We recently told you that we wanted to write more about wooden houses, especially those made in Romania. Not long ago we wrote about little houses on wheels made in Oradea which are highly appreciated by customers in Germany and other European countries. But not only small wooden houses are made in Romania. There are many people who make spacious log houses, log houses, cabinets or prefabricated wooden panel structures, and their fame has long since spread beyond the country's borders.
For example, in the north of the country, in the Moldavian Valley, a place not far from Suceava, a family for whom wood has been part of life for 4 generations builds houses on prefabricated wooden panel structures. What are these prefabricated structures? Basically they are the walls and other components of the house that are made in the factory and then transported to the site where the house will be built, assembled and joined together. The house is no longer erected by putting up the posts, knocking down the planks, putting in the insulation, but is made like a Lego game, connecting the component parts together.
Now don't imagine it's a game, it's very serious, even impressive. Houses are made just like demountable furniture. Each wall is carefully assembled, materials are put layer upon layer according to the customer's choices. The layers are then tightly sandwiched together and the walls are erected and put into the stands. Everything is worked according to the architect's design, which is then 'broken down' into component parts by engineers specializing in timber construction. High-performance design software is used, and the whole project is first realized and simulated on computer. The walls are then made on the basis of this design. Finally, all the house components are loaded into a truck and transported to the site where they will be assembled.
I saw all this in the company's production hall Litarh, where I went for a visit a while ago. I was curious to see them "at home" after having met Vlad Liteanu-Voinescu, a very energetic and enthusiastic young man, at the BIFE SIM 2017 fair in September. Vlad is like his father a wood industry engineer and the wood "bug" runs in their family since Vlad's great-grandfather, a well known carpenter in the area. He practically co-founded the company with his father.
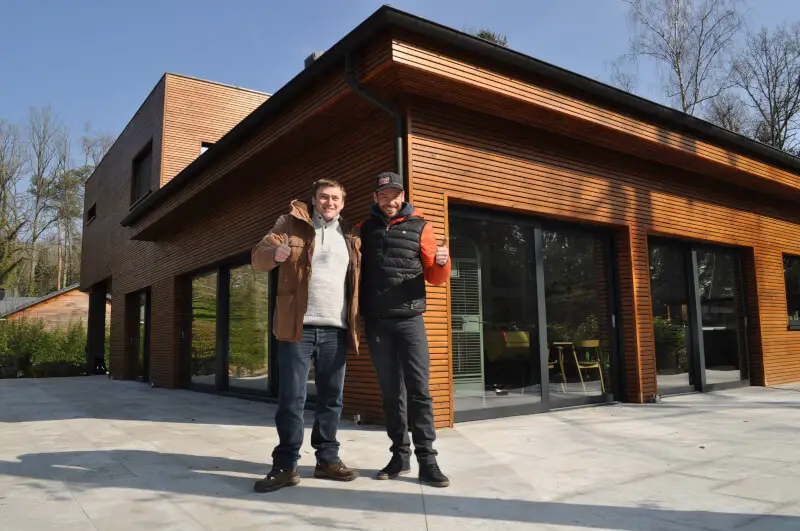
I was impressed by how well equipped the manufacturing hall is. Vlad told me that they have the first Welnmann system in Romania, a German system used for prefabricated walls. I saw it at work and Vlad's enthusiasm caught me too. It's a huge table with two sides, which I call "butterfly". On one side is made the wall with the necessary layers for the interior. It's then tightly clamped and a system is operated to turn it over to the other side. The 2 sides of the table rise up like the wings of a butterfly, and the wall is slowly, without being brushed, passed to the other side. In this way all the components remain fixed in place, without the risk of shifting, as would happen when turning using a crane. After turning, the exterior elements are added, then the wall is assembled, lifted up and placed in the stand. This system allows walls up to 6 m long to be assembled.
Prefabrication can be very advanced, so that there is as little as possible left to do on site. For example, if wood paneling is used on the outside, it is already treated and painted with exterior-resistant products. Likewise, if timber framing is used on the interior, it can be finished. Only when the customer wants to finish it in a particular way are the walls left unfinished.
How advanced the prefabrication is also depends on where the assembly takes place. Because, as I told you, the ready-made walls are transported by a truck and there they are put in place with a crane. If there is room for the truck then there are no problems. But if access is difficult, the "game pieces" have to be made smaller so that they can be transported by suitable means.
Transportation and assembly is also done by them. The more advanced the prefabrication, the simpler and faster the assembly. Vlad told me about a house in Bucharest that was assembled in just one day. Of course, the foundations were already in place.
Very important is the collaboration with the beneficiary. They must come with a project. I can also help those without projects, but they have to have a very clear idea of what they want. Great things can come out of collaboration. Vlad was talking about some young, IT-savvy clients who built a house near Bucharest. They have equipped it with all sorts of sophisticated intelligent systems, some of which are absolute novelties in Romania. The fact that they knew from the start what they wanted and by communicating all their wishes to the builder, they were able to install the systems right from the start, without the need for any further intervention.
The houses made in the Valley of Moldova have reached countries such as Italy, France, Belgium, Norway, even Austria, which is recognized as an important producer of wooden houses. Note that they have all the necessary accreditations and certifications for all the countries where these houses are built.
Sub-assemblies are professionally manufactured by unmotivated workers. If they were equipped with quality overalls and not their own clothes, the company's image would be improved. Pity. Overalls are not expensive.
Good evening, Mr. Gustav. the first thing our workers receive on hiring after the work protection training is the protective equipment, which includes overalls/trousers and is renewed whenever necessary; unfortunately, this equipment is not worn all the time, for more or less objective reasons; if you will follow our website you will see many achievements where it is worn; in no case we have unmotivated workers or we do not make ´´economies´´ by not purchasing equipment; we appreciate, however, your post.
Hello,.
Nobody is looking for a knot for the sake of looking, but we Romans have a quality of drowning in a glass of water.
I'll give you an example of Mr Liteanu's perception of the customer who enters the site, looks at the forums, makes hundreds of comparisons between companies and their products and finally has to decide.
The impression left is that when you walk into a few star restaurants, order food and find yourself served by a waiter dressed in your personal clothes from home.
You ask the head waiter if that man works there or if it's some kind of live prank and he apologizes, saying that...: "unfortunately, the "equipment"/suit is not worn all the time, for more or less objective reasons".
Unfortunately, it is not the employee's fault for not wearing the equipment provided, but the employer's fault for failing to instil in the employee the policy of the company in which they work.
In fact you know what the paradox is ????
You are running amounts and turnover figures with many zeros which is exceptional but the impression is that you are making this money with day labourers.
Isn't it a pity Mr Liteanu for all the work you have done so far to drown yourself in a glass of water???
NB:
A man looking for a company that can make him a home!
We are builders of gazebos, terraces, pergolas.. and I can tell you from experience that I have been to work in overalls and in personal clothes, the conclusion is that in the end it mattered more the quality of the work, the relationship with the customer, to be responsive, jovial, the price and others.Yes, maybe in a large company many would emphasize the exterior, but there are other more important aspects.
The problem with unmotivated people is a common one in many companies, as long as a person is not doing what they like it is hard to be motivated consistently, the solution would be a leader among them.