Yosegi-zaiku is a way of making wood-like designs intarsia. The difference lies in the technique and specificity of the drawings, which are geometric. The method is specific to the city of Hakone, less than 100 km from Japan's capital, Tokyo, and is almost unheard of in other parts of Japan. As I have always been impressed by traditional Japanese carpentry, this way of getting aesthetic veneers with incredible designs caught my attention.
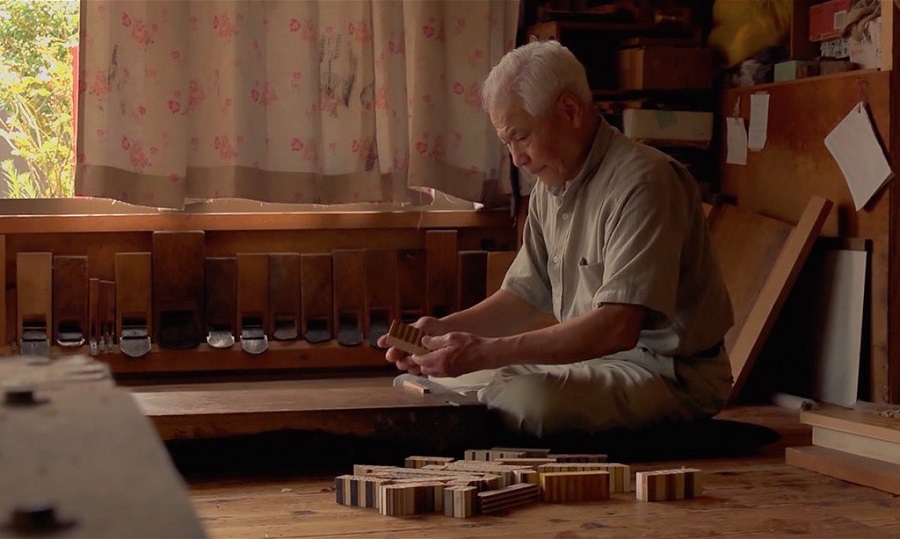
When and how Yosegi-zaiku appeared
Yosegi-zaiku is not as old a tradition as Kumiko or Sasano Boribut it's just as spectacular. It originated in the late Edo period, around 1850. Its inventor was a carpenter - Ishikawa Nikei - from the village of Hatajuku near Hakone. It was he who first made the decorative veneers from small pieces of wood, which are still popular today. In 1984 the Japanese Ministry of Industry and Trade declared Yosegi-zaiku a traditional national craft.
Hakone is a mountainous, heavily forested area, renowned for its diversity of wood species. These species are different both in structure and design and, above all, in color. It is this great variety of colors that made this Yosegi-zaiku possible.
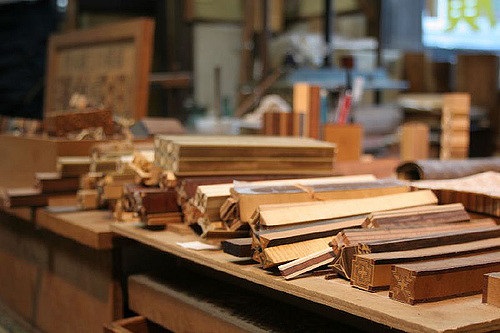
What this exotic name means
The name of the craft says exactly what it stands for:
- yose = to gather, to put together;
- gi = wood;
- zai = small, sensitive;
- ku = work
Loosely translated, Yosegi-zaiku is the art of putting small pieces of wood together to make delicate patterns.
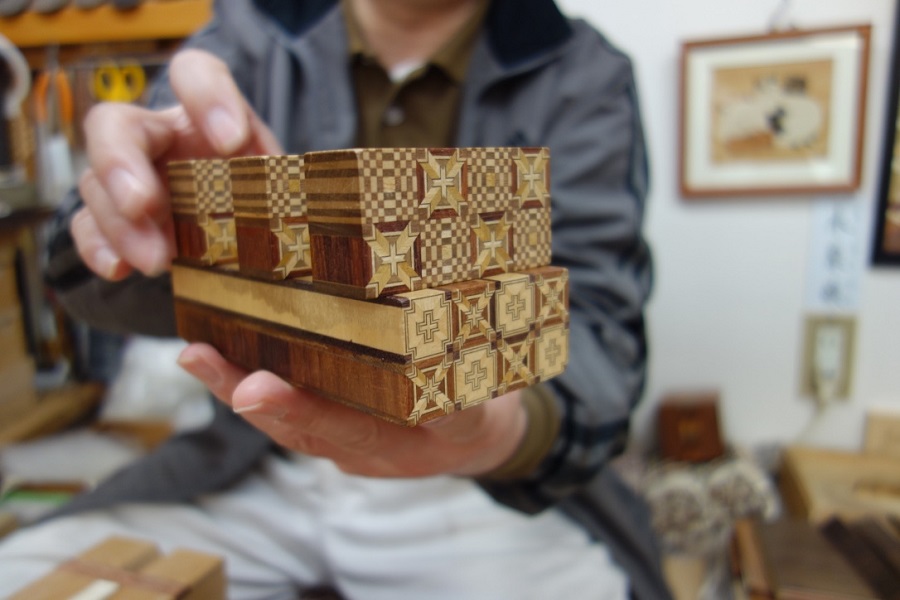
How to make veneers
First wood of different species is chosen according to color and texture. It is chosen frasin for white, cherry for light brown, Japanese magnolia for dark brown and many other species found in the area that each comes in its own specific color.
Each piece of wood is then cut and processed, resulting in very fine wooden rods of different colors. These are glued together in the shape of a hexagon, cylinder or parallelepiped, so that in cross-section they form a geometric pattern from the interplay of colors. No baiquet or other coloring is used. The pattern results, as in classical inlay, from the difference in color between the various species of wood.
After the glue has hardened, the hexagons (or other shapes) are cut into smaller pieces which are glued together to form a larger piece with a geometric pattern - Tanegi. Such small wooden panels are made with the same geometric pattern or, using pieces of several kinds of "tubes", with different patterns. At the end, very thin veneers - Duku - are cut out with a very sharp-bladed planer. The resulting veneer is smoothed with an iron and then glued to various objects.
It's a laborious process and from the time the wood is cut to the veneer can take days, maybe even weeks.
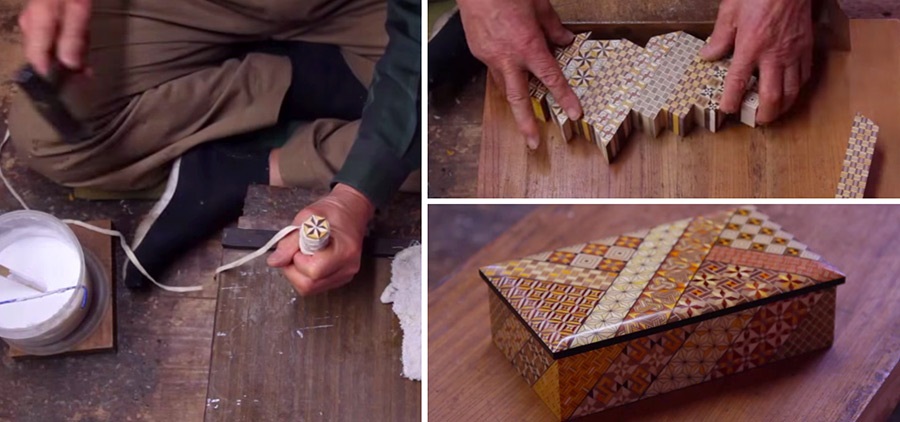
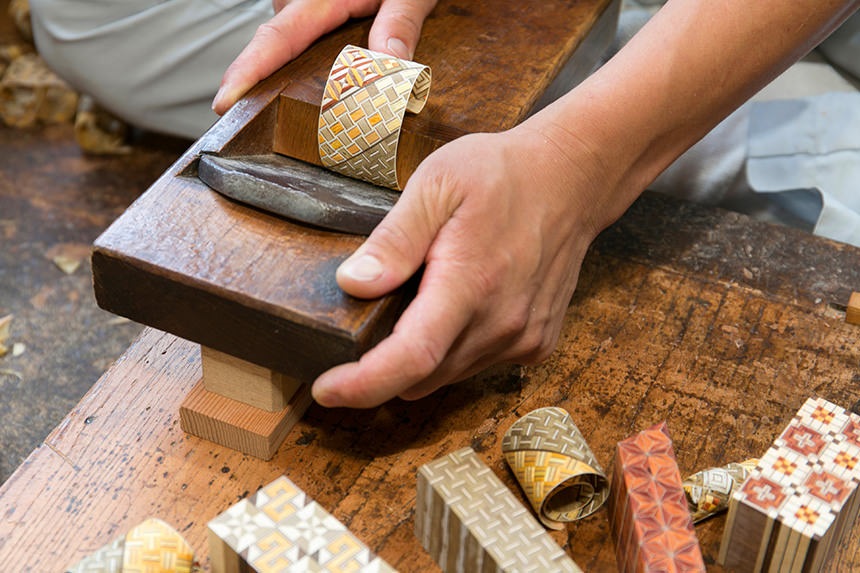
What veneers are used for
The veneers are glued onto boxes, vases, door or drawer fronts of furniture, decorative objects. After the glue is applied and the veneers are placed on the object, the surface is carefully smoothed with a flat piece of wood to remove any air or excess glue, so that everything comes out perfect in the end. All the operations, from cutting the thin wooden rods to gluing the veneer, are done by hand.
Traditionally there are 60 basic models, but the myriad colors of local wood species make the number unlimited. The basic patterns each have a specific name and there are clear indications on the wood to be used.
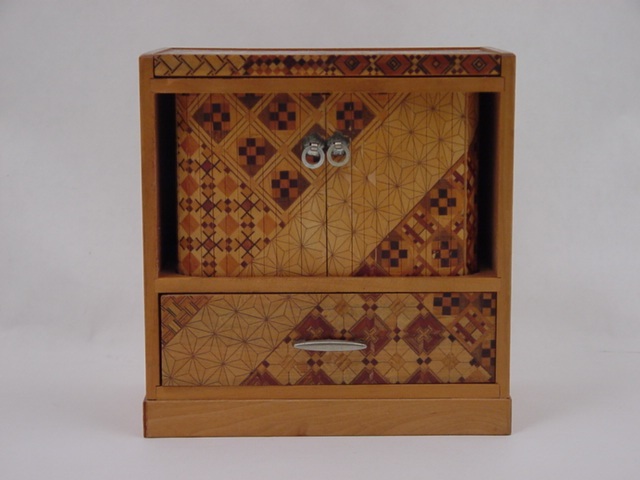
The new wave of masters. Yosegi-zaiku in the 21st century
There was a time when interest in the craft waned. Those interested in learning were fewer and fewer, and true masters remained fewer and fewer. Interest was revived with the state's involvement in preserving traditions.
The revival of the art has given rise to a new generation of craftsmen, called Zoukubayashi, who have brought the craft back into the 21st century. They make mouse pads, cell phone covers, car key fobs and car key fobs out of the wood. But everything stays in the Hakone area, where the tradition was born and developed.
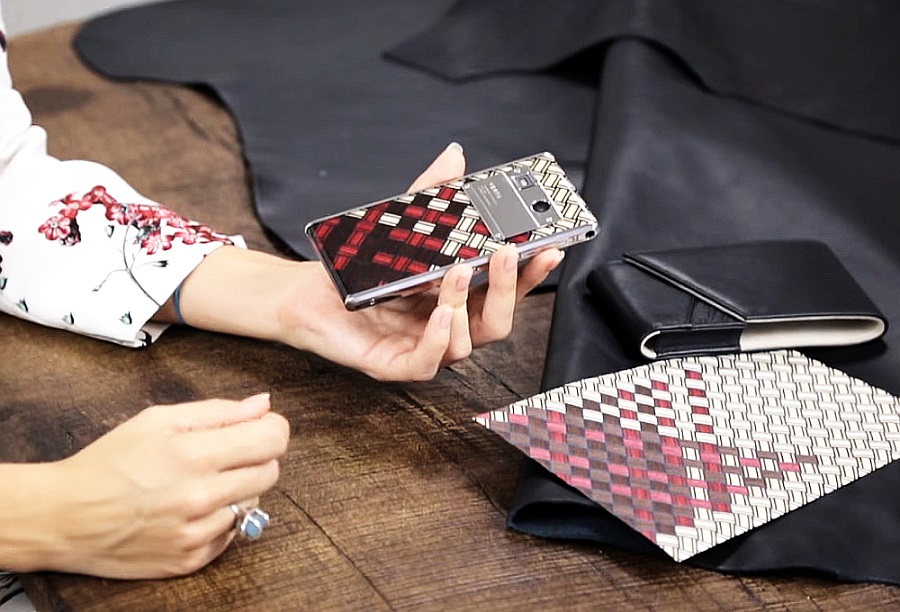
Because, no matter how well I explain how they work, it is impossible to realize the finesse with which these craftsmen work to create these wonderful veneers, I invite you to watch the video below. Who knows, you may find inspiration for your future projects.
Add comment