Much solid wood furniture is made from solid wood panels. There are factories that make such panels for both the domestic and export markets. It's a big help for manufacturers because they no longer have to make the panels themselves, concentrating on the execution of the designs. As I said a while ago, solid wood panels are solid wood, despite the fact that many consider them to be a by-product made from glued scrap. On the contrary, the use of panels comes with a number of advantages which I'll point out in a moment. A very important material for a quality panel is glue. In general, solid wood panels are made using PVA adhesives, those adhesives that we call "aracet type". Depending on their type, panels can have different qualities, for example they can be used for indoor or outdoor furniture. Not every "aracite" can be used, so I think an article on the qualities of PVA adhesives used to make solid wood panels would be welcome.
Why massive panels
Back to solid wood panels to show some of the advantages of using them in furniture production.
Panels at much larger sizes than one-piece elements. You can't think of a one-piece tabletop unless it comes from a very old, very large tree. Normally the top is made of several planks joined together, glued together. The solid board makes it possible to make the top (or other large pieces) directly, without any intermediate operations.
In the production process of the solid wood panel areas with defects or knots are removed so the risk of cracks, unwanted natural discoloration or other problems caused by wood defects is eliminated.
The panel has a very good stability. Cutting into smaller elements removes the stresses specific to solid wood and thus eliminates the risk of cracking or warping of the panel.
Solid wood panels have no formaldehyde emissions because they are made with PVA adhesives that do not contain formaldehyde in any form (free or bound).
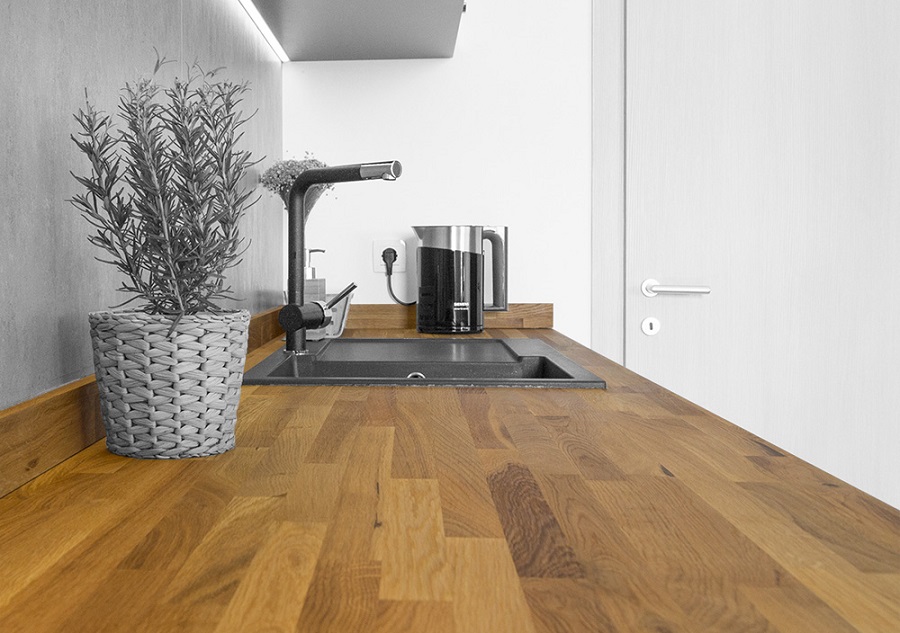
Characteristics of adhesives used in the manufacture of solid wood panels
For a DIY project the choice of adhesive is simple. The most important demands are to bond quickly and well. In production, however, the choice is more nuanced. In addition to sticking well, the adhesive must be resistant under certain conditions, be more or less elastic, have a very good resistance over time, the glue line must be transparent or not, have the lowest possible emissions, etc. There are different types of adhesives, each with their own strengths and characteristics, and the choice must be made so that the glued object looks and behaves as well as possible over time.
PVA adhesives are used for bonding solid wood panels. These are aqueous dispersions of polyvinyl acetate that react (bond) when the water evaporates and the molecules come together. There are several types of PVA adhesives and those used to make solid wood panels must meet certain conditions. Here are the most important ones:
1. Moisture and water resistance
It is very important because the panels may end up being used to make furniture that sits in a steamy area (bathroom, kitchen) or outdoors and the glue line may be affected. This is why it is recommended to use D3 or D4 type adhesives for increased moisture resistance.
If you have a personal project, you can use D1 or D2 adhesives only if you know for sure that the object will never be in an area with high humidity.
Classification of adhesives in terms of moisture resistance (D1-D4) has been extensively covered in a separate article.
2. Transparency of the adhesive film
A white line between the wooden elements will spoil the appearance of the panel. This is why it is good if the adhesive becomes transparent after curing. The transparency of the film is a sign that the adhesive has not had fillers such as chalk or other such products, which make the product cheaper, but also less elastic and transparent.
3. Film elasticity
A very important feature that reduces production costs. After gluing, the wooden panels are calibrated and sanded before being packed for distribution or used in furniture production. A resilient adhesive offers less resistance during these operations, prolonging the life of the abrasives and tools used. They will last longer and the calibration and sanding will be of good quality. Over time, longer abrasive tool and material life translates into material savings and reduced production costs.
The elasticity of the adhesive film is also important for DIY projects. Even if material saving is not a priority here, the easy removal of the cured adhesive on the panel surface and sanding without continuously changing the sanding paper are arguments in favor of choosing an elastic adhesive.
4. Average setting and hardening time
The adhesive should not harden too quickly, but neither too slowly. A medium reaction time allows time for the adhesive to be absorbed into the wood to make the strongest possible bond. A fast setting, in the case of PVA adhesives, can mean a less resistant bond over time.
Very slow drying is also undesirable as it increases production time and decreases productivity.
Quality panels for IKEA or companies in France and Germany with TISZABOND adhesives
One of the suppliers of PVA adhesives for solid wood panel factories is Szolvegy, Târgu Mureș. TISZABOND adhesives are used to produce quality panels for the domestic market and for export. One of the companies manufacturing solid wood panels with these adhesives is Dippanels, whose products we've already talked about in the magazine.
TISZABOND adhesives recommended for panels are D3, D3D (a D3 adhesive with improved adhesion and elasticity), Winter D3D (freeze-thaw resistant adhesive) and D4 mono and bicomponent. D4 adhesives are used to make panels with very good resistance to moisture and outdoor conditions. We told you about this type of adhesives when we talked about hives or exterior doors.
For Solvegy, the manufacturer of TISZABOND adhesives, the most important aspects are to ensure a high quality product and continuity of quality over time, meeting all the requirements of European standards. Continuous quality can only be ensured with the help of raw material suppliers. They have to put special emphasis on permanent quality control of the materials, thus being the guarantor of the quality of the adhesives.
In addition to the very good relationship with raw material suppliers, Szolvegy also has a close relationship with renowned European laboratories, with the TISZABOND range of adhesives being certified at both the Rosenheim Institute in Germany and the Wood Institute in Sopron, Hungary. Quality tests and quality continuity control are proof that TISZABOND class adhesives meet the requirements of European standards, giving partners in the wood industry the assurance that their products, bonded with TISZABOND adhesives, will also be high quality products.
Szolvegy prides itself on the very high quality of its adhesives, proven by laboratory tests carried out at the above-mentioned institutes. The director of the company told us that samples of adhesive and wood glued with TISZABOND adhesive are regularly taken for testing, even without the beneficiary asking for it. This is the way in which the quality of the products is constantly checked, so that the customer has proof of the continuing quality of the adhesives used.
I hope you find this information useful, whether you work in industry or have a personal project in the pipeline. If you think it could be useful to others, please feel free to share. If you have any comments or questions, you can leave them below in the dedicated space.
Add comment