Xavier, a Belgian living in Switzerland, wanted a well-built timber-framed house as soon as possible. The house was to be built on a plot of land surrounded by vineyards in Saint Clement in the canton of Valais, a well-known hilly wine-growing area in Switzerland. In 2017 she started searching online for the right construction company for the 380 m² house. To decide which one to choose, he talked to each one, asked for quotes and visited the factories. Among the firms chosen as "finalists" was Litarh. And following his visit to factory in Valea Moldovei decided to work with the Romanian firm.
A strong, well-insulated house built in a very short time
One of the advantages of timber frame houses with prefabricated walls is the reduced working time on site. The house is erected in a short time, the site is clean, and the resulting waste is minimal. This is possible thanks to the advanced processing that takes place in the factory. The higher the level of prefabrication, the shorter the working time on site. It was exactly what Xavier wanted. He hoped that the construction site would be as short as possible and that the vineyards would be as undisturbed as possible by the construction debris. What's more, he wanted the house to be sturdy and very well insulated.
The project was a large one - 380 m² of living space divided into 4 apartments, a garage area - all built on a sloping plot of land between vineyards. The timber-framed house was to sit on a foundation built by the owner on the consolidated land. The garages for each apartment were to be built on the high foundation.
Access to the area was not easy and there was no way to get there by truck. But a solution was found to transport the prefabricated walls to the site. In order to minimize time on site and to transport as little material as possible to the area, the builder decided to do most of the construction in the factory.
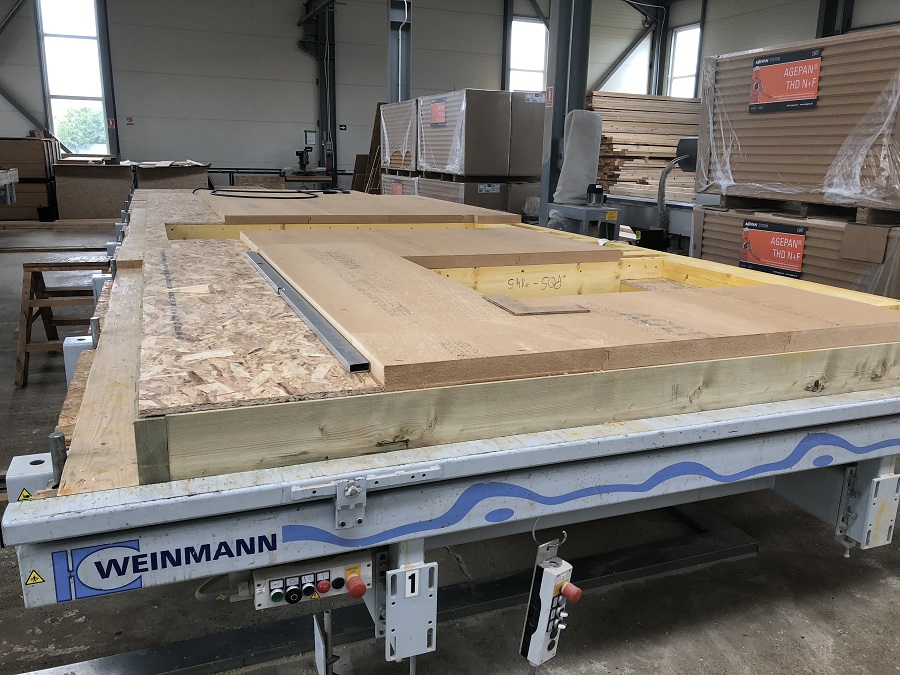
House almost ready since Valea Moldovei
This is the highest level of wall prefabrication. All the necessary wall elements were assembled in the factory, leaving only their assembly and additions in the joint areas for the construction site, which could not be done otherwise. It took almost 2 months in the factory to build the walls, the floor and the roofing.
The structure of the wall before it was loaded into the TIR truck looked (from outside to inside) like this:
- wainscoting larch 27 mm thick
- 30 mm technical guideline for façade ventilation space
- vapour dispersion film
- 60 mm external wood fiber insulation
- 200 mm wooden frame filled with high performance insulating material with λ=0,034 (λ is the thermal conductivity of the material in W/mK and indicates the ease with which heat passes through the material. The lower the value, the better the material insulates)
- vapor barrier
- OSB panel 15 mm
- 50 mm technical space
- Vidiwall panel (a high-performance version of plasterboard with a much higher density than normal drywall - 1450 kg/m³ compared to 700-800 kg/m³).
In addition to these elements of structure, strength and insulation, windows were installed in the walls. Also in the factory were made the floors and the framework, with all the necessary elements. Everything was packed, loaded into a truck and transported to an area close to the construction site. Here, using the crane, all the prefabricated elements were moved into a smaller means of transportation and taken one by one to the construction site.
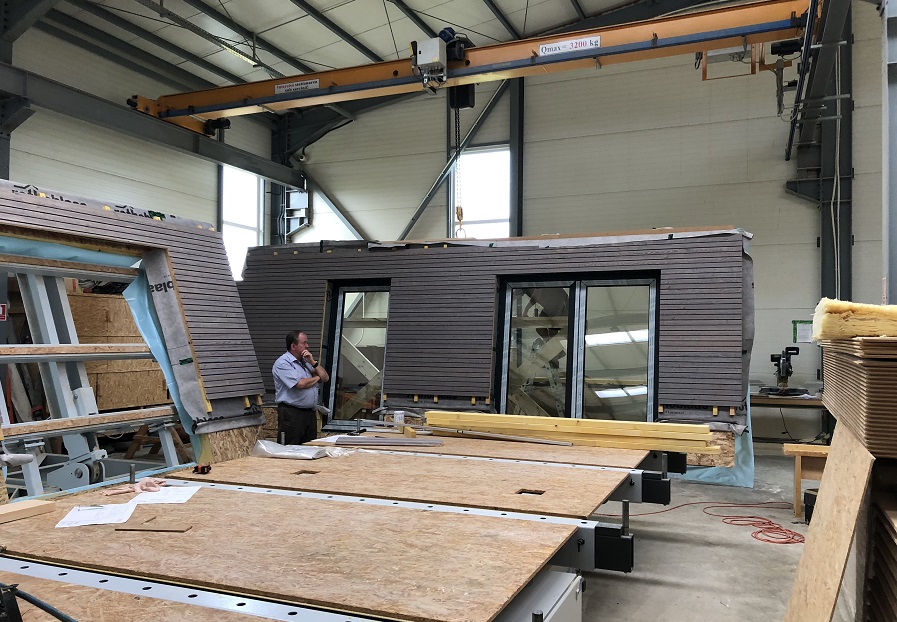
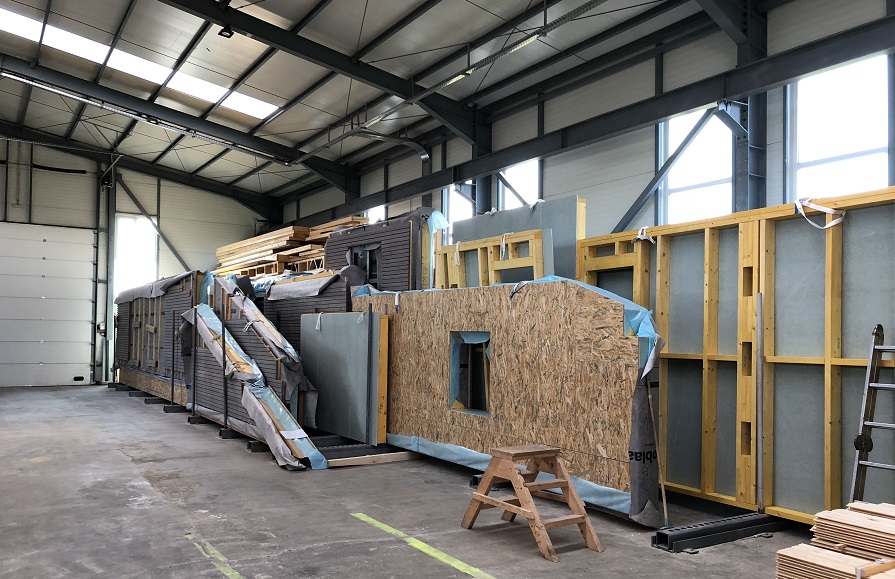
Sound insulation taken to another level
Among Xavier's requirements for the performance of the house was sound insulation. Being 4 apartments, he wanted very good sound insulation between them, both in the walls, floors and ceilings.
The thermal insulation materials used also have an important sound insulation component, but not enough to reach the level of performance required by Xavier. It seems that some of the sound waves propagate through the connectors and this had to be prevented. The technical solution proposed and provided by Rothoblaas was used, which reduced the intensity of the sound coming through the walls by 15-20 dB, thus contributing to the sound insulation of the house as required.
The insulation used in the wooden frame of the house and that in the floorboards, together with the solution provided by Rothoblaas, solved the problem of sound insulation. Now that the house is inhabited, there are no complaints about this issue and Xavier's friendship with Vlad Liteanu is still safe. 😉
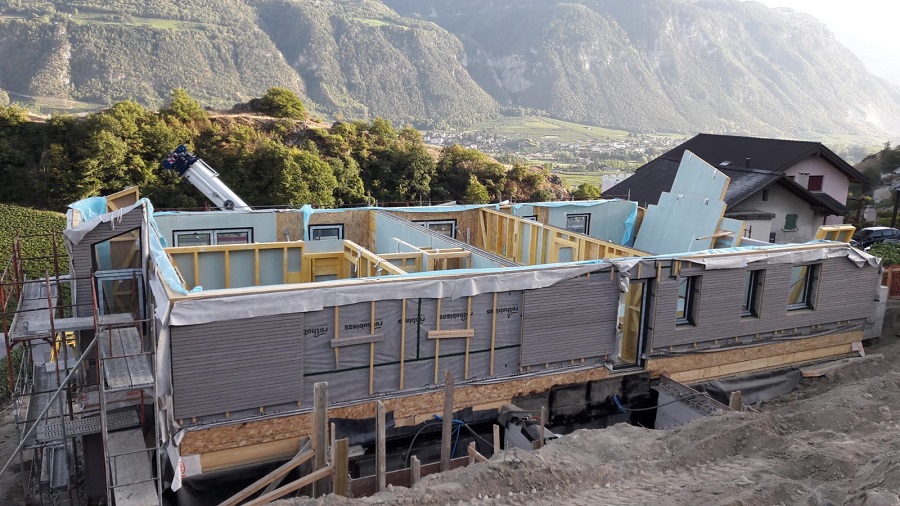
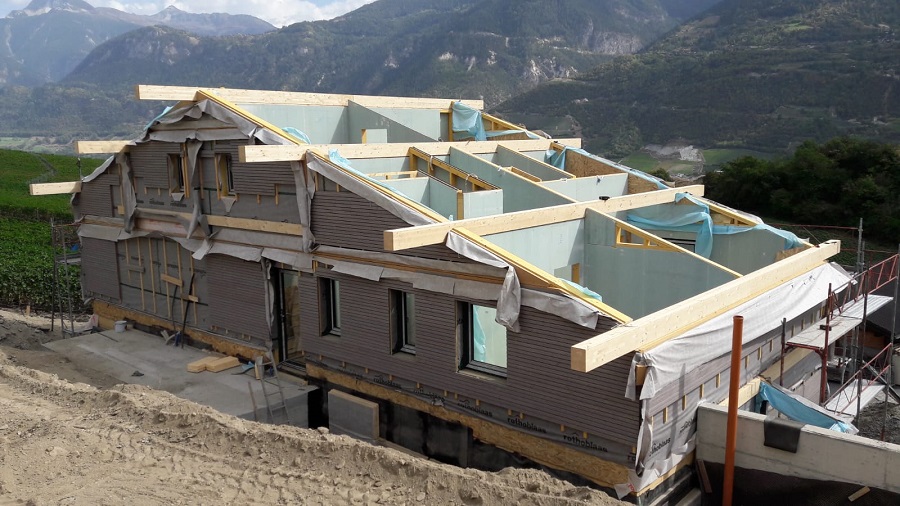
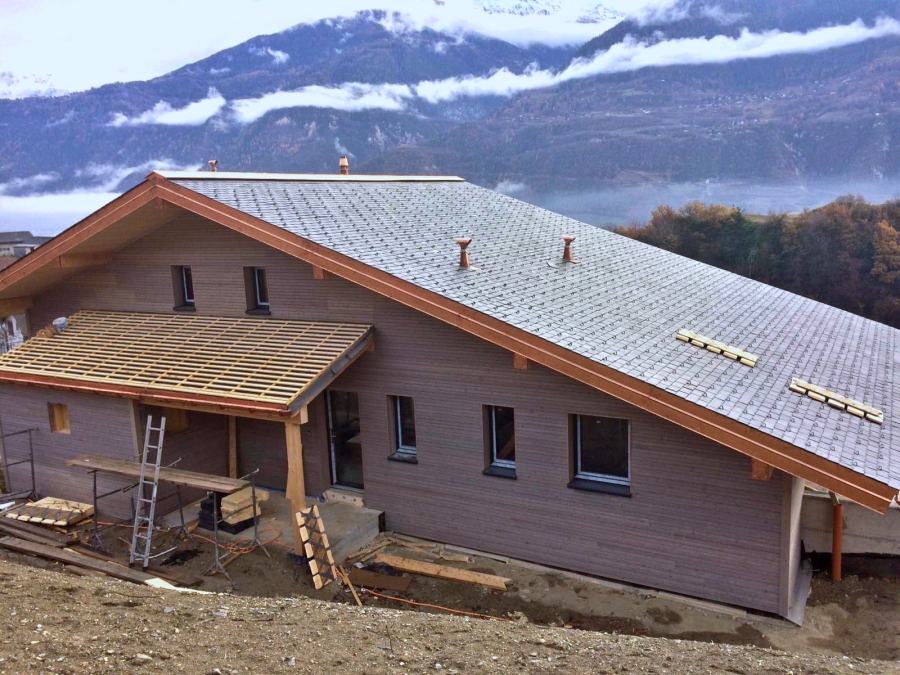
380 m² house built and roofed in 4 weeks
It took 4 months to build the house on the construction site until it was ready to be lived in, and it took just 3 and a half weeks to erect the house and put the roof on. And it was all done by a team of 3 Romanian carpenters. That's what we try to say every time we show such a prefabricated house. Its construction eliminates the waiting times inherent in a classic building site. The advanced processing in the factory results in structures that are assembled on site in a short time and without loss or waste. After the 4 weeks it took to get the house up and running, it was possible to work indoors in peace, regardless of the weather.
The technical space provided in the wall already in the factory allowed the Swiss electrician to quickly pull the electrical wiring without any additional work. Where necessary, sealing was done so that the thermal insulation was perfect and the house as energy efficient as possible.
On the exterior, the larch wainscoting was closed on the corners of the house, the walls were joined, the deck was installed and the balconies were built supported on sturdy treated wood posts. Incidentally, all the wood used for the exterior fittings has been autoclave impregnated with class 4 resistance. This means outdoor resistance for over 50 years. Construction of the house was started and completed in 2018 and it has been permanently inhabited ever since.
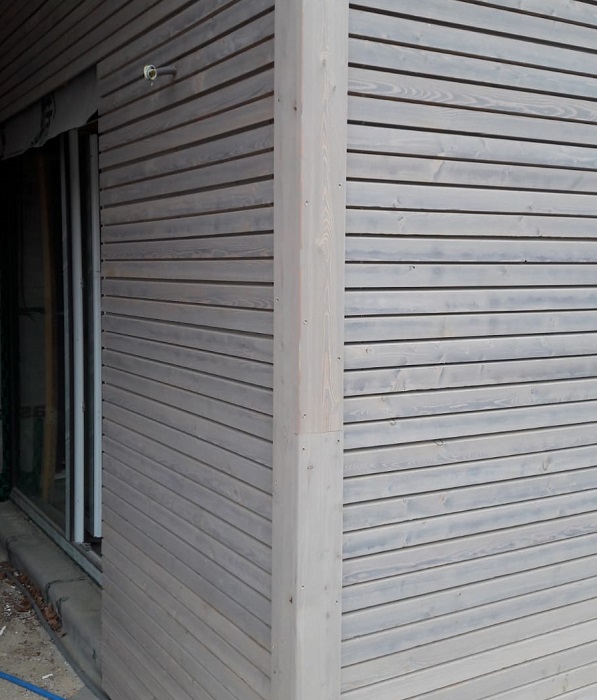
Timber frame houses with prefabricated walls are quick to build, strong, safe and energy efficient. Romanian builders have been making such houses for years in Europe and are recognized and appreciated for the correct and professional way they work. Due to a lack of information, there is still a reluctance to build them in our country. However, the information presented lately on several channels and the presentation of some houses built in the country have led more and more people, especially young people, to choose this modern, safe and sustainable way of building.
Add comment