Another novelty that Biesse plans to present at Ligna, alongside the AUTOMACTION, is the AKRON 1100, a machine that brings state-of-the-art technology to small workshops. Ligna, the biennial meeting of forestry and wood industry professionals, will take place May 27-31 in Hannover, Germany. The fair is impressive every time, a real show of strength where companies from the sector present their latest products, technologies and concepts. It will certainly be the same this year. The focus will be on the latest technologies in the field, digitalized, automated solutions, IoT platforms or interconnected systems. An excellent opportunity for Biesse to present its concept and latest machines.
The capping operation
The capping machine is an important piece of machinery in factories and workshops wood-based panels. Large panels are cut to make component parts of furniture, but the interior of the boards becomes visible. In addition to the unpleasant appearance, there is also the risk that through those areas moisture entering or compounds emitting from inside the plate which are among the most unpleasant (formaldehyde) All these problems are solved by applying a panel-width strip, known as a cant. The edging can be PVC, ABS, acrylic, melamine, veneer or wood. In the past, this was all done by hand and the results were not always the best. A hot-melt glue was used, and an iron was often used for pressing and as a heat source.
Now, however, when the market is faced with an increasing number of orders, higher and higher standards, shorter delivery times and more sophisticated designs, machine manufacturers need to provide the most appropriate technological answers, adapted to each working style and business size. This is what Biesse is doing, continuously adapting its products to market requirements and bringing the most advanced technologies to the shop floor.
State-of-the-art technologies used by Biesse on its carcass linting machines
Biesse's offer in the field of cartoning machines is diversified and adapted to each type of production. The company's R&D department is continuously developing modern systems that make work easier and increase the quality of the finished product. Here are some of the systems that can be found on Biesse cartoning machines:
Air Force System - a system that achieves very good bonding quality, with invisible edges, very good resistance to time and humidity. The system is based on the convection principle. By means of a flow of compressed hot air the edge is perfectly bonded to the panel, the bond line between the edge and the panel face being invisible. This makes the panel very water resistant, which is a great quality for wood-based panels.
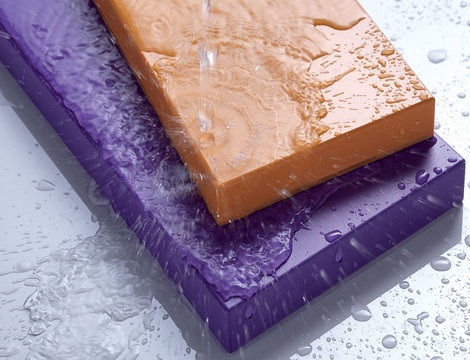
Pre-freferencing system - Equipped with 2 motors, it is programmed so that processing is perfect and executed in the shortest possible time. The programming makes the process run automatically with maximum precision.
End Trimmer System - High-fine final adjustment system, especially recommended for delicate high-gloss surfaces. Cutting and final edge trimming is done with a system that perfectly copies the edges so that they cannot be rubbed or scraped. The cut is very fine, the distance between the edge and the panel is minimal (the smallest on the market).
The AKRON 1100, the smallest and most powerful car in its segment on the market
AKRON is a series of highly adaptable and easy to use lathing machines. The predecessors of the Akron 1100 are the Akron 1300 and Akron 1400. Each of these has its own series which, starting from basic features, can be configured in multiple variants to adapt the machine to the factory working mode, production type and existing space.
AKRON 1100 is the smallest, and the only, full-length tape liner on the market. It is simple and compact, easy and intuitive to use, and the results are very good. It uses the same technology as machines for large factories. This makes the high-performance technology accessible even to those with small workshops or those just starting out in making wood-based panel furniture. It is a sure way to be much more efficient and to increase product quality significantly.
The machine features high quality components, Rotax electrospindles manufactured by world leader HSD, removable and refillable glue reservoir, rigid and safe. Simple to use thanks to technical solutions specifically designed to simplify everyday work.
All activity can be monitored with the 7-inch Smart Touch control panel, on which production parameters are always available. The SOPHIA work platform informs the operator when certain parts need to be replaced or when machine maintenance is required.
More technical information can be found at Accessories-Equipment. I entered my e-mail address in the field under "Technical Specifications" and automatically received the brochure by e-mail.
If you want to see the latest in woodworking technology, don't hesitate to plan a visit to Hanover from May 27-31.
Add comment