We have always associated powder coatings with metal, with coloring and protecting it. This is how car bodies, refrigerators and washing machines are painted, with electrostatic application and the 'baking' of the paint in ovens at fairly high temperatures, as the metal can withstand this rather harsh technology. Wood can also be painted in electrostatic fieldI told you about this recently. But the high temperatures required to fix them made it impossible to think that powder paints could be used to color wood.
But this has not been impossible for some time now. Research has already moved far beyond the research stage and into production. Admittedly, for the time being we are only talking about production with MDF, but there have also been very successful trials with oak and ash panels.
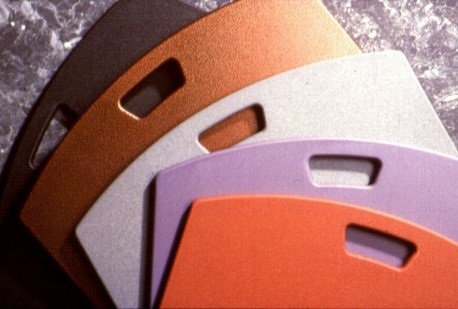
The powder coating process involves 3 key elements: substrate, temperature and electrical charge. Each of these elements plays an important role in the process. Let's take each one in turn.
Support it must be a good conductor of electricity and have as smooth a surface as possible. Metal fitted these requirements very well. Tests on wood and various wood-based panels showed that MDF is the material that comes closest to these characteristics. The main requirement is a moisture content of 5-7%. This moisture makes MDF board a good conductor of electricity.
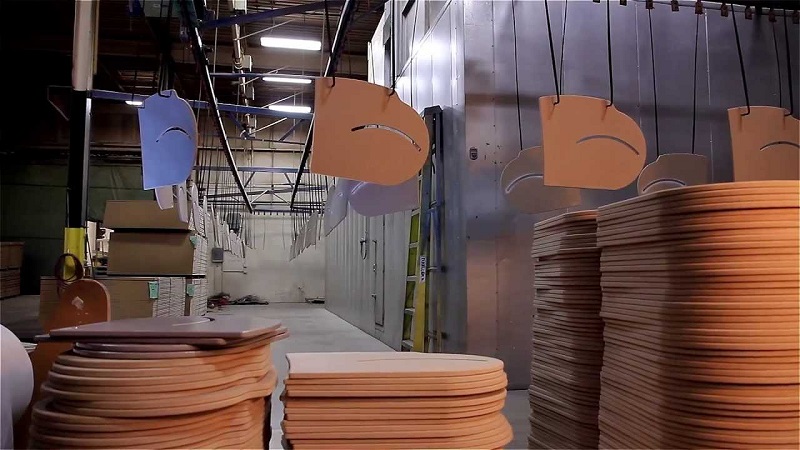
Temperature is also very important because, after the powder paint is applied, the reaction is finalized in ovens with temperatures above 120 grd.C. From the moment they decided that wood could also be powder-coated, it was clear to the researchers that the working temperature had to be lowered. In addition, the duration of the process also had to be reduced so as not to get all the water out of the wood substrate, which would certainly lead to problems. And that's how powder coatings that react at temperatures of 90 degrees Celsius in a very short time were developed.
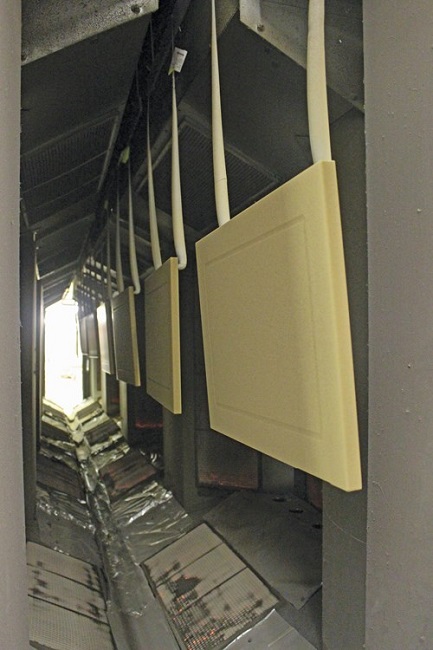
Electrical charging was solved by preheating the MDF boards before coating. This pre-heating is done in a very short time and brings moisture to the surface, turning an insulating material into a good conductor of electricity.
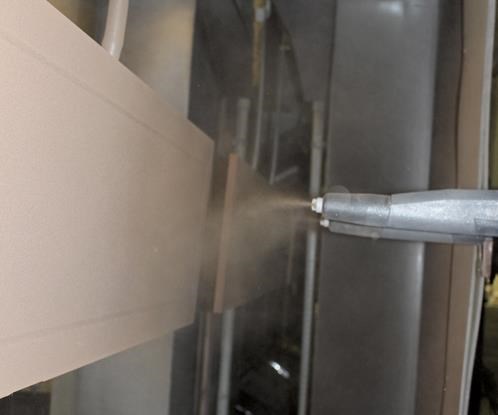
But why do we need to powder coat wood when there are already well-established systems that have been used successfully for years? Because powder coating comes with a number of benefits that make the system vastly superior to existing systems. These benefits are:
- powder paints are very environmentally friendly. They contain no solvents and 95-98% of waste is recovered and can be reused;
- have very good chemical and mechanical resistance, far superior to traditional paints, melamine coatings, foils, etc;
- the painting system ensures a continuity of the surface film on the edges, so that the risk of skipping or cracking at the edges is eliminated;
- you can do all kinds of special effects, you can apply all kinds of colors;
- material costs are reduced because losses are practically negligible.
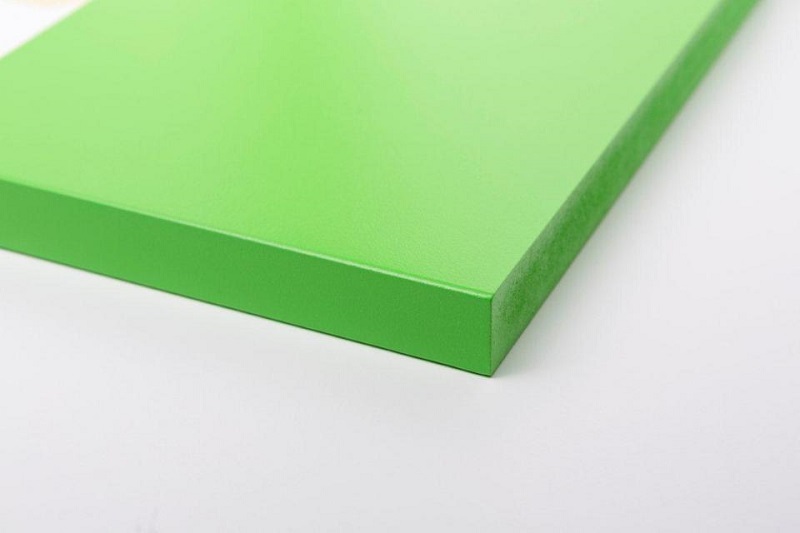
But their main strength is that they are environmentally friendly. All those volatile organic compounds (VOCs) that have been talked about for so long and whose emission must be continuously reduced, all those particles of liquid substances in the atmosphere left over from spraying processes, are a danger to both the environment and our health (even if the products are water-based). These problems can be solved by using powder paints.
There are already factories around the world that finish MDF with powder coatings. In a nutshell, the technological process is as follows: the MDF panels, CNC-machined and thoroughly roughened, are passed through an oven to raise their temperature. They then reach the electrostatic gun and are coated with powder paint, after which they enter another oven where they are reheated to finalize the reaction. The paints used are thermoplastic and soften at a certain temperature. This is exactly the temperature at which the panels are preheated, so that the paint becomes liquid-viscous when it reaches the board. Then, in the dryer, the polymerization reaction takes place and the paint hardens again, this time as a film strongly anchored to the MDF surface. Because the heating in the preheater must be done quickly, UV or IR ovens are used. The whole process is continuous, basically a finishing line, and the boards are hung on a chain, a continuously moving chain.

We spoke a while ago about powder paints with Gabi Mănoiu, the Falk Consultingwho distribute the guns and spray systems Sames-Kremlin in Romania. He told me that this seems to be the future in the wood industry, and this future is very close. We talked a lot about electrostatic field spraying systems and I understand that Sames Kremlin are well prepared for the future. Application systems, both manual and industrial, occupy a large part of their portfolio. I think perhaps it wouldn't be a bad thing to think about this future too. Especially as the future is coming towards us at breakneck speed.
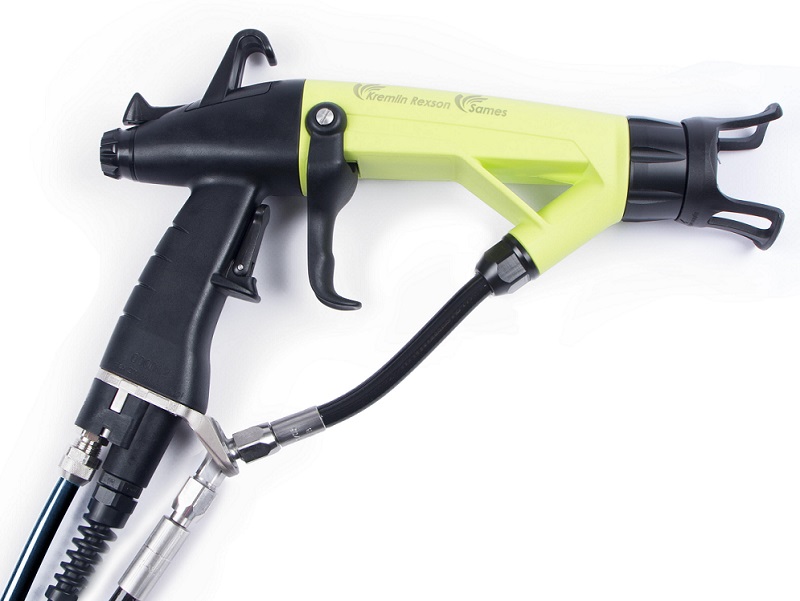
Add comment