The energy efficiency of houses is a major issue in European countries, and the issue of reducing fuel consumption in homes is taken very seriously. New houses are being built with the idea of keeping subsequent energy costs as low as possible, even close to zero, using the best insulation materials, ingenious jointing solutions to eliminate thermal bridges or triple-glazed windows.
Directive 2010/31/EU Directive of the European Parliament and of the Council of the European Union on the energy performance of buildings, published on 19 May 2010, requires new buildings to become more efficient and stipulates that all new buildings must be nearly zero-energy efficient (nZEB) by the end of 2020. For new public buildings, the deadline is the end of 2018, which means that the directive is already in force for them. The Energy Efficiency Directive 2012/27/EU also obliges Member States to set efficiency targets by 2020.
At the beginning of 2016, the Government adopted an Emergency Ordinance which stipulates, in line with the European Directive, that all new buildings approved on the basis of building permits issued from 31 December 2020 onwards must have near-zero energy consumption. In the case of public buildings, the ordinance is valid from December 31, 2018.
Insulating old houses
In Romania, the largest energy consumer is the buildings sector, whether private or public. At the level of a building, thermal energy consumption for heating and domestic hot water accounts for about 701TPTP3T of total energy consumption. One problem is the residential sector due to the age of buildings. According to data National Statistical Institute, 31% of residential buildings are built before 1961, 19% - between 1961 and 1970, 23% - between 1970 and 1980, 14% - between 1981 and 1990, 7% - between 1990 and 1999, 6% - after 2000. All these buildings should be made energy efficient by thermal insulation.
Thermal insulation aims to restrict heat flow, thereby reducing energy consumption for heating or cooling. Heat flow is determined by temperature differences between inside and outside the house. In winter, heat in the house tends to flow out, and in summer, heat tends to flow in. Now, in order to continue to have a comfortable environment in our homes, we make up for the drop or rise in temperature through energy consumption. It's proven that the greatest heat loss - up to 70% - occurs through exterior walls and the roof. Sensitive areas are also windows, doors and floors, but for a significant reduction in the cost of heating or cooling your home, attention should be directed to the biggest heat "losers", i.e. the outside walls and roof.
There is thermal insulation solutions for all types of houses, whether concrete, brick, timber, log, prefabricated walls, steel or mixed. Viable solutions have been found for old houses, even those with carved exteriors. From studies done in Germany on renovated and insulated old houses, energy costs have been reduced by at least 65% and in many cases by more than 90%.
Energy efficiency of wooden houses
All this "craze" about energy-efficient homes started after the 1973 oil crisis. Governments were so spooked by the prospect of running out of heating supplies that they pushed for energy efficiency calculations to be introduced into house design. This evolved into European Community directives that require homes to be built so that they can operate at near-zero energy consumption, with some of the energy needed being produced by the homes themselves.
Building an energy efficient house involves many aspects, thermal insulation is not enough. The house must provide green energy sources using solar panels, have windows with 3 rows of glass so that heat exchange is very low, ensure indoor air circulation with heat recovery and reuse. Wooden houses are the most thermally efficient because wood is by nature an insulating material. They also provide very good thermal insulation because of the way they are built.
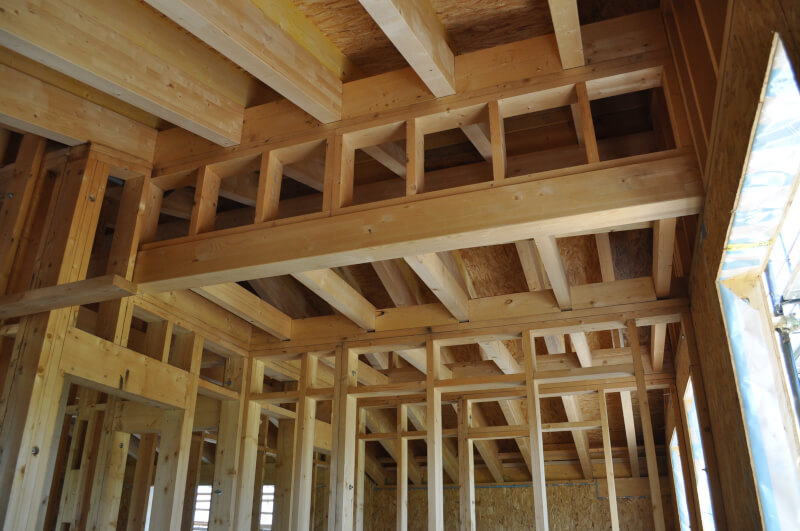
Types of wooden houses
Timber frame houses. I assume building a structure of wooden posts, frames and beams on site and forming the walls between the structural elements, using OSB and insulating materials. Even if no insulation was put in (which is not usually the case), and the walls were just closed on either side with OSB or drywall, the air layer inside would act as a thermal insulator.
Houses made of prefabricated structures are factory-made and only assembled on site. The walls are made of several layers of different materials that ensure very good energy efficiency. The processing is done with high-performance machines so that the walls are joined on site easily and without loss, and the pieces fit together perfectly. In addition to very good energy efficiency, this type of house has the advantage of a short construction time and a clean building site.
Round wooden houses or square. The walls of these houses are the result of successive overlapping of wooden beams or logs. Virtually the entire wall is made of wood - a very good thermal insulator. The workmanship or construction solutions are chosen in such a way that the joints are well made and the wall does not 'fall apart' if the wood dries out. Insulating material (mineral wool, wool, polyurethane foam) is placed between the logs and beams to increase the insulation efficiency. The houses are warm in winter and cool in summer, ensuring the comfort of those inside.
Houses in CLT panels. The thickness of CLT allows it to be used as a structural element with outstanding strength and stiffness properties. The house structure consists of CLT panels which are used for walls and floors. CLT - industrialized wood - has significant advantages in terms of fire resistance, energy efficiency, acoustic performance or stability over time.
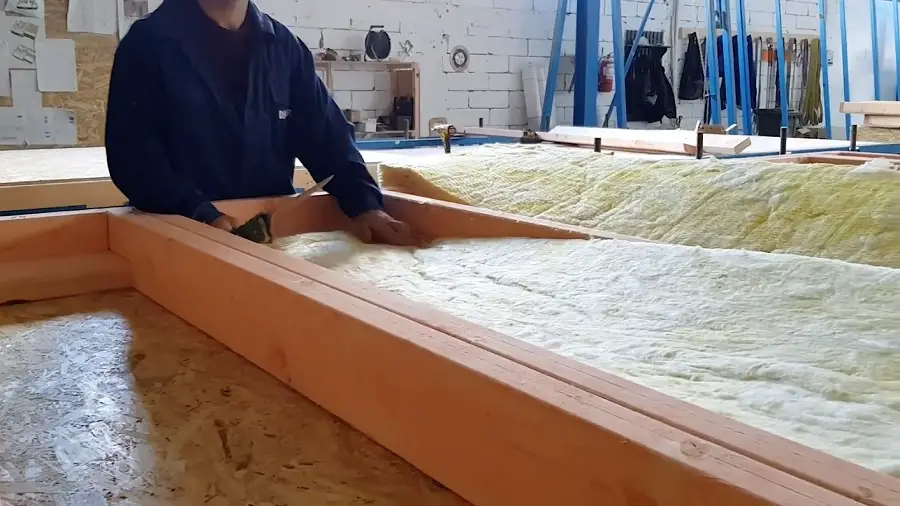
Passive House concept
Passive house is a concept that, although older, has become very relevant nowadays when people started to realize the environmental and economic impact of energy consumption for home comfort. It all started with Wolfgang Feist, a German physicist who built the first passive house. Read the full story here. Passive house design aims to reduce energy consumption and use renewable energy so that the house is independent from utility companies.
In general, this type of dwelling combines building systems and materials that work to our advantage to achieve pleasant and healthy conditions in the home. To realize such a home you need to understand how it works. It is about using architectural strategies and natural products to achieve indoor comfort with minimal energy needs that are covered by renewable, clean and cheap energy. Architectural strategies are simple ideas, such as south-facing windows or covering a terrace to protect it from the summer sun, but with an impact on energy consumption. In other words, resources such as daylight, solar energy, rainwater or natural ventilation are used as much as possible to achieve maximum comfort all year round. The materials used are important not only to achieve energy efficiency in the home but also in terms of carbon footprint. Wood is preferred not only for its excellent insulating qualities but also because it is natural, biodegradable and recyclable.
The passive house is very well insulated and has such high-performance windows that it no longer needs a traditional heating system. Heat losses are so low that heating and cooling energy savings are up to 90% compared to traditional houses and more than 75% compared to new construction. The energy source inside the building is the body heat of the inhabitants or solar heat entering the building. A mechanical ventilation system constantly introduces fresh air filtered of dust and noxious particles for superior air quality. A highly efficient heat recovery unit allows the heat contained in the exhaust air to be reused.
Passive house standard
To be certified as a passive house, a building must comply with several principles and meet certain performance criteria set by Passivhaus Institute from Germany. The principles are:
- continuous thermal insulation made with quality materials of the required thickness;
- high-performance windows and doors;
- solar gain in winter. The house is positioned according to the sun, large windows are mounted on the south facades and on the north facades, the number of windows is minimized;
- mechanized ventilation system with heat and moisture recovery.
Performance criteria are based on annual energy consumption:
- thermal load for heating max.10W/m²;
- heat demand for heating max 15 kWh/m²/year;
- space cooling needs max 15 kWh/m²/year;
- maximum 42 kWh/m² total annual energy demand.
- high air-tightness n50 ≤ 0.6 shifts.
The certification system is based on auditing buildings for thermal insulation performance, heat loss control, indoor air quality, solar energy use. The certificate attests that the house has very low energy consumption - close to 0 - for heating and cooling compared to a conventional dwelling. There are also companies in Romania accredited by the Passivhaus Institute that can design and accredit a passive house. There are also courses for all builders and architects interested in this type of construction.
We all want to pay as low energy bills as possible. We all want to live in homes that are warm in winter and cool in summer. Soon this desire will become an obligation. We need to understand the European Commission's approach as beneficial both for us and for our big home - the Earth. And that is why we must think as seriously as possible about the energy efficiency of our homes and try to improve it.
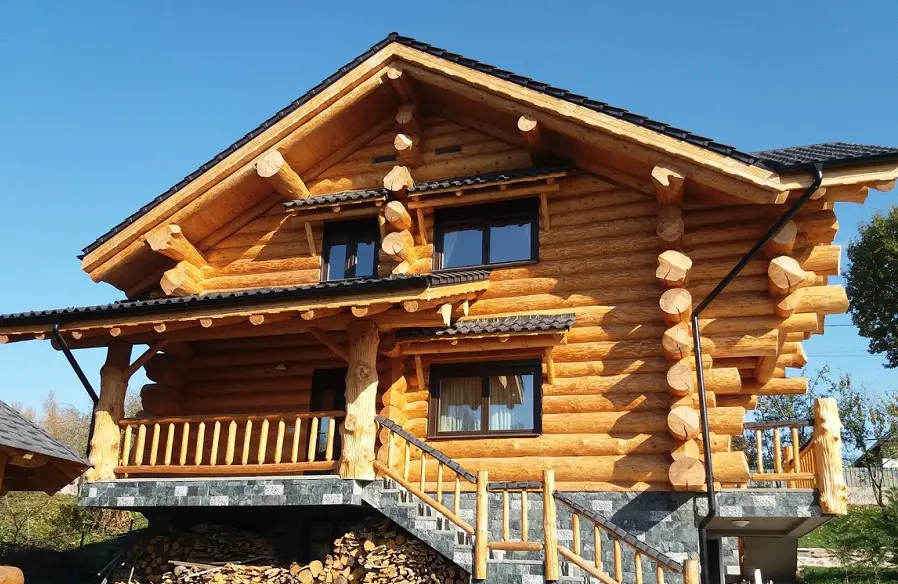
can you recommend a serious company able to build a turnkey mini-block with six apartments in the area of koln germany?
Thank you