Adhesives are very important auxiliary materials in the wood industry. Unlike varnishes and paints, which are visible and their presentation can be done through spectacular examples, the qualities of adhesives are revealed when it comes to the durability of furniture and other wooden/wood-derived objects. This is why I think that information about adhesives, their characteristics, how to choose them according to the environment where the glued object is to be used, is important.
Adhesives are natural or synthetic materials that create strong bonds between two pieces of the same or different materials. In the past, natural adhesives of animal or vegetable origin were used. I'm sure many people remember the bone glue that was made at Mărășești. I still remember the mountains of bones (and the smell) that I "admired" for 30 minutes while the train from Iași stopped at Mărășești station to change the locomotive. Bone glue is not the only natural glue. Fish glue, casein glue, animal blood glue and starch-based glues are just a few examples.
In wood, adhesives have various uses. They are used in:
- production of wood-based panels
- gluing of furniture components
- veneering of panels
- production of solid wood panels and laminated wood
Synthetic adhesives are used in all these areas, natural adhesives having long since been abandoned because of their inability to keep up with industrial requirements.
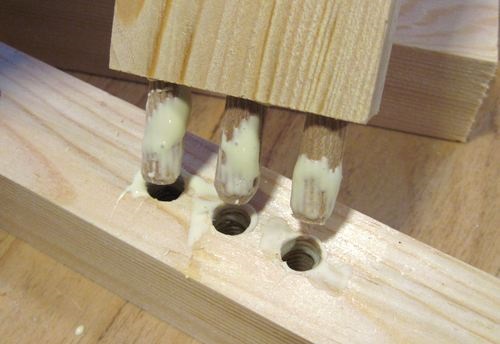
There are various types of adhesives used for wood, the most important being ureo-formaldehyde (urelite), vinyl (polyvinyl acetate PVA), polyurethane, epoxy or chloroprene. No matter what the glue is, the most important thing is the strength of the joint. This is determined by laboratory tests, and a good joint is one that does not split at the joint line but in the bonded material (the wood cracks).
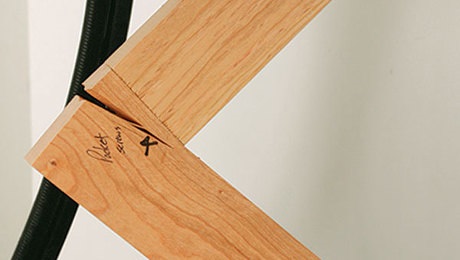
Adhesives are used to join all kinds of objects together, hence their characteristics. These objects can be used indoors or outdoors, they can be subjected to different forces, they can be finished objects or objects to be processed. The choice of adhesive must be made according to these uses. But even within each category there are classifications. One of the most important is the resistance of adhesives to water and moisture, which is very important for wooden objects used outdoors or in environments with high humidity. From this point of view, adhesives are divided into 4 classes:
- D1 - for the jointing of softwoods used indoors in environments not exposed to moisture;
- D2 - for the joining of wood of any type used indoors in environments not exposed to moisture;
- D3 - for interior construction exposed to damp or humid environments, but short term, for exterior construction in mild climates. It is the adhesive used for joining steps, doors or windows in protected areas.
- D4 - for joints requiring increased moisture resistance. It is used for indoor joints in areas exposed to moisture (bathroom, kitchen) or outdoor joints in exposed areas (garden furniture). It is a very suitable adhesive for solid wood panels, laminated wood, doors and windows. [Details of a D4 adhesive]
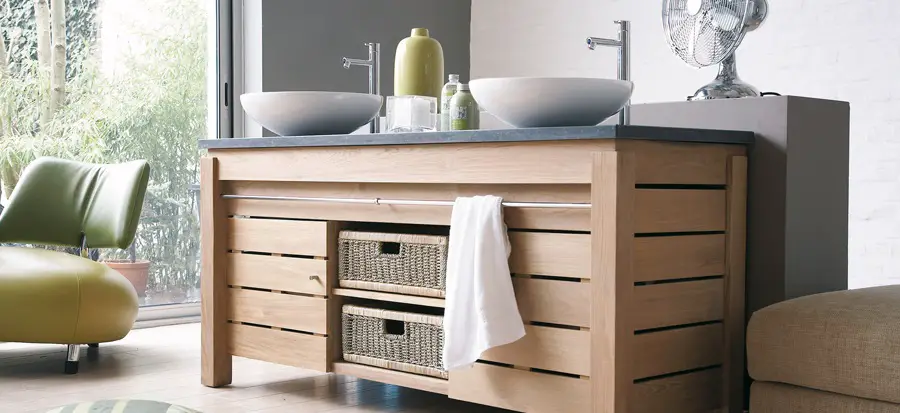
As I said, the strength of these joints can be tested. There is laboratory equipment that subjects the joint to forces until the object fails. Tensile strength is measured in N/mmp and there is a minimum value for each class of adhesives, as required by international standards. When testing the strength of the adhesive in wet conditions, the joint is kept in water for hours or even days before testing. The immersion time, strength level and test method are standardised.
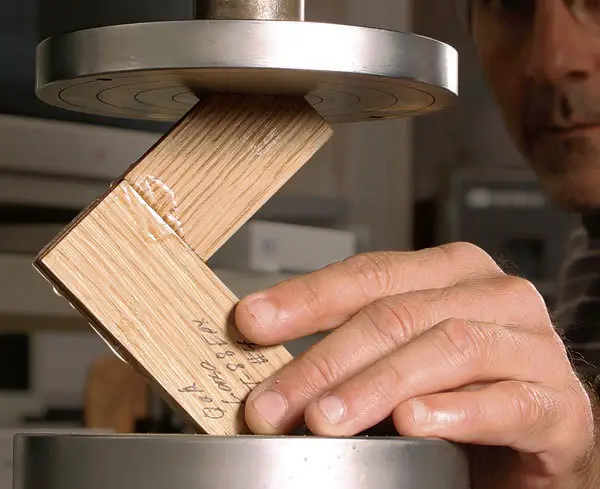
Often, in order to find out the strength of joints, those interested do empirical but very conclusive tests. It is similar to coin tests to see adhesion of the varnish to the substrate. I was talking at one point with Mr Matefy Csaba from Szolvegy, the distributor of Tiszabond adhesives, on how he tested an adhesive. It all started from a discussion about the situation in the wood industry and how they always have to find solutions to help producers keep their prices in line. Wanting to help a partner, he thought of replacing the one-component adhesive he used with a two-component one that was used in the past and was cheaper. But he needed some joint strength, so Mr Csaba glued two pieces of wood together, took the board home and fired it up. He should have tested it after 3 hours in the water, but to be sure he left it boiling for 8 hours. The joint held, it didn't come apart, so he exchanged the product to his partner with a peace of mind.
The quality of the solder is not only about its resistance in different environments. There are many other requirements to be met, related to elasticity, transparency, sandability, formaldehyde emission or VOC. But you can find all this in other articles.

Add comment