Another production experience again led to an article. During some tests, small flaws appeared on the surfaces where the lacquer was applied, spoiling the final appearance. As the general opinion was that it was the varnish that was to blame, the contrary had to be proved. And I assure you it is not the easiest thing to do. But let's see how it all started.
The purpose of the visit was to test products for finishing veneered MDF doors and MDF board objects. The requirement was to apply both transparent and opaque pigmented products. The materials were applied in a dedicated finishing room, where there was a regular dry-filter spray booth with a normal spray gun with a can. The site has exhaustion plant in both the mechanical processing and finishing areas.
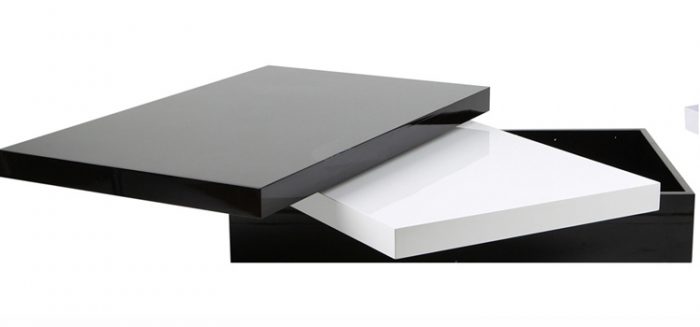
The first day was used to prepare the surfaces prior to varnish application. That is, the veneered MDF boards were thoroughly sanded, and the MDF boards were sanded only in the mechanically machined areas. Two coats of primer were applied, wet-on-wet, clear on the veneered MDF and white on the unfinished MDF. Between coats, 20-30 minutes were allowed to allow the first coat to flash a little, after which the boards were left to dry until the following day.
The next day all surfaces were sanded first and then the varnishes were applied. And this is where the problem started. Small impurities appeared on the varnished surface as if the varnish had not been well filtered or had solid deposits.
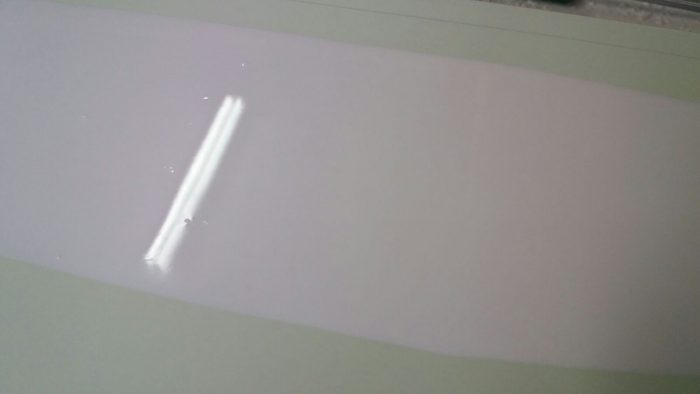
We were convinced it was not the varnish's fault, but we had to prove it. So, here's what you can do to see if the fault is the varnish, the application system or the environment:
- apply, under the same conditions, another material with the same characteristics. That is, if the defect appeared on a white gloss varnish, try using a clear gloss varnish. If the film will have exactly the same defect it is impossible that the 2 gloss clearcoats will have the same problem;
- if the applied product is a 3-component (with catalyst and thinner), change the whole system. Otherwise you will not be sure whose fault it is. The moment all 3 components are changed and the defect remains unchanged, the fault is definitely not the finishing materials;
- Mix a small amount of the materials (varnish, catalyst and thinner) in exactly the original proportion and pour it onto a piece of plate. If the defect appears, then you can remove the gun and the compressed air with the whole filter system from the guilty party.
- by eliminating the above it is clear that the fault is environmental. Don't be fooled by the fact that there is an exhaust system that removes impurities. Sometimes the lack of filters on the trails can cause impurities to get into the spray area.
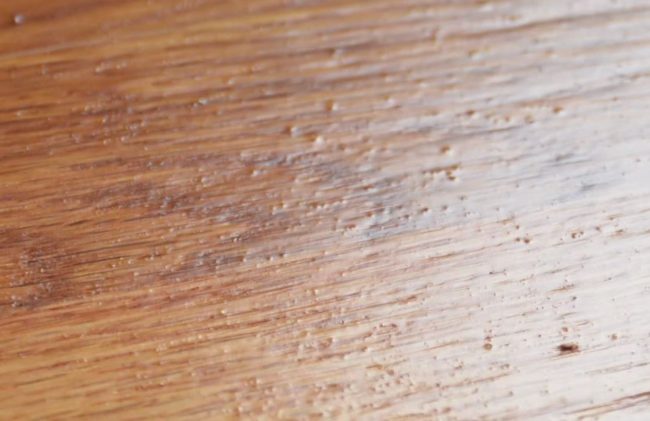
Impurities in the finishing and drying areas are the biggest enemy of film quality. To avoid their appearance it is best to make sure that:
- the mechanical processing area is as far away from the spraying area as possible;
- the filters used at the cabin have been thoroughly shaken and vacuumed (even if new). To remove impurities, after shaking, leave the suction in the spray booth to run for a long time;
- before spraying, splash water on the floor. Water attracts dust. Do not sweep the area until you have finished applying the products and the lacquered tiles have been moved to another room;
- if possible, introduce more air into the room being sprayed than is being removed. This will create an overpressure that will keep impurities at bay. This is basically how a pressurized spray booth works. Or invest in a pressurized spray booth. You won't regret it.
- do not work with very high air pressure. It creates currents that entrain dust particles in the area.
You may think that it's simple to distinguish a lint or a speck of dust from a defect that's the fault of the varnish. I assure you it is not that simple. I have seen varnish defects that look very much like a speck of dust or a hair. Especially when it comes to curing varnishes. A very good example can be waterborne hardeners. If the hardener is not mixed very well with the base product and water is added to dilute it, small solid particles very similar to sand may form on contact with water. In this case it is therefore recommended to mix the two components very well before dilution or, much better, to dilute the base product with water first, homogenize and add the catalyst at the end.
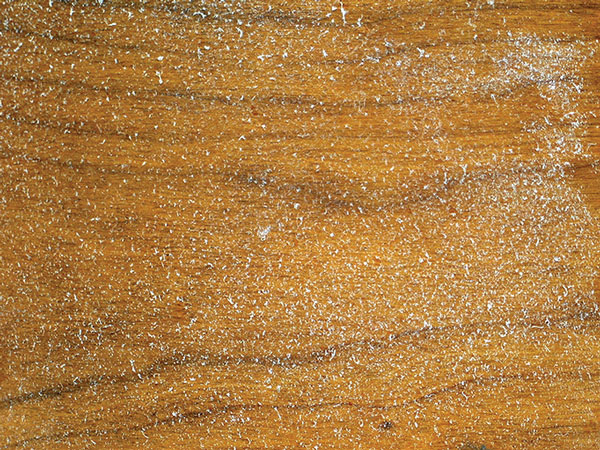
What I've learned from this experience is that you can only convince people of the truth of what you say with patience and by demonstrating it. In a dispute there are several points of view and everyone is convinced of their own truth. To win you need convincing arguments.
Nice and interesting article! Congratulations !