Like solid wood panelsGlulam beams - glulam as they are also known - are products derived from solid wood. They are used more and more in construction and are preferred not only for their beauty and the possibility of creating truly spectacular buildings, but above all for their particular strength. This is not the first time I present lamellar beams, but I will explain their special properties in more detail below.
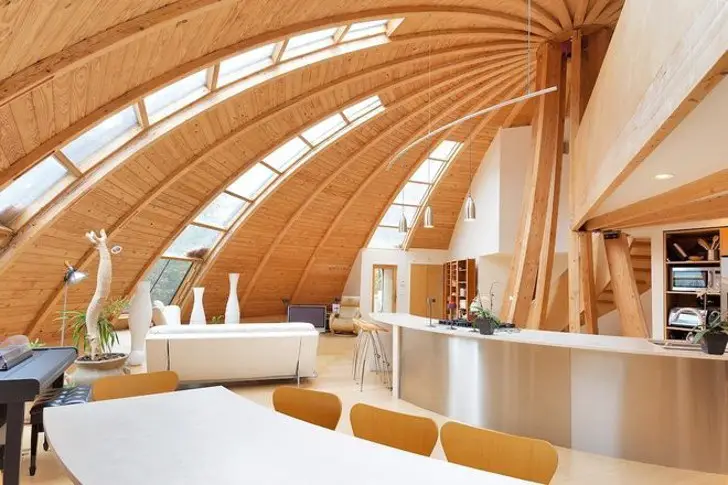
I have been saying glulam beams, because that is what they are known as. The correct name is "glued laminated timber" as specified in the product standards. Glulam comes from the English product name -Â glued laminated timber - and it's basically a beam made from several layers of wood. But why should another product, wrongly considered by some to be inferior, be made when you can make beams from solid wood? By sawing into strips, the stresses in the wood are reduced and defects and knots are removed. The wood becomes more homogeneous and the mechanical properties increase dramatically due to the reduction of defects.
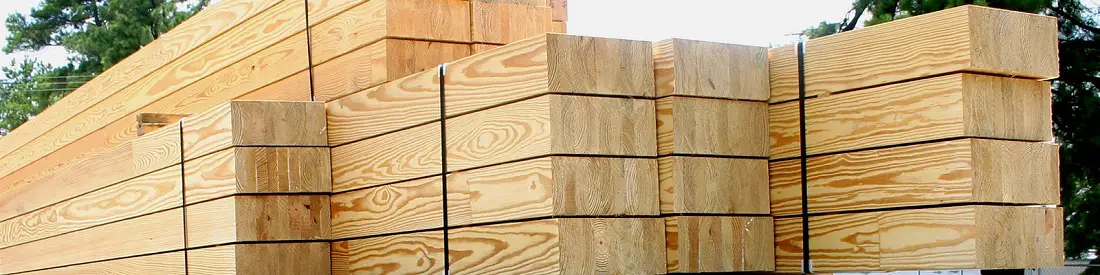
In glulam, the glueing of the wooden slats is along the grain. The wood used can be either resinous (grind, larch, pine) and deciduous (oakash, ash, maple, cedar). joint in teeth, then laid on top of each other and glued together. This can produce beams several meters thick and over 50 m long. Also thanks to the fact that it is made of slats, the beam can be shaped into arched forms.
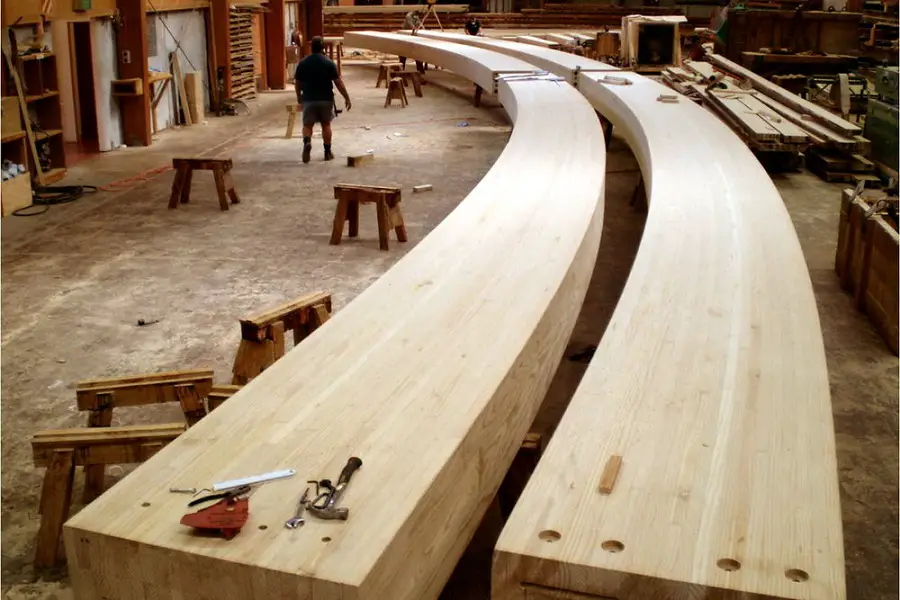
The glue is very important in the production of beams, which must ensure the strength and durability of the clamps, given that these beams are structural elements. The adhesives used are melaminic, polyurethane or resorcinic. Melamine (melamine-urea formaldehyde MUF) and polyurethane adhesives give white bond lines, whereas the resin-bonded adhesives give darker, brown bond lines. The adhesives used have high strengths and the beams can also be used outdoors or for building construction where chemicals that can destroy other building materials will be used.
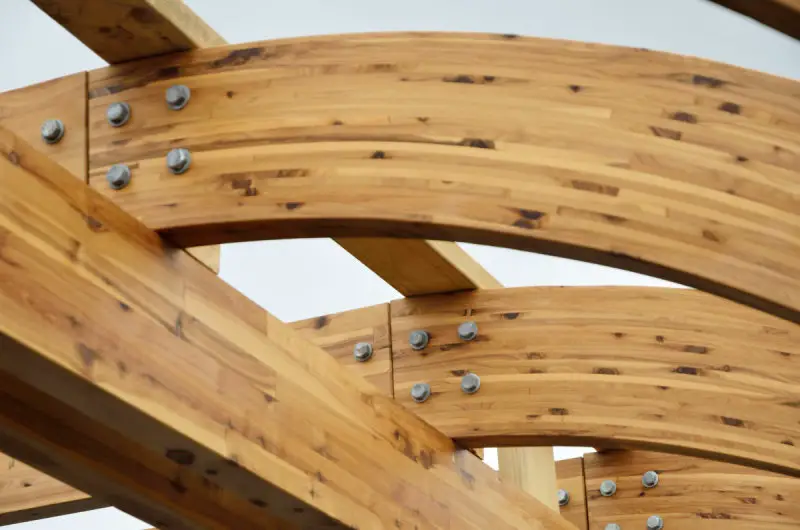
Laminated beams are increasingly used in construction because of properties that traditional materials do not have. Perhaps the most important of these is chemical resistance increased. They are resistant to most acids, oxidation, ammonia or chlorine derivatives. This is why they are used in the construction of animal farms (ammonia), swimming pools (chlorine), in salt works or in the construction of salt or coal deposits. Steel, for example, cannot withstand the conditions in a salt works.
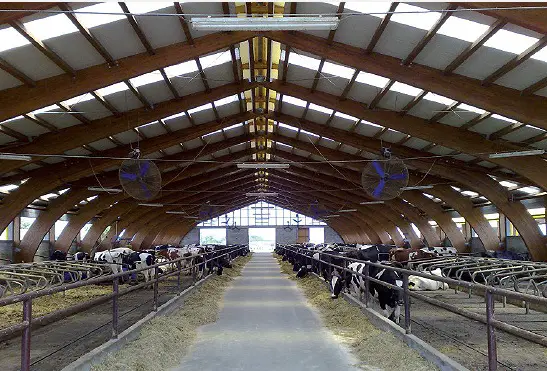
Despite being made of wood - a combustible product - they are very fire resistant. If we look at traditional building materials, we find that steel loses its mechanical properties and is no longer considered a building material above 550grd.C (well below its melting temperature), and reinforced concrete cracks and deforms due to reduced hardness at high temperatures. Wood burns, but it does not change its properties, so that even if there is a layer of charcoalized wood on the outside, the wood has the same mechanical properties on the inside. In the case of laminated beams, the wood burns on the outside, but it is very difficult to break through the adhesive layers, so it advances very slowly. During this time the unburned wood retains its properties even at high temperatures, so the construction is still safe.
Another advantage of using laminated beams is much lighter weight for the same mechanical strength. Depending on the species used, the specific gravity can vary from 400 to 600 kg/mc (spruce beams have an average specific gravity of 430 kg/mc). At the same strength, a steel beam is 20% heavier and a reinforced concrete beam 600%. For example, a beam with a specific gravity of 600 kg/mc provides the same strength as a reinforced concrete beam with a specific gravity of 2500 kg/mc. Do you realize what this means for a building?
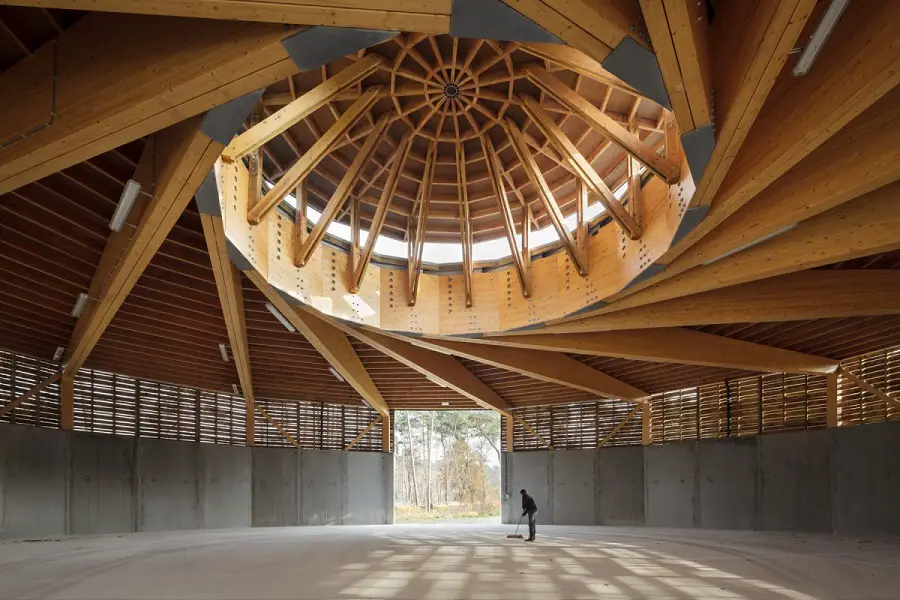
Constructions made on laminated beams have a much higher earthquake resistance due to the high elasticity of the beams. The overlapping of the slats parallel to the fiber leads to increased elasticity. This elasticity helps to damp the telluric movements and makes the construction much stronger (and lighter) compared to a rigid reinforced concrete construction.
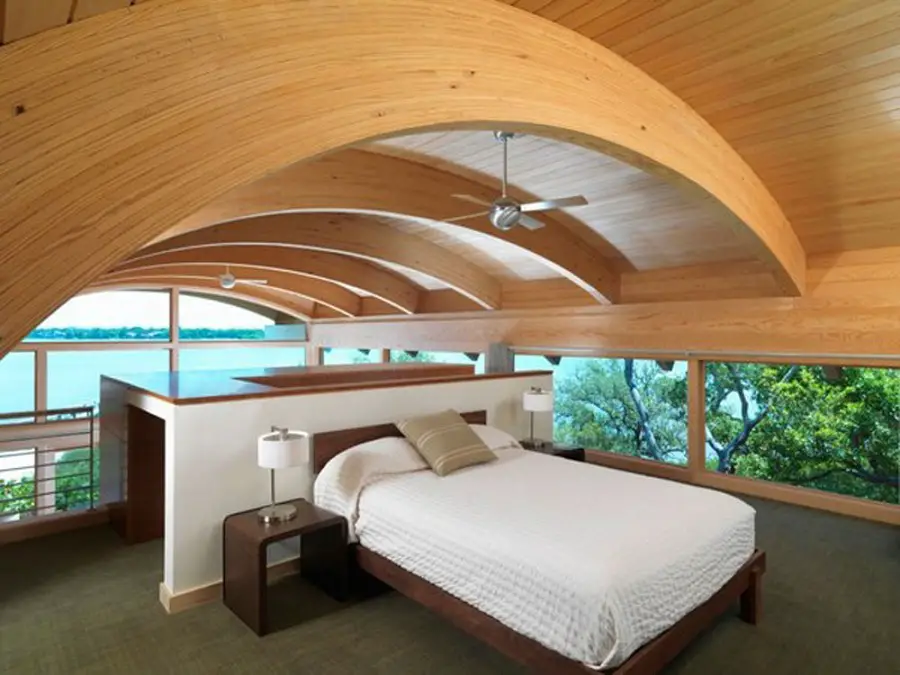
Laminated beams are an architect's dream because no limits on design. They can be straight or curved, thin or very thick, short or long. Long beams, obtained by lengthening the slats, have a very high load-bearing capacity and can be used to construct buildings with very large spans and very few vertical supporting columns. This is another reason why they are used in the construction of Olympic swimming pools, sports arenas, riding stables or greenhouses.
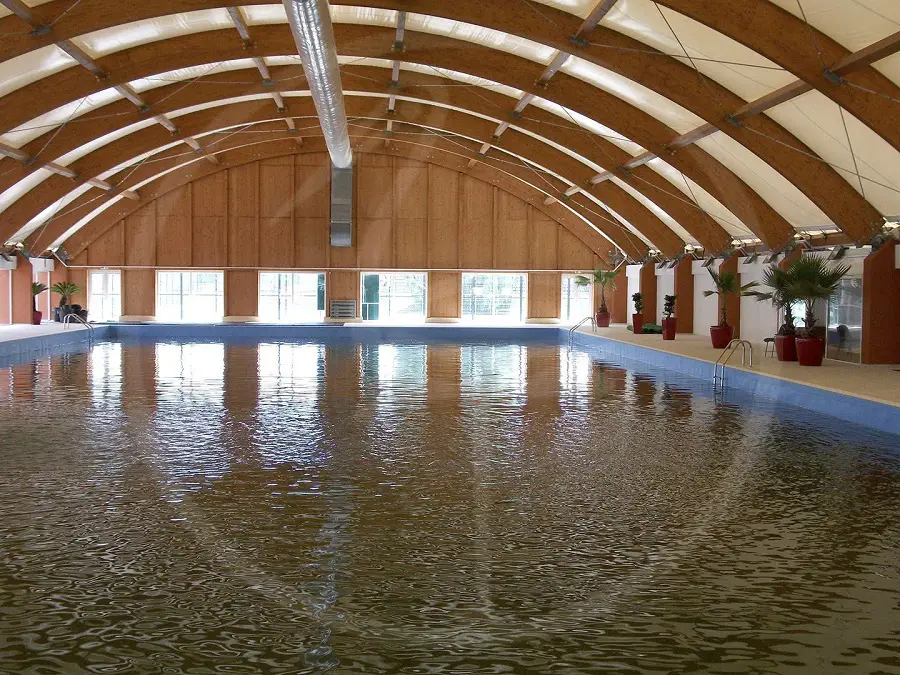
In Romania, too, more and more buildings are being built using these beams and it's no wonder, because there are large manufacturers in the country, one near Targoviste, in Harghita and in Timis. I am sure that many of you have admired the Turda salt pans or the Therme in Bucharest, which were built using glulam beams made in Romania.
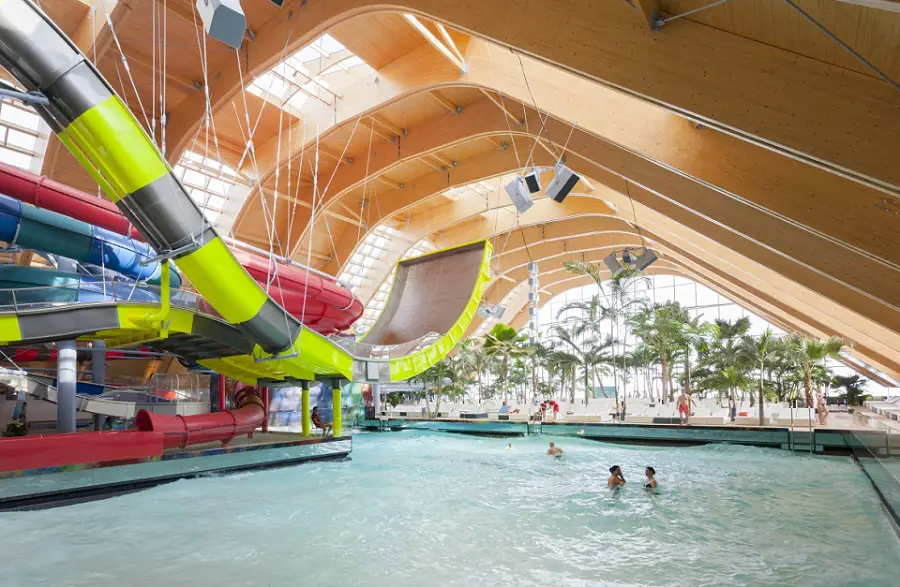
Hello! I might be wrong with the question, but I risk: can these laminated beams also be used for the construction of multi-storey buildings, such as a block of flats or a multi-storey building?
Good evening,
They can also be used in recent times, tall buildings have been built using laminated beams. However, very serious strength calculations must be made for multi-storey buildings. If you search on the internet for the word "glulam" you will be surprised to see what extraordinary buildings have been built on structures made with these beams.
All the best!
[...] with the danger of loss of stability. There are, however, materials - such as glulam (lamellar beams) - with which higher constructions can be made (but not much higher [...]