LVL - Laminated Veneer Lamber - is a wood construction material in the same category as glulam (glued laminated timber) and CLT (cross laminated timber). Concern about the protection of wood resources and their rational exploitation has led to the emergence of materials that increasingly tend to replace solid wood in construction. wooden houses. On the other hand, the problems linked to carbon emissions and the need to use products with as low a carbon footprint as possible are driving us towards building materials manufactured with the lowest possible emissions. As a result, materials such as reinforced concrete, steel and even bricks are increasingly being replaced by this industrialized wood, which in many cases has superior properties to traditional materials.
What is LVL
The English name - laminated veneer lamber - can be translated as laminated veneer lumber. This means structural timber - panels, beams, beams, supporting posts - made from veneer sheets laid one on top of the other along the grain and glued together. The difference tackle, a material with which we are quite familiar, is that the sheets of veneer are not laid perpendicular to each other but in the same direction. Another difference is that the number of veneer sheets can be uneven without the risk of getting a panel that warps.
In contrast to plywood, which appeared at the beginning of the 20th century, LVL appeared in the second half of the 20th century, with the advent of advanced wood processing technologies and the need for rational wood exploitation. This required the use of qualitatively inferior, lesser-used species and much smaller timber.
There is no unified idea about the first appearance of the material. Some sources say that the term was first used by Wayerhauser - an American company - in the 1960s, when it made LVL by pressing veneers. Others say that LVL came after OSB and cites as its inventor Arthur Troutner, also from the US, who in 1971 built a house using only LVL to demonstrate the material's qualities. In the US, however, the material was first mentioned in the National Design Specifications - the document governing the construction of wooden houses - in 1991.
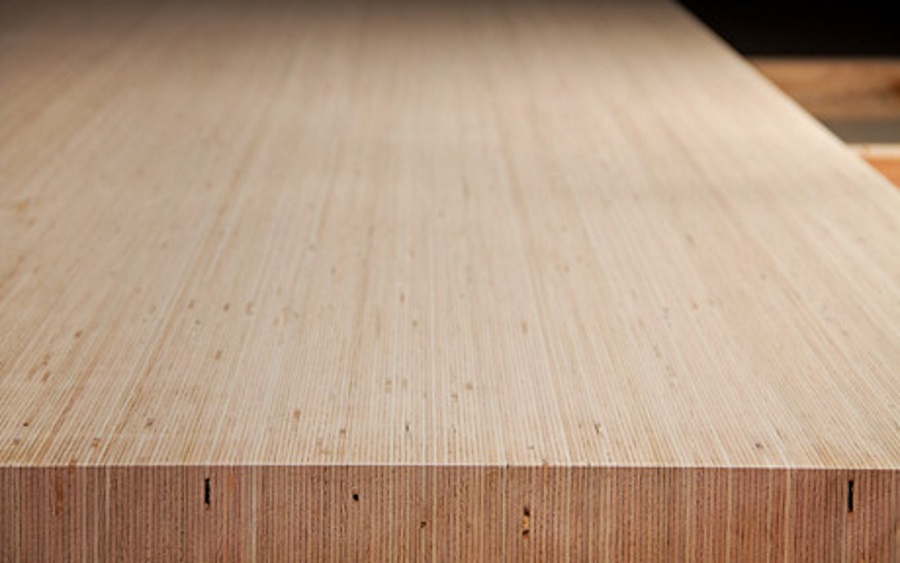
photo source: structurecraft.com
How to get LVL
To make LVL boards, the logs are first cut to size and peeled. No particular species is specified, but the species found in the greatest quantity in the region are used. For the most part resinous, and while in northern Europe (Finland, Russia) pine is used, in the USA it is used spruce or fir.
Before the veneer is peeled, the logs are soaked in warm water for 24 hours to increase the wood's elasticity, and the veneer so they don't break during cutting. They then go to the derinding where the veneer is cut up to 3 mm thick. Uncoiling is used to produce a long sheet of veneer that can be cut up to 1,4 m long. The veneer sheets have defects removed and are then dried to a moisture content of 8-10%.
After drying, the veneer is straightened by trimming the edges, sprayed with glue and placed on the platen of a continuous hot-pressing press, where it is laid sheet on sheet with a gap of a few centimeters. A continuous panel emerges from the press, which is then cut to the desired size. To understand how the veneers are laid to obtain the continuous panel, watch the video below.
During production the wood can be treated against moisture, insect infestation or molds, depending on the requirements and the required quality level.
Main properties
The material obtained by pressing veneers has many qualities that make it a very good building material. Here are some of the qualities of LVL:
- Elasticity - the arrangement of the veneers in the same direction makes it possible to obtain a highly elastic material. For example, the elastic modulus of LVL is 24% higher than that of spruce;
- resistant to bending - it is twice as strong as spruce;
- homogeneous - because it is made of many overlapping wooden boards and the defects are removed, the final product has equal properties over the entire surface of the board, unlike solid wood;
- stability - it is a much more stable material than solid wood, with much less water absorption, so there is no dimensional variation;
- better fire resistance than solid wood - being a material with successive layers of wood and glue, it is more difficult to maintain combustion (the phenol-formaldehyde or phenol-resorcinic glues used do not maintain combustion). In addition, the high density lowers the air content inside the wood, which slows down the spread of fire;
- better resistance to salty air, water vapor, ammonia than concrete or steel. That's why it's used in swimming pools, swimming pools or animal farms;
- has the same strength at much lower weight compared to concrete. This makes it possible to build strong constructions on a smaller foundation and makes installation quicker and easier;
- is a good insulating material and can be used to make prefabricated elements that also contain insulation material. It is widely used in Western Europe and the USA to make passive houses and those energy efficient.
Like any material, it must have drawbacks. Firstly, it is not recommended for outdoor use. There are manufacturers who say that their products have very good resistance to moisture due to treatments during production, but I have not found many recommendations for unprotected outdoor construction.
LVL panels without special treatments should not be placed directly on the ground as they absorb moisture over time and can be attacked by insects.
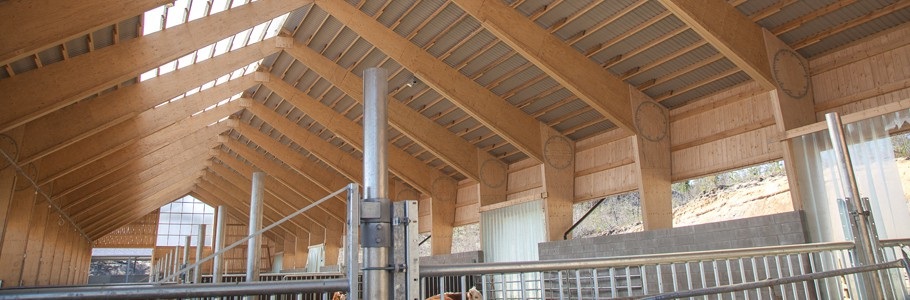
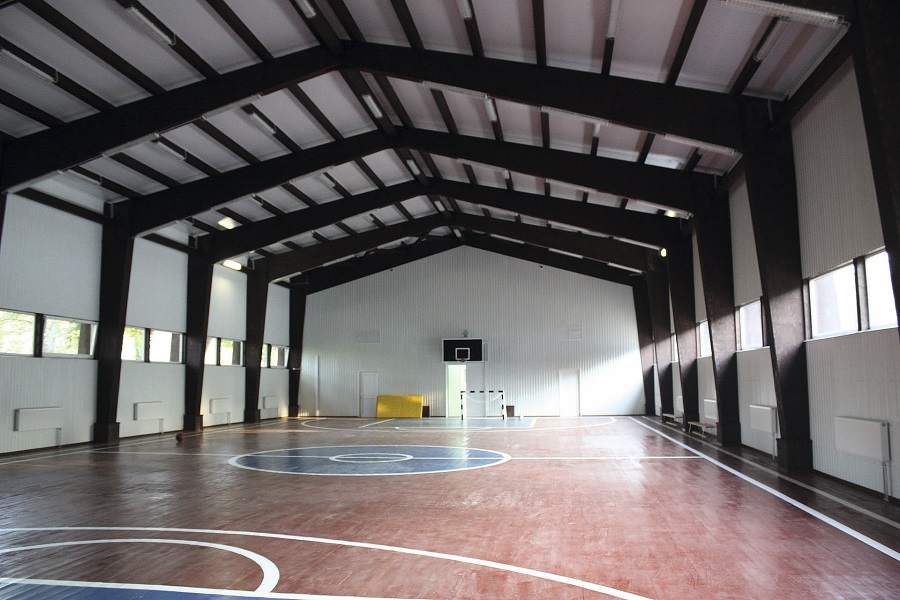
Types of LVL
LVL can be in the form of panels or beams. The process is the same for both. The resulting panel can then be cut into beams or posts.
There are types of LVL, referred to as Q or T, which also have veneers laid perpendicular to each other. The number of parallel veneers along the fiber is much higher than the number of perpendicular ones. Such products are much stiffer, as the presence of perpendicular veneers prevents the panel from twisting or bending.
What it is used for
LVL is mainly used as a building material. Although it is almost unknown in our country, it is widely used in Western European countries and the USA for both civil and industrial construction. It can be used for both new and renovated buildings.
Being strong and dimensionally stable it is used for:
- resistance walls
- floors
- roof elements
- beams and resistance columns for wooden structures
- achievement prefabricated walls
- door and window elements
- stairs and steps
LVL panels or beams can be made in such a way that the visible face is formed by the ends of the veneers. It's sort of an "end grain" look, but being veneer it looks like thicker parallel lines, horizontal or vertical.
Being easy to work, it makes it possible to create buildings with a distinctive design. Below is an example of an office building in Boston using LVL as wood. The top floor is quite spectacular.
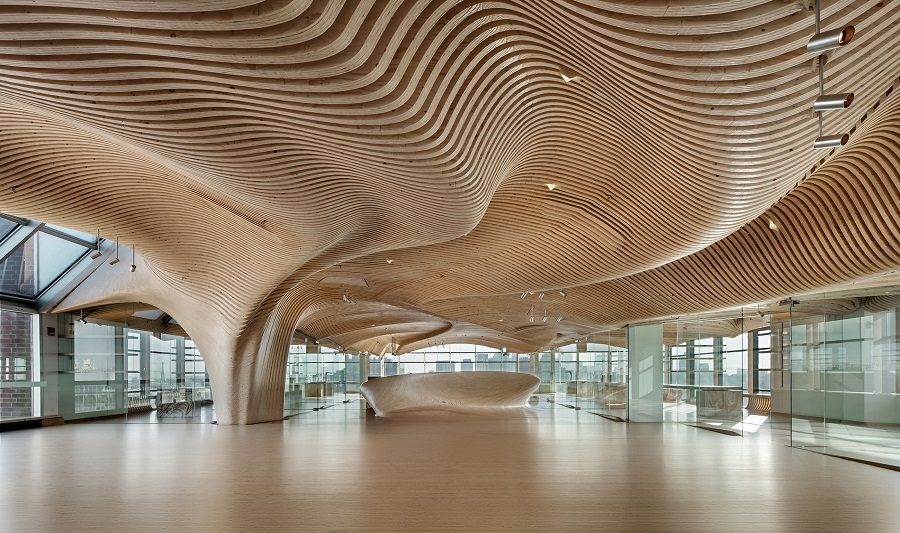
Comparison with glulam and CLT
If you've also read our articles on glulam and CLT, you're probably wondering what the difference is and why you should choose one or the other.
It is similar to glulam in the way it is made. The laying of the wood layers is also parallel to the fiber, but with LVL it is 3 mm veneer and with glulam it is 30-35 mm timber. They are both elastic, but LVL accepts higher pressure without the risk of warping.
Compared to CLT, they differ both in the way the layers are laid - in CLT they are laid perpendicular, as in plywood - and in their size. It is not veneer, but timber, like glulam. CLT panels are very strong and stable over time and can also be used in tall wooden buildings. But they are heavier and stiffer.
There are factories in Romania that have been producing glulam for years now. In the meantime I understand that some of them also make CLT. I haven't heard of an LVL manufacturer in the country yet, but I found the product in the Holver showroom in Bucharest.
I hope I've managed to come up with some new and useful information, and if you think it might be of help to others you can share it. If you have any questions, clarifications or additional information on the topic please leave them below in the comments.
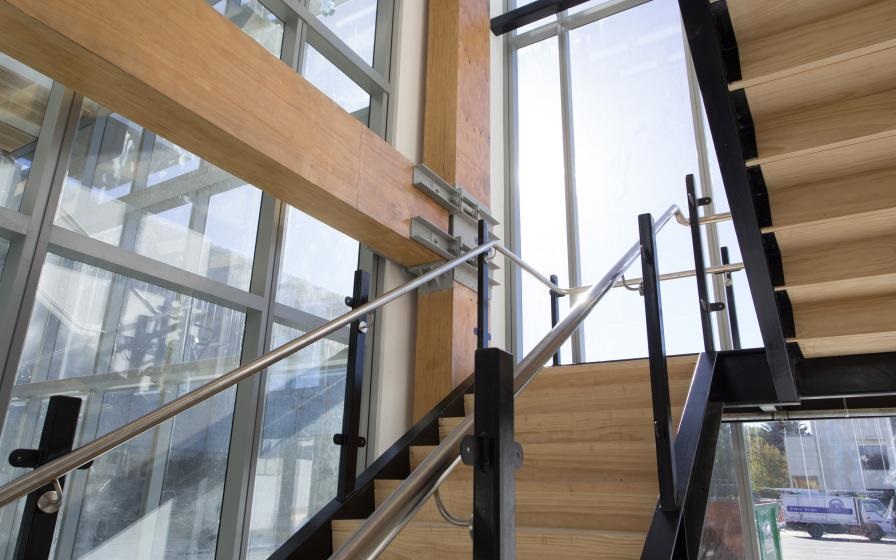
interesting email addresses for those who distribute them can you?
Hello.
As I said in the article, I saw the product at Holver Bucharest. I know there is a distribution network for Holver products, but I don't know details. The best is to contact them on holver.ro or at the centers in Bucharest and in the country.
All the best!