End grain - end grain, in translation - is the term we also use to describe a way of cutting and laying wood to make floors, chopping boards, kitchen worktops and even panels used to decorate walls. It was from such decorative panels that the idea for this article came. Before the holidays, every 2 days, I was asked by different people to explain how some very interesting looking end grain panels are finished. Right after the holidays I received, again, the same request from a different person. I don't know who in my place wouldn't have thought that this was a sign and that I was bound to write an article on this topic. 🙂
What 'end grain' means
As you already know, end grain is Romanian for end grain. Cutting solid wood can be done in several ways, resulting in elements with different appearance and properties. Tangential cuts can be made to the annual ring, resulting in the cathedral-like appearance of the natural wood design (fl flanging, as they are also called). Another way of cutting is parallel to the annual rings, in this case resulting in a pattern with parallel lines.
When the appearance is end grain, the cut is made perpendicular to the grain, practically in the direction of growth of the tree. Annual rings are seen in this case as concentric circles. If a young trunk is cut the circles are complete, the image is similar to a shooting target. If the wood is already cut into beams or planks, the cut is made perpendicular to the length, and on the surface you will see parallel arcs of circles representing several annual rings. This is the most common layout and the one that produces the most interesting designs.
"Slices of wood from twigs used to make table tops or flooring in combination with epoxy resin, very popular lately, are also cut in this way. However, the term 'end grain' is less commonly used, because in our country the term also has an aesthetic dimension, given the way the pieces of wood are laid and the way they are finished.
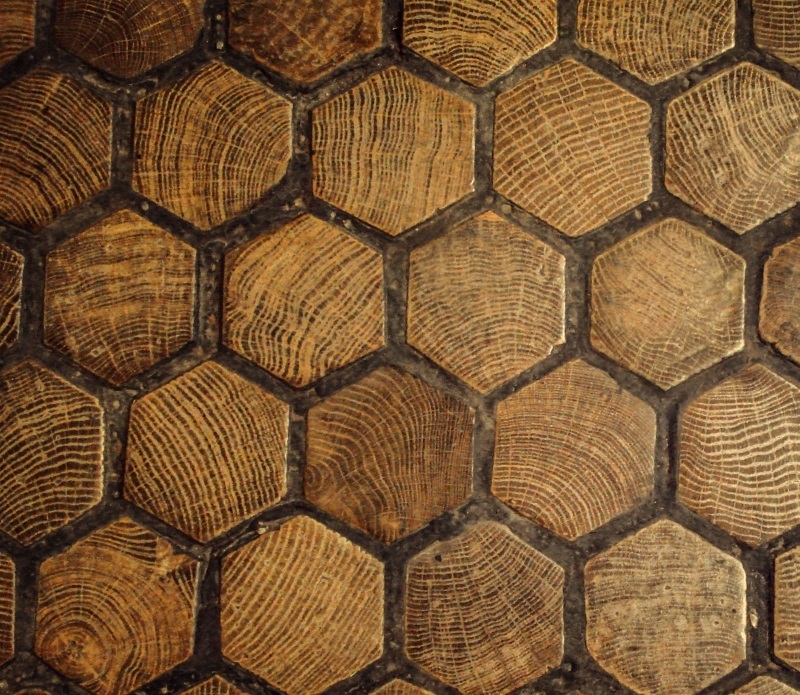
Properties of the wood thus cut and laid
I say cut and laid every time because every piece of wood has fiber ends, except that this area is hidden, or in any case not the main face. In table tops, flooring, or end grain grinders, the pieces of wood are laid and assembled so that the fiber ends form the "face" of the object.
This way of cutting and laying comes with different properties than the other ways. The most important of the properties is the much faster and much higher moisture absorption. Basically, through this area, the amount of water absorbed can be up to 100 times higher compared to a piece laid along the fiber. This is a disadvantage and specialists often recommend blocking the fiber ends immediately after cutting, before further processing. And the release of moisture occurs just as quickly and in large quantities which causes the wood to vary dimensionally quite a lot with the variation in moisture, if the locking of the fiber ends is not done properly.
Another property is the much higher strength of wood. That's why end grain wood flooring are much stronger. That's why even in the past, streets, alleys, factory floors and floors in high-traffic areas were made with pieces of wood cut in this way. You can still see such a 'podire' at Manuc's Inn in Bucharest. At the entrance there is still an area paved with pieces of wood, and the old ones have been recovered and can be seen stored next to the wall. I hope to use them in time to furnish other areas inside.
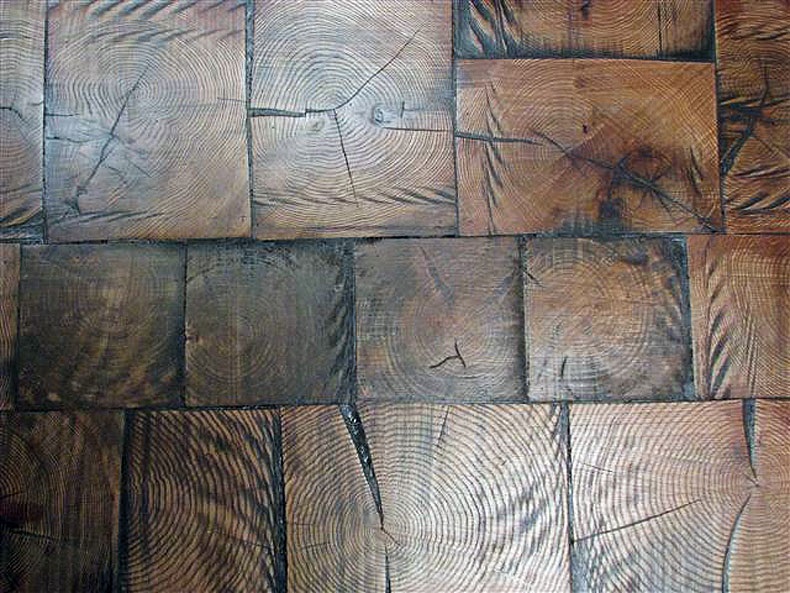
Products made from end grain
They are made from pieces of end-grain wood - table and kitchen worktops, chopping boards, interior and exterior flooring, decorative panels for furniture and walls, paintings. For long, trouble-free operation, all these items must be finished in such a way that the fiber ends are as closed as possible, minimizing absorption.
Of all these objects, perhaps the most successful are toasters. They are preferred by professionals in the field. To justify their choice they have the following arguments:
- used knives last much longer unsharpened. When cutting or chopping the knife blade doesn't hit the hard fiber but slides through the fibers, which increases its life;
- the shredder lasts longer without scratches. The explanation is the same as above - the knife blade slips through the fibers and doesn't end up scratching them;
- do not spread germs and micro-organisms. Due to the rougher surface than other types of mincers, when cutting chicken, fish or pork, tiny pieces of meat are retained strictly on that portion and do not reach other areas. After use, a regular rinse with water and detergent removes debris and any micro-organisms and the mincer can be used safely. However, it should be protected with mineral oil beforehand to avoid strong absorption into the wood through the fiber ends;
- are heavier than similarly sized products, but with the wood laid along the grain, which gives stability and safety when working.
Different species of wood can be used to make them, giving them a delightful aesthetic appearance. They are usually more expensive than the usual wooden choppers, but they are stronger, healthier, safer and, last but not least, better looking.
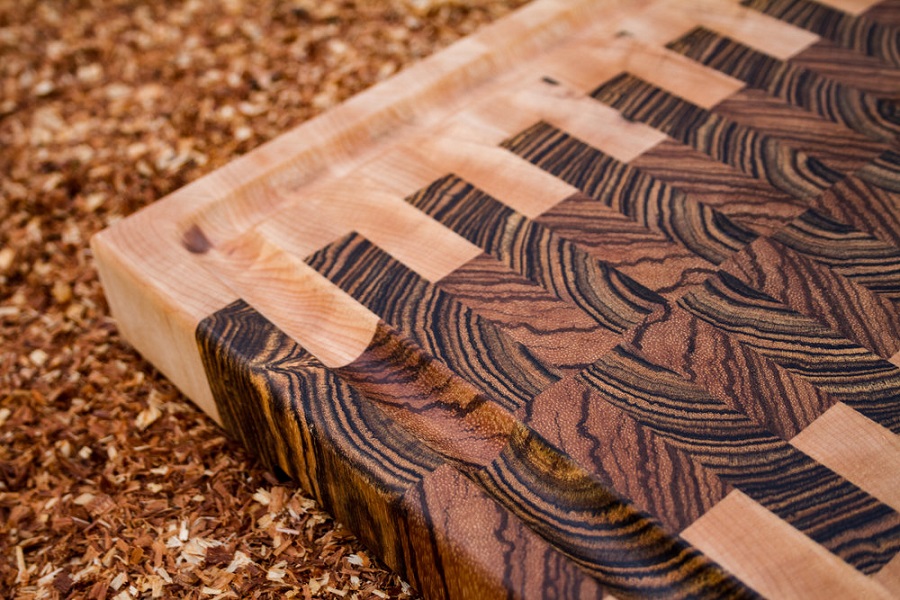
Briefly about how to make "end grain" decorative panels
Using wood to make decorative panels and even paintings is nothing new. I wrote a while ago about a Russian-born artist which makes reclaimed wood very popular paintings. In my opinion the end grain ones are the most expressive. The drawing made by the annual rings and the different absorption of the colorants in the annual ring leads to a very pleasing result.
The request to explain how the finish is done started with a panel like the one below. Because it's not difficult to do, I thought you might find a few pointers useful. Who knows, you may at some point consider making such decorative wooden panels as a DIY project.
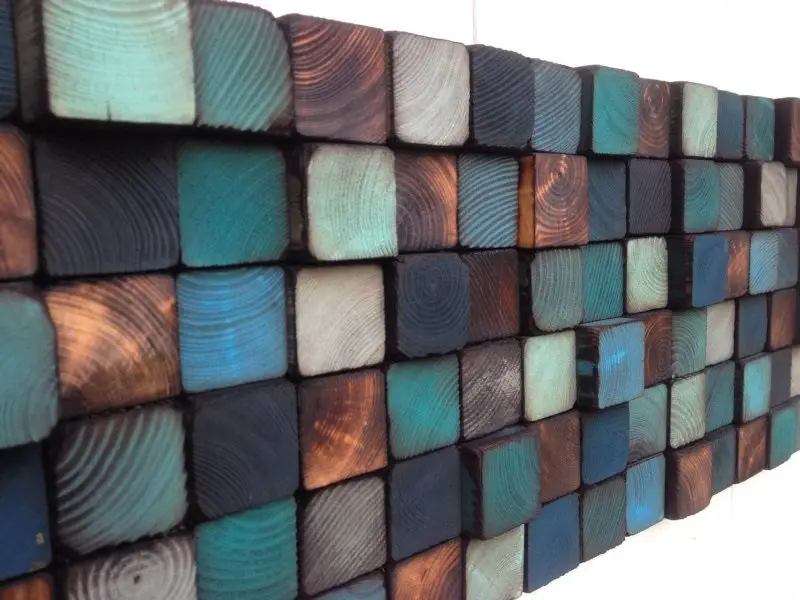
1. Preparing the pieces of wood
To make the panel, the pieces of wood are glued to a support. A strong piece of plywood is good because the wood is quite hard and the backing can bend. There are two types of decorative panels: with the same size and with different sizes of wood. The more spectacular is the one with different sizes, but the uniform one is easier to finish.
The wood is cut to match the appearance of the panel. The cut can be flat or oblique, but one side must be flat to stick well to the backing. After cutting, the pieces of wood are sanded very well, sanded and placed on the backing, without gluing, to see if they cover it completely and to make the desired pattern. If they are the same size and shape they can be glued together at this stage, and the whole panel finished. If the sizes are different each piece of wood is also stained separately. Protection with varnish or oil can be done both on each piece and on the glued panel. By finishing the pieces individually, the process is more controlled, even if more laborious.
2. Burning
To achieve the effect in the picture above, the wood must be burnt superficially. Burning brings out the natural design of the wood because late and early wood burn differently. Burning also influences the subsequent absorption of the colorant.
Burning wood chips can be done with an ordinary stove torch. Such a device makes it easier to control the level of burning. If a more powerful device is used, the burning may also be stronger. In this case, further brushing can also be done and the wood can be profiled.
Burning can also be used as a patina after coloring. But the effect must be tested beforehand to determine the duration of the burn. This results in a "smudging" of the color, a more uniform patination with reduced contrast.
3. Colouring
It can be done with water-based or solvent-based stains, brush, sponge or cloth. After applying the color, wipe off the excess immediately so that it does not penetrate deeply into the wood. The annual ring will stain differently, with the early wood becoming darker and taking on the color of the berry used, and the late wood remaining almost unchanged. Dip staining is not recommended as color absorption will be very high.
4. Protection (varnish or oil)
After staining and drying, they should be protected with oil or varnish to prevent water absorption and preserve the effect. Do not sand the wood at this stage as you may ruin the color. If the wood feels rough (especially if a water-based stain has been used), sand after a coat of varnish or oil has been applied and dried. Apply min. 2 coats for a good locking of the fiber ends.
5. Arranging and gluing
If the pieces of wood have been finished separately, the next step is to arrange and glue them to the chosen support. Follow exactly the laying out as you did at the beginning. Do not use too much glue as it will become increasingly difficult to remove as the glued pieces of wood multiply. Once you have finished gluing, allow at least up to 24 hours before putting the panel upright so that the gluing is complete. Fix it securely to the wall. Such panels are heavy and you need to make sure that the fastener will not crack over time.
I hope you find this information useful and use it to make your own decorative panel. If you find the information useful to others you can share. If you would like more information, have any queries or have any other information related to the topic you can comment below.
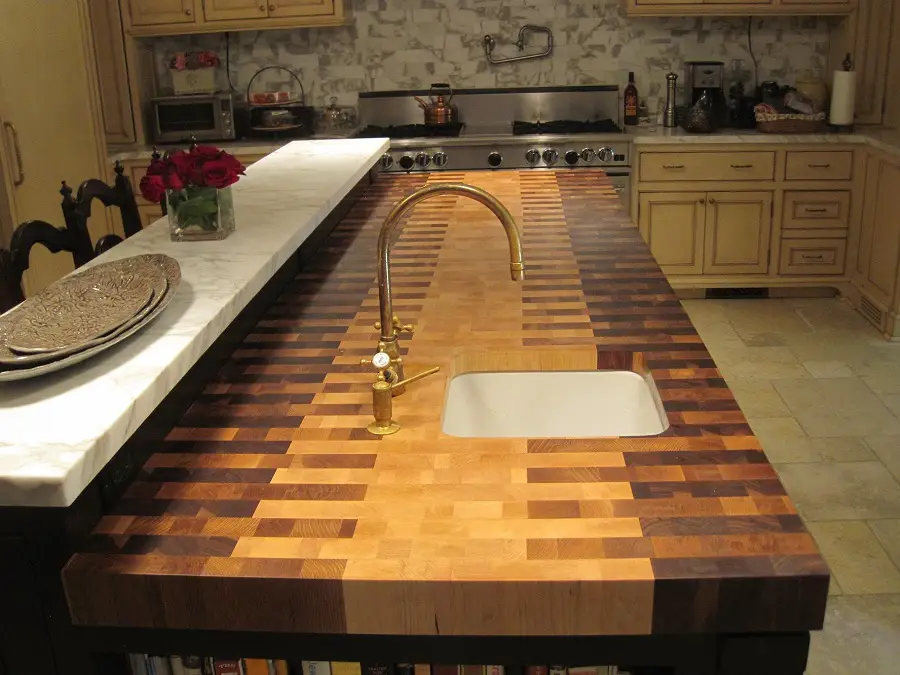
Add comment