It's a subject that fascinates many woodworking enthusiasts. It will be about Japanese tools, specifically traditional hand tools used for hundreds of years by Japanese masters. I write with excitement because I know there are many enthusiasts of traditional Japanese carpentry and I wouldn't want them to be disappointed. However, as I have a long-standing passion for the Japanese art of woodworking, for their traditional joints, for the way they place this craft between art and science, I dare to tell you a few things about traditional tools, about tool kits and what the differences are between some Japanese tools and similar ones from Europe, America or Australia.
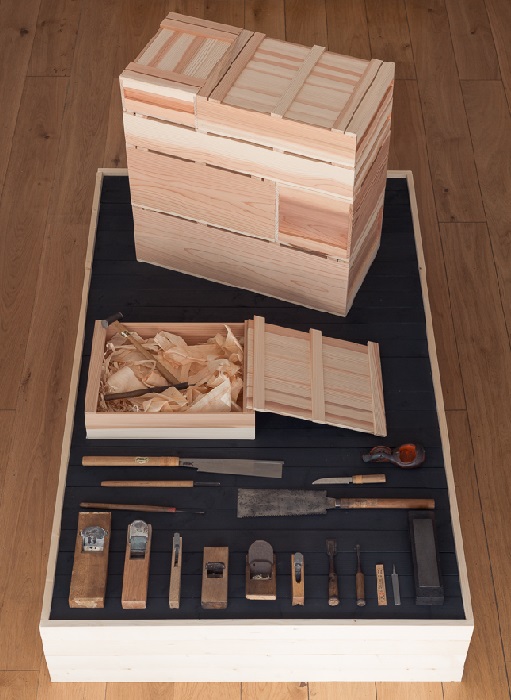
Why are these tools so interesting? Why are they the subject of so many discussions, presentations and lectures?
Japanese tools are so interesting because of the craftsmen who stubbornly work with such hand tools, managing to achieve works of a finesse and precision difficult to achieve even with the most modern tools. Many of them continue to be handmade, their perfection resulting from the collaboration between the carpenter and the toolmaker.
It's hard to believe, but even now saws are being made whose teeth are cut by hand with great precision. Blades for carving knives are made using the same technology as for making the swords of the old samurai.
The fascination comes precisely from this unaltered preservation of traditions, from the finesse with which the wood is worked and from the liveliness of the objects and constructions. Yes, we too have a tradition of woodworking. We have people who preserve tradition and work with wood using traditional tools. I don't want to belittle or cancel their merits or those of the old carpenters and joiners. It is simply the presentation of another tradition and a culture that has managed to work and join wood in such a way that we now have the oldest wooden building in the world, a building that is still standing.

Traditional Japanese hand tools
But let's get back to Japanese tools. Concern not to lose the tradition and carry on the centuries-old legacy led to the establishment of a museum of carpentry and joinery tools in Kobe in 1984 - Takenaka Museum. Takenaka Corporation, a construction firm dating back to 1899, was the one who founded it. The museum contains over 30,500 tools and objects related to wood and woodworking, 20,000 of which are tools. Initially it was only Japanese tools, but in the meantime tools from other parts of the world have appeared.
I am happy to say that this museum inspired (as he states) Cătălin Sorescu to set up in Timisoara, Tools Museum. The refurbishment is in full swing and I admit I can't wait to visit. I take this opportunity to congratulate him once again for his initiative and effort.
Exhibitions and displays of Japanese tool collections exist all over the world, but it is clear that there is a fascination with Japanese art in the US. Perhaps it's also because there are many American masters born in Japan or first generation born in the US (George NakashimaThere are specialized schools that have Japanese carpentry courses in their curriculum and at Harvard University has an exhibition of old Japanese tools that Toichi Takenaka, the company's president, presented to the Faculty of Design.
Despite the fact that there are so many thousands of tools on display, most of the presentations and descriptions are for 4 categories; rendele, saws, chisels and knives. Each time the tool kit, which appears in old Japanese prints from the 14th century, is also present.
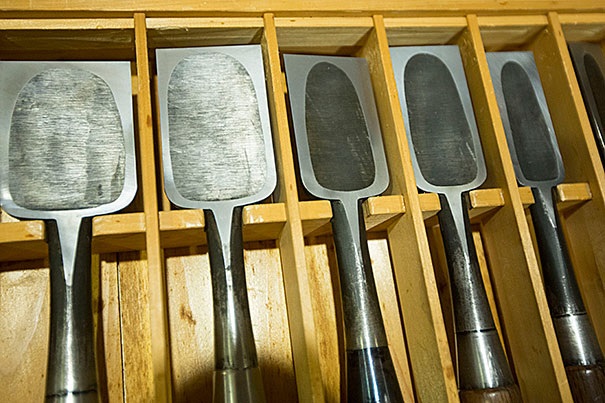
Windlass
The generic name for this class is kanna. There are various types and sizes, each with its own specific name. Unlike European or American rhinestones, which push when you work with them, Japanese ones pull.
The design of the Japanese rhinestones are very simple, a rectangular wooden box and a blade that attaches to its sole. The way the blade is fixed and maintained and the smoothness of the sole are what determine the smoothness of the workmanship and the layer of cut wood. And the Japanese achieve remarkable performance in the thickness of this layer. There are competitions to get the longest and thinnest strip of wood.
The blade of the rhinestone is sharpened and maintained with the sharpening stone (toichiIt is made of very high quality steel so it will not lose its properties over time.
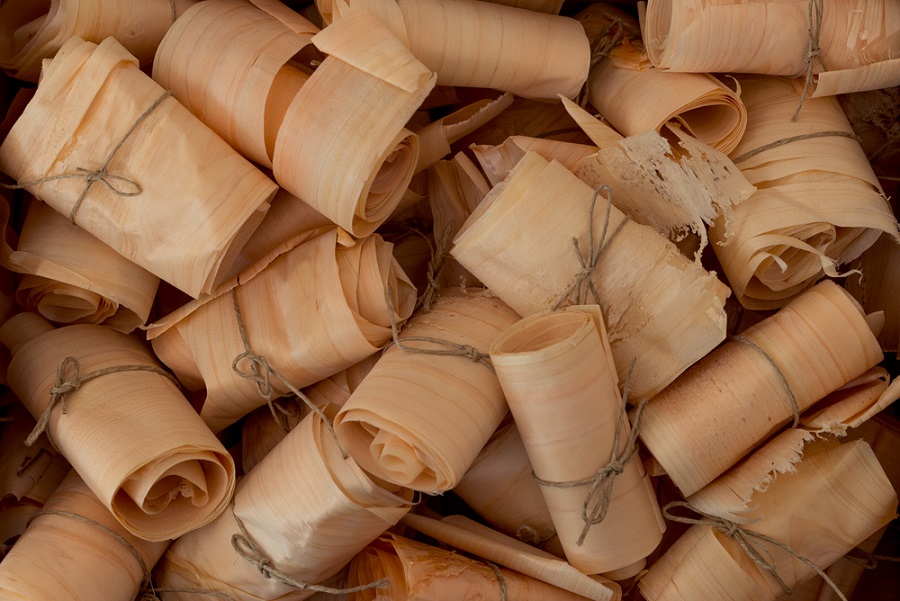
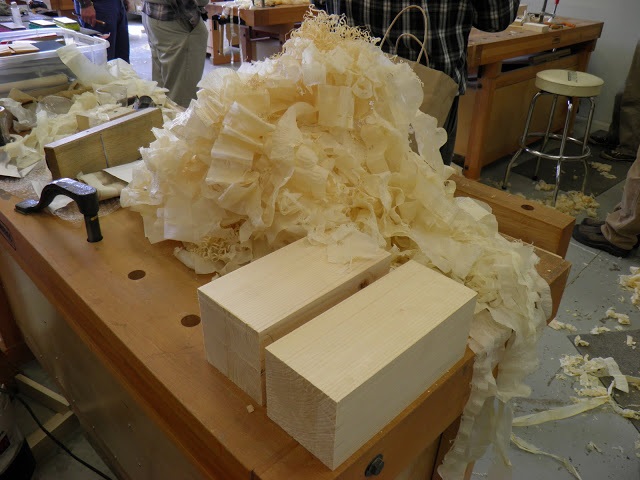
Sawmills
The name of the gear group is nokogiribut here too we have different models. The most commonly used saw is rhubarb. It is a trapezoidal steel blade, wider towards the outside and tapering towards the handle. It has teeth on both sides, but they are different. On one side the teeth are made to cut along the grain of the wood and on the other side to cut perpendicular to the grain. The wooden handle is long, giving the woodworker perfect control over the blade. The special flexibility of the blade also allows level cutting.
The saw dozuki - Swallowtail - has teeth on one side only and are positioned so that they work, like the rhinestone, when pulled. The handle is also long, for very precise control. Many carpenters say it's an easy saw to use, it puts much less demand on the hand, and the fact that it pulls makes the blade not bend while working and the cuts are smoother, more accurate. The blade is also flexible, which is useful for level cuts.
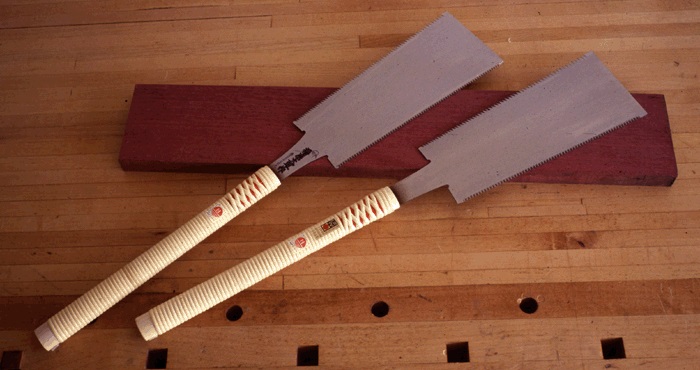
Chisels and knives
Although the world's largest chisel producer is in Europe - Pfeil in Switzerland - there are many who prefer Japanese chisels (names). And that's because of the steel the blades are made of and the way they are machined. The same high quality is found in the blades of knives used for carving or cutting thin strips of veneer.
The quality of the blades comes from the fact that they were made by master armourers, the ones who made samurai swords. In 1876, in a bid to reduce samurai privileges, the government banned the wearing of swords in public (Haitorei Edict) Only nobles, military and law enforcers were exempt from this law. Due to a lack of orders, armourers were forced to re-profile. This gave rise to high-quality kitchen knives and knives and chisels for woodworking.
Chisels come in different shapes and sizes. If you want such Japanese tools specialists recommend you to get a complete set.
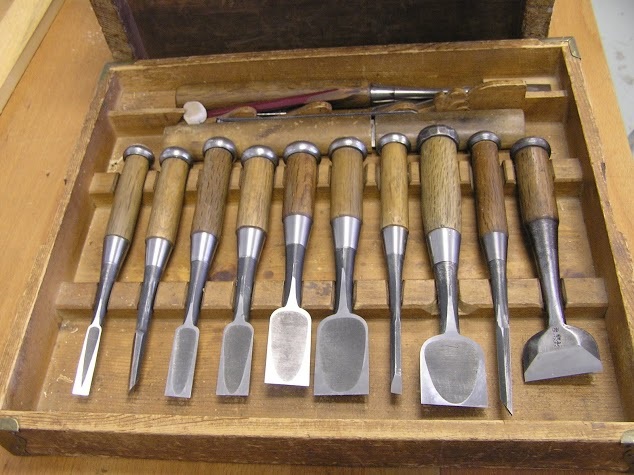
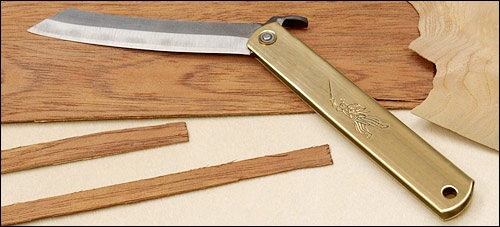
Japanese lesson
The tools, tradition, craftsmanship and various Japanese woodworking arts can be talked about endlessly. But the most important lesson we should learn is the respect with which tradition, the roots, are preserved while looking forward. Japan is not a country stuck in the past, unwilling to evolve. On the contrary, it is a modern country that is a trailblazer in many fields.
Keeping traditions, respecting the past, is not standing still. You can keep moving forward, but you'll do so much better knowing who you are and what your roots are. That, in my opinion, is the Japanese lesson.
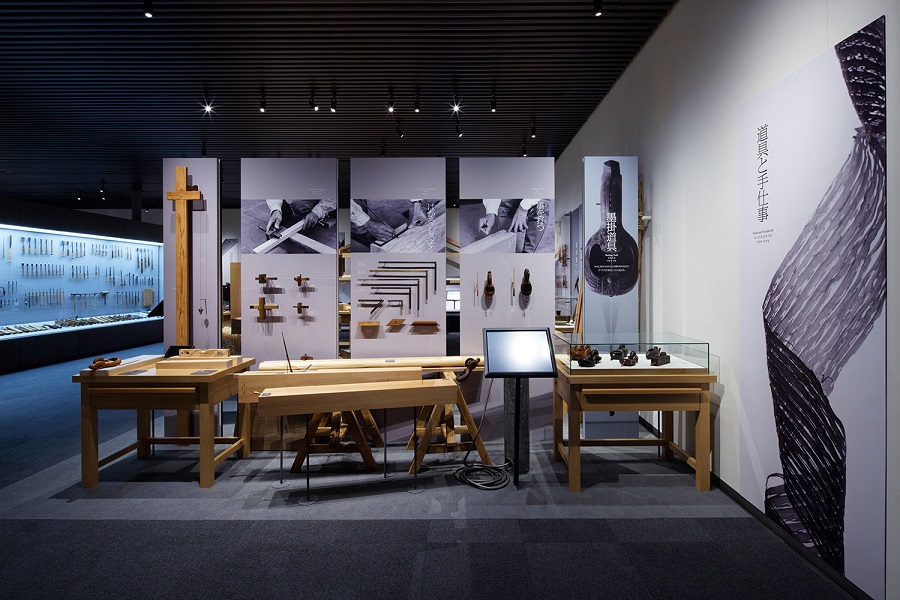
Hello.
My name is Valerii.
Where can I get quality Japanese windows.
Respectfully.
Good evening, Valerii.
Try finetools.ro. They also have Japanese tools (and saws).
All the best!