We all like houses in bușteni or those clad with planks, furniture and solid wood flooring or beams and the wooden supporting pillars in the attic. We consider all solid wood to be both beautiful and durable. We forget, however, that there are many other derivatives of wood which, although they do not match the natural and sometimes wild beauty of wood, are more stable and stronger. I'm thinking of solid wood panels, laminated wood, paneling and plywood, but also those that are sometimes looked down upon, such as MDF or chipboard, but are present in most homes (sometimes without even knowing it). I've talked about some of them before, telling you about the history of their appearance or how they are finished. This time, I will briefly present all these wooden semi-finished products, trying to highlight both their pluses and minuses.
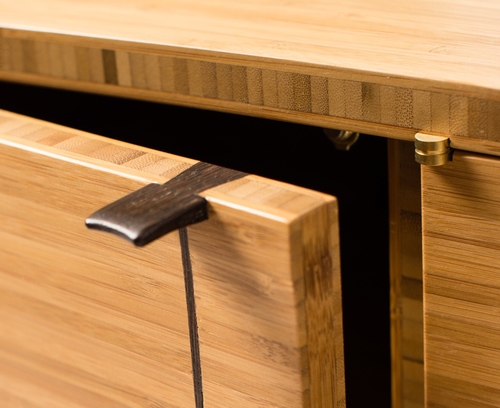
Massive panel is made from equal pieces of solid wood, properly dried and cut to size, which are glued together, both lengthwise and widthwise to form a panel. Elements of the desired length are first obtained by finger-jointing or straight-jointing several pieces of wood.
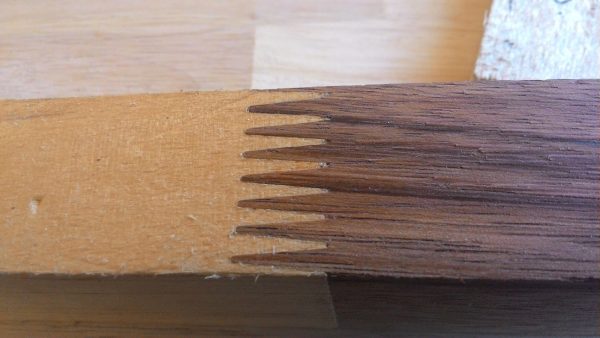
photo source: puspamandiri.com
Then glue is applied lengthwise on one side. The pieces of wood thus prepared are placed side by side in the presses and kept there until the adhesive hardens (cold hardening, i.e. at room temperature). Finally the panel is sanded to remove excess cured adhesive and then calibrated.
The advantages of such boards are their better stability and much larger dimensions compared to planks cut from logs.
Disadvantages: discontinuity of the wood design, possibility of delamination, problems of unevenness in staining or highlighting of glue lines.
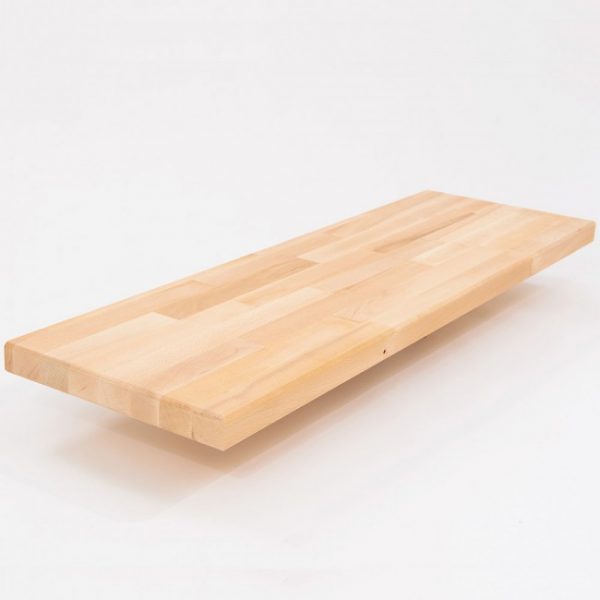
The panel is made from a middle, a core, made of solid wood strips, placed between two sheets of technical veneer (thick veneer, 3-7 mm). Usually, the inner lamellas are made of wood of a lower quality than the top or lighter than the top. For example, you can make a panel with the core of the panel made of resinous wood and the faces of oak. This will make the panels look like oak, but much lighter. Another advantage is the continuity of the design. The more veneered panel look than solid wood is the main disadvantage.
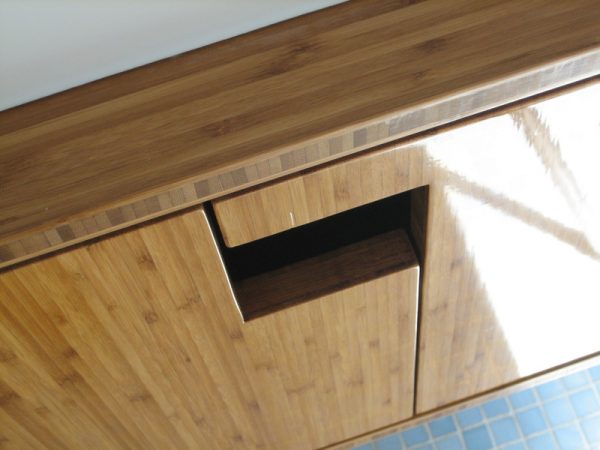
Plaque is a wood derivative consisting of an odd number of technical veneers laid perpendicular to each other. They are glued with hot glue in special presses. It is possible to make plywood from 3, 5 or 7 veneer sheets. Initially, plywood was used more for the backs of furniture or for low-quality work. Over time, due to their stability, they began to be used in production (especially thick ones with a large number of interlocking veneers). Panels can also be veneered with aesthetic veneers and can be used without problems in furniture. However, as with all semi-finished products which use adhesives for gluing, care must be taken to emission of formaldehyde.
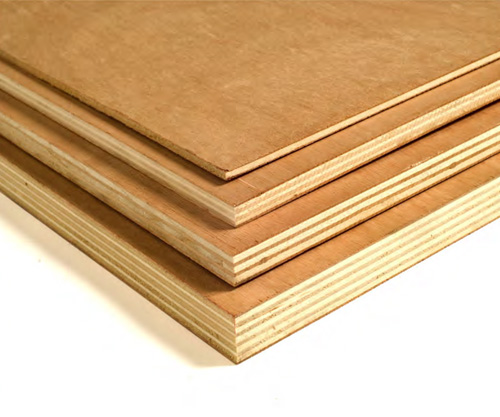
In addition to this type of plywood, where the sheets are laid perpendicularly, there is also plywood made of sheets laid parallel called parallel plywood laminated plywood. The resulting product is elastic and resistant, and is widely used to make supporting beams (glulam), but also in the seating industry. Find out more about the origins of plywood, its evolution over time and its use in various fields (including aeronautics) here.
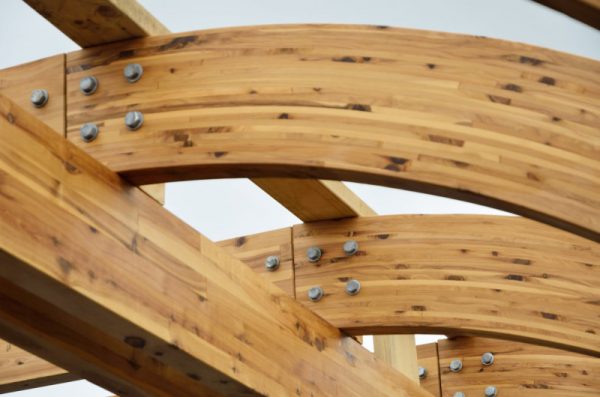
Laminated wood is a semi-finished product made from layers of solid wood. Such blanks are used in obtaining parking or for double-pane window frames. Overlapping layers of wood increases stability. The production of laminated wood and the comparison with solid wood will be the subject of a separate article.
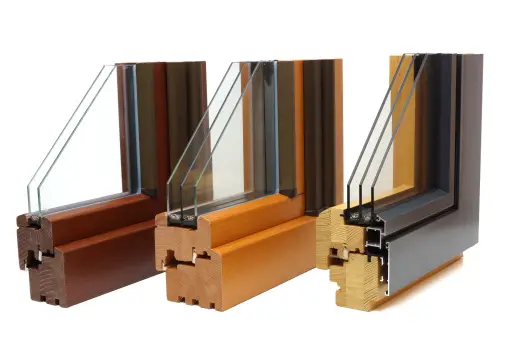
Wood chip panels (chipboard) are made by hot pressing wood chips mixed with adhesive resins. The most commonly used resins are ureoformaldehyde resins. During the process of making chipboard a small part of the formaldehyde in the adhesive remains free and is released over time. This is that pungent odor characteristic of new furniture. The classification of formaldehyde as a product harmful to health has led to the development of countless methods and products to reduce emissions, emission limits and classification classes have been imposed for PAL according to emission of formaldehyde. By using new adhesives or special products called formaldehyde scavengers, it has been possible to obtain panels with very low or even zero emissions.
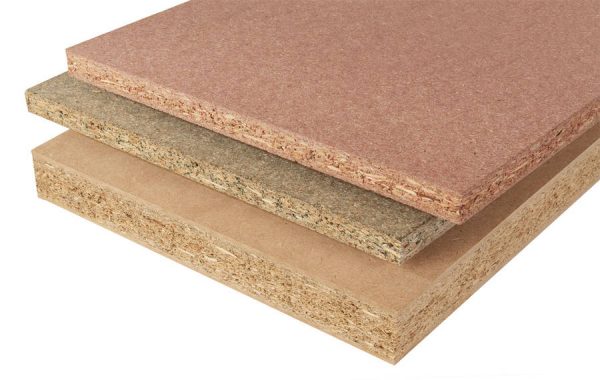
Chipboard panels are rarely used as such. In general, they are covered with veneer, paper (caquer), melamine, etc. They are widely used in office and home furniture. I said at the beginning that we may not know we have chipboard in our house. In order to reduce production costs, veneered chipboard is often used with solid edging. A person less familiar with wood may be convinced that they have solid wood furniture in their home
The advantage of chipboard is its low price. Disadvantages - the impossibility of deep processing, formaldehyde emission (especially in cheaper versions), weight.
The panels in MDF (or PAF, as it used to be called - chipboard and wood fiber panels) are made by hot-pressing wood fiber mixed with resins. Wood fiber is obtained by partially removing the lignin from the wood. The resulting product is very similar to wool. Compared to chipboard, wood fiber panels can also be used without veneer or other materials. The best-known types are MDF (medium density boards) and HDS (high density boards). HDS is produced by the wet process at high temperature and pressure. The fibers are bonded mainly with naturally occurring resins.
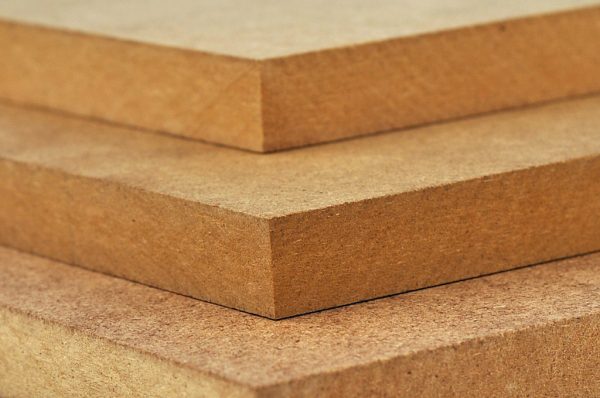
MDF is obtained by the "dry" process, using low temperature and low pressure. Synthetic resins are added for gluing. MDF panels are obtained with different densities or surface treatments: fire, water or weather resistant.
Advantages: deep-processing possibilities, use as veneer or panel, stability. Disadvantages: weight, emission, price (compared to chipboard)
Aesthetic furnishing, like the technical one, is obtained by unrolling or cutting the log into "slices" of wood. In contrast to technical veneers, aesthetic veneers are much thinner, 0.5-0.8 mm thick. Both the quality of the wood and the machines used are important for quality veneers. Poor quality knives mean veneer with defects, which may not be immediately visible, but which will show through during finishing.
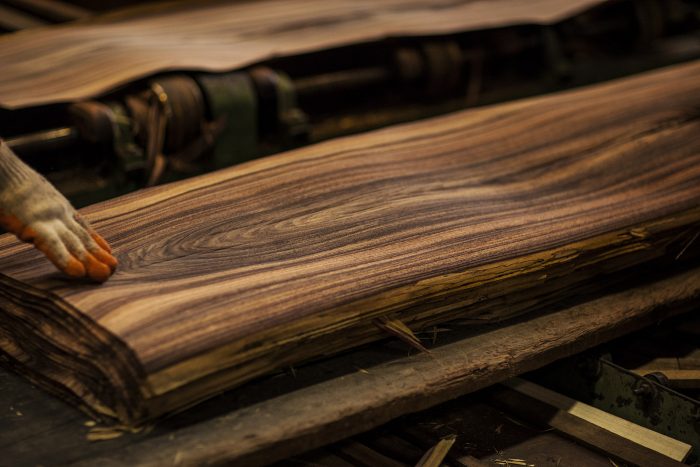
Depending on the cut, the design of the wood is also obtained. For example, cutting parallel to the annual rings (friz) will produce a pattern with parallel lines, while cutting flush to the rings (flader) will produce curved lines forming sequential patterns.
There is much to say about each of these individual semi-finished products. Some have been treated separately, others follow. But put together they can be compared more easily, making the choice simpler.
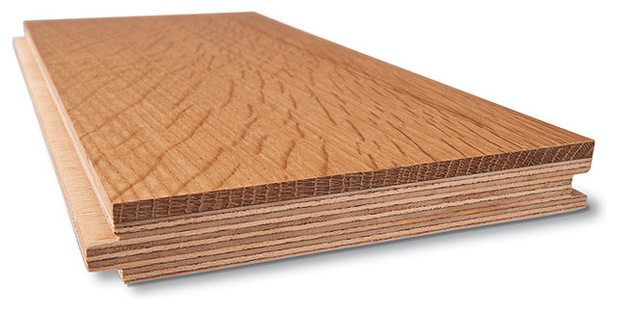
very interesting detailed !
Is formaldehyde in Pal toxic to humans?
Learn more about PAL and formaldehyde from the following link https://revistadinlemn.ro/2016/04/13/pal-ul-si-emisia-de-formaldehida/
Hello, very interesting but you didn't go all the way: as those of us who are interested and apply ourselves not just get excited, dreamy about what you show us, where can we buy what you show us?