I recently wrote an article about industrial sanding of wood using machines. As the subject is very broad, we talked about wood sanding in general, abrasive materials in the form of sanding paper (a generic term that also includes textile backing) and belt sanding machines. Another category of wood sanding machines - very common in the industrial environment - includes rotary brush machines. Let's see why they are needed and what factors influence the quality of sanding.
What rotary brush sanders are used for
Rotary brush sanding machines are very versatile. The positioning and number of brushes, the abrasive material used, the characteristics of the machine allow them to be used for different operations.
The machines can be used for both șlWhite wood finishingand for sanding the primer or polishing the lake. But the abrasive material is different for each of these operations.
The usefulness and efficiency of the brushes is clearly seen in șsmoothing of profiled and carved elements. The configuration of the brushes allows the abrasive material to reach places that are very difficult to get to with belt grinders without damaging something, both for sanding wood in white and sanding between coats. Brushes are also used for desprăfuirea profiled elements.
Using hard brushes with a certain structure can make structuring or îforced wood ageing. Unlike sandblastfor example, whereby one can make just an ageing of the wood by partial removal of the early wood, with brush sanding machines it is possible to obtain surfaces with different structures and aspects, the appearance of old wood can be varied by using different brushes.
Using recovered wood is now all the rage, being used in furniture, flooring and even house construction. The passage of time leaves its mark on wood, and it's not just the profiling but also the accumulated dirt. This reclaimed wood can be cleaned with brusheswithout spoiling its old look and without removing the natural profile it has acquired over time.
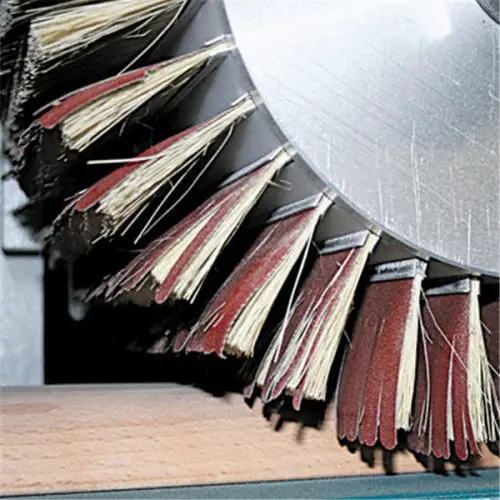
Sanding quality on rotary brush sanders
The quality of sanding does not only depend on the abrasive material used. Being a machine there are many factors that influence the process. These factors are dependent on each other and the perfect combination must be found for each operation or object to be sanded.
Basically, the quality of the sanding is determined by the combination of the abrasive material used, the cylindrical drum (shaft) on which the abrasive is placed, the rotational speed and the pressure on the workpiece.
The abrasive material
Sanding is done by abrasives mounted on a drum. These can be pieces of abrasive tape, bristles made of different materials or different textiles that will have a different effect on the surface they are sanding.
I won't go back to the structure of abrasive tapes because we have talked about them at length in article on the choice of abrasive materials. They are the same except that they are small pieces, the sanding being influenced by their length and width. The narrower and shorter ones are used for flatter or rounder surfaces, while the wider and longer ones are used for surfaces with profiles and edges.
Abrasive tape pieces are often combined with synthetic bristles. This combination results in a perfectly sanded surface, comparable to that resulting from successive hand sanding with progressively grained abrasive abrasive. The length and thickness of the brushes also influence the sanding. Short brushes make sanding more aggressive and are used for wood, while long brushes are used for sanding primer, where there is no need for aggressiveness.
Structuring is done with metal brushes. I won't go on because this is also a large subject to be dealt with separately.
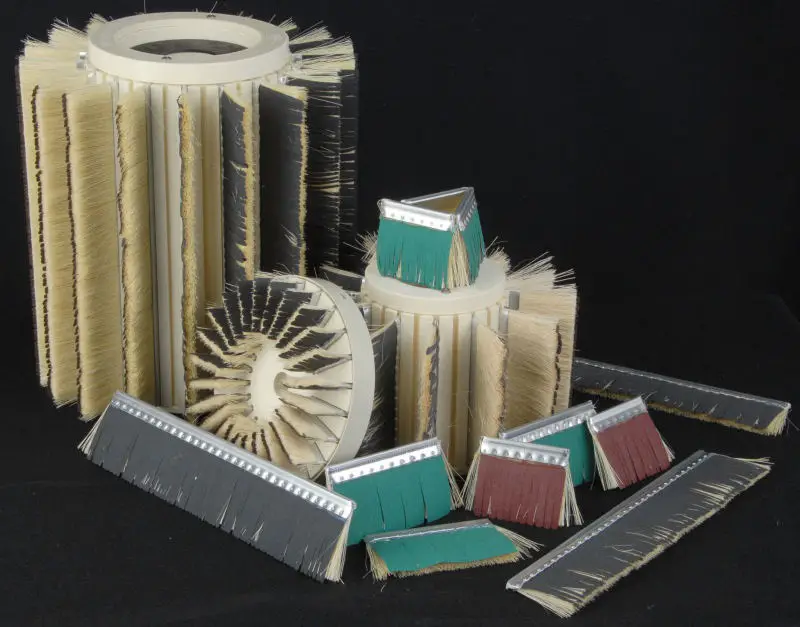
Drum rotation speed
Drums can be of different lengths and diameters depending on the machine. The abrasive material can be bonded to the drum to form a common body with the drum, or it can be separated and the chopped abrasive can be easily replaced.
The rotational speed of the drum influences the durability of the abrasive material. The lower the speed, the longer the life of the brushes and the better the sanding quality. Speed is inversely proportional to hub diameter. For example, for a diameter of 280 mm the optimum speed is between 50 and 280 rpm, and for a diameter of 50 mm the speed reaches 1200-1500 rpm.
When sanding profiled elements a very high rotational speed is not recommended. The high speed will cause flat surfaces to remain almost unpolished, while corners and profiles will be very rough. A lower speed will cause the abrasive material to not pass quickly over flat surfaces and the passage over profiles and edges will be smoother, resulting in a quality sanding.
The best results are obtained with large-diameter drums that rotate at the lowest speed in the accepted range.
Influence of pressure
This is the pressure with which the brushes press on the material to be sanded. The optimum pressure is determined according to the object to be sanded. Basically the drum is initially set so that the brushes just touch the plate. Lowering it will cause the brushes to bend and determine the sanding pressure when the drum is in motion.
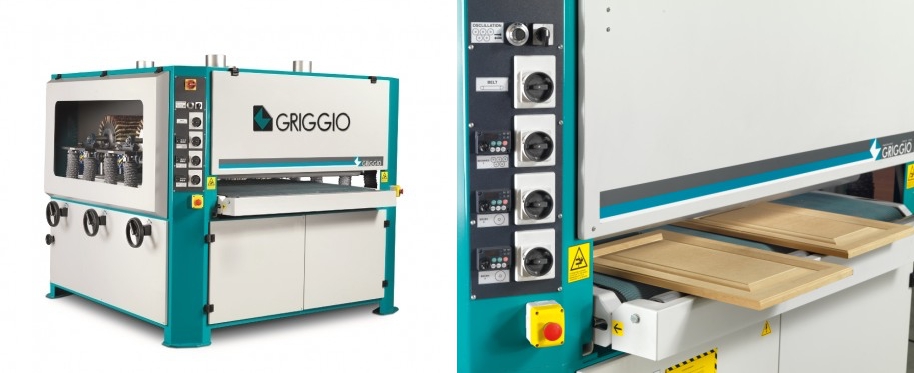
Rotary brush sanding machines
The machines are very different and may have one or more rotating brushes. The positioning of the drums is also different. The brushes can be placed perpendicular to the belt the workpieces are on, at 90º or at a lesser angle so that the "entry" into the plate is gradual and less aggressive. Combining multiple brushes on the same machine results in better sanding. For example, the combination of two rotating brushes with different directions of rotation gives very good results on profiles. The first brush brings the wood fiber in one direction and the second cuts it.
You can also combine 3 or 4 rotating brushes. They can be all with the same direction of rotation or one in one direction and the others in the opposite direction. The combinations depend on the objects to be sanded and the results to be obtained.
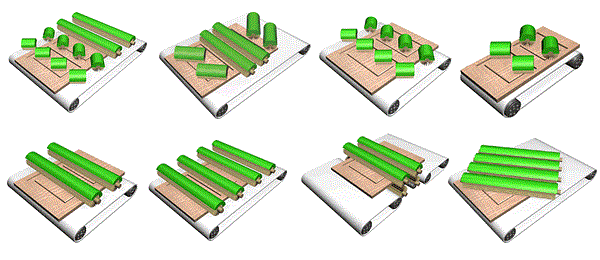
There are also machines with an abrasive disk system whose rotation is perpendicular to the workpiece. Basically it's not the same motion for all the abrasive on the drum, but each abrasive group mounted on the disk comes in gradually, the sanding is much less aggressive. It is similar to the situation where the drum is not set at 90º, but multiplied several times. Very suitable for profiled doors, curved and carved elements.
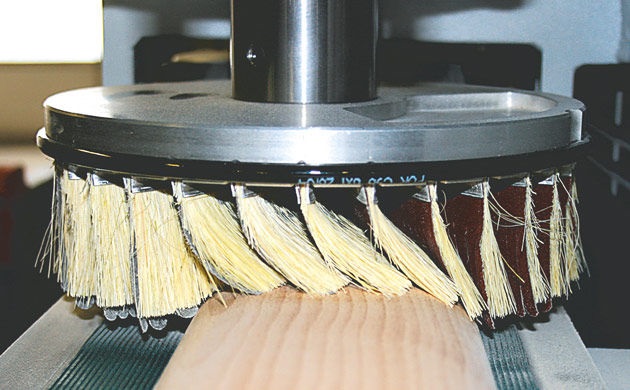
The combinations that can be found on such machines are very interesting. There are machines that profile and grind at the same time. For example, with double profiling and sanding unit of the Greda, Italy, which you can find at DanibrumThe same machine can be used to produce shaped and sanded elements for chairs, tables or sofas. The machine reduces working time by combining several steps.
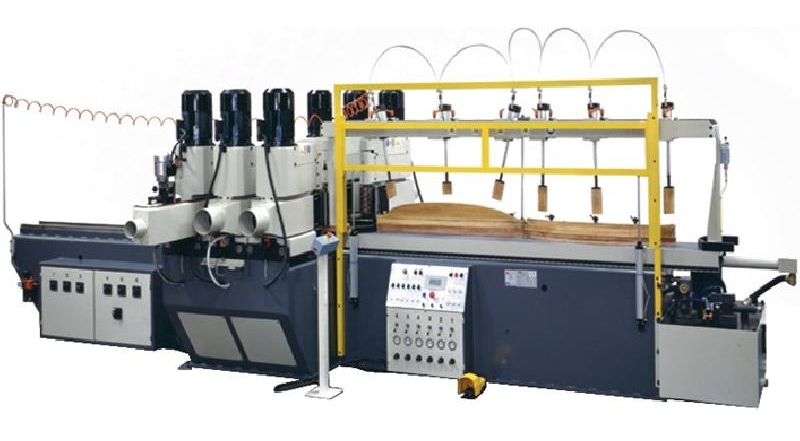
Rotary brush sanders are not just for large factories with complex machining lines. Like belt grinders they can be stand-alone machines that can also find their place in a workshop. They don't have to be big to be complex and help you get the best results in the shortest time and using state-of-the-art technology. Sanding and structuring machine with brush and Profile Sanding Disk Grinding Machinewhich you can also find at Danibrumare only two examples.
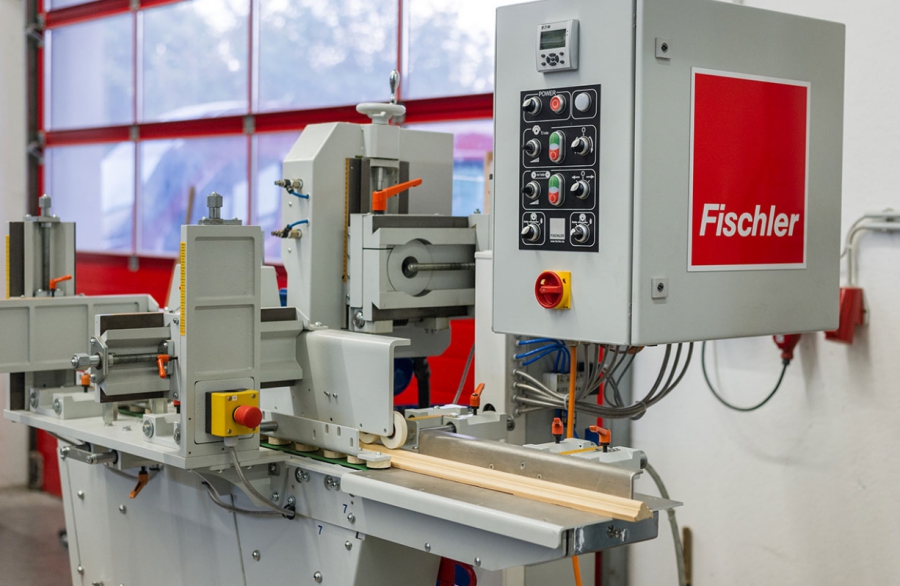
photo source: danibrum
All in all, rotary brush sanders are the best solution when you have profiled or carved items to sand. The brushes have the ability to get into the most hidden nooks and crannies and can sand the most diverse shapes. If profiles are part of your production such a machine certainly helps to increase the quality of the finished product.
Hello, can you please tell me where I can purchase a drum with interchangeable blades, (I try to make wooden toys and have little problems with sanding) thank you for your time, have a nice day!
Hello.
It seems quite difficult to find a drum with interchangeable blades. I have not been able to find it from suppliers and manufacturers in Romania. My opinion is that you should ask importers or manufacturers of rotary brush grinding machines. They work directly with the abrasive manufacturers to get the best solutions for rotary brushes.
I'm sorry I can't help you more. If I can find the time in the supplier, I'll get back to you.
All the best!
Hello, I am a manufacturer of sapwood-free acacia poles between 10-24 cm thick. I am interested in a rotary brush sanding machine because at present they are sanded manually with electric flexes.
Where to order reels with blades of about 60-70 cm length
thank you