We continue our series of presentations of wooden houses with a construction that Vlad Liteanu, from Litarh, says it is a real school house. The way it was done isolationThe materials used, the routing, the heat-recovery ventilation, the heating system used, all of this can always be used to teach a lesson on how to build a highly insulated and earthquake-resistant wooden house. The house, owned by young IT-geeks who were involved throughout the construction (often even working alongside the Litarh team), is a projection into the future. The water turns off automatically if a pipe bursts, heat can be turned on from your phone before you leave the office, and other such "science fiction". We spoke to both the builder and the owner, and the article below is the rather technical presentation of the house built in Voluntari, near Bucharest.
Project
Cătălin Ciurea and his wife are IT specialists and wanted a house where this would be visible. But more than that, they wanted to be involved in the construction, in the choice of materials, to understand why one material is better than another - in short, they needed a builder they could communicate with.
"I had the project detailed by the strength designer to exact material quantities from the catalogs of the relevant companies (eg: Rothoblaas, Egger) and drawn in a specialized software. I emailed this kit to all the firms I found online that would build wooden houses".
They contacted several firms, but they had the best communication with Vlad Liteanu. They discussed, paid him a visit and received a first offer. To be convinced that they were making the right choice, they also talked to the owner of a house in Bucharest built by Litarh. They understood that they could talk to Vlad, that they could get involved in the construction as they wished, and this made them choose to build their house with Litarh.
The discussion with the architect followed. "We proposed something, but the architect recommended something else in relation to the size and shape of the site. We also used elements from our original proposal, but in general we went with the architect's version. We discussed and adjusted here and there."
The house, with a usable area of 130 m², has a ground floor and a first floor. The ground floor has been designed as a meeting place and the first floor as a place to relax. On the ground floor there is a generous 41 m² living room, a 9 m² kitchen, a 5.3 m² study, an entrance hall and a service bathroom. Upstairs are 3 bedrooms, 2 bathrooms and a technical room. The master bedroom, measuring 15 m², has access to one of the bathrooms and the technical room. The other two bedrooms are smaller, around 11 m².
Work at the Valea Moldovei factory
When all the project details were finalized and the land ready for the new house, construction began. This time the walls were made largely in the Valley of Moldova. Unlike when they were built 6-8 years ago, house in France and the one in Aradthe factory was much better equipped, with state-of-the-art prefabricated wall construction systemspurchased in Germany.
First of all it must be said that it is a very well insulated house. In addition, it has a state-of-the-art exterior material from Egger which allows moisture to escape from the wall structure to the outside - in other words, it's a perspiring house. Why is this a good thing? Because if moisture is left in the structure it can escape to the outside, which is very important for a timber-framed house. Moisture left inside can over time lead to mold or even wood rot.
The walls were made entirely in the factory, and their structure from the inside out was as follows:
- chipboard
- technical space for pipelines, routes, etc.,
- 50 mm insulation
- OSB structure board
- 200 mm joist made of 60/200 mm uprights with 200 mm thick basalt wool insulation
- 15 mm DHF (material allowing vapors to escape)
- 150 mm high-density basalt wool insulation
- vapour dispersion film (anti-condensation)
- ventilation ruler
- heat-treated wood panelling.
The roof was also worked on in the factory, but not completely, the trusses were assembled on site. Structure:
- plasterboard
- technical space
- OSB board
- vapor barrier
- rafters 60×250 mm
- 250 mm rolls of basaltic cotton wool
- asterisk
- High density DHF
- high-density basaltic cotton wool
- vapour dispersion film
- rulers
- plank roofing
- galvanized sheet.
The house, almost finished in the factory, was loaded into a truck and taken to Voluntari to be assembled on the poured and reinforced foundation. Everything was much simpler compared to a house that is built from scratch on site. Cătălin says that from the time they bought the land until they moved into the house was 3 years. Of these, only 1 year was needed for the actual construction, of which 3 months were not worked for various reasons. They moved into the house a few months ago even though there was still finishing work to be done and a number of systems to install. They continued to work "from the inside out" as they would say, but they didn't finish. The arrival of the baby in their lives slowed the pace and changed their priorities a bit. 🙂
Insulation
Aside from the IT features I'll tell you about in a moment, the house's strongest asset is the insulation. Three types of mineral wool have been used - glass wool, semi-rigid basaltic and rigid basaltic - and extruded polystyrene for the plinth. Because the Environmental Fund Administration does not consider these materials organic, they could not apply for funding under the Green House Plus program, as they had wished.
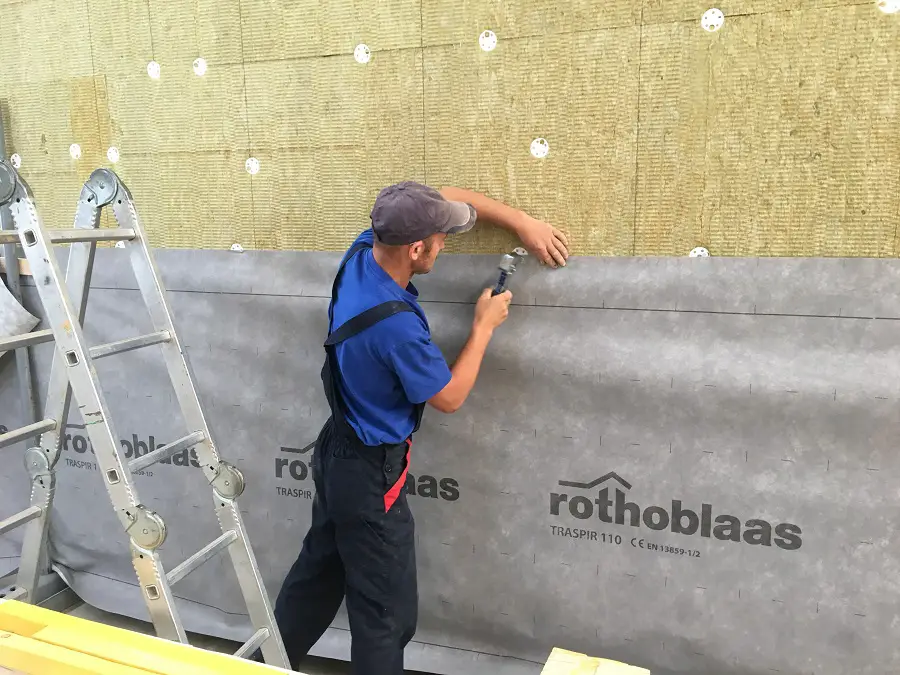
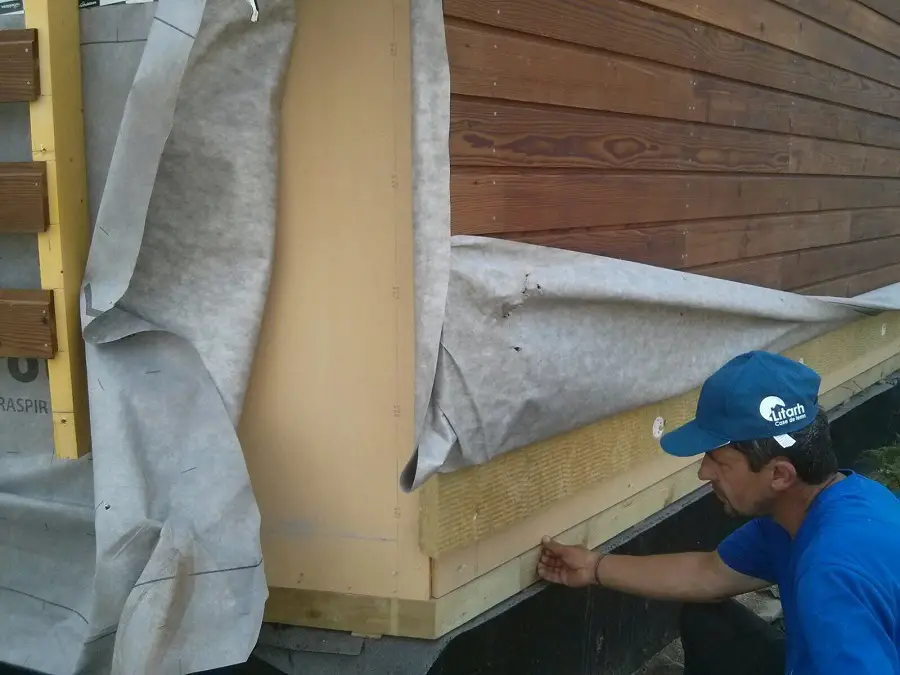
Heating systems. Home energy efficiency
For the heating of the house they chose systems predominantly used in office buildings, which meant planning and execution of the respective installations adapted to a house. Air-to-air heat pump heating and heat recovery ventilation - certified by Passive House Institute (Passive House Institute).
The house is energy efficient, but it's not a passive house. The calculations have been made for a consumption of 50 kWh/sqm/year, but as it has not yet been a year since they moved into their new home, I can't say yet if it is within the range.
All water and sewage pipes in the house were very well insulated. The windows and front door were chosen on the basis of quality, also certified by the Passive House Institute. It was quite an adventure to plan, design and make them, with one window weighing about 440 kg and the other 330 kg.
Home IT systems
As I told you from the beginning, the house is owned by IT specialists and this is very visible. There are things that we wouldn't even think of, but that Catalin considers very important and he finds it practically unthinkable to have a house without such systems.
- Temperature sensors installed in specific places in your home to monitor temperature and humidity. They have been configured to send alerts to your phone when the temperature is above or below a certain threshold.
- The air conditioners are equipped with Wi-Fi controllers and can each be switched independently into heating or cooling mode.
- The recovery ventilation unit has been specially purchased with remote control mode (on/off/ shut off/ shut down etc.).
- The outer rollers have a wind sensor that commands them to rise if the wind is too strong and there is a risk of being blown off the rails.
- Smart sockets with consumption monitoring for the water pumps in your home to shut them off in the event of a breakdown (bur burst pipe, for example).
Cătălin says it's far from over. There are many other systems they want to experiment with, but they haven't gotten around to focusing on them yet. He is happy that he was able to use good quality materials and products, that he worked with a builder with whom he was able to collaborate so they could put their ideas into practice, and that they have the strong, sturdy, energy-efficient wooden house they wanted.
Although they already live here, they told us that there is still a lot to be done, both to the house and the yard. They suggested we come back when everything is ready. We will do so knowing that there will be all sorts of interesting surprises waiting for us.
Add comment