It is not always possible to make furniture from a single piece of solid wood. Especially if the furniture is larger. The solution can come in the form of panels made from joined solid wood, called solid wood carpet. These are narrow strips of wood that are jointed both lengthwise and widthwise.
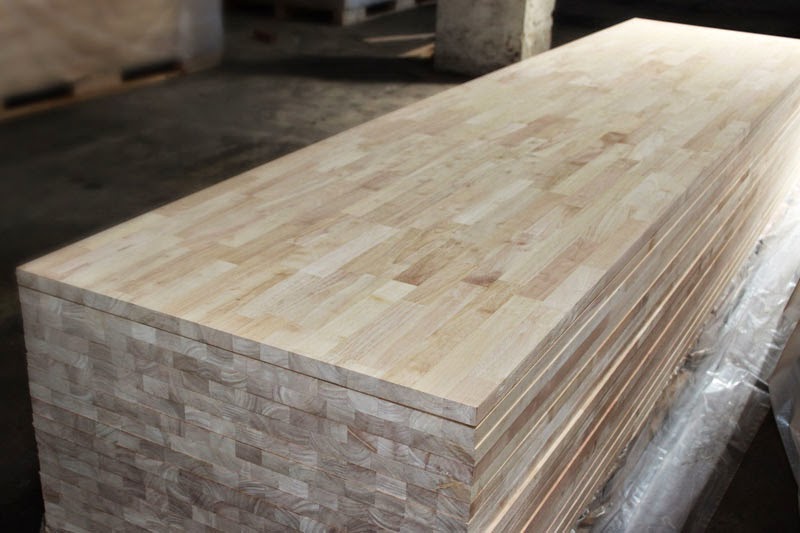
How solid wood panels are made
To lengthen solid wood elements, either finger-jointing or straight-jointing can be used. The elements are prepared at the ends, glued, usually with cold glue, and held in presses. In the case of width splicing, the elements to which the adhesive has been applied are placed side by side and then placed in a cold press until the adhesive sets. After being removed from the press, the panels are sanded to remove excess adhesive and to be calibrated.
These finger-jointed solid wood panels are a type of solid wood widely used in industry. Due to the joining of several pieces of wood that may behave differently, some problems may occur during finishing. In the following you will find some tips for a flawless finish.
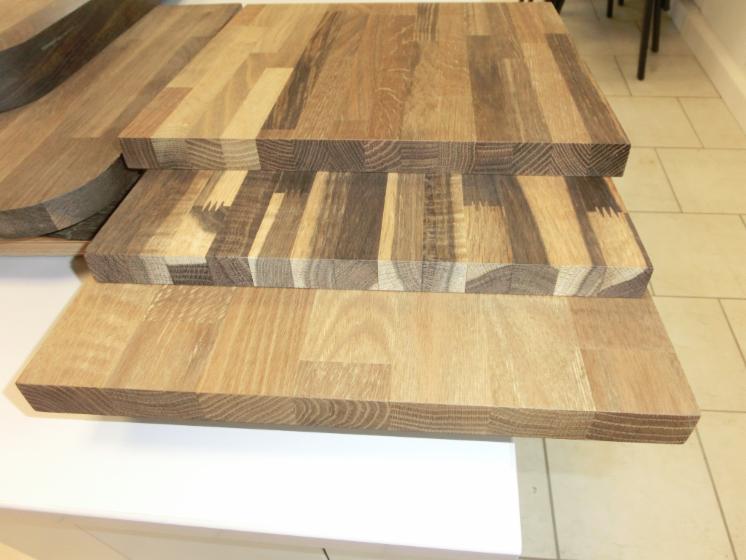
Staining of solid wood panels
The colouring Stains may appear on the carpet due to different absorption. The pieces of timber come from different logs and have different densities. During staining, the wood is absorbed differently resulting in uneven staining. Absorption of the wood also highlights the joints in the teeth.
To reduce uptake, quick solvent-based baths can be used, which evaporate quickly and the bath does not go deep into the wood. It is a handy method, but increasingly difficult to use because of environmental requirements related to the emission of volatile organic compounds (VOCs).
To eliminate the problem of VOCs, you can use water-based waterborne paint sprays. It is known, however, that waterborne balsams absorb deeply, emphasizing the wood's design. In the case of a solid carpet that absorbs differently is not the best option. That is why it is better to dilute the stains with a mixture of water and a special resin that reduces the absorption, thus obtaining a uniform color.
Also for a uniform appearance, coloring can be done with colored primer, with the recommendation to control very well the amount of colorant in the primer and the thickness of the applied layer so that the finish does not have a plastic look.
Another disadvantage of using solid wood panels is the discontinuity of the design. Whereas solid wood is stained in such a way as to bring out the natural pattern of the wood, panels are usually stained in a discreet, uniform, uniform coloration.
If the coloring solution is not compatible with the glue used for gluing, a fine white line appears along the joint. The defect is not very common because the adhesives commonly used for gluing are compatible with most coloring solutions. For rare cases where there is no compatibility it is recommended to use an insulator before staining the panel.
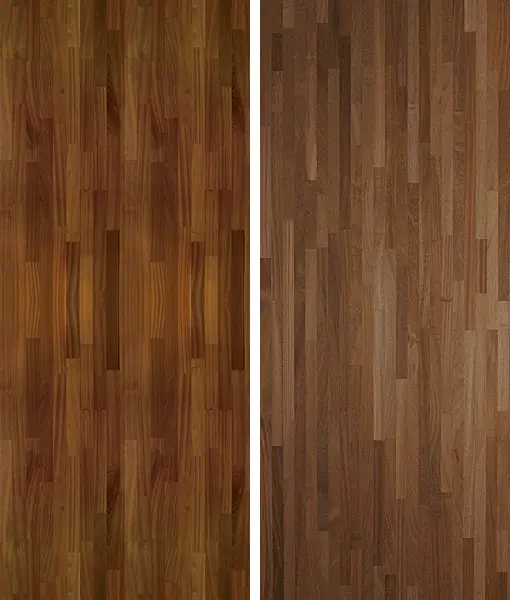
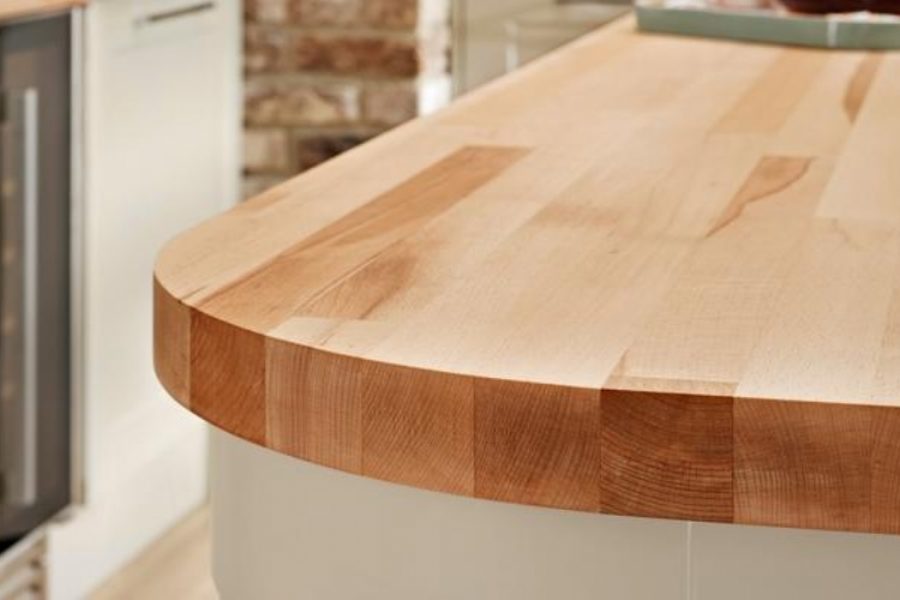
Defects that can occur after varnishing
Fine holes may appear along the solder lines following the application of the film-forming materials. The defect resembles the pore-filling of the finish and occurs due to the small amount of adhesive applied. In order to avoid holes, the adhesive is applied in excess. When the solid elements are squeezed in the press to form the panel the excess has to come out. This excess is removed by sanding.
If the defect nevertheless appears, the panels should be puttied with a putty compatible with the coloring solution and the primer to be applied before finishing. If, however, fine holes have been observed at the end of the finishing, try to repair them by using putties of the same color as the panels. This solution is valid for very small defects, otherwise the putty will make the situation worse.
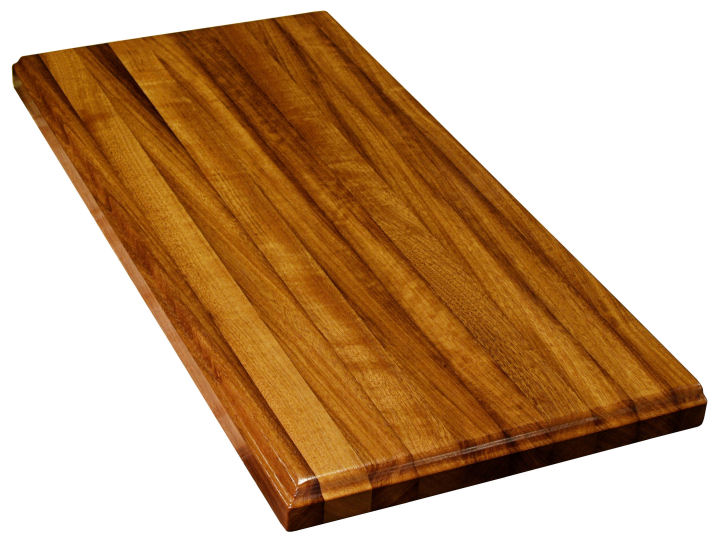
Solid wood panels are a great solution for solid wood furniture. They are stable, easy to work, and if a few rules are followed the finish can be very successful.
What solutions do you recommend for finishing a solid wood panel used as a kitchen worktop. We do not recommend solid wood for this part, but it is insisted on and there are many requests. I am not aware of a viable solution, which in the medium term - 2-3 years will not show warping in real used kitchens. I'm not talking about museum kitchens, where no cooking is done, but those with sinks and stoves or ovens used daily, frequently.
I understand it's about the wooden table top in a functional kitchen. In this case you should use a harder polyurethane varnish with high scratch resistance (like parquet varnish). Even so, customers should know that they cannot cut directly with a knife on the worktop without leaving marks. Lacquer applied with a spray gun, without special technology, has its limits. You could get a very high resistance if you applied a UV hardening varnish, but for it you need UV line. My recommendation is to use polyurethane varnish with catalyst 100% but to inform your customers how to use the top (no direct cuts). The varnish resists without problems also to humidity in a working kitchen and to hot liquids (hot pots). As the wood used is oak (so I suspect 🙂 ) the worktop will have a good resistance over time. I hope I understood your question correctly. Good luck!