No se me ocurre nadie que no haya visto sillas, sillones, butacas, poltronas u otros muebles que, aunque tienen formas diferentes, presentan un diseño continuo de madera por todas partes. Seguramente te habrás preguntado si no se trata simplemente de un diseño impreso en papel, ya que es suelo laminadoque no tiene ni rastro de madera. Pero esta vez hablamos de madera. Se trata de contrachapado moldeado, con el que se pueden crear muebles con diseños interesantes. Las sillas de contrachapado moldeado son ligeras y cómodas, elásticas pero muy resistentes. La aparición del contrachapado moldeado marcó un antes y un después no sólo en la industria del mueble. Es un material interesante y atractivo tanto para los grandes fabricantes de muebles como para los carpinteros o diseñadores aficionados.
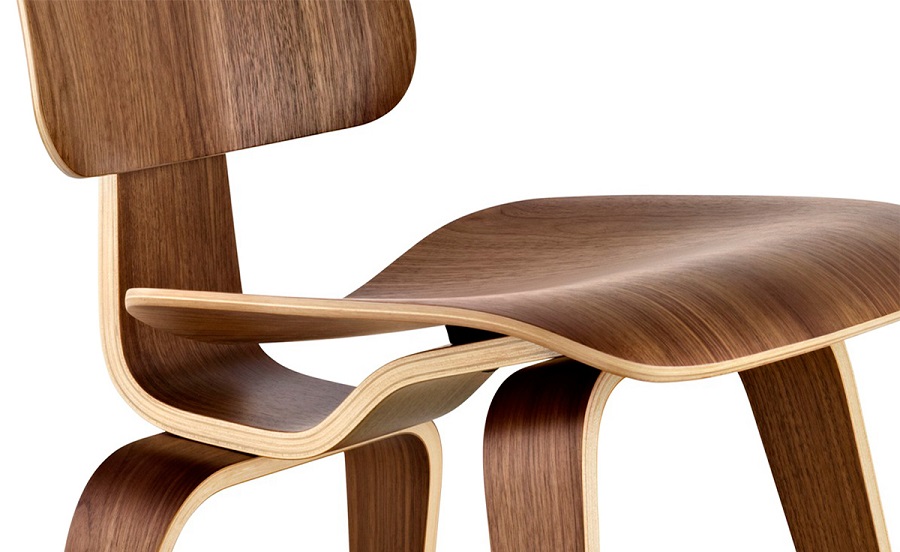
¿Qué es el contrachapado moldeado?
Ya hablé antes de la madera contrachapada cuando hice una breve historia o cuando hablamos de paneles de madera. En resumen, el contrachapado es un material que se ha utilizado durante mucho tiempo para fabricar muebles, y en los museos hay muebles con partes de contrachapado que datan de finales del siglo XVIII y principios del XIX. El contrachapado es un derivado de la madera que se fabrica superponiendo y encolando chapas. El material resultante es más estable y resistente, con una superficie generosa que puede trabajarse como la madera maciza.
Los hornos pueden colocarse perpendiculares entre sí o paralelos a lo largo de la fibra. En el primer caso, el número de chapas debe ser impar para equilibrar las tensiones. El material resultante es rígido, estable y ligero. En el segundo tipo, el número de hojas de chapa sólo es importante en términos del grosor del contrachapado resultante. También se denomina contrachapado laminado y es muy elástico y resistente. Si, tras aplicar el adhesivo y solapar las chapas a lo largo de la fibra, se realiza el secado en un molde a presión, el resultado es contrachapado moldeado.
Breve historia
Los primeros intentos de fabricar madera contrachapada moldeada fueron realizados ya en 1830 por Michael Thonet. Sin embargo, abandonó esta dirección y se concentró en curvar la madera maciza. Y así fue como - a partir de haya curvada - Silla Thonetel mueble más vendido de todos los tiempos.
En el siglo XIX había habido varios intentos -en Europa, EE.UU. y Canadá- de conseguir madera contrachapada moldeada, pero sin repercusión en la industria. A finales de la década de 1920, diseñadores y arquitectos descubrieron la versatilidad del contrachapado y trabajaron cada vez más con él. El momento importante para la entrada del contrachapado moldeado en la fabricación industrial de muebles fue 1933. Fue entonces cuando comenzó la producción en serie de la silla Paimio (más bien un sillón), creado en 1932 por el arquitecto finlandés Alvar Aalto para el sanatorio de la ciudad de Paimio. La silla pronto se exportó a Inglaterra, Alemania e incluso Estados Unidos.
Otro momento importante en la evolución del contrachapado moldeado fue la Segunda Guerra Mundial. Fue entonces cuando se fabricó Avión Mosquito con fuselaje de contrachapado moldeado, el caza más ligero y rápido de la época y el que volaba a mayor altitud. Durante la guerra el avión se fabricó en Inglaterra, Canadá y Australia.
Otros hitos en la historia de los muebles de contrachapado moldeado fueron la creación de la silla en 1952 Hormiga por el arquitecto danés Arne Jacobsen y la colección de muebles realizada en 1956 por Ray y Charles Eames para el fabricante estadounidense Herman Miller. Estos fueron los momentos que desencadenaron una oleada de producción de muebles de contrachapado moldeado en todo el mundo. Salas de espera, comedores, cantinas, restaurantes, cines empezaron a utilizarlos de forma generalizada, y así los muebles de contrachapado moldeado se convirtieron en algo habitual. Pero eso no quiere decir que no sigan existiendo piezas de diseño espectaculares y únicas.
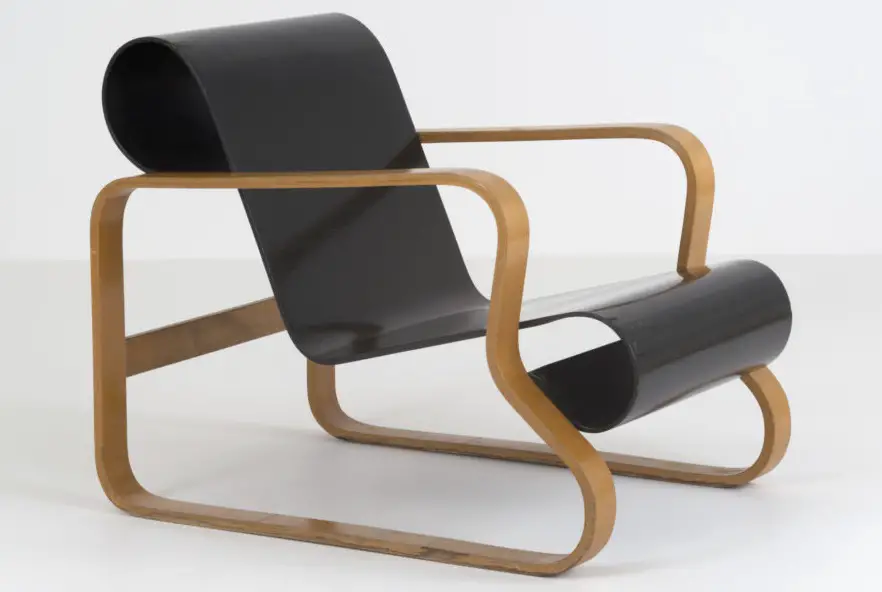
foto: alvaraalto.fi
Qué se necesita para obtener un contrachapado moldeado
Basta de historia, volvamos a la técnica 🙂 Para hacer contrachapado moldeado necesitas :
- chapa de madera
- adhesivo
- molde, plantilla
- Pulse
Horno utilizado para el contrachapado tiene un grosor de entre 0,5 y 3-5 mm. Las chapas de menos de 1 mm se denominan fUrna estética y se utilizan para las caras del contrachapado. Pueden ser diferentes en esencia de los demás, por lo que se puede obtener contrachapado de cal o de plop con las caras de nuc o cereza. El contrachapado será ligero y tendrá un diseño muy bonito. Las chapas más gruesas se llaman mobiliario técnico.
Asignación adhesivo debe estar relacionado con la tecnología de trabajo. Ciertos tipos de adhesivo se utilizan para la unión en frío (PVA), para el procesado en caliente, otros tipos (ureoformaldehídico, resorcínico, fenolformaldehídico). El tratamiento en caliente también puede tener de formaldehído libre.
El molde es lo que dará al contrachapado moldeado su forma final. Normalmente, en el curado térmico, el molde forma parte del Pulse. Es del tipo madre-padre, es decir, hay un molde en el que se coloca el paquete de chapa y sobre el que viene el "negativo" del molde inicial que se prensa y calienta al mismo tiempo. También es posible obtener los moldes en prensas de vacío, en este caso no necesitamos un "negativo" del molde. Independientemente de cómo se fije el molde, se pueden obtener modelos 2D o 3D, dependiendo de lo elaborado que esté el molde.
La modelización también puede realizarse con un plantilla de diversos materiales, incluida la madera contrachapada moldeada. Las chapas sobre las que se ha aplicado la cola se modelan siguiendo esta plantilla y se sujetan con pinzas para crear la presión necesaria para una buena unión. Hay que trabajar con rapidez para sujetarlas a la plantilla antes de que la cola empiece a secarse. Es una buena idea comprobar de antemano cómo se hará la sujeción utilizando el paquete de chapas sin adhesivo aplicado.
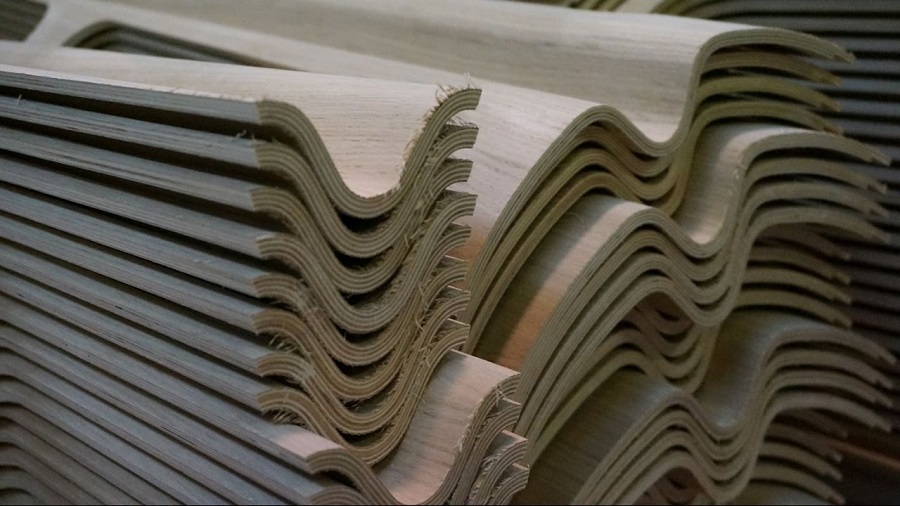
foto: youtube.com
Técnicas de fabricación
La forma en que se fabrica el contrachapado moldeado depende de si el adhesivo cura en frío o en caliente.
Salir adelante prensa en frío se utiliza para hacer piezas únicas o para proyectos de diseño o bricolaje. Como ya se ha dicho, se utilizan plantillas normalmente cortadas de madera contrachapada o plástico. Se coloca una tira o lámina de acero flexible entre la plantilla y el haz de láminas de chapa de madera que se va a prensar. Durante la sujeción, el exceso de cola saldrá y la madera contrachapada puede pegarse a la plantilla, a menos que haya una barra antiadherente. Es una buena práctica aplicar el adhesivo sobrante para asegurarse de que las chapas se adhieren en todo el perímetro. Deben utilizarse muchas pinzas, sujetadas con frecuencia, para que la presión sea lo más uniforme posible (por eso las abrazaderas nunca son suficientes 🙂).
La ventaja es una mayor flexibilidad. La desventaja es el largo tiempo de prensado, que a veces lleva hasta 24 horas para que el contrachapado adopte la forma deseada.
Pulse caliente Puede realizarse en prensas con calentamiento normal o en prensas CIF, es decir, utilizando corrientes de alta frecuencia. La ventaja del segundo método es el tiempo de trabajo muy corto, ya que la madera contrachapada tarda entre 1,5 y 2 minutos en salir de la prensa lista para ser moldeada. El prensado en caliente se utiliza principalmente en la industria, donde se requiere un tiempo de curado corto y una reproducción idéntica del patrón.
El endurecimiento CIF se utiliza ampliamente en todo el mundo y se debe a que el calor se distribuye uniformemente dentro de la capa adhesiva. El contrachapado resultante es más homogéneo, con propiedades uniformes en toda la superficie. Las corrientes de alta frecuencia son suministradas por un generador acoplado a la prensa. El generador también puede funcionar con 2 o más prensas.
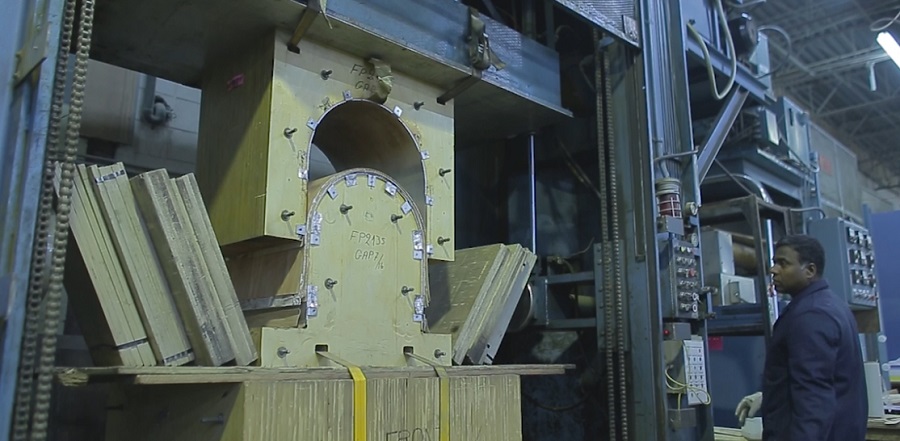
Propiedades, procesamiento
Tras su fabricación, el contrachapado moldeado puede procesarse como cualquier otro tipo de contrachapado o derivado de la madera. Inmediatamente después del prensado, se recortan los bordes para eliminar las fugas de cola endurecida o las partes sueltas. De este modo se obtienen bordes limpios en los que son visibles las capas de madera y adhesivo. A veces, la capa adhesiva de color diferente (tonos marrones) da un aspecto muy bonito e interesante.
A continuación, el contrachapado moldeado puede cortarse en elementos más estrechos que representarán las patas o los brazos de sillas y sillones, o mecanizarse en diversas máquinas tradicionales para trabajar la madera o en CNCs.
La fijación entre elementos moldeados puede realizarse con tacos, clavos, tornillos o pegamento. La fijación a andamios metálicos puede hacerse con tornillos. A pesar de su elasticidad, el contrachapado es un material duro y resistente que puede procesarse sin problemas.
La calidad final del contrachapado depende de la calidad de las chapas utilizadas. Las chapas sin defectos, roturas o desgarros de fibras darán como resultado un contrachapado de muy alta calidad. Tras el procesado y la unión, el objeto de contrachapado moldeado puede lijarse y acabarse del mismo modo que los muebles chapados.
Espero que la información le resulte interesante. Si cree que puede ser útil para otras personas, no dude en compartirla. Si tiene alguna pregunta, comentario o comentario que añadir, por favor, déjelo a continuación en el espacio previsto para ello.
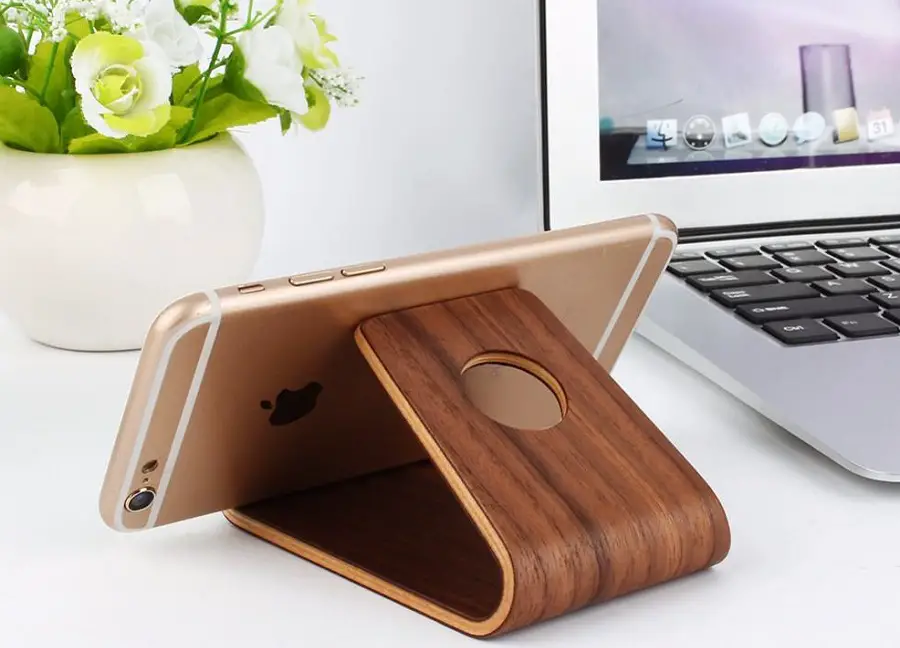
Hola
Gracias por un artículo tan bueno, informado y útil.
El contrachapado está recuperando su lugar y su aprecio en la industria de fabricación de muebles en Rumanía y fuera de ella.
Me interesan mucho los detalles de los adhesivos utilizados en la industria por los fabricantes de tableros de madera.
Gracias de antemano si me pueden recomendar algunas fuentes de información sobre este tema.
¡Buena suerte para el futuro!
Hola.
Gracias por su apreciación.
De hecho, el contrachapado ya no es sólo ese material que se utiliza como soporte de muebles.
Por desgracia, en el campo de los adhesivos hay poca información en los sitios web rumanos. Hemos escrito algo sobre adhesivos, pero más sobre los de tipo "aracet" o para actividades de bricolaje. Sobre los industriales tocamos ligeramente el tema en el artículo sobre la amina formaldehído. Tengo intención de escribir pronto un artículo sobre los adhesivos industriales.
Le deseo lo mejor.
Esta información es muy importante,
Muchas gracias a los promotores