The primary processing of wood, the cutting of veneers, and the processing of semi-finished products result in rough surfaces due to the splitting of the wood fiber. Also as a result of processing, dents, scratches and stains may appear, which must be removed if we want to end up with a quality product. White sanding is the operation that solves these problems and is a very important step. The final quality of the products depends on how it is done, how well the materials are chosen and the machines used. Proper sanding results in a well-gauged, even surface with a nice, even and pleasant texture. So you will read an article about wood sanding in general, industrial sanding of wood and derived panels, the choice of abrasive materials, abrasive cloths and belt sanding machines.
Factors on which quality sanding depends. Choice of materials
Wood abrasives come in various forms: rolls, strips, disks, abrasive sponges. Regardless of their presentation they have three component parts - the backing, the abrasive grains and the adhesive that holds them together. Each influences the sanding process.
Support
It needs to be strong to withstand the pressure exerted during sanding and to hold the granules stuck to it. The most commonly used backings are canvas and paper. Canvas is used when strength and flexibility are needed, for sizing and profile grinding. Paper has different weights, ranging from 90 g/m² to 280 g/m². The weight is directly proportional to the strength and stiffness of the abrasive material. For sanding machines the heaviest of 220 g/m² is used.
Adhesive
Bonding is done in 2 stages, gluing and re-gluing, using synthetic resins as adhesives. Glueing glues the granules and re-gluing fixes them. The amount of adhesive applied also has an influence. A thinner layer makes the material more aggressive but less resistant, while a thicker one decreases the aggressiveness and increases the resistance over time. An aggressive material should be used for calibrating and a less aggressive one for sanding between layers.
Abrasive granules
They are the ones that actually act on the material to be sanded. The most commonly used are aluminum oxide and silicon carbide. Aluminum oxide can be used for all types of grinding, as the grains are sharp and sufficiently hard. Silicon carbide is harder, but the grains are less sharp. It is used for sanding hard wood (oakThe density of the grains is also important (sprinkling). If the grains are sparse, the abrasive materials will be more difficult to load with dust from sanding and a high density will make sanding more uniform.
Granulation is the main indicator for the choice of abrasives and is represented by a number. European Federation of Abrasives Producers (EFAP) has chosen the Pxx representation. This is also used here although it is not the only representation. The grain sizes get smaller as the grain size increases. A paper with a small grain size is used for coarse sanding (P80, P100), while a paper with a large grain size is used for fine sanding (P320, P400).
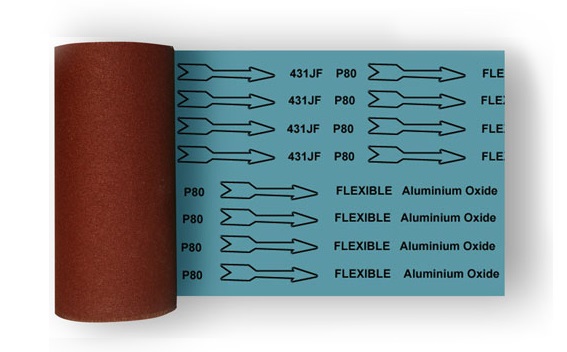
Industrial sanding machines
Indistrial sanding can be done with abrasive belt machines or rotary brush machines. Wood sanding is mainly done with belts. Brushes are used to obtain special surfaces such as structured or antiqued wood. In contrast sanding between layers or special brushes with 'bristles' made of fine sandpaper or more delicate materials such as felt or wool are used for polishing varnish. But sanding machines with rotating brushes are the subject of another article.
Belt sanding machines
Sanding machines can be single or multiple (2 or 3) belts of different grit sizes, mounted one after the other. It is very important with these machines that the belt is easy to install and remove and that it is well tensioned for efficient sanding. The device on which it is mounted rotates continuously and the object is sanded the moment it comes into contact with the belt.
They can be separate or integrated in processing lines following the technological flow. They are single-belt machines (single grit) or have successive abrasive belts with different grits, reproducing an entire sanding process in stages. Machines may be more or less automated depending on production requirements.
On all these machines the abrasive belt is the one that does the work. Being a repetitive mechanical movement, the quality of the belt and the absence of defects is very important. Any defect, no matter how small, will be multiplied and magnified on the sanded surface. For example, a paper splice flaw can be seen on a sanded panel as a band of spots appearing at even distances. What is sadder is that the defect that appears is almost invisible after sanding, but is very visible after filling and varnishing. This is why the way the strips are spliced and their storage are very important.
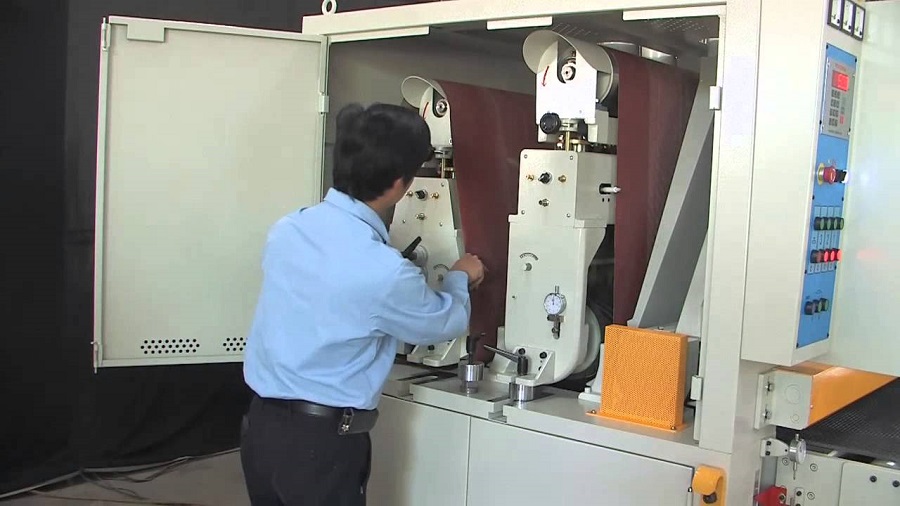
Joining and storing abrasive belts
The joint must be as strong as the abrasive material, have the same thickness, and the resulting belt must be perfectly cylindrical. Two types of splices are most commonly used, type A and type B splices.
Type A junction is specific to the paper backing and is made by overlapping the ends without interrupting the continuity of the abrasive material (without removing it). The belt has the same thickness along its entire length and the sanding is done without the appearance of bands on the product.
Type B Joint is made of textile-backed strips. In the overlap area, the abrasive material is partially removed so that the tape is not thicker on that portion.
How abrasive cloths are stored is also important for maintaining quality. The temperature and humidity in the warehouse, the way they are stored (hanging or shelved), whether they are in the original packaging or not, all have an influence on the belts and failure to follow the manufacturers' instructions can lead to small defects that lead to large rejects. For example, if they are kept hanging, it is recommended that they have enough room to avoid rubbing against each other. This friction can cause the abrasive material to grind or peel off and reduce quality.
Another important criterion for sanding machines is the sanding speed. Not all materials sand at the same speed and too high a speed can lead to overheating of the cloth and a decrease in quality. For example, a hard hard hardwood is sanded at a speed between 15 and 22 m/s, the same as MDF, while resinous wood between 12 and 18 m/s. The highest speed is needed for veneer (20-30 m/s) and the lowest for primer (5-15 m/s).
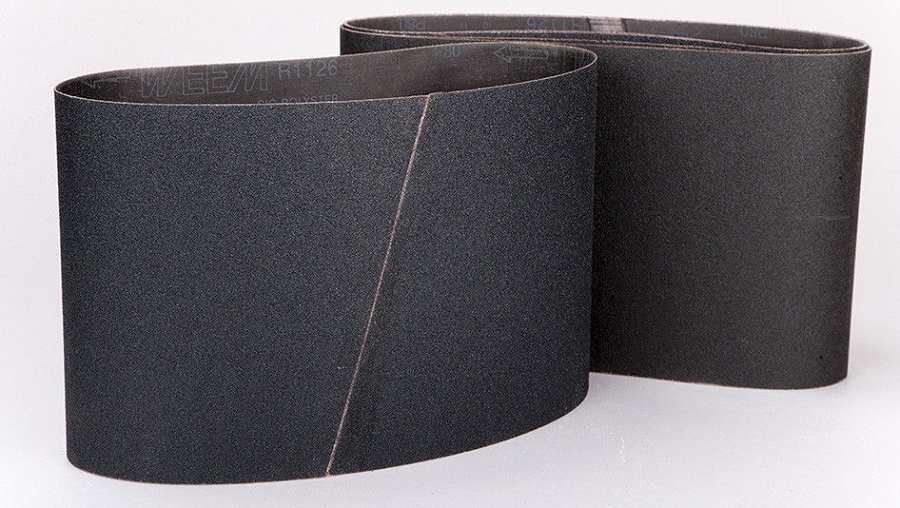
How we can make abrasive tape last as long as possible under the same quality conditions
During the sanding process dust can accumulate in the space between the abrasive grains. This leads to a decrease in sanding quality and an increase in temperature during the process. The belt loses its qualities and must be replaced in order to continue to produce quality products.
Another result of prolonged or improper use of the tape is the grinding or stripping of the grains. Their continued use leads to poor sanding with defects.
What should be done so that the sanding belt can be used as much as possible without compromising on quality? Here are some suggestions:
- Choose the sanding machine speed according to the material;
- Always choose the sanding belt according to the type of operation (calibrating, sanding between coats, etc.) and the material to be sanded (hardwood, softwood, veneer, MDF);
- Choose the right grit size for the work step;
- Check the sanding machine beforehand, mount the belt correctly and adjust the parameters when the technological process or the material requires it;
- Check that the exhaustion system is working properly and that the dust resulting from sanding is immediately and properly vacuumed up. The use of special abrasive belts, such as stearate belts, can reduce the build-up of dust between the abrasive grains.
Correct sanding really depends on many factors, but it is good that they are respected. Otherwise the risk is that you will not get a very good surface quality and this may not be visible until late in the production process, when it is much more difficult to remedy. To avoid such problems it is best to ask your abrasive and grinding machine suppliers for as much information as possible and do not hesitate to ask for their support whenever needed.
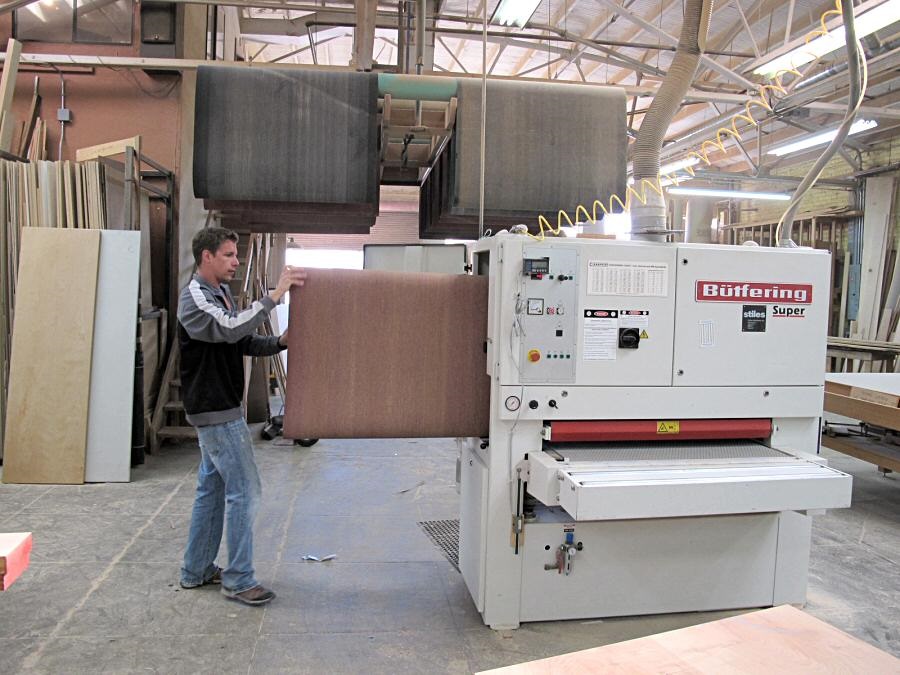
Add comment