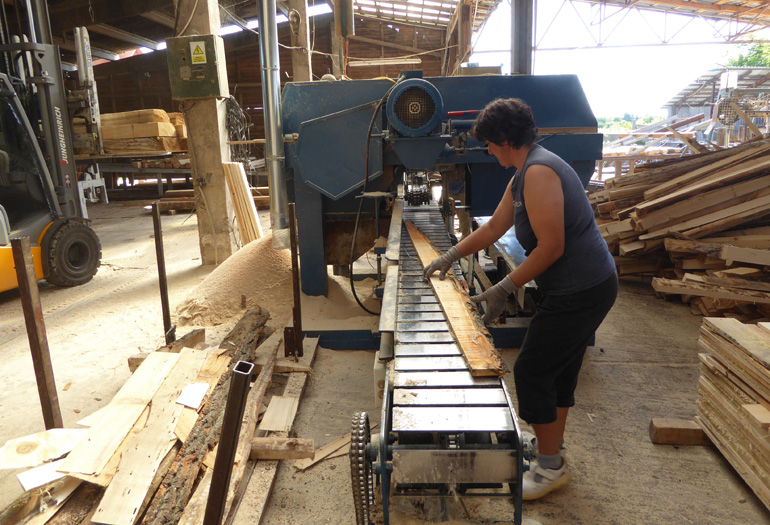
under the TITAN brand
"When the pallets are assembled by nails, it is not possible to twist the wood in the dryer", explains Mr. Stănсălie, "The pallets are smooth and of high quality, confirmed by the EPAL certificate, which is required for any pallet manufacturer operating on the European market".
"Actually, we're still at the beginning of the road," says Mr. Stănсălie. "We have big investment plans and we know exactly what we want to eliminate from production. Pallet production requires professional skills, and reliable equipment becomes half the success."
As a next step, DECO TIMBER will purchase Wood-Mizer horizontal ribbon-cutting saws to cut the dill.
Source: www.woodmizer.ro
Add comment