Life is constantly changing and sometimes situations arise when we need more space. Events such as the birth of a child, setting up a workspace at home, elderly parents needing more attention almost always come with the need for extra space in order to maintain the same quality of life. Those who live at home are privileged because the need for new space may not involve changing their home. They can extend or atticize their home and end up with considerably more space. One of the quickest and cleanest ways to do this is to build with prefabricated wooden structures.
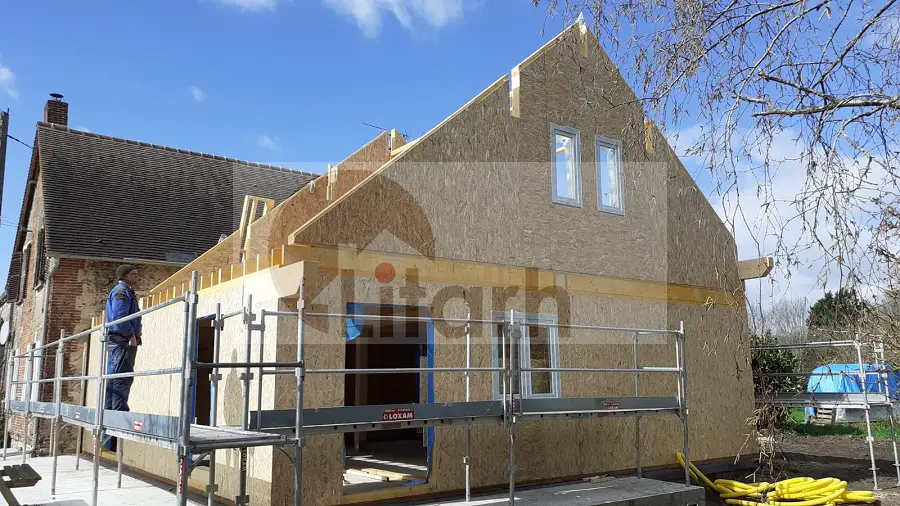
Litarh, builder of wooden houses in the Moldavian Valleyhas had such projects mostly abroad. Foreigners are much more open to this way of building than we are and prefer it to the traditional way, especially as land for a new house is expensive and increasingly hard to find. From simple lofts and simple extensions, to building a one-storey house incorporating the old house or extending a 19th-century house, everything has been made possible thanks to the flexibility and safety of prefabricated wooden structures. Vlad Liteanu, the director of Litarh, recently returned from France to work on the extension of a 19th-century house in Courcelles les Gisors, in the Oise region. From him, we learned why foreigners choose to extend and atticize their houses using wooden structures. Here are just 5 of their arguments.
Short working time on site
The problem with attics or extensions is that people are already living in the house. A months-long building site is the last thing they want. Even more difficult is when it's a vertical extension. The house has to be unroofed, and a long time without a roof means seepage from the rain, which can lead to unpleasant consequences.
When working with prefabricated wooden structures most of the operations are done in the factory. The walls, in addition to the insulating material inside, may have windows and doors fitted or may be finished on the outside up to the wainscoting. On site these walls are simply fitted following the project guidelines. Everything is very well calculated so that the fit is exact and no further work is needed.
In addition, on a construction site where prefabricated timber structures are being built, there are none of the downtimes of a normal construction site, such as the time needed to harden the concrete. The floors and walls are ready-built, and the only time needed is erection. The whole floor can be erected in a single day and the extension completed on the outside in less than a week. The working time on a house without a roof is greatly reduced and the risk of leaks very limited.
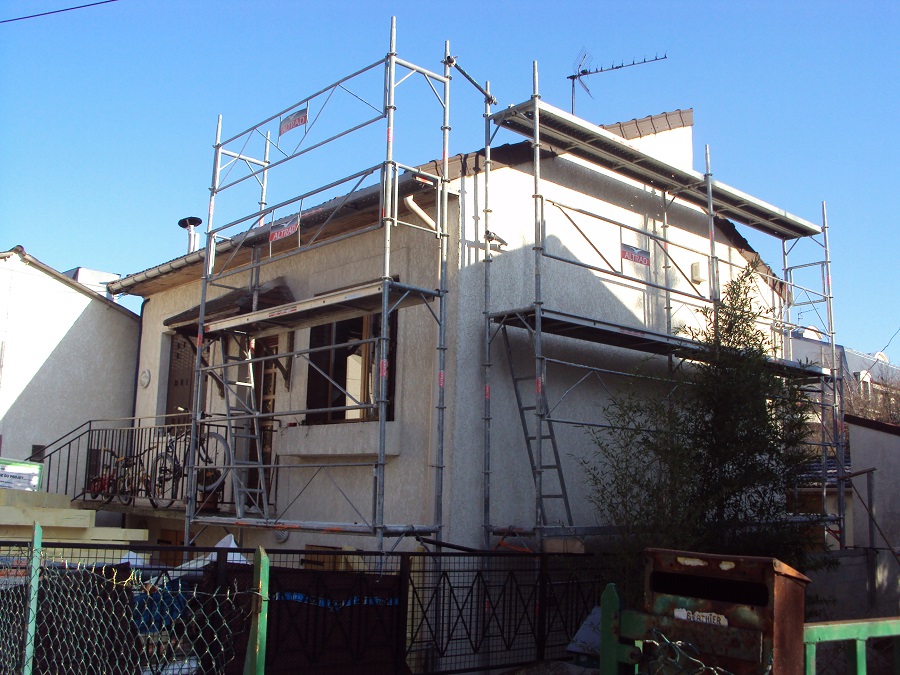
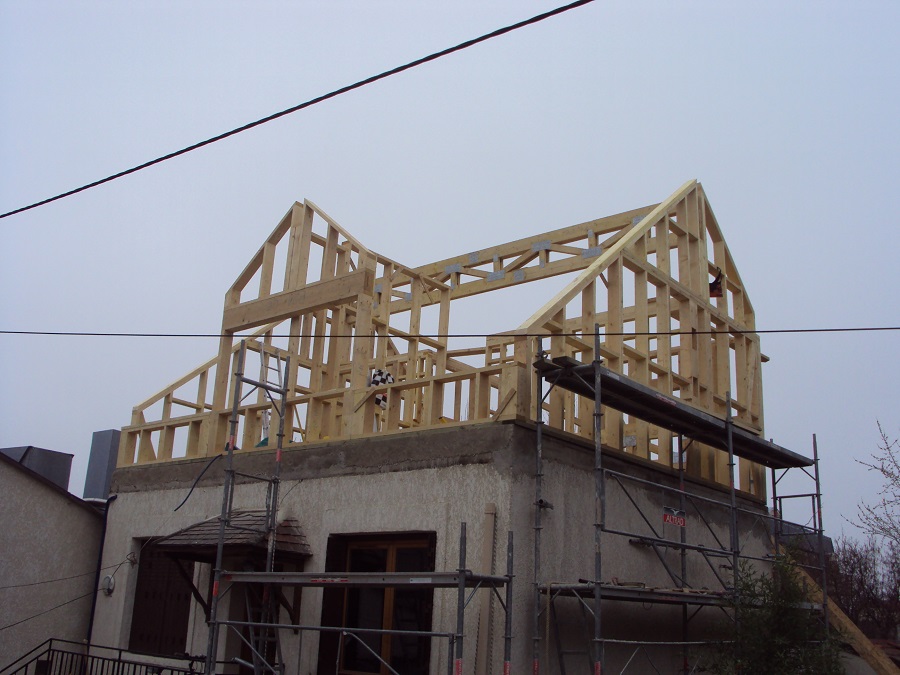
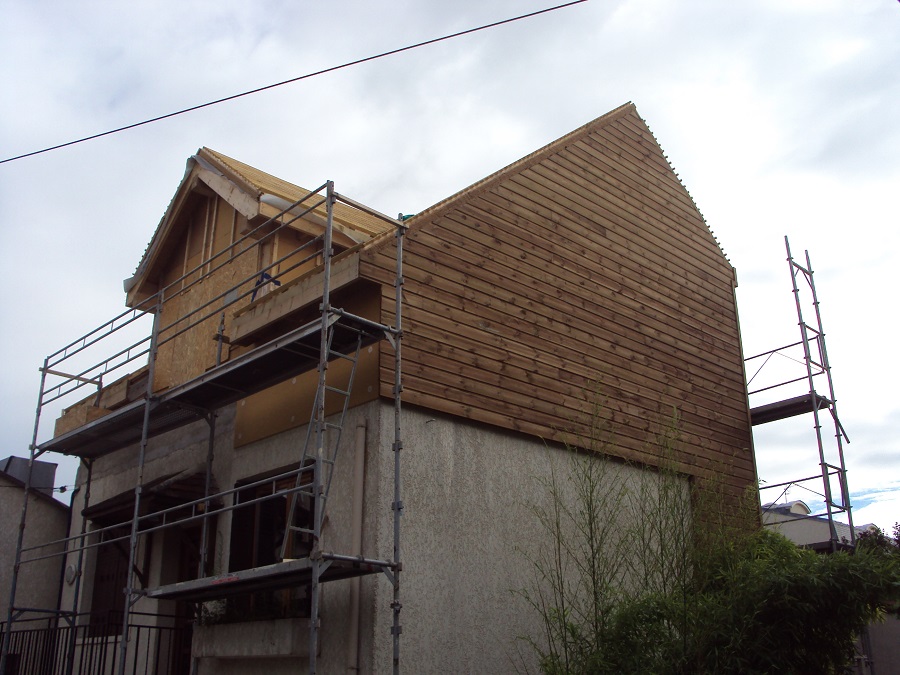
Clean, waste-free construction site
The attic or extension done with a timber frame house building company starts with a design. Everything is very well calculated and sized so that the walls and floors end up fitting perfectly. The more advanced the prefabrication, the more precise everything is. That's the essence of this work. If the walls didn't fit perfectly, the whole job would be compromised. All this precision also results in a very clean construction site. There's no scrap wood or insulation materials because they're built into the prefabricated structures right from the factory. All the waste from such a site ends up in a few bags. It's all clean and carried out with minimal disturbance.
Even if the walls were formed on the construction site, there would not be as much waste as on a traditional construction site. There are no empty bags of cement, hardened concrete scraps, irons and other such debris. The wooden structures (posts and beams) are made in the factory according to the design, and the smaller pieces of insulation are reused, so they are not waste.
Buildings with prefabricated wooden structures are lighter and independent in terms of strength
It is well known that wooden structures are much lighter than brick or concrete. The walls of your house may not even be able to withstand a traditional over-storey, but there is no problem if the floor is built on a wooden structure. And no, don't think lightweight means that the wind will blow it away. This type of construction is very popular in Europe, the USA and Canada, so strong fastening systems have been developed. There are plenty of connectors that fasten the loft or storey securely to the underlying construction, totally eliminating the risk of wind damage.
Nor do extensions need very complicated fastening systems. They are designed and built as stand-alone systems (a house in their own right) and do not need to be attached to the old construction to be strong. Thanks to the multiple finishing possibilities, the exterior will look like a single, 'one-piece' house, although in reality it is two adjoining buildings joined together only by the crossing points. "The 'independence' of the buildings also has the advantage of preserving the strength of the walls of the old house, which are not being pinned together. This is how the extension to this old house in France was designed. The new wooden structure is completely independent of the old one in terms of strength.
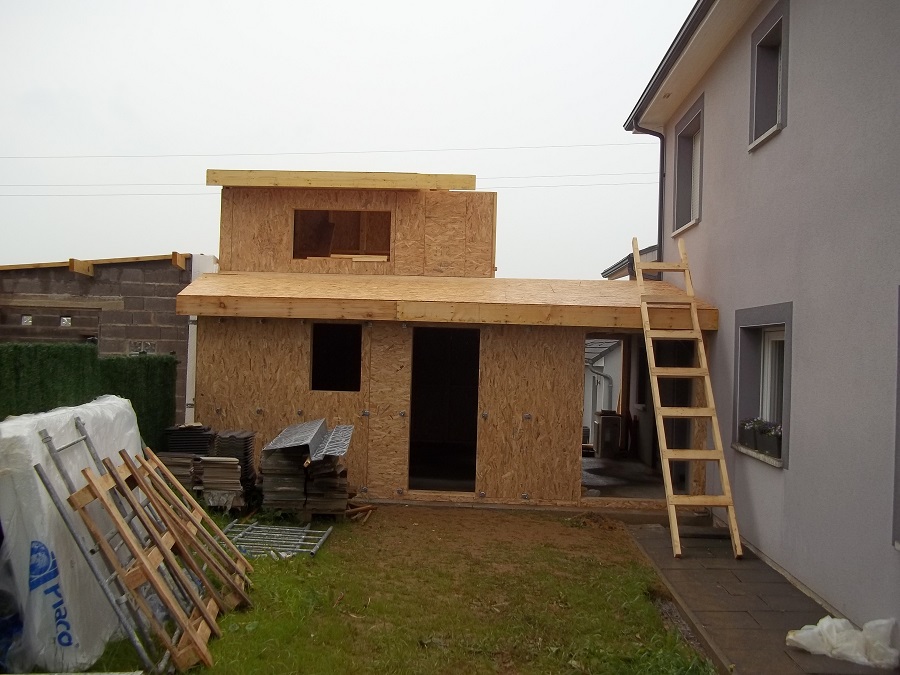
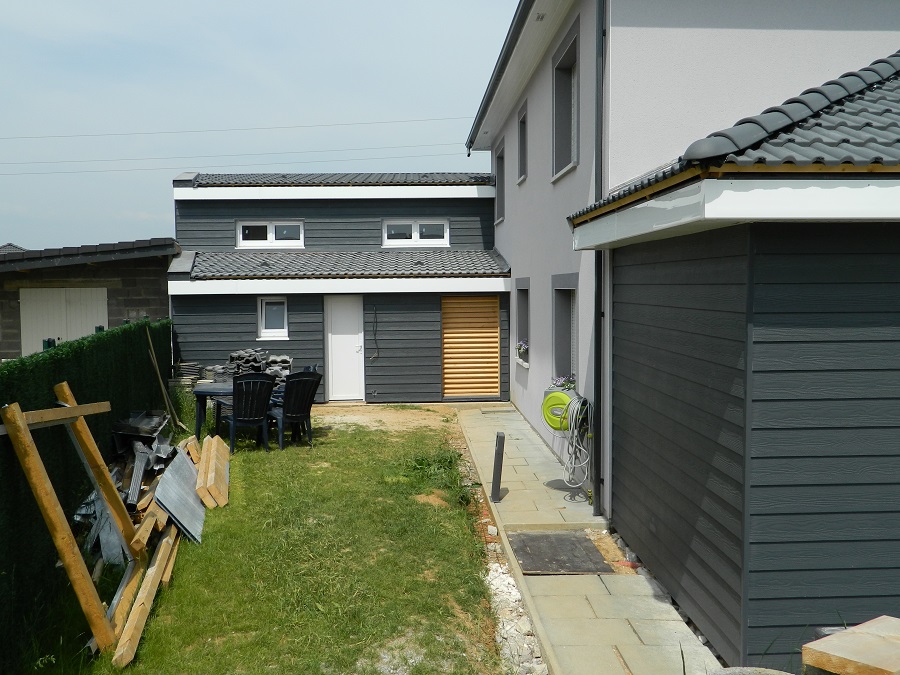
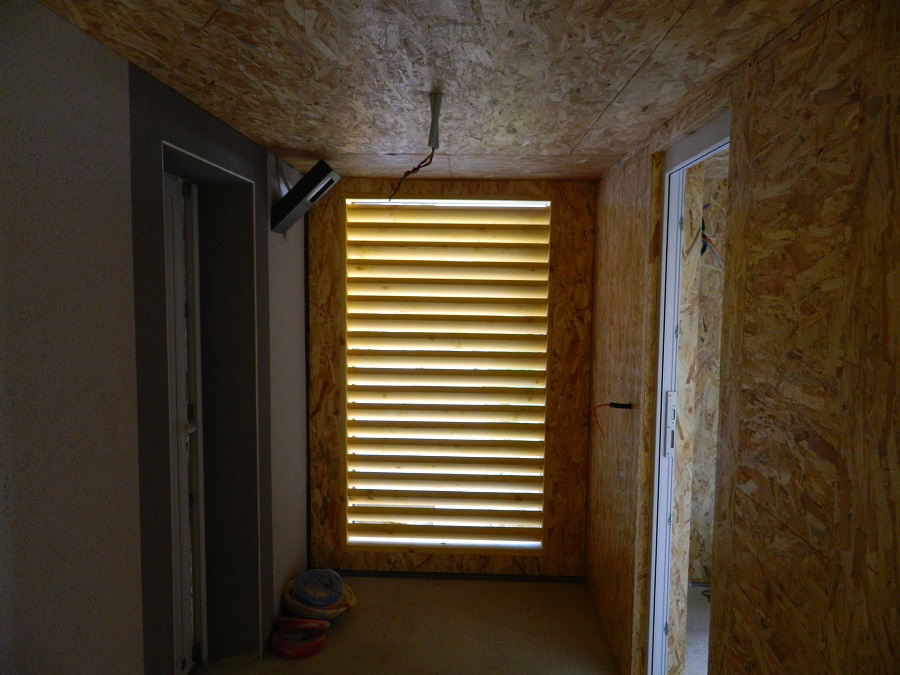
The additional advantages of an extension or attic on wooden structures would be the increased possibilities for insulation and energy efficiency
Energy efficiency in houses is an important requirement now. Reducing their energy losses is regulated in the European Community and, since the end of last year, building permits have not been granted in our country without energy efficiency calculations.
Walls in wooden structures are inherently more energy efficient. The thick layer of insulation inside the wall, the insulation fitted on the outside, all the systems for fastening the walls, windows and doors are designed to minimize energy losses. In addition to the increased comfort and substantial reduction in heating (winter) and cooling (summer) costs of these houses, good insulation also reduces acoustic discomfort.
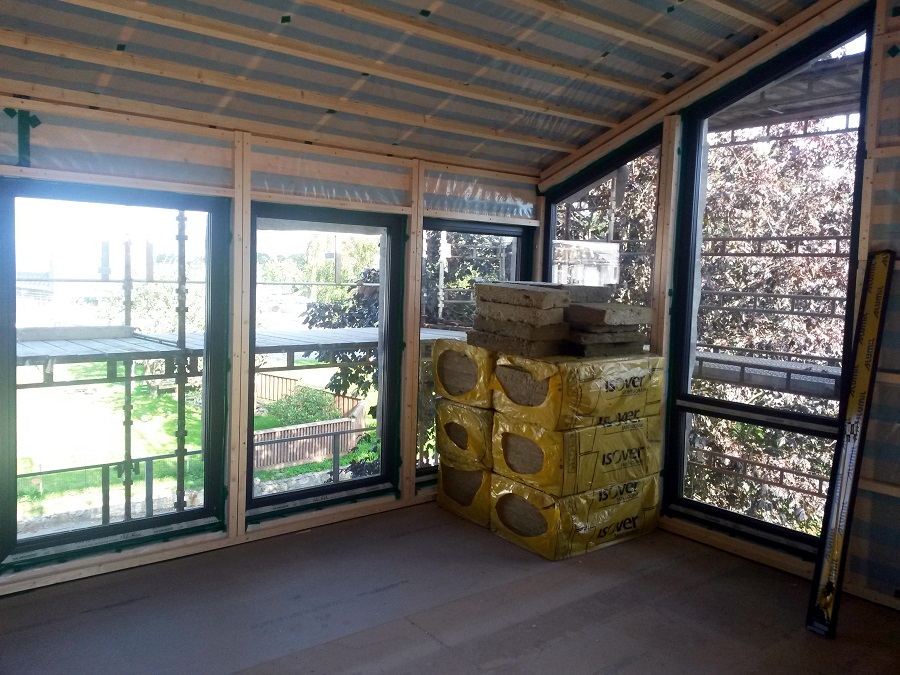
Simple combination with masonry or metal
Timber structures are very flexible and can be used to extend all types of construction. Whether it's brick, concrete or metal, the wooden structure behaves very well and can be attached or joined without any problems. Flexibility also applies to the exterior finish. A timber frame house doesn't have to look like a timber house if you don't want it to. It can be plastered and painted identically to the original house. And if you want large glazed areas, laminated beams are perfect. Their strength allows much larger openings than can be made with traditional building materials.
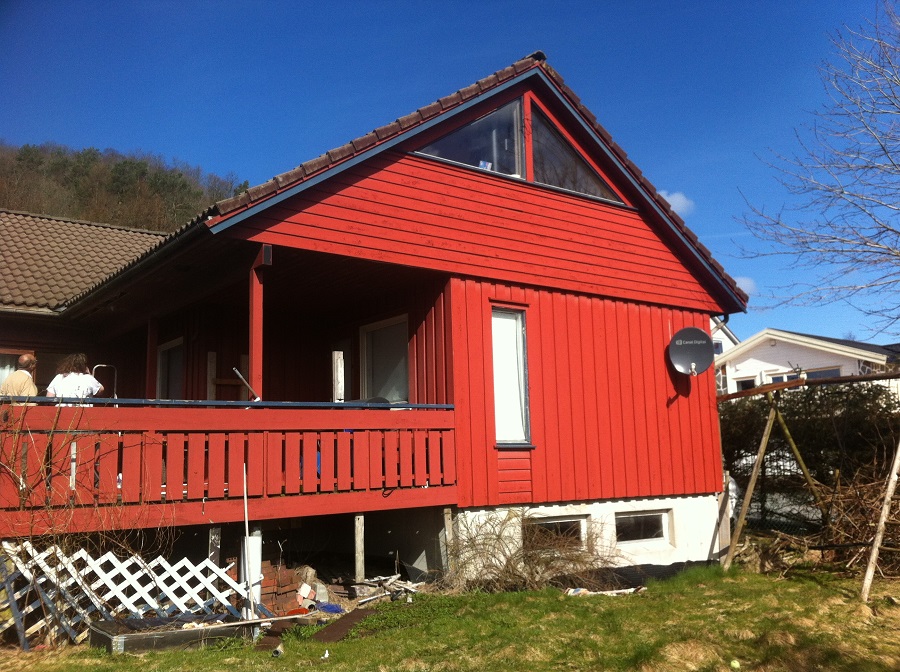
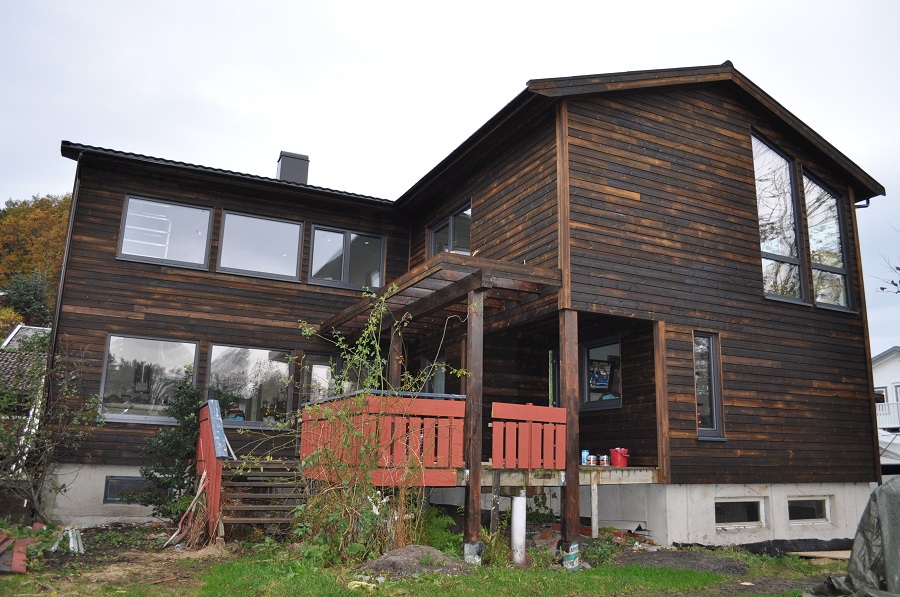
The photos in the article are from Litarh home extensions in France and Norway. They were completed years ago, and the owners are pleased with the newly added space, the short time spent on site and the liveliness of the construction. Unfortunately we don't have any final photos of the 19th century house extension. Meanwhile the COVID-19 story has intervened and work has stopped. It will be completed as soon as this period passes and work will resume. And we will of course come back with photos.
I lived for 16 years in a wooden house made on a cabinet structure with osb and plasterboard closures, with cashmere mineral wool insulation. It was a wonderful 16 years, grew children there, I recommend such houses, they are wonderful. I am longing for it, I sold it because someone paid me an unbeatable price for the area it was in.
Hello!
Thanks for the feedback. We want to present the advantages of this type of housing and the experience of someone who has lived in a house on the structure is very welcome.
All the best!
Have a nice day! We are planning to renovate our existing old house and possibly, if the structure fits, extend it with a wooden floor. Can you assess the structure of the existing house if you can build on it? If so, how much would it cost? It would probably add about 70 - 80 sq m. I am asking for a quote.