Sometimes, in the factory, after the finishing process has been completed and the film has dried, it is noticed that if the surface is hit or something falls on it, a white mark appears. It looks like broken glass. One may think that the varnish is to blame, being too hard or too brittle. The appearance of the white mark actually indicates a lack of adhesion to the wood-free substrate. In that place, the varnish has easily come loose due to mechanical shock and air has penetrated between the varnish and the wood. The varnish film practically remains suspended in the air and breaks. Lack of adhesion can also occur between layers of applied material. In this case, too, it manifests itself in the appearance of a white mark following a mechanical shock.
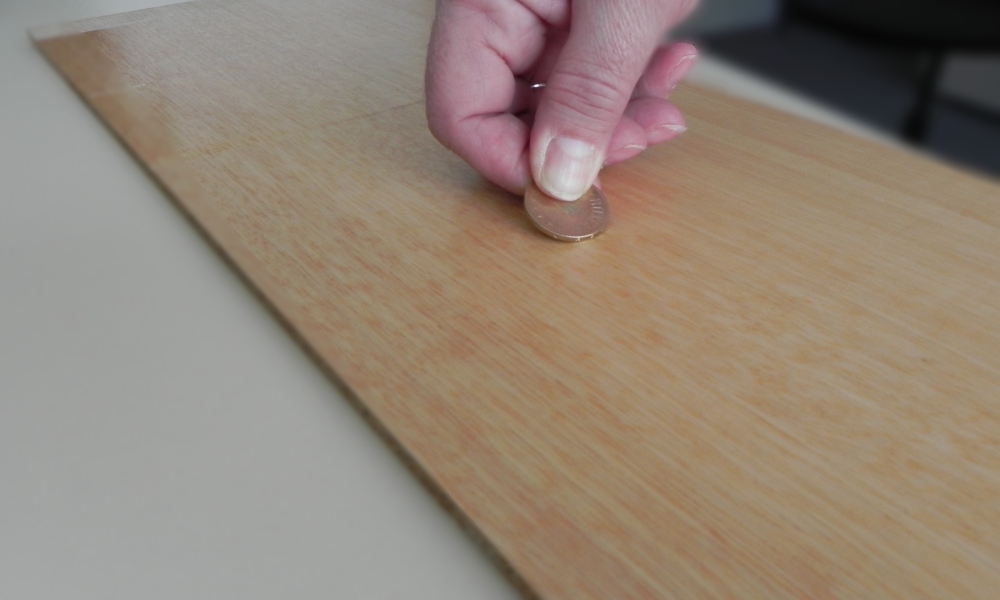
How to test for poor grip without special equipment
The simplest is coin test. Basically, you pull the edge of a coin over the varnish-coated surface. If a white, fairly wide mark appears, it means that there is no adhesion, the layers have peeled off and air has penetrated.
Another way to check adhesion is to grid test. In a less visible area, make a grid with a cutter like in the game "x and o". The resulting squares should be 1-3 cm wide. Stick a piece of tape over the grid and tear it off. If more than 6 of the varnish squares remain on the tape, the varnish has no adhesion.
Film breakage occurs in solvent-based varnishes. With water-based varnishes, a different phenomenon occurs. The film formed after drying is the result of a three-dimensional polymerisation that makes the molecules tightly bound to each other. If the film does not adhere to the substrate or to the lower layer, it is detached by impact. A white trace still appears, but it does not break but can be peeled off like a skin.
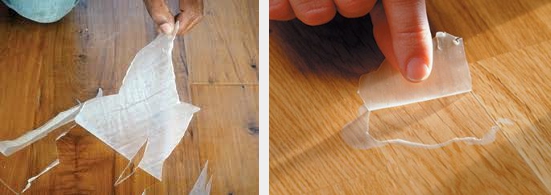
What are the causes and what to do to have a good adhesion to the support
The main cause of the defect is improper sanding or lack of sanding. Whether it is sanding the wood backing or sanding between layers, the process is equally important.
In the case of sanding the wood backing, the quality abrasive materials and replacing them when damaged is very important. Basically, adhesion is the result of penetrating the primer as well as possible into the wood and gripping it. The more correctly the wood is sanded, the more roughness is created for a good bond. This optimal roughness must be found. If it is too high it will make it very difficult to sand the primer afterwards, lowering the quality of the finish, and too low a roughness will lead to poor adhesion.
In general, final white sanding is done with 180-220 grit for furniture and 120-150 grit for windows. Abrasives should be changed when dusting or after the period of use recommended by the manufacturer. Heavily used abrasive tape is loaded with wood dust and the abrasive material is shredded. The result is a finer-grained belt that no longer sands the wood but smoothes it. In some places there may be very smooth and shiny areas, called mirrors, where adhesion is very low.
Too high viscosity on application is another cause of poor adhesion. Being very viscous, the primer can't penetrate the wood to grab hold. In this case, the application should be done according to the technical data sheets and application technologies, and the viscosity should be controlled with viscosity cups.
Adhesion between layers
The situation is the same when sanding between coats - roughness must be created so that the next coat can grip. There are exceptions. This is the case with nitrocellulose varnish, which does not need sanding for the next coat to adhere. The thinner in the top coat softens the bottom coat and the contact area blends.
This is not the case for polymerisation-curing (drying) varnishes such as polyurethane varnishes. In order for the next coat to adhere, the application of the next coat must be done immediately after sanding between coats. Deep drying of the polyurethane varnish layer takes longer, but surface drying takes 2-3 hours. If the top coat is removed by sanding, the softer side is reached and adhesion is much better. If left for more than 3 hours after sanding, the surface layer dries again and adhesion decreases. In the time until the surface dries, the next coat can be applied without sanding, the so-called wet-on-wet method. Only 15-20 minutes are needed for some of the thinner to evaporate.
The water-based varnish also needs to be sanded because it hardens through polymerisation. When the water evaporates, the molecules come together and react with each other, forming the varnish film. This is why the varnish film cannot be attacked with its own solvent (water), as in the case of nitrocellulose varnish.
As with the other finishing defectsit is important to identify their causes and avoid their occurrence.
I hope you find the above information useful. As usual, additions are welcome. And if you have any questions or queries, please leave them in the space below. I'm sure I'll reply.
Add comment