I've written several times about wood jointsemphasizing those in traditional Japanese carpentry which I admit I am fascinated by. Each time the comments appreciated those joints, but they also mentioned the skill of the Romanian folk craftsmen who built wooden houses and churches using swallowtail joints, which have stood the test of time and stood the test of time, standing still. Being a beautiful and durable joint, I will elaborate a little on the subject.
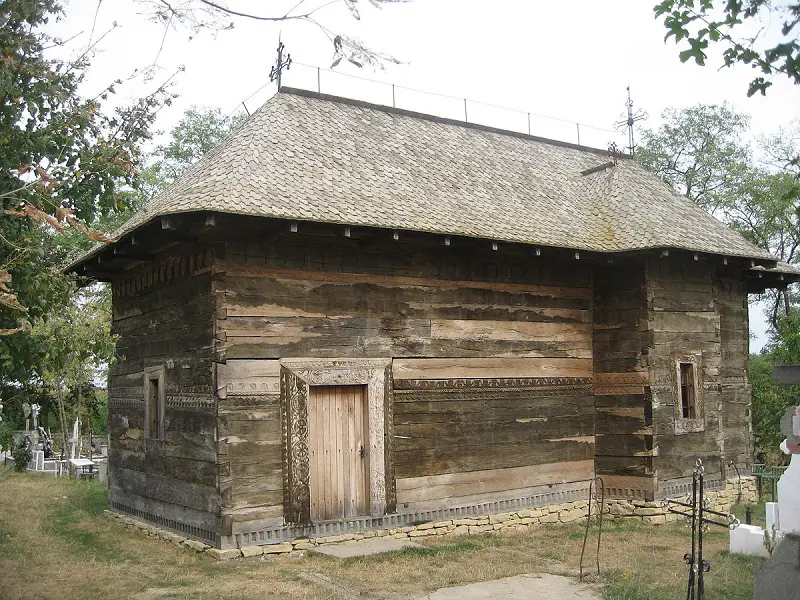
The dovetail joint is a corner joint that is not only used in houses. It has long been used in furniture construction, for example in cabinet or drawer joints. It has a very high tensile strength, which explains the preference for drawer front joints.
There are several ways of cutting and joining, and it is also a way of identifying the period to which the piece of furniture belongs. In all these joints, the wood is cut at the ends in a trapezoidal shape and the 'teeth' thus formed interlock, creating a very durable bond.
Several such teeth are made at the ends of the pieces to be joined, cutting at various angles. The teeth can be joined with or without adhesive, but nails or screws are never used. The joint holds very well without glue.
There are several types of dovetail joints:
- Proper splice - after the pieces of wood have been spliced the ends of the fiber are visible on both sides of the splice;
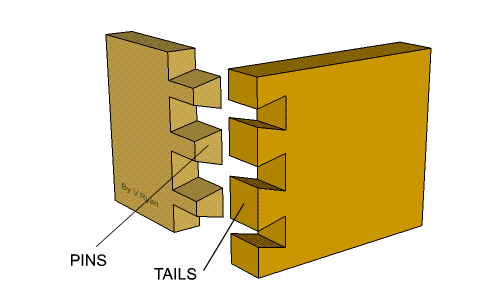
- half swallowtail (half stump) joint - the cutting of the teeth is done in such a way that after the joint the ends of the fibers are only visible on one side of the joint;
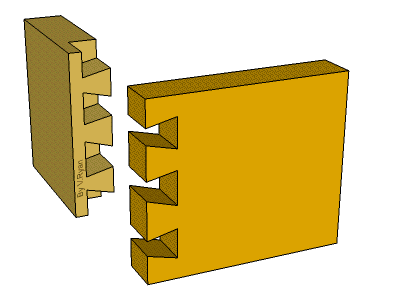
- finger-jointing - a groove with a trapezoidal cross-section is cut on one piece of wood and a trapezoidal tooth is cut at the end of the other piece. The joint is made by sliding (translating) the tooth from one end of the groove to the other
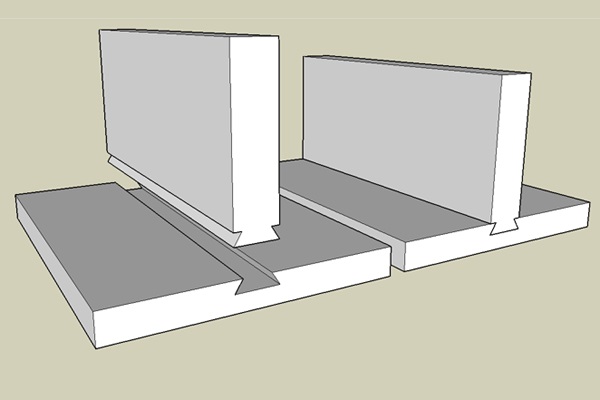
Joining drawer fronts is often done using the second method to stay hidden.
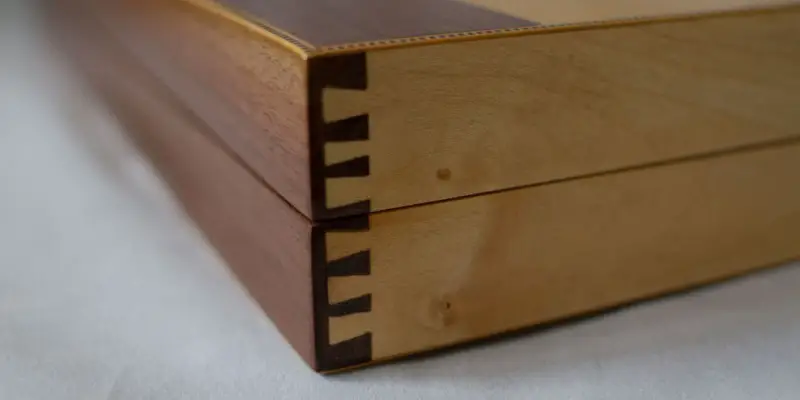
As the swallowtail is an aesthetic joint, which if done well adds value to the object, there are also craftsmen who choose to do the normal joint, visible on both sides.
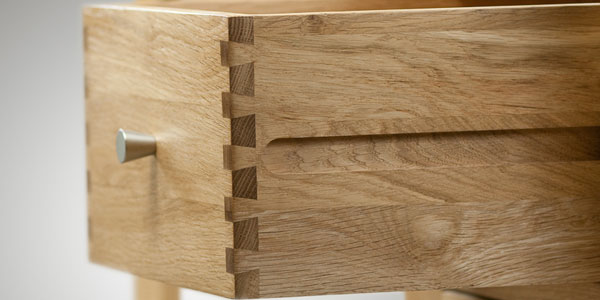
In the past, all this cutting of the wood was done by hand, with great precision, so that the wood was perfectly joined. Once it had been drawn, the sawing was done with a saw, and the fine work with a chisel.
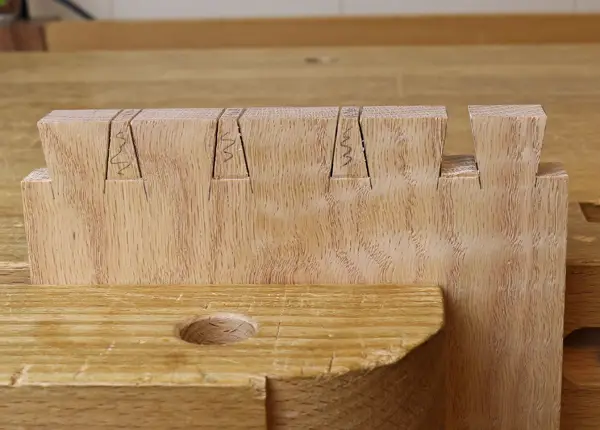
There are now router cutters that can be used to easily make the cut-outs, and on an industrial level they are made with great precision using CNCs. However, the classic craftsmen, who go the traditional way, continue to make the joints by hand, and the objects are much appreciated by those who follow the traditional crafts.
The mortise joint is the way in which logs/timbers/timber/timber strips are joined together for wooden houses. Specific to our country are log houses with a rectangular or square cross-section, as can be seen in old houses from the Maramure region or in wooden churches all over the country. Our older friends may remember church in Leleascawhich I wrote about after a visit to the area. I have seen such joins in wooden churches all over the country, so I cannot say that they are specific to any particular area.
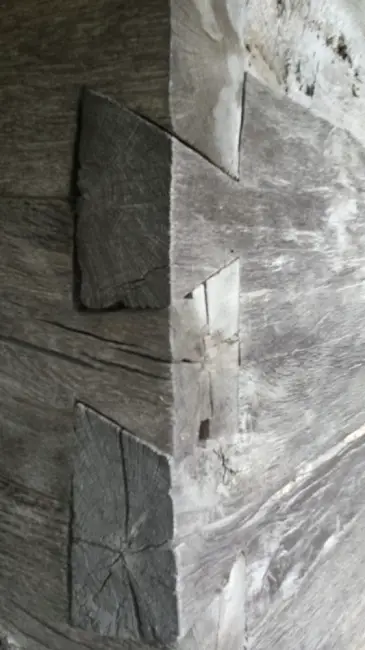
Rectangular or square-section cabinet joinery is practically the strongest, most durable option for wooden houses. It has tensile strength and is very mobile in earthquakes. It is much safer than round logs. Basically, our ancestors found the most efficient way to make strong and safe houses.
The method is the same as for furniture joints, except that they are made at macro level. The shape of the cut-out is again trapezoidal, imitating a swallowtail. In the past the pattern was carved with an axe, so you can imagine how skilled those craftsmen were who were able to make perfect joints between cabinets by making the cuts with an axe. Now they use a chainsaw and templates to make the joints as accurately and quickly as possible. In the case of industrial machining, they also use CNC.
I didn't set out to write about making dovetail joints. I am certainly not in the best position to tell you about cutting angles and dimensions, as many of you are specialists with years of experience behind you. It is, however, a joint close to our hearts, a joint with which we have begun to identify. It is a calling card to the old craftsmen who have built houses and churches that have stood the test of time, bringing proof of their skill to the present day. It is a kind of gratitude to a long and ancient line of wood carvers.
I never thought I'd learn carpentry from a woman! 🙂
There is a difference between the dovetail joint used in furniture and that used in houses. The furniture joint has tails on one side and pins on the other. It can only take traction in one direction, the other direction is used for joining. The houses have tails in both directions, thus resisting traction in both directions, but the joint is assembled by overlapping the beams alternately. Once overlapped, the joint cannot be untightened by pulling.
Compare the corner of the house (teeth are trapezoid-shaped on both sides) with the corner of the drawer (teeth are trapezoid-shaped on one side and rectangular on the other).
Thank you for the clarification.
We built a house made of wooden beams, shaped, treated, numbered and joined in circular rows one after the other in a dovetail system, ground floor and first floor on a foundation of 3.20 m with 22 pillars and three rows of 16mm reinforced concrete beams and 8mm braces, calculated according to engineers to withstand an earthquake of degree 9 on Rihter. We left it for 3 years in the initial phase, we treated it fireproof, antifungal inside and outside for three years, then we wrapped it outside with dense fireproof pilistiren of 10 cm, and inside with mineral wool and fireproof plasterboard. It has a great thermal, acoustic and electromagnetic insulation (we used autoclaved aluminium foil on the roof, and inside mineral wool with aluminium). I am at your disposal with details.
Thank you for your availability.
Hello,
I would need as many details as possible about the construction of a dovetailed beam. Can you help me? (cosmin_ghionea@yahoo.com)
Thank you!
[...] round or profiled, worked to the same size and joined into a swallowtail or nut and fed (lamb's lettuce and uluc). They are assembled at the place where the house will be, putting [...]
[...] or profiled, processed to the same size and joined into swallowtail or nut and fed (lambsquarter and uluc). Their assembly is done at the place where the house will be, putting [...]