Manufacturing pallets for nearly 40 years, Indiana-based Coomer & Sons Sawmill has grown from a start-up in a small garage to a commercial-level operation producing thousands of pallets a day. The family-owned company has worked with a variety of production equipment over the years, but today operates three Wood-Mizer WM4000 thin-cutting industrial Wood-Mizer WM4000 thin-cutting industrial bandsaws and two multi-head resawing bandsaws for primary and secondary cutting of logs into pallet components. Over the years, Coomer & Sons has continued to succeed in tough economic times and overcome unfortunate mishaps by developing a solid business model, taking care of their employees and providing excellent service.
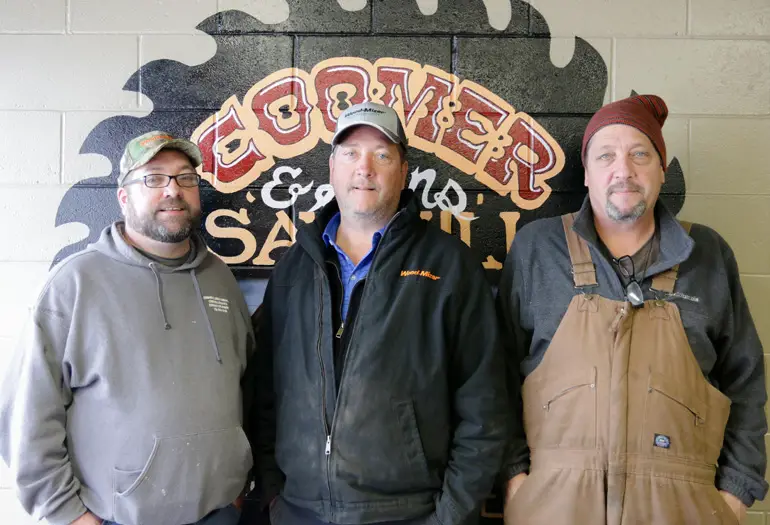
History and development
Founded by Charles Coomer in 1978, Coomer & Sons Sawmill is a family owned and operated business with its beginnings in a garage in Frankfort, Indiana, with four employees producing about 75 pallets a day by hand. Throughout the 1980s and 1990s, Coomer & Sons grew rapidly, moving into larger buildings and installing automated production equipment to keep up with the demand for their products. During this period of growth, the company developed a close working relationship with nearby Wood-Mizer's Indianapolis headquarters, just 45 miles south of Frankfort. The Coomer family has owned Wood-Mizer bandsaws for decades, operating one of the first multi-head resawing bandsaws in the early 1990s. Coomer & Sons has also become a valuable partner in testing prototype equipment and blades for the Indiana-based bandsaw manufacturer.
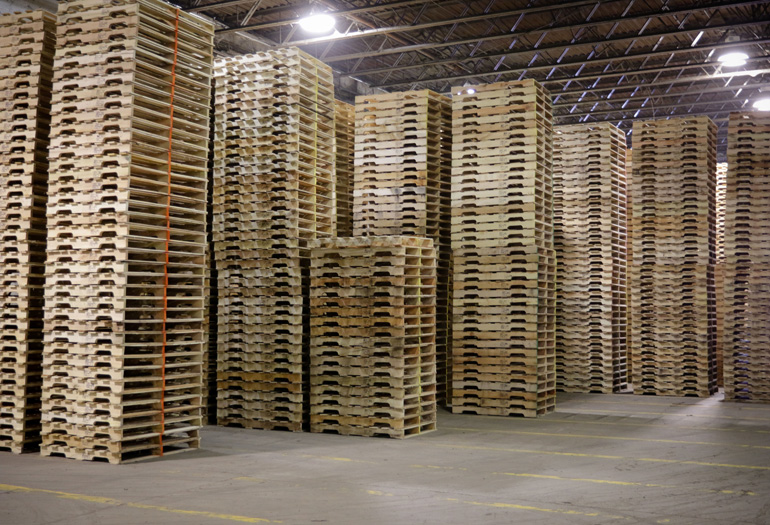
In 2007, the family business changed leadership after the death of Charles Coomer. His son, Jeff, bought the firm and became president just before the economic downturn in the late 2000s. During those bad times for business, Coomer & Sons continued to be profitable by offering second-hand pallets to companies trying to economize in any area of their business. "When the economic situation was bad, we started making used pallets and within a year we were already a fully developed pallet business, selling one and a half million pallets a year."said Jeff Coomer. "It grew so fast because everyone at the time wanted used pallets instead of new pallets to save money." By diversifying the business, Coomer & Sons has developed a successful model by supplying new and second-hand pallets to a variety of international customers shipping automotive filters, plastics, recyclables, tires and more. Combined, the market cycles of each customer's industry provide constant demand to avoid large gaps in production. In addition to new and used pallets, today, Coomer & Sons also supplies specialized heat-treated pallets for international shipments and complements its pallet business by offering by-products from production, such as mulch and firewood from log ends.
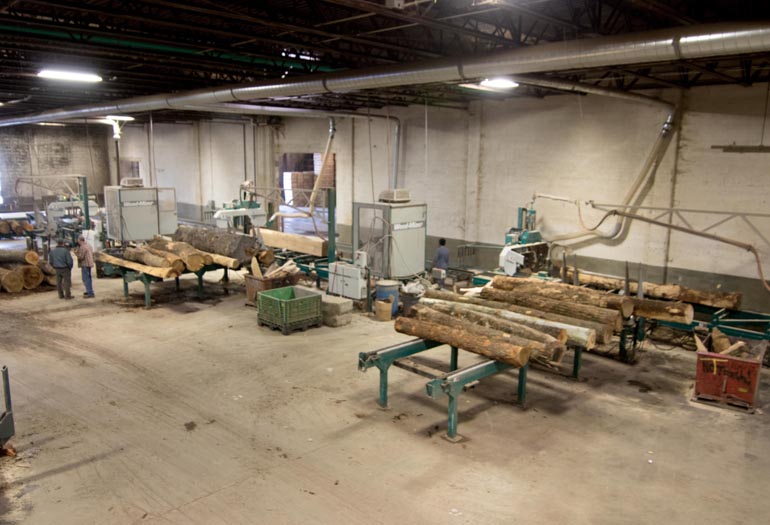
The success of the family business continued until June 2014, when Coomer & Sons experienced a tragic fire that completely burned the building and production equipment. Although no one was injured, the business suffered major losses. At the time of the fire, the company was using a circular saw and two older models of industrial Wood-Mizer industrial bandsaws to manufacture pallet boards. This setup was efficient in producing pallets at a rate of 1,500 pieces per day, but Jeff knew there was room for better. Fortunately, Jeff had purchased a building six months earlier and decided to start rebuilding the family business in the new location. During the remainder of the year, Coomer & Sons installed three Wood-Mizer WM4000 industrial Wood-Mizer WM4000 industrial bandsaws, green chain, conveyor and HR1000 industrial bandsaw for the restart of production. "We decided to replace the circular saw, which I think was a very wise choice because now that we've had these three saws [WM4000] for two years we can see the results of less waste, less sawdust and more profit at the end of the day."Jeff said. Today, Coomer & Sons cuts up to 18,000 board feet of oak, ash, ash, hickory, maple, sycamore, elm, and cotton each day to produce more than 3,000 pallets daily - double the amount of pallets produced on previous circular and ribbon saws. The company continues to grow its operations with the scheduled addition of a Wood-Mizer WM1000 industrial Wood-Mizer WM1000 industrial bandsaw later this year. The WM1000 will allow Coomer & Sons to cut large logs up to 67" in diameter.
Making pallets with the WM4000 industrial saw
First the logs are peeled, then transported to the main building for processing. Once the logs are sorted, they are passed through one of three WM4000 industrial WM4000 bandsaws for primary sawing and then fed onto a conveyor that leads to the green chain. The prisms are then hemmed and cut to length on the slitting saws. The prisms are then passed through one of two multi-head cutting bandsaws for cutting and making the upper deck planks and stringers before final assembly into pallets using an automatic nail-shooting machine. The finished pallets are either delivered the same day or stored inside the 88,000-square-foot facility.
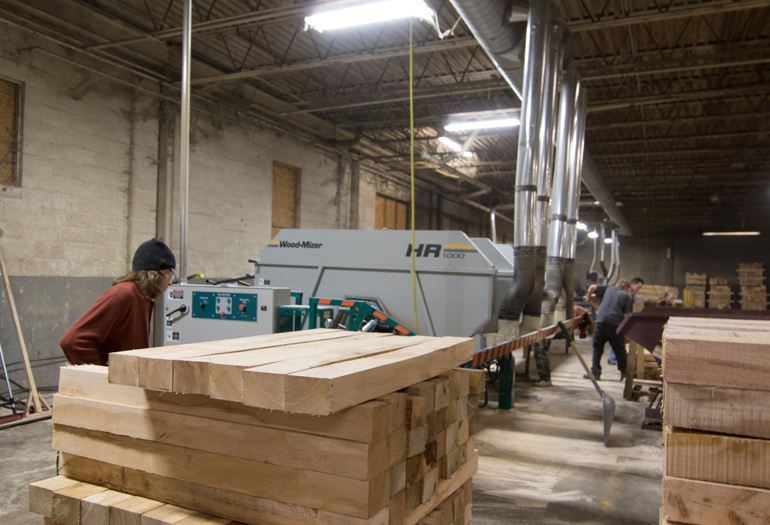
Troy Shimmel, has been with Coomer & Sons for 15 years and says "WM4000 is great to work with". Compared to older models of Wood-Mizer bandsaws, Troy says the WM4000 cuts logs much faster and praises the improved log handling features. "I can cut bigger logs and the log turner is double"Troy said. "It has three stops on the back instead of two, which helps keep the logs on the saw bed." Jeff says the WM4000s saws are an integral part of the pallet operation and points out that the computerized positioning system provides accuracy and efficiency when cutting logs. "WM4000 saws are great machines", Jeff said. "I think Wood-Mizer has proven that you can use less material to make a better saw; heavier doesn't always mean better. The simplicity of Wood-Mizer equipment is just really beautiful."
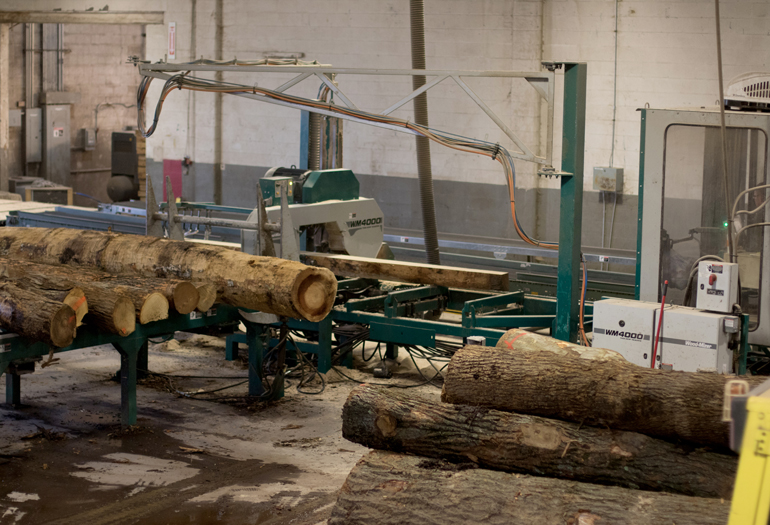
Coomer & Sons equips its wood-cutting equipment with Wood-Mizer blades and has its own blade sharpening and waxing equipment. By owning their own blade maintenance equipment, they save money on shipping and can sharpen their blades up to four times before needing a new blade. "When I get a canvas from Wood-Mizer I can cut a lot of material with it, even after it's been re-sharpened two or three times"Troy said. Coomer & Sons was one of the test sites for Wood-Mizer's new Vortex ribbon-web from Wood-Mizer for ribbon saws and resawing ribbon saws. The reshaped profile of the cloth is designed to remove sawdust during flow to minimize or eliminate the need for sawdust removal after wood processing. "The Vortex blade removed 98 up to 99% of sawdust and it was impressive how much sawdust it removed compared to a typical saw blade"Jeff said. "We have many transactions with a filter company where, if there is dust on the pallet, it gets into the filters and becomes a major problem. Our goal is to get the 100% 100% dust removed. If you don't remove the dust, you lose the customer." Currently, Coomer & Sons takes several measures to ensure dust-free pallets for their customers, including the use of a de-dusting machine and also by brushing the final product during assembly. The innovative Vortex sail can reduce the labor and time associated with removing sawdust from the end product.
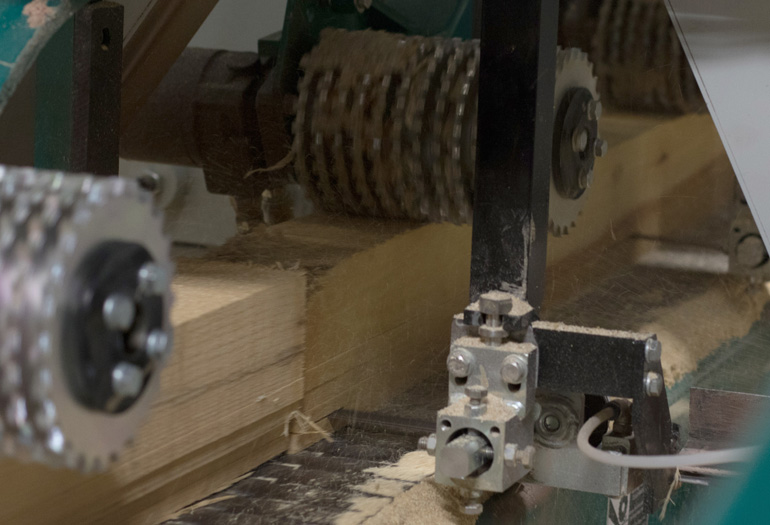
With a proven ability to adapt with the times, Coomer & Sons is positioned for continued success, wherever it goes. "In the pallet business, anyone can sell and build pallets, I think we sell services"says Jeff. "If you stick to your time frame and do a good job on the service side, you keep your customers. Our service is exceptional and you can't replace that."
Author: Chase Warner
VIDEO: Coomer & Sons, a family-run pallet factory, produces 3,000 pallets every day with WM4000 industrial WM4000 bandsaws
Add comment