Suppliers of wood finishing products are continually telling their staff that sanding between coats is a prerequisite for a quality finish. I actually use to say that the products are very good, but they can't work miracles. But what is it, why and how is this sanding done and, more importantly, why is it so important?
Sanding between coats of varnish is not totally different from white grinding, i.e. that which is done before it is coated with finishing materials, but it has its own particularities. It is done to achieve the best possible surface quality and to ensure adhesion between the finishing coats.
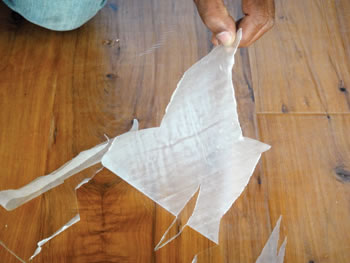
photo source: petripaint.com
Let's take quality first. When the first coat of finishing material is applied, the wood absorbs the material and the wood grain rises, less so if the materials are solvent-based and more so if they are waterborne. When the applied material dries, this raised fiber becomes very stiff and feels scratchy when you run your hand over it. For the surface to become smooth this roughness must be removed, and removal is done by sanding.
But it's not only the high fiber that creates problems, it's also the atmospheric dust or film gassing that can occur when spraying. Gassing occurs when dry varnish particles from the atmosphere fall onto the wet film and get trapped in it, behaving like an abrasive (you can scratch into them). When spraying the varnish is transformed into very fine particles. A very volatile thinner (very fast), combined with a working environment where it is very hot, causes some of the varnish to still dry from the air and fall onto the wet part and ... ready to spray. Both these varnish particles and the dust particles trapped in the varnish film are removed by sanding.
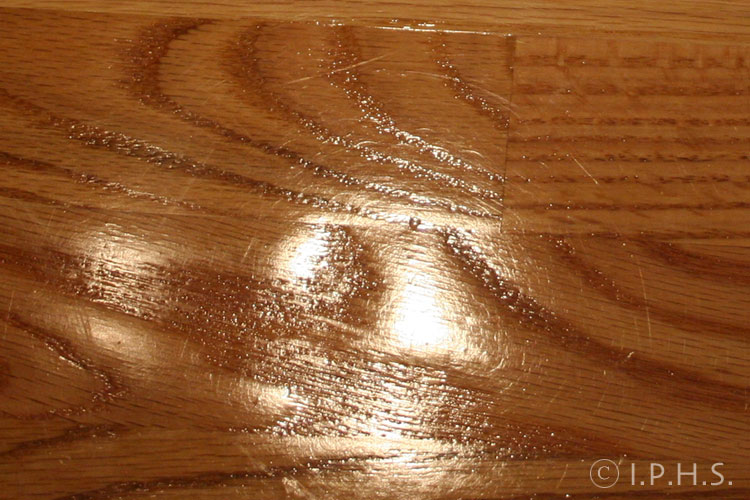
photo source: woodflooringedu.org
If more than 2 coats of material are applied, it is best to sand after each coat. There are technologies that recommend applying the coats by the "wet on wet" method. In other words, if 2-3 coats of primer are to be applied, they should be applied without waiting for complete drying, but as soon as part of the thinner has evaporated, i.e. within 15 to 30 minutes after application (no more than 45 minutes in the case of polyurethane products). In this case, of course, the layers are not sanded, but it is obligatory to sand this multilayer after total drying, before applying the final coat of varnish. The same applies to intermediate layers of UV products which do not fully cure but only gel.
Another property influenced by sanding between layers is the adhesion of the material layers to each other, where the nature of the materials used is very important. If nitrocellulose products are used, the layers of material will adhere even if there is no sanding. In this case the thinner in the upper layer penetrates into the lower layer, softens it and bonds with it to form a whole. This is not the same for chemically cured materials. In this case, because the thinner no longer attacks the lower layer, a way must be found for the upper layer to "cling" to the lower one. And this is done by sanding between the layers, when small rhizoids form in the film, to which the top layer clings. In addition, sanding removes the fully hardened part from the surface of the deposited layer and gets into the interior, where the material is softer and the reaction is not completed. It is therefore best to sand before the next layer is applied. It is not advisable to leave a long time between sanding and application (e.g. from one day to the next) because during this time the "uncoated" layer comes into contact with the air, hardens completely and you end up exactly where you started.
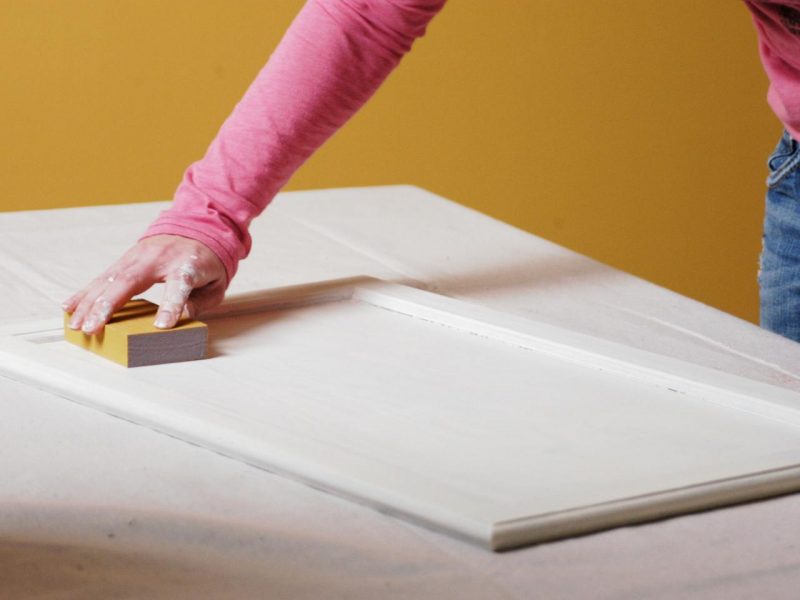
photo source: diynetwork.com
The adhesion between coats can be controlled simply with materials we have at hand. One method is with a coin which is run with the edge over the varnish layer. If a broad, white streak remains, then the layers are not adhering to each other. Another way of testing is by making with a fine cater a grid of type x and 0 on a hidden part of the finish. A scotch tape is placed over the grid and pulled. If more than 15% is removed from the formed squares then the varnish has no adhesion.
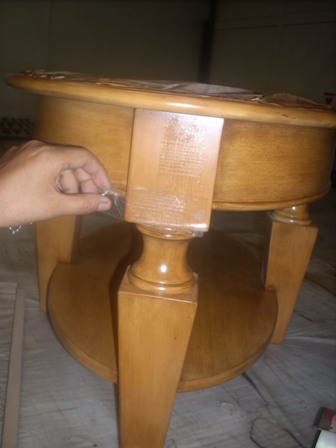
photo source: wisnofurniturefinishing.com
In contrast to white sanding, sanding between coats is done with fine abrasive sponges or 280-320 grit sandpaper for matt lacquers and 400 grit and more for glossy lacquers. The use of a coarser sandpaper (e.g. 100-150) is totally not recommended because the rhizomes formed are very large and become very visible after the next coat. Also, sanding with a coarse paper removes a much larger amount of primer and there is a risk of getting wood. I have seen in some factories where, in order to make the sanding quicker, coarse paper was used, which removed the primer completely. It was a kind of "work in vain" because you would get back to the wood and when the next coat was applied the wood fiber would rise again.
To avoid the risk of getting into the wood, even if you use the right materials, it's a good idea to carefully sand around the edges of the panels first and then sand the center.
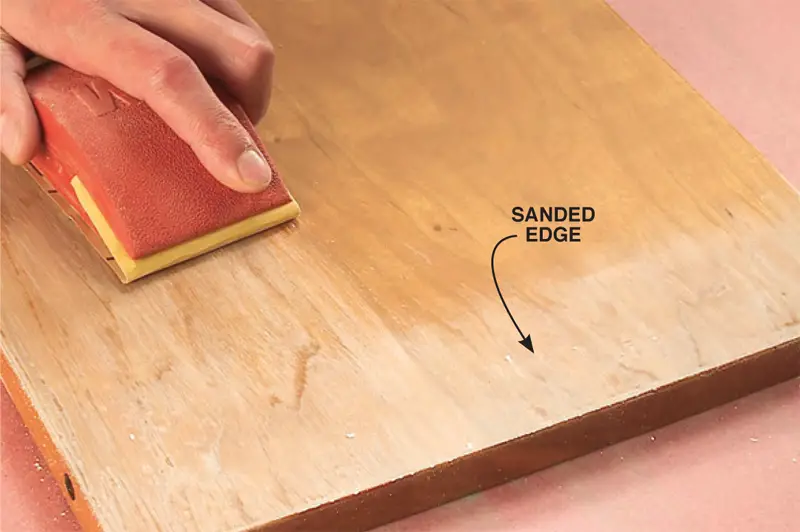
photo source: popularwoodworking.com
It is also a good idea not to use sandpaper, which is stiffer, but sponges or other materials that mold to the profile, for the profiled parts, table or chair legs or other such areas. This avoids "burning" some areas, i.e. removing the finishing materials in those areas down to the wood.
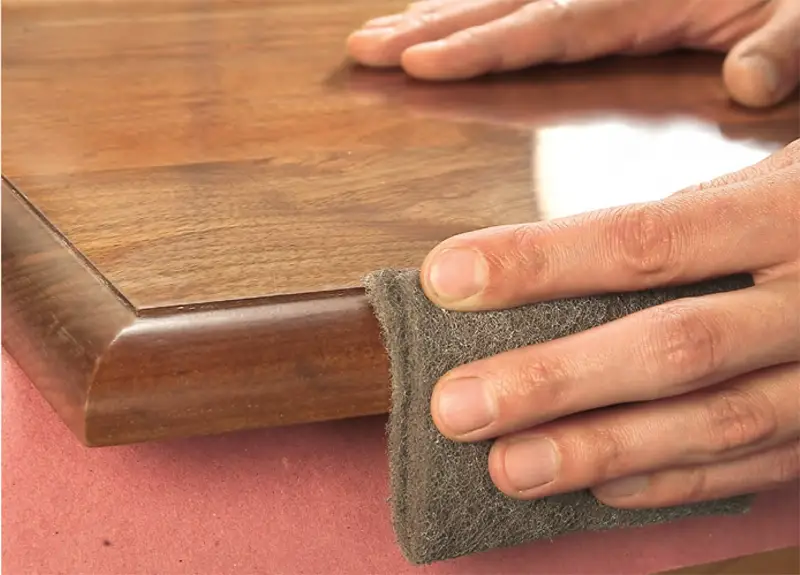
photo source: popularwoodworking.com
Sanding between coats can be done both manually and mechanically, with special machines with rotating or in plane movement, the important thing is that the sandpaper used is the right one.
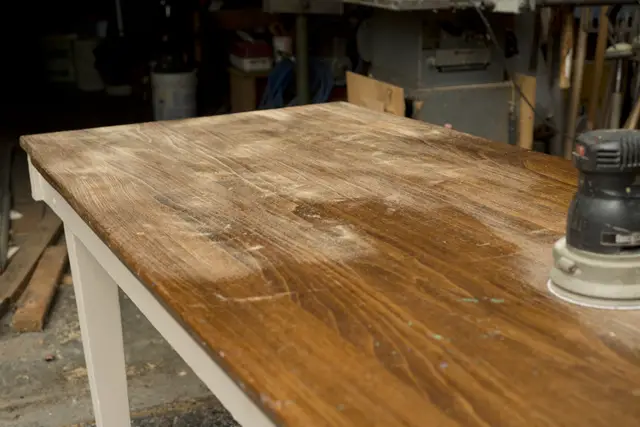
photo source: biggerthanthe threeofus.com
I hope you've managed to get an idea of what intercoat sanding is and why it's good to do it. There is much more to say on this topic, but I think it's already too much for one article.
Great! Thanks!
I'm glad the information is useful to you.
All the best!
Congratulations! well-written article, both by a theorist and especially by a PRACTITIONER. IT SHOWS THAT YOU HAVE EXPERIENCE. THANK YOU, I ALWAYS FOLLOW YOUR SITE. WITH CARE, JM
Thank you too!
Good evening,
I recently made a wooden table and painted it with water-based varnish. Unfortunately the brush application gave me a lot of trouble and the result is not what I expected. Its countertop is painted "in waves", there are several areas where you can see a rather large excess of varnish.
Do you think sanding the countertop would help me in getting a better result?
Thank you very much!
Hello!
Sanding can solve uneven film and brush marks. It will need to be vigorous to get to a flat surface that you can feel by running your hand over the entire surface. Colour stains may not be resolved by sanding and you may need to remove the fine sanding strand. You can also do this by sanding or using a notched trowel.
Water-based varnishes have thixotropy, a property that prevents them from dripping when applied vertically, but gives problems when applied with a brush because the film does not spread well. To improve the application, especially if it is on a horizontal surface, you can dilute with water up to max.10%. The lacquer will spread much better. Do not add more water because the water will be absorbed by the wood and you will have problems with the wood grain lifting and you will get a rough surface if you do not sand between coats.
All the best!
Hello! What grain size should the sanding paper of a sanding machine have for sanding varnish between coats?
Hello!
If the varnish used is matt, the recommended grits are 280 or 320. For gloss varnishes, 400 grit or finer is recommended. Gloss magnifies defects, and the fine curls that appear after sanding between coats can be seen, spoiling the final appearance.
All the best!