An adhesive that ensures a very moisture-resistant bond of wooden elements is very necessary because high humidity can be both indoors and outdoors. Pieces of furniture in bathrooms or kitchens, anything that involves wood furnishings in these areas, need to withstand higher humidity than in other rooms. Likewise doors, windows or garden furniture need the elements to stay stuck together even if they are battered by rain. An adhesive with such strength is a D4 adhesive. It falls into this category because of its qualities. I intend to tell you more about this type of adhesive below.
What is a D4 adhesive and how is it different from a D3 adhesive
I was telling you recently about a improved D3 adhesive for use in winter conditions. The area code D3 means, according to European standard DIN EN 204, that it can be used for interior construction with short-term exposure to damp or damp environments, for exterior construction in mild climates, for jointing steps, doors or windows installed in weather-protected areas.
Unlike D3, D4 adhesive is used for joints that need much higher moisture resistance. It can be used both indoors (bathroom, kitchen) and outdoors (garden furniture). It is a very suitable adhesive for solid wood panels, laminated wood, exterior windows and doors. One such adhesive is Tiszabond 1kD4-D cod 4133 of the Szolvegy Târgu Mureș.
Main features of Tiszabond 1kD4-D 4133 adhesive
The adhesive is a single-component, aqueous dispersion of polyvinyl acetate (aracite). It has improved grip on the substrate, which results in a much higher bonding quality.
The film formed after curing is transparent and highly elastic which is a big advantage for manufacturers of composite panels. What is this advantage? Apart from the fact that the adhesive film is not visible at the joints, it substantially increases the average tooling (planer) uptime, of the machines).
The hard films formed when using inelastic adhesives attack tools and shorten their life. When the film is elastic the hardness is lower and the tools suffer less. The elasticity of the Tiszabond adhesive film is due to the fact that the adhesive does not contain fillers (generally chalk).
But the main feature is moisture resistance. The formed adhesive film has a very good water resistance and is, according to DIN EN 204, a D4 adhesive. The moisture resistance is comparable to that of a D4 adhesive with hardener. Despite being one-component it hardens after a short pressing time, resulting in a solid, firm bond.
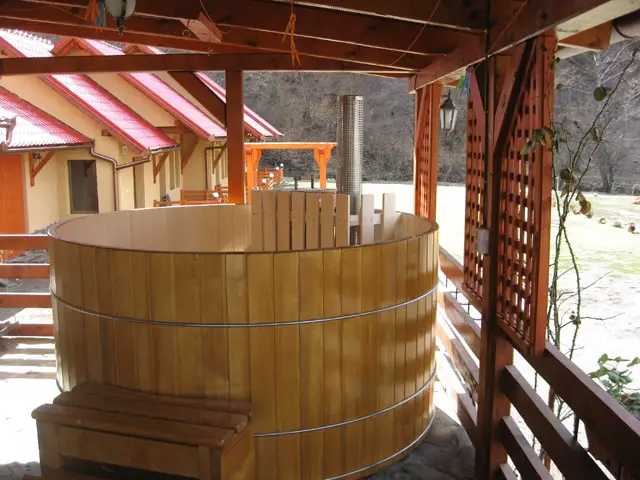
Where Tiszabond 1kD4-D 4133 adhesive can be used and where not
⊕ The adhesive can and should be used for gluing wood elements used indoors in environments with very high humidity (bathrooms, kitchens). Rising temperatures in these areas amplify the effects of humidity.
⊕ It is very suitable for gluing wood panelling, wooden steps or laminate flooring.
⊕ It is recommended for making solid wood panels and for bonding veneer to wood or chipboard panels.
⊕ Being resistant to external conditions, it can be used for gluing laminated wood to make windows, wooden door panels for exterior use. It is also recommended for gluing garden furniture.
⊗ But there is one area where polyvinylacetate-based adhesives are not recommended. These are obtaining the supporting beams. Builders need to differentiate support beams from other beams, and manufacturers MUST NOT use aracite-type adhesives in their manufacture. Szolvegy recommends one-component D4 (1kD4 PU) polyurethane adhesives certified for this purpose.
What you need to know when using this adhesive
I used to say that any product, no matter how good it is, never works wonders. That's why, to have a perfect moisture-resistant bond, several parameters must be taken into account:
- surfaces to be soldered must be smooth and free from impurities or greasy substances;
- ambient, adhesive and wood temperature not be less than 10°C
- relative air humidity must be 60-70% at an ambient temperature of 20-22°C or 45-55% at 23-25°C
- wood moisture shall be 8-10% when the interlocking elements are used indoors and 11-15% for elements used outdoors;
- quantity applied depends on the absorption capacity of the wood and should be between 120 and 180 g/m².
The variation of these parameters influences the reaction times of the adhesive.
As far as pressing is concerned, increasing the temperature speeds up the curing process of the adhesive. For example, gluing hardwood elements (oak, ash) takes 17 min. at 20°C, but decreases to 9 min. at 50°C, and to 6 min. at 70°C.
Tests with very good results, even better than expected, have convinced manufacturers that they are on the right track
At Szolvegy we want to build long-lasting partnerships with our customers. That's why they are always concerned to offer not only the best service (permanent stock, regular transportation with heated machines, technical support) but also the best products. That's why they usually test products before putting them on the market in conditions much tougher than the standards require.
I told you a while ago that a one-component adhesive with similar properties to the two-component, was boil-tested for 8 hours instead of 2. In the case of 1kD4-D 4133 they pushed the boundaries again. They fabricated, by finger-jointing and laminating, a 4 m long beam with a 40×30 cm cross-section, which was heat treated (boiled) in an autoclave 3 days after bonding instead of the recommended 7 days. It was then left outdoors for 2 years. The beam held up very well, which was a surprise even to the poducers.
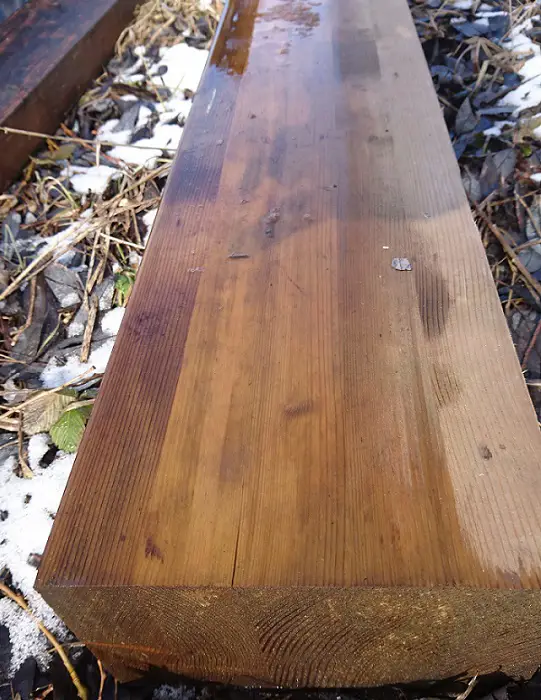
I forgot to tell you a very important advantage. The adhesive is also available in small packages of 10, 5 and even 0.750 kg. This does not mean that if you need 32 kg, 130 kg or even 1100 kg, you can't find it. You just have to decide.
Add comment