Problems when gluing wood are not necessarily the fault of the adhesive. There are many other factors to be taken into account, including storage and workroom temperature, preparation of the wood substrate, its humidity, the amount of adhesive applied, and the setting time. The parameters to be respected as well as the way of working are always specified in the product data sheets and for a good quality of gluing, they must all be taken into account. As I always say, products no matter how good they are, don't work wonders. I spoke to representatives of the company Szolvegy from Targu Mures, the manufacturer and distributor of adhesives TISZABOND, to see how problems can occur in bonding even when using quality adhesives. So let's see how gluing is influenced by working parameters, wood qualities and environmental factors and what problems can occur when gluing wood.
PVA-based dispersion adhesives (polyvinyl acetate) have a liquid base component and finely divided solid components floating in the base component, together forming the dispersion. During drying of the adhesive, when it transforms from liquid to solid, the water is removed with the effect of the grains coming together and then coalescing, forming the film. This is how the tack is achieved and the process is irreversible (there is no return to the original liquid form). If this process of particle bonding is not complete, the adhesive will not provide the desired tack. Solidification of the adhesive is achieved only under optimum conditions, which are always specified in the product data sheet.
Minimum film forming temperature
One of the most important parameters influencing bonding is the minimum temperature required for clamping. PVA adhesives are water soluble, so water is the main liquid component. This type of adhesive freezes at temperatures below 0°C and the adhesive is destroyed. Consequently, a temperature above 0°C is required for the adhesive film to solidify.
Minimum film forming temperature (TMFP) is the temperature at which the adhesive can still create a continuous film. At temperatures below this the film will not form. The result of drying will be a white, tack-free, powdery coating that peels away from the wood. The temperature at which this occurs is also called "bleaching point". This information is always included in the product data sheet, and is always around 5°C.
There are various reasons why the adhesive film does not reach the required minimum temperature. Here are some of them:
- The adhesive has a low temperature, below the minimum film-forming temperature. The reason may be that the adhesive is stored in an inappropriate place. For example, the storage room is not heated at the end of the shift (during the night) or at the weekend. During this time the temperature drops very low. The temperature of the adhesive will also drop and at the start of the job, if it is not allowed to reach the required temperature (minimum film-forming temperature), problems will occur when the adhesive is frozen.
- the temperature of the wood to be glued is too low. This may be because the wood stored outdoors or in storage has not had sufficient time to reach the minimum film-forming temperature before processing begins. In pieces that have been glued in this way, because the entire cross-sectional area has not been heated, the center of the plane of the glue "cools" below the minimum film-forming temperature. Even though the grip will be good at the edges, only a powdery layer is formed inside and the adhesive film loosens.
- reduced temperature in the workspace.
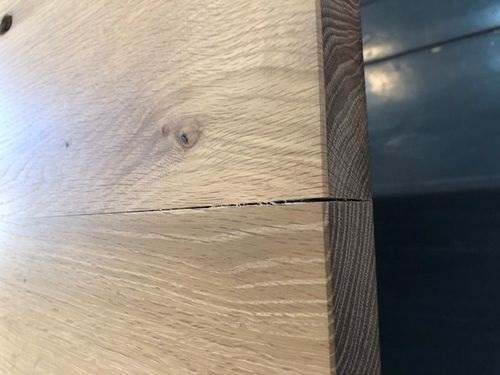
How to avoid problems caused by low temperatures. Eliminating the causes
Adhesive should be stored in heated rooms. Avoid cooling it below the minimum film-forming temperature. That is, the adhesive should never be stored in rooms where the temperature is below 5ºC, even if it is outside the actual working time (off-shift, weekends).
Before applying the adhesive the wood must be heated so that the temperature of the wood over the entire cross-sectional area exceeds the minimum film-forming temperature. It is recommended that the wood material be stored a few days prior to processing in suitably heated rooms and that the piles/stacks be so divided and arranged that the warm air from the heat source has access to as large an area of wood as possible. If the stacks are not spread properly the air will not reach the middle planks which will not heat up. Remember that wood is a very good insulator.
The workshop in which the gluing is done must be heated to a temperature compatible with the gluing process. Cannot be glued in unheated rooms or where the heating has only been switched on for a short time and the temperature inside is very low, preventing the wood and adhesive from exceeding the minimum film-forming temperature.
Removing water from the adhesive to form the film
Another parameter influencing the quality of the bonding is water removal. The adhesion of PVA dispersion adhesives is achieved by the evaporation and/or absorption of water into the wood pieces. Water is removed from the adhesive in two ways:
By evaporation. The characteristics of the adhesives and their working mode are usually set by the manufacturers at 20°C and a relative humidity of 50-60%. If the conditions of use in the factory differ from the above, the parameters of use of the adhesives (open time, release time, rest time, etc.) will also have to be changed. If the deviation from the optimum values is very large the above mentioned times are modified.
Increasing the temperature will lead to faster drying of the adhesive resulting in a decrease of the technological times. On the contrary, if the temperature decreases, the technological times increase. The variation of air humidity in the working area also influences water removal. If the humidity decreases, the adhesive dries faster and the processing time decreases, and if the humidity increases, the processing time also increases. Variations in temperature and air humidity are particularly important in winter and summer because this is when values are reached that affect the bonding process.
Through water diffusion in the wood. The humidity of the wood influences the time it takes for the adhesive to cure. If the wood is drier, the water in the adhesive is absorbed more quickly, whereas if the wood is wetter, the water in the adhesive is absorbed much more slowly. If the wood material is too dry, the adhesive will be absorbed deep into the wood, leaving an insufficient layer of adhesive on the gluing plane and an inadequate bond. And if the humidity of the wood is too high, the adhesive layer will dry more slowly and the technological times (press time, rest time) will increase considerably. In extreme cases, when the wood is very wet, curing may not even take place.
How to avoid problems with water disposal. Explanation of different behavior
As the external environmental parameters (temperature, humidity) change, it is also necessary to change the technological times accordingly. Especially during the change of seasons, in spring when there are big changes in temperature from one day to the next or during the hot summer months.
The moisture content of wood is very important as it has a significant influence on the workability, gluing capacity. Freshly cut wood contains a large amount of water, which must be removed before processing. This is done by drying. After drying, the wood will change its moisture content according to the external environmental conditions, until it reaches equilibrium with the external humidity in the given climate zone. So, a given temperature and relative humidity corresponds to a given wood moisture content.
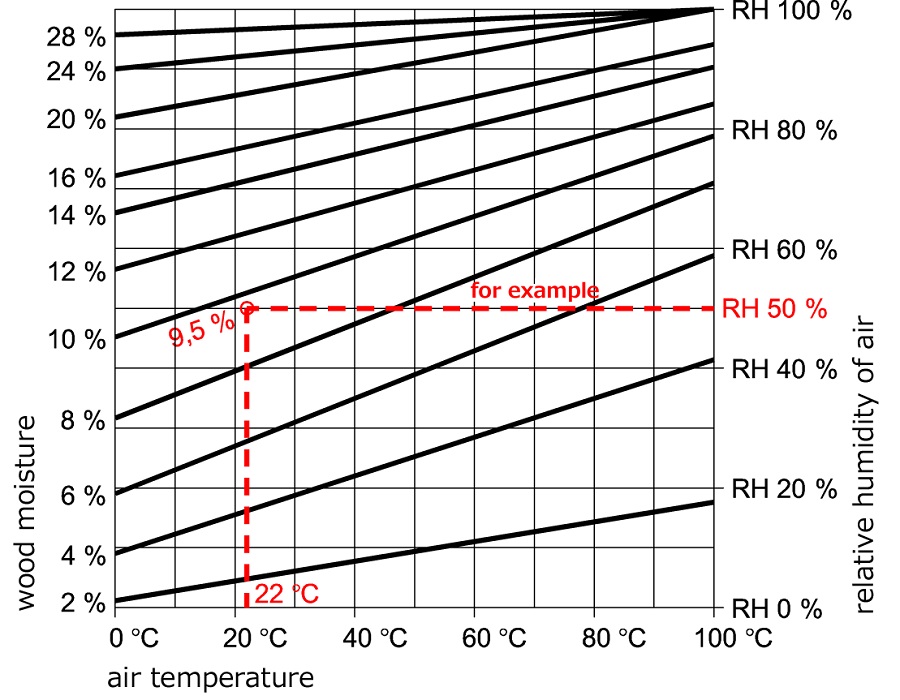
source: woodproducts.fi
Wood should be dried according to its intended use, indoors or outdoors. Interior wood (furniture, paneling, decorative objects) should have a moisture content in the range 8-12%, while exterior wood (exterior cladding, pergolas, fences) the 14-18% will dry out.
It is recommended to reach a moisture equilibrium during drying that is close to the moisture content during processing. This saves energy and greatly reduces subsequent dimensional changes and deformation of the finished product.
Another consequence of the variation of the element's humidity is its dimensional variation and sometimes deformation. Dimensional variation in wood usually manifests itself by shrinkage or swelling. Because of these changes, the bond is subject to additional stresses. In addition, wood is an anisotropic material, having different properties in different directions, along, tangential or perpendicular to the grain. This makes its variation different depending on the type of cut. Thus, pieces that look almost identical but are different in terms of cut (along, perpendicular or tangential to the fiber) will have different changes when the moisture varies. The result will be that some parts will curve and others will not, or the curvature will be different even if the parts are identical.
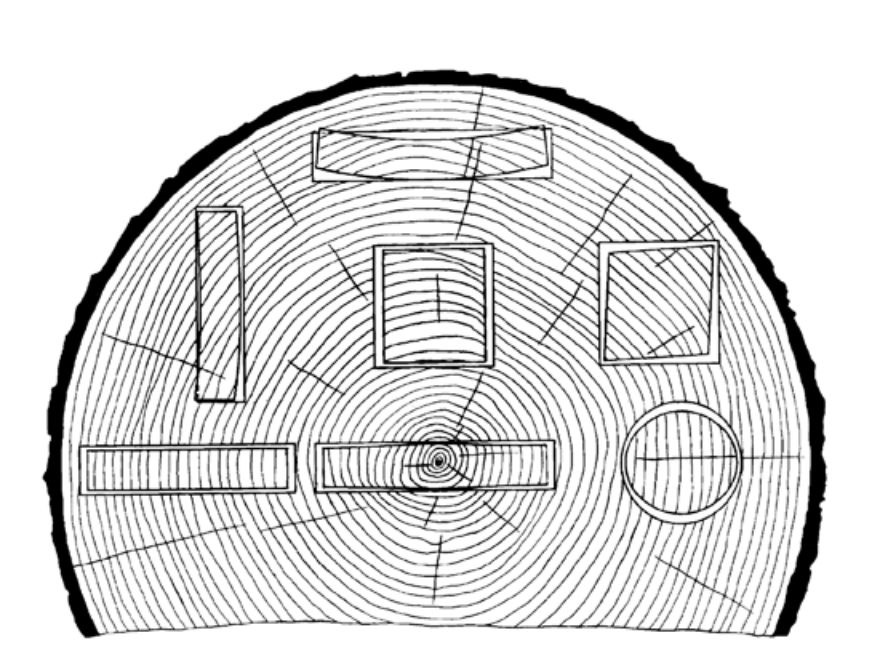
Source: instructables.com
Timing is very important
In order to be able to determine the causes of problems in gluing wood, it is very important to see whether the problem occurred during or after gluing, as well as the time elapsed before the problem occurred. In some cases quality problems occur during or immediately after gluing. They are easier to notice and to remedy. If they occur days or even weeks later, however, the causes can be multiple and it may take time to pinpoint the exact cause of the problem. The wood used may play a role. If the gluing is not done perfectly, following all the instructions given by the manufacturer in the product data sheet, dimensional variations in the wood caused by changes in external parameters generate additional pressures which stress the glue and can lead to its destruction.
Szolvegy professionally addresses any problems that may arise in the wood nailing process. The company's specialists focus first and foremost on finding the cause so that problems are eliminated and the risk of their reoccurrence is completely removed. The combination of the professionalism of the technicians, quality adhesives and a very good relationship with the partners, based on cooperation and honesty, make "for a secure bond use TISZABOND" adhesives not just a corporate slogan.
Add comment