Manchmal kann man in der Fabrik, nachdem der Veredelungsprozess abgeschlossen und die Folie getrocknet ist, feststellen, dass ein weißer Fleck entsteht, wenn die Oberfläche angestoßen wird oder etwas darauf fällt. Er sieht aus wie zerbrochenes Glas. Man könnte meinen, dass der Lack daran schuld ist, weil er zu hart oder zu spröde ist. Das Auftreten des weißen Flecks deutet in Wirklichkeit auf eine mangelnde Haftung auf dem nicht hölzernen Untergrund hin. An dieser Stelle hat sich der Lack durch mechanische Einwirkungen leicht gelockert, und es ist Luft zwischen den Lack und das Holz gelangt. Der Lackfilm bleibt praktisch in der Luft hängen und reißt. Eine mangelnde Haftung kann auch zwischen den aufgetragenen Materialschichten auftreten. Auch in diesem Fall äußert sie sich durch das Auftreten eines weißen Flecks nach einem mechanischen Stoß.
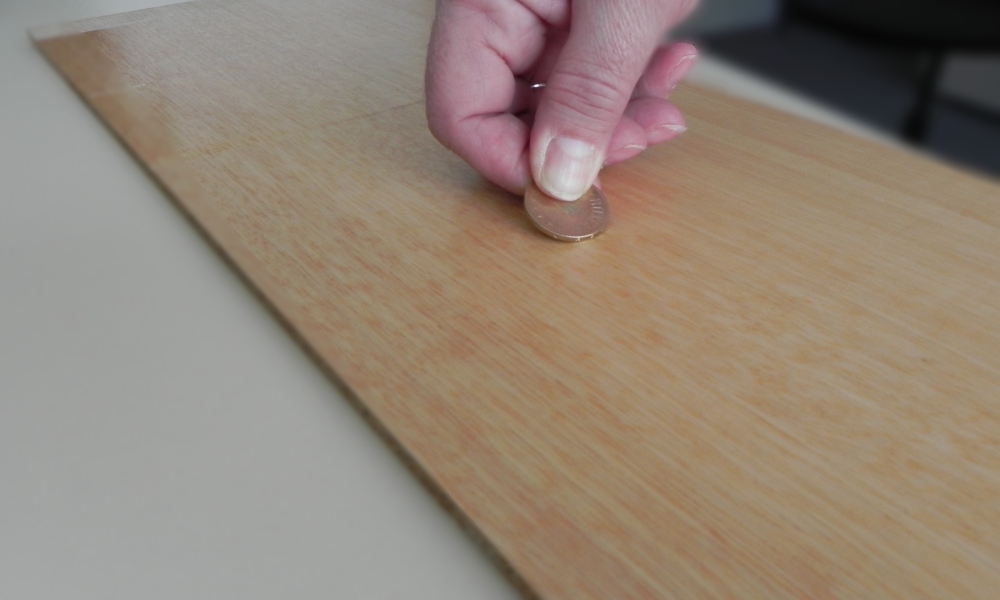
Wie man ohne spezielle Maschinen die Griffigkeit prüft
Die einfachste ist der Münztest. Ziehen Sie dazu mit dem Rand einer Münze über die lackierte Oberfläche. Wenn ein ziemlich breiter, weißer Streifen erscheint, bedeutet dies, dass die Haftung nicht mehr gegeben ist, die Schichten sich getrennt haben und Luft eingedrungen ist.
Eine weitere Möglichkeit zur Überprüfung der Griffigkeit ist Netzwerktest. In einem weniger sichtbaren Bereich wird mit einem Cutter ein Gitter wie beim Spiel "x und o" erstellt. Die entstandenen Quadrate sollten 1-3 cm groß sein. Klebe ein Stück Klebeband über das Gitter und reiße es ab. Wenn mehr als 6 Lackquadrate auf dem Klebeband verbleiben, haftet der Lack nicht mehr.
Bei Lacken auf Lösungsmittelbasis kommt es zum Filmabbau. Bei Lacken auf Wasserbasis tritt ein anderes Phänomen auf. Der Film, der sich nach dem Trocknen bildet, ist das Ergebnis einer dreidimensionalen Polymerisation, bei der die Moleküle fest miteinander verbunden sind. Wenn der Film nicht auf dem Untergrund oder der Grundierung haften bleibt, wird er abgeschlagen. Es bleibt ein weißer Streifen zurück, der aber nicht reißt, sondern wie eine Haut abgezogen werden kann.
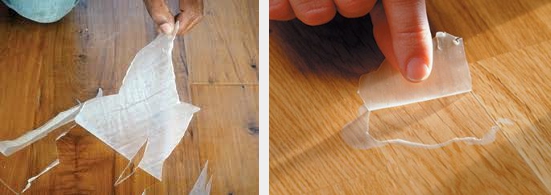
Was die Ursachen sind und was Sie tun müssen, um sie in den Griff zu bekommen
Die Hauptursache für diesen Fehler ist unsachgemäßes oder gar kein Abschleifen. Das Verfahren ist gleichermaßen wichtig, ob es sich um das Schleifen der Holzunterlage oder das Schleifen zwischen den Schichten handelt.
Beim Schleifen der Holzunterlage ist die Qualität abrasive Stoffe und es ist sehr wichtig, sie bei Beschädigung zu ersetzen. Im Grunde genommen ist die Haftung das Ergebnis davon, dass die Grundierung so gut wie möglich in das Holz eindringt und es festhält. Je besser das Holz geschliffen wird, desto rauer ist es, um die für eine gute Haftung notwendige Rauheit zu erzeugen. Diese optimale Rauhigkeit muss gefunden werden. Eine zu hohe Rauheit erschwert das Schleifen der Grundierung und mindert die Qualität des Finishs, eine zu geringe Rauheit führt zu schlechter Haftung.
Im Allgemeinen beträgt der weiße Endschliff bei Möbeln 180-220 Körnung und bei Fenstern 120-150 Körnung. Schleifmittel sollten gewechselt werden, wenn sie mit Holzstaub belastet sind oder nach der vom Hersteller empfohlenen Nutzungsdauer. Das stark beanspruchte Schleifband ist mit Holzstaub belastet und das Schleifmaterial wird zerkleinert. Das Ergebnis ist ein feinkörnigeres Band, das das Holz nicht mehr abschleift, sondern glättet. An einigen Stellen kann es sehr glatte und glänzende Bereiche geben, die als Spiegel bezeichnet werden und an denen die Haftung sehr gering ist.
Eine zu hohe Viskosität beim Auftragen ist eine weitere Ursache für schlechte Haftung. Aufgrund der hohen Viskosität kann die Grundierung nicht in das Holz eindringen und aushärten. In diesem Fall sollte die Verdünnung entsprechend den technischen Datenblättern und Anwendungstechniken erfolgen, und die Viskosität sollte mit Viskositätsbechern kontrolliert werden.
Adhäsion zwischen den Schichten
Dasselbe gilt für das Schleifen zwischen den Anstrichen - Sie müssen Rauheit erzeugen, damit die nächste Schicht greifen kann. Es gibt aber auch Ausnahmen. Dies ist der Fall bei Nitrozelluloselack, der nicht geschliffen werden muss, damit die nächste Schicht haftet. Die Verdünnung in der Deckschicht weicht die Grundierung auf und die Kontaktfläche verschmilzt.
Dies ist bei polymerisationshärtenden (trocknenden) Lacken wie Polyurethan nicht der Fall. Damit die nächste Schicht haftet, muss die nächste Schicht sofort nach dem Schleifen zwischen den Schichten aufgetragen werden. Polyurethanlacke brauchen länger, um in der Tiefe zu trocknen, sind aber oberflächlich in 2-3 Stunden trocken. Wenn die oberste Schicht abgeschliffen wird, wird der weichere Teil erreicht und die Haftung ist viel besser. Lässt man den Lack nach dem Abschleifen länger als 3 Stunden stehen, trocknet die Deckschicht wieder oberflächlich und die Haftung nimmt ab. In der Zeit, bis die Oberfläche trocken ist, kann die nächste Schicht ohne Schleifen aufgetragen werden, die so genannte "Nass-in-Nass"-Methode. Es dauert nur 15-20 Minuten, bis ein Teil der Verdünnung verdunstet ist.
Auch wasserverdünnbare Lacke müssen geschliffen werden, da ihre Aushärtung ebenfalls durch Polymerisation erfolgt. Wenn Wasser verdunstet, kommen die Moleküle zusammen und reagieren miteinander, um den Lackfilm zu bilden. Deshalb kann man den Lackfilm nicht mit seinem eigenen Lösungsmittel (Wasser) angreifen, wie es bei Nitrocelluloselacken der Fall ist.
Wie bei den anderen Verarbeitungsfehler ist es wichtig, ihre Ursachen zu erkennen und zu vermeiden.
Ich hoffe, Sie finden die obigen Informationen nützlich. Ergänzungen sind wie immer willkommen. Und wenn Sie Fragen haben, können Sie diese in dem unten stehenden Feld stellen. Ich bin sicher, ich werde Ihnen antworten.
Kommentar hinzufügen