I've been using the phrase "finger-jointing" lately when talking about how a piece of wood can be "extended". It is a much used method so I think more should be said about it. About other joints such as swallowtail is much more talked about, perhaps also because it is more spectacular and widely used by those who regard woodworking as an art. But finger-jointing, although used for important semi-finished products such as massive panels and lamellar beams, where endurance requirements are very high, is not so widely promoted. But now its time has come.
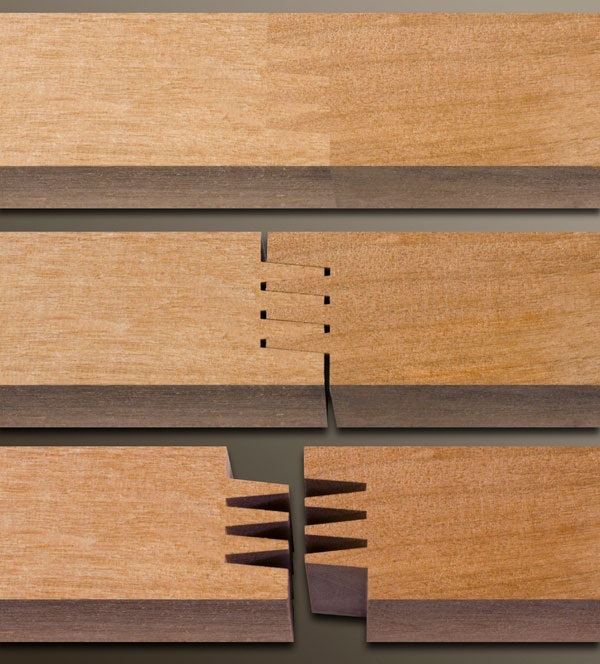
Wood joints fall into two broad categories: demountable and non-removable joints. I don't think I need to specify what each means, the names are self-explanatory. Each category has a variety of ways to make the joint. The in-tooth joint falls into the category of non-demountable joints, and is considered the most stable joint in length. It is not only a matching of 2 pieces of machined wood, but also the glue, whose qualities influence the performance of the joint. A piece of finger-jointed wood is stronger than a piece of the same size but in one piece, because the stresses in the wood are eliminated. As a result, the wood no longer twists or bends, and the risk of cracking is eliminated because weak, defective areas have been eliminated.
I told you it is the most stable and strongest joint lengthwise. But why is it stronger than one made on flat ends? Because, with the introduction of the splice teeth, the method of joining is totally different from butt joining:
- the contact surface becomes much larger,
- bonding is not done on the end of the fiber but parallel to the fiber.
The pieces of wood to be jointed are machined at the ends to create a zigzag profile that makes you think of teeth (or fingers, in English known as a 'finger' joint). finger joint- finger joint). The teeth of the two ends must match perfectly in order to get a quality bond. If one side has longer teeth the glue will not be able to hold because they will force the recess. The result will be a weak bond that may fail. If the teeth are shorter there may be holes in the glue line or larger buildup of ugly looking adhesive.
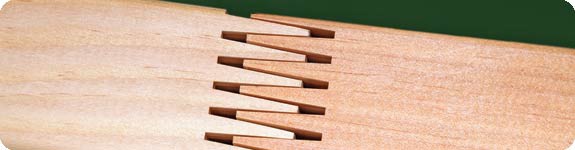
The geometry of the joint is very important and that is why it is now made with high precision tools (milling cutters). It is quite difficult to do by hand, a deviation of a tenth of a millimeter can result in a failed joint. The teeth can be made longer or shorter, thicker or thinner, depending on the cutter used. It is good to know that a joint with longer teeth is stronger than a joint with shorter teeth, just as a joint with more and thinner teeth is stronger than a joint with fewer and thicker teeth.
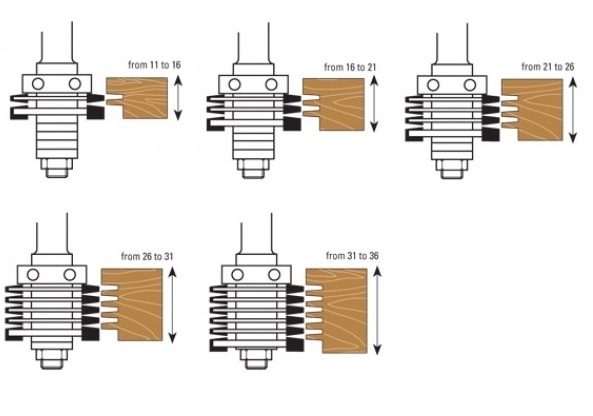
In factories where solid wood panels or laminated beams are made, joining pieces of wood to make long elements is part of the production process. That is why there are special, sometimes automated, lines that do this. The steps in such a process are as follows:
- choice and preparation of material
- tooth formation
- application of adhesive
- aligning and pressing the ends of the elements
- strengthening the adhesive
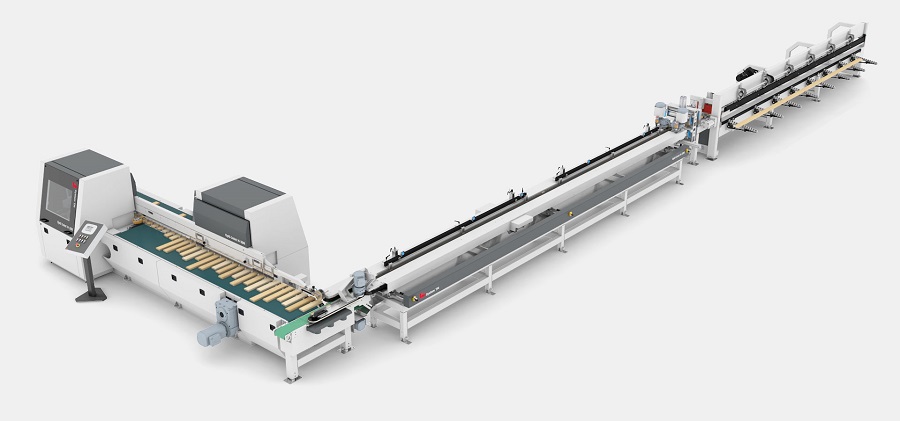
Material selection and preparation involves removing wood defects and straightening the ends for milling. Prior to this stage the wood is dried to an equilibrium moisture content of 10-14% depending on the requirements, after which it is cut to the required dimensions.
Tooth formation is, as I have already told you, the most important step. The wrong choice of profile compromises the bond and strength of the panel or beam. The length of the teeth is different depending on the requirements of the finished product, those for beams being much longer than those for panels. The teeth are made with milling machines performance with very high accuracy.
Adhesive application can be made with various devices. For example, an applicator that reproduces the profile of the heads can be used. Adhesive is placed on the applicator and then passed over the profiled heads, thus transferring the adhesive to the teeth. Nozzle devices similar to spray guns are also used. As the profiled tip passes through the nozzle, a quantity of adhesive is released and deposited on the teeth. Whatever the method, the amount must be very carefully controlled. Too little will result in a bond that can loosen. The amount of adhesive should be slightly more than that covering the 2 ends so that when they are assembled and pressed to fit snugly together, the excess adhesive will come out. This is to make sure the glue line is continuous.
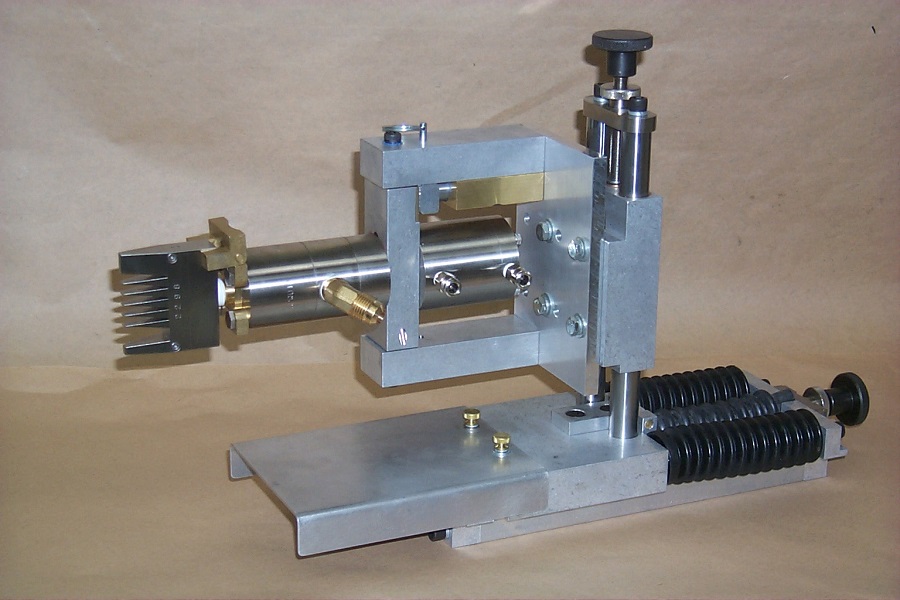
The adhesives used in the industry are generally melamine-urea farmaldehydic or resorcinic. They must provide a secure and moisture-resistant bond. These adhesives are heat-cured. PVA (polyvinyl acetate), a cold-curing adhesive, can also be used. PVA is widely used in small factories or workshops.
To make the joint, adhesive-coated ends must be aligned and pressed. The operation is very important because if the pieces of wood are not correctly aligned, crooked elements can result. Also, if the pressure exerted on them to join them together is not high enough, empty places can remain inside the glue line, thus weakening the strength. To eliminate such problems special machines.
The last stage is strengthening the adhesivehot or cold, depending on its nature.
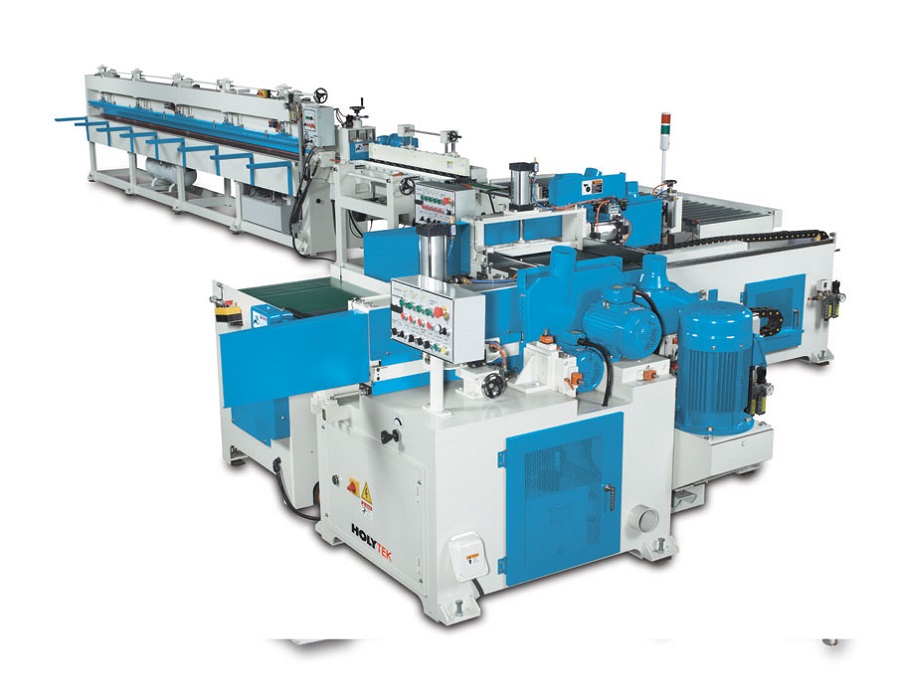
Finger joints can also be made between pieces of wood of different species. The transition from one color to another is quite interesting. They are also used for other wooden objects, not just panels (chairs, tables, furniture, doors, windows). As a curiosity, in the past it was used to join wooden elements in the first cars. And now there are still wooden elements finger-jointed in luxury cars.
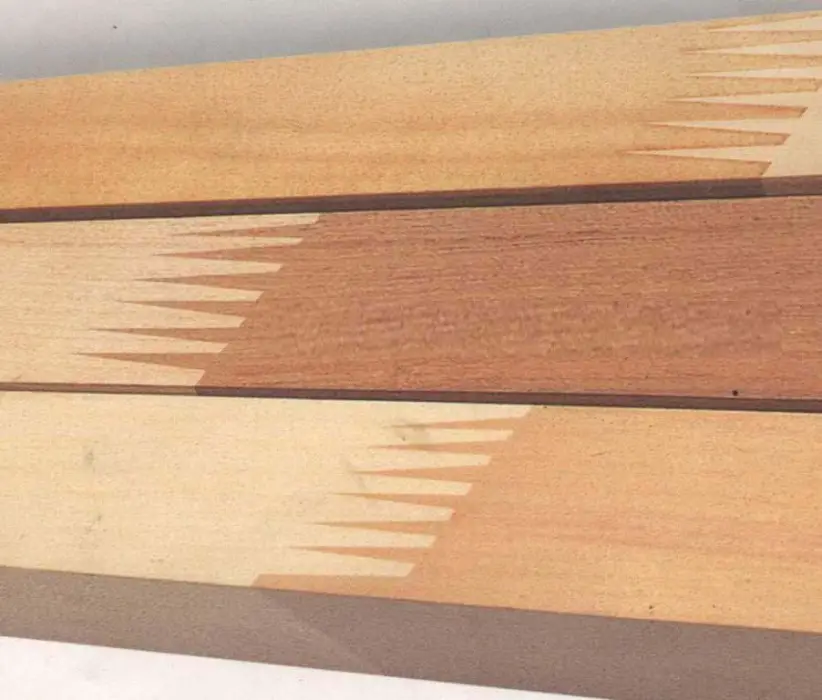
The adhesive line is very discreet and transparent or slightly brownish. There are no problems of incompatibilities when finishing, as the panels or beams can be colored and varnished or treated with oil. Finishing materials should be chosen according to where the joined products will be used, indoors or outdoors.
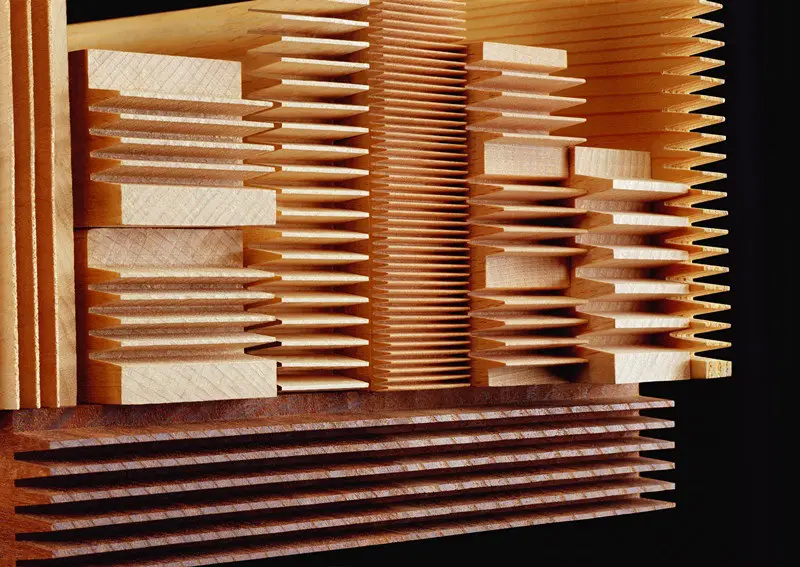
Add comment