Japan is a wonderful mix of new and old. The country that has been at the forefront of cutting-edge technology since the post-World War II years is still working with wood as it did 1000 years ago. Traditional Japanese carpentry is carried forward by authentic carpenters, true artists who respect and protect their cultural heritage.
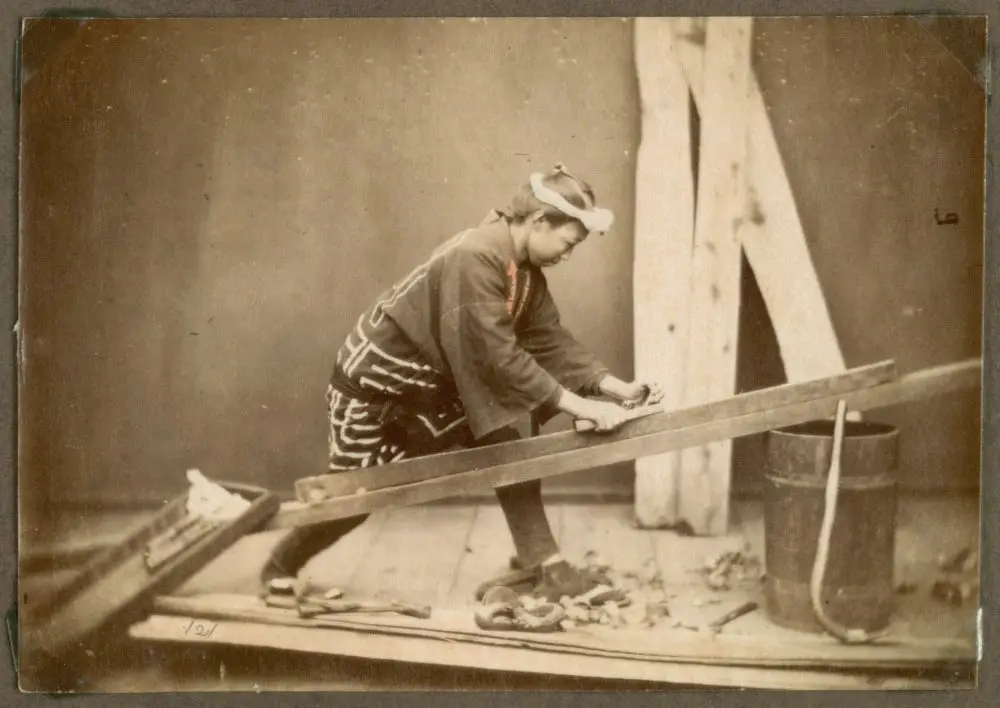
photo source: west-wing.com
The art of woodworking
Japanese carpentry is both an art and a science. Japanese carpenters manage to build furniture, houses or temples without using nails, screws, adhesives or other such methods to join wooden elements. They are hand-carved into different shapes that fit together perfectly. They are much stronger and more durable than modern joints. Temples built hundreds of years ago using these traditional jointing techniques have withstood all typhoons and earthquakes perfectly.
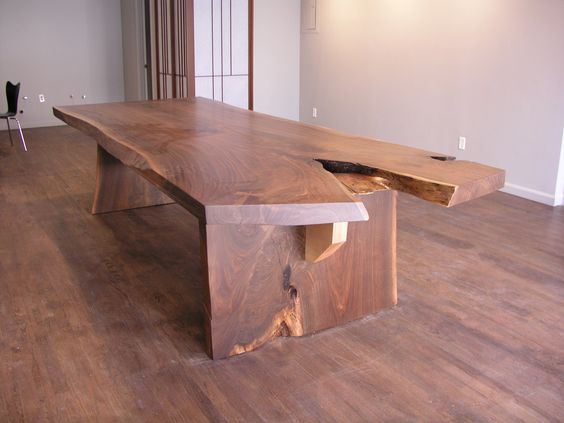
photo source: miyashoji.com
You have to work with nature to achieve your goal
Hisao Hanafusa, a carpenter who uses traditional techniques, says that in traditional Japanese carpentry you don't make nature work for you, you work with nature to achieve your goal. This belief covers a wide spectrum, from preserving the natural forms of wood without interfering with them, to philosophical ideas such as using wood from the base of the tree to work the base or frame of furniture, thus preserving the order of nature. This avoids bending the wood because "the tree does not grow upside down".
Hanafusa left Japan after graduation and settled in New York City where she and her son own a furniture store - Miya Shoji.
The furniture is handmade by the two in their own workshop, with traditional tools and a huge respect for wood. He says the traditional carpenter doesn't consider wood dead but believes in giving it new life, which is visible in the shrinking and splitting of the wood even after it becomes furniture.
The process starts with the tree, which is cut and "sliced" into planks that are left to dry and 10-20 years. Then the carpenter chooses the plank and sees what he can do with it. Again, nature prevails. You don't do the project and look for the right wood for the project, you look for a project that fits the wood.
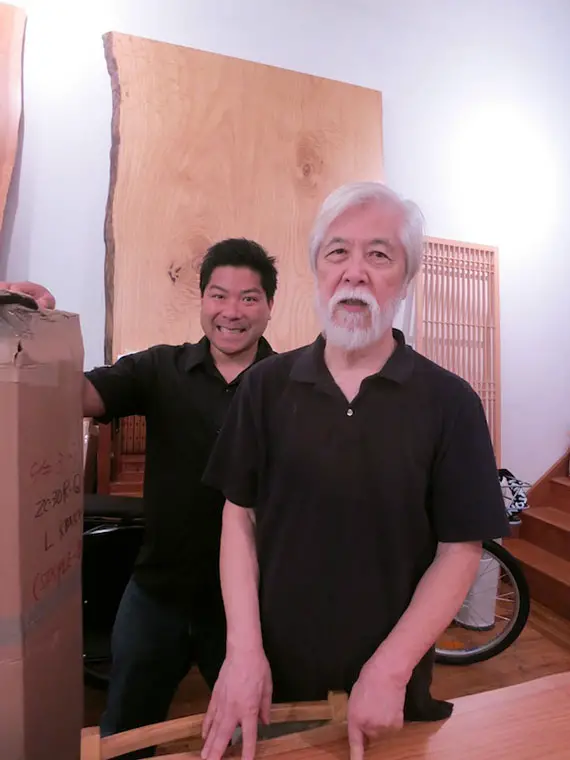
photo source: heart-2-heart-online.com
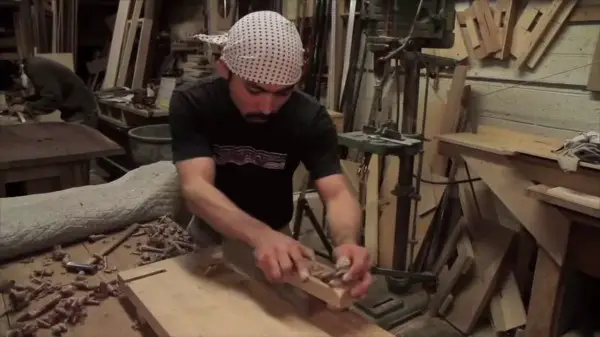
photo source: visiontimes.com
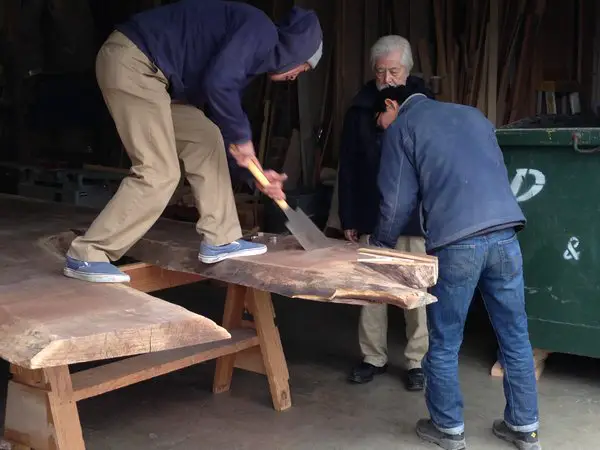
photo source: twitter.com
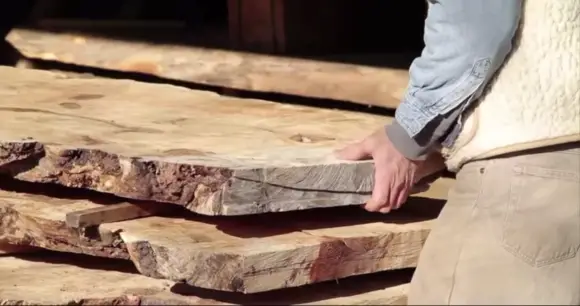
photo source: en.rocketnews.com
Joints so no nails, screws or adhesives are needed
Once the project is identified, the wood is not damaged by nails, screws and other such objects. The joints are made traditionallywith hand tools.
Working with such tools is difficult and time-consuming, but it creates an even deeper bond between the carpenter and the wood. Once prepared, the wooden elements are joined together to form the final object. This all-natural style allows the parts of the piece to contract or relax together, giving the furniture great resistance, even to strong stresses such as earthquakes.
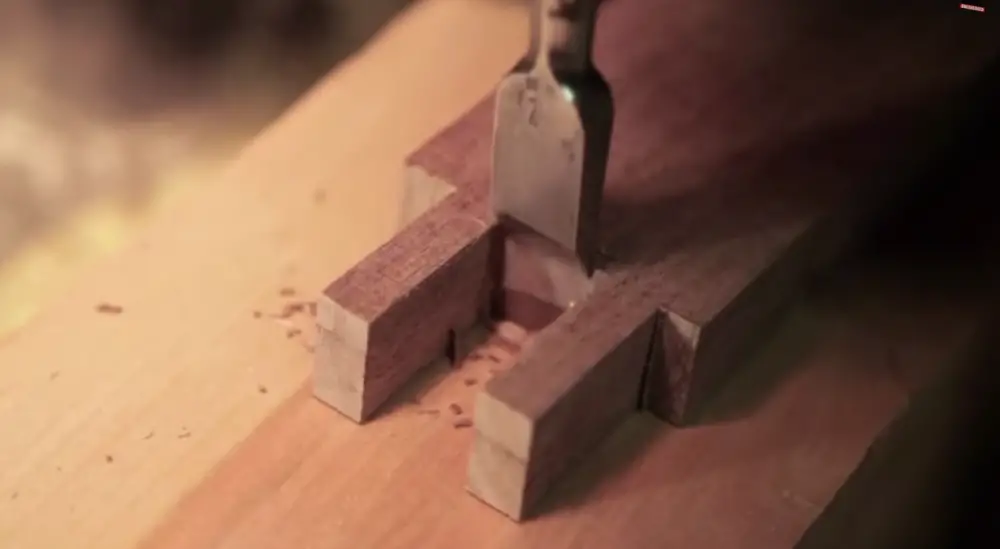
photo source: en.rocketnews24.com
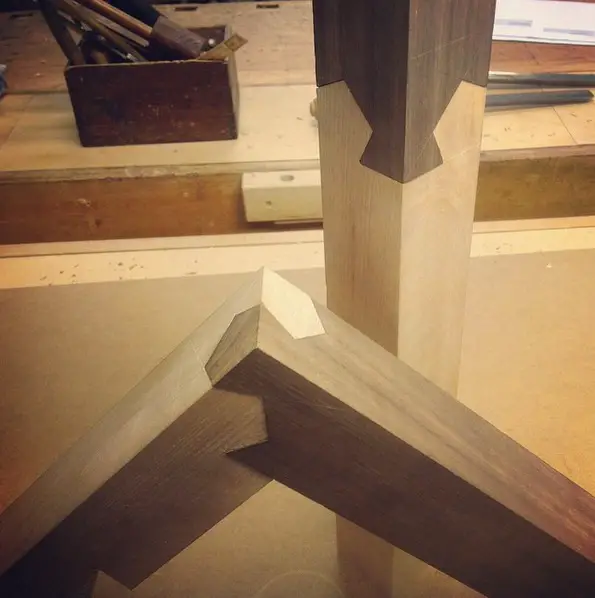
photo source: core77.com
Japanese philosophy
Over time the object will age, taking on the patina of time. Hanafusa says that this makes it even more beautiful and appreciated. In Wabi-Sabi philosophy, old objects are valued because they inspire the viewer to contemplate the passage of time and the imperfect nature of life.
Traditional Japanese carpentry is not only used to make unique and special furniture. Unique buildings are constructed with the same techniques used to build Buddhist temples hundreds of years ago. The roofs of temples were made of naturally jointed beams that gained a very high load-bearing capacity. There was no need for a large number of supporting pillars, and the Buddha statue was very visible. You can see such a traditional procedure of joining beams in the video below. The achievement of the joint is truly impressive.
One can talk endlessly about traditional Japanese carpentry. The subject is far from exhausted. You can also read about traditional wood joining techniques(you also have a downloadable book) and Japanese hand tools.
Are there carpenters in Romania who master these techniques?