Wood has been used since ancient times to make furniture, to build houses, boats, the fuselages of early airplanes and many other objects. Modern materials such as steel, concrete or plastic have replaced it because they were much better in terms of strength and hardness. But now the performance of a material is also judged in terms of its environmental impact, and wood is the clear winner. So it's back in the spotlight, and scientists are finding new ways to improve its performance. Such is the case group of researchers from the University of Maryland which has produced a wood with remarkable properties, 12 times stronger and 10 times harder than before treatment, comparable to steel, titanium alloys or carbon fiber.
Removing part of the lignin and pressing the heated wood
Treating may not be the most appropriate term because the wood is not treated with any other substance but only processed in a certain way. Unlike Accoya or Kebony, where the wood has been treated with different resins to increase its resistance to the outside, super wood - as it was called - was subjected to a partial delignification treatment followed by pressing.
The main materials that make up wood are cellulose, hemicelluloses and lignin. They are what create the wood cell. Cellulose and hemicelluloses form the matrix, and lignin impregnates the matrix, which gives the wood stiffness, weight and color. Researchers at the University of Maryland, who have in the past transparent woodThey subjected the wood to partial delignification with chemicals and then pressed it for 24 hours, during which time the wood was continuously heated to 65°C.
The partial removal of the lignin made the wood lighter and spongy. Subsequent pressure collapsed the cell walls, causing the cellulose fibers to compact and form new, very strong hydrogen bonds. The pressing also eliminated defects such as voids, twisted fibers or knots, and the properties of the wood became more uniform.
It should be noted that researchers have succeeded in finding that limit of delignification that leads to remarkable performance of the obtained material. A higher or lower percentage of lignin removed leads to very different results, with the resulting wood performing much worse. It is all due to the hydrogen bonds formed when the percentage of lignin remaining in the wood structure is optimal.
A wood with new properties, much stronger and tougher
The resulting wood is 5 times thinner than it was originally, but 12 times stronger and 10 times harder. Nails were made from this material and hammered into the wood by passing it easily through 3 plates or knives that cut thick pieces of beef. The material was also shot with bullet-like projectiles, which passed easily through the normal wood but failed to penetrate the densified wood. The test can be seen here.
When used in construction, wood is reproaches that, although it is very strong along the grain, it fails when force is applied perpendicular to it. In the case of densified wood, it takes 10 times the force to cause it to fail. Densified wood is just as strong as steel, but 6 times lighter. Researchers believe the new material could be used to make cars and airplanes, in construction - basically anywhere steel is used.
Applying the method industrially would allow the use of fast-growing species with very low strengths and hardness to produce a very strong material that is both biodegradable and has a low carbon footprint. This would protect species with very good qualities but very slow growth. Combined with permanent reforestation and sustainable harvesting, it would be a very good way of using high-performance materials without harming the environment and the health of the planet's inhabitants.
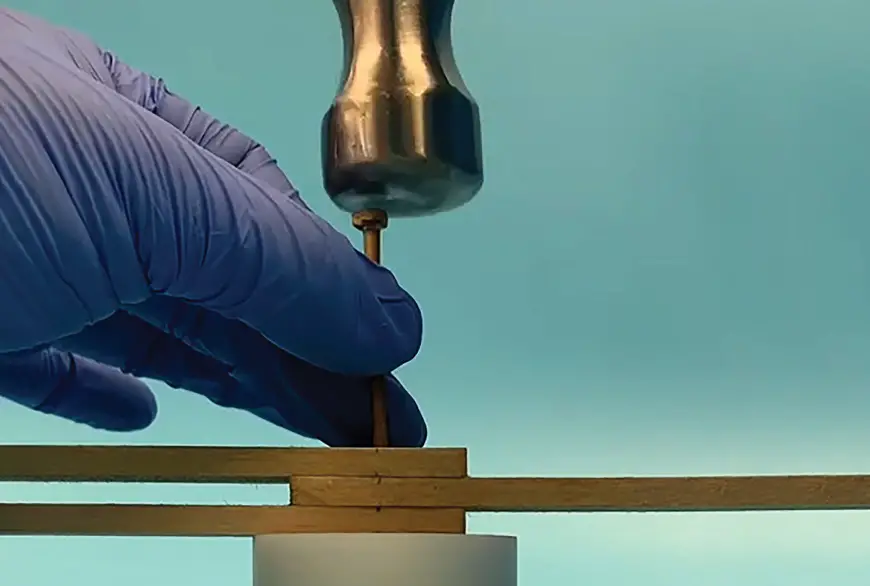
Although very resilient, water remains a vulnerability
As no material is perfect and super wood has its weakness, namely its vulnerability to water. The new material does not lose wood's recognized affinity for water, and as humidity increases, its physical and mechanical properties decrease. So densified wood must be protected from water and moisture in order to benefit from its special properties. One method of keeping water out is coating or partial impregnation with oils. This is a method inspired from the past when protecting boats was done with oil or tar obtained by heating wood at high temperatures.Â
But the affinity for water is useful for wood biodegradation. Current requirements are to increasingly use biodegradable products that do not harm the environment in the long term. Wood is such a material, but it needs water to degrade. That's why the fine balance between moisture resistance and moisture affinity must be found.
The 21st century seems to be about wood
Although the first densified wood was obtained more than 5 years ago, the results of the research have not yet reached industrial level. But it is a process that requires time and investment, and the group of researchers have already established some contacts. That level will certainly be reached, because the 21st century seems to be about wood. The emergence of new and new industrialized products that make the construction industry use it more and more shows the desire to make wood as high-performance a material as possible. And super wood is such a material.
To continue to enjoy wood and its special qualities, however, we need sustainable forest management, permanent afforestation and solutions for using species that are considered inferior but are much faster-growing.
Add comment