Stratified Boards is a company from Mures which, with the help of European funds accessed through the Regional Operational Program (ROP 2.1), has succeeded in equipping a complete line for the processing of solid wood windows and doors, from the drying of the wood in the factory and its actual processing, to the finishing and exhaustare. Together with Nika Machinery, which won the tender by offering the best technological and commercial solution, a complete and complex plant was structured. The investment also followed the ecological aspect, the exhaustion part including a silo for the collection and reuse of the sawdust by briquetting.
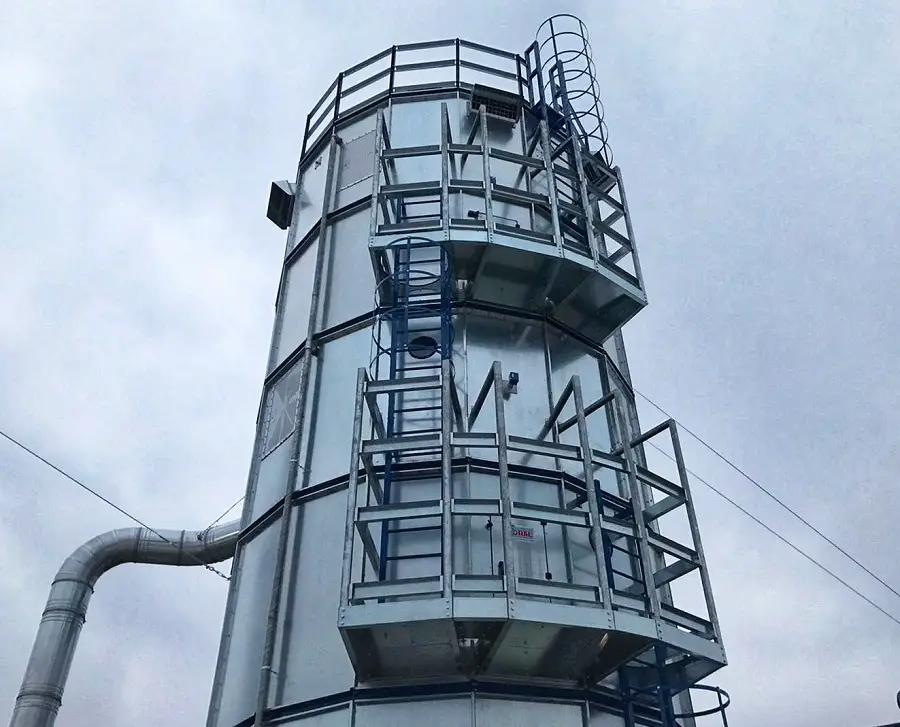
The project officially started on September 5, 2018 and ended on May 31, 2020. The value of the contract was, according to the statement on the website (ferestregold.com), over 2,300,000 lei, of which over 1,350,000 lei in non-reimbursable funds. He told us about the project developed in Miercurea Nirajului, as well as about the beginnings in window manufacturing and future plans Janos Szatmari, the company's technical director.
Start
The production of wooden doors and windows began, with enthusiasm and hope, in 2013, in a workshop in Miercurea Nirajului, Mures County. We were processing the wood with second-hand machinery and 6 employees, and only selling the products locally. The demand was growing, as was our interest to produce a higher quality and gradually we started to purchase special tools and devices, specific to the production of doors and windows. Gaining experience, we kept on improving the production technology and also increased the quality of the finished product by using quality raw materials and finishing materials available on the Romanian market.
They produced exterior and interior doors, windows and shutters, solid wood stairs. Now the offer has diversified and has been completed with the production of wooden and brick houses. The product range is rich, offering a variety of designs, colors and species (spruce, pine, oak). Particular emphasis is placed on safety, thermal and sound insulation, watertightness and, last but not least, finishing.
Our philosophy is that by producing laminated wood windows and doors, we bring life to buildings through the joy of their appearance and durability.
The desire for evolution and development, European funds and collaboration with
Nika Machinery
As we have been carrying out increasingly large and complex works, we have realized that if we want to face the competition and respond to market demand as well as possible, the only solution is to invest in new and high-performance machinery. In 2017, we decided to apply for a project financed by European funds under priority axis 2- Increasing economic competitiveness through the purchase of machinery. Following the public tender we realized the project implementation with the company Nika Machinery, a company that has won both the tender and our trust through the seriousness it has shown.
The project was very complex, involving 25 machines, from wood drying until painting doors and windowswith all necessary utilities. The production line is modern and complex, yet intuitive and easy to use by the operators. Every part of the factory was carefully thought out, whether it was wood processing or finishing. Environmental compliance was also emphasized, with the project including an exhaust air filtration unit of the spray booth and a complex silo for filtering exhausted air from machines and storing the complete sawdust with a sawdust briquetting plant.
This silo V Coral 4.4 is a very important machine from an environmental protection point of view. It filters the air of the sawdust generated in the wood-processing processes, ensuring a safe environment for the workers. The resulting sawdust is automatically collected in the silo, which is connected to both a boiler and the briquetting plant. The hot water produced by the boiler is used to dry the wood, to ensure an optimal temperature for the painting process in pressurized spray boothas well as for heating the hall. By using these technologies, virtually all waste from the production process is utilized.
The specialists of Nika Utilaje delivered and installed all these machines on time, providing technical assistance until the factory reached the expected parameters, but also during the warranty and post-warranty period.
At the moment, all project documentation is finalized and has already been checked and settled by the Managing Authority. The value of the project amounted to about 400.000 euro, but at the end of the project we managed to have a modern, totally changed wood processing enterprise.
Technical solutions allow us to accept highly complex orders
As I said, it was a complex project involving 25 machines. We now have lumber dryer with associated central heating plant, compressor with dryer and a modern silo for the collection of sawdust with all the necessary exhausting equipment. The door and window profiling section now has a modern milling machine with automated operations, a 4-sided profiling machine with 5 shafts, both equipped with tools for making the Eurofalz profile with a wood thickness of 68-78-78-92 mm and all the classic woodworking machinery you need in a factory. The finishing department is equipped with a sanding and calibrating machine of the highest quality and a pressurized spray booth with all necessary facilities.
All these technical solutions allow us to take on highly complex orders and execute them at the highest technical and quality level.
We all realize that it is not easy to implement such a large and complex project with so many machines. And the deadlines have to be respected because there are checks to certify that the machines exist and are working in production. Only then can the money be paid out. Difficult moments always arise and are not always easy to get through. I asked Janos Szatmari Now, at the end, how do you see this whole adventure? What was the hardest thing to accomplish?
We have gone through all the stages of a project with European funds. But with hard work and competence from us, the consultant and Nika Utilaje, we managed to get to the end. Of course there were some difficulties, but we managed to overcome them all. Now we're laughing at the moment when the power went out The same day when the final tests were being done on the drying room and the heating plant, or when we had to move the location of the 16-meter high silo. We always found solutions and managed to get everything completed successfully.
Future plans
Although the project has just ended, the plans don't seem to stop there. There is a desire for more and better, for automation and expansion into other markets.
At the moment we are satisfied with the result of the project implementation. With the new line we manage to achieve the desired increase in production, both quantitatively and quantitatively.i from quality and efficiency. We want to continue to equip the company with modern, automated machines, with software design of doors, windows and stairs. In the future, we want to increase the company's competitiveness, increase our share of market and to expand into foreign markets.
So it can be done! I know, it's cliché, but that's the reality. It's not easy, there are hurdles and moments when you think it was probably better not to start. But Janos Szatmari, Binale Stratified and Nika Machinery just showed us that it can be done. Coming up next national and European development programs and funds that can be accessed. Here's food for thought!
Add comment