Large furniture manufacturers are continually faced with a demanding external market that is demanding ever lower prices, a market they have to take into account if they want to stay in the game. Many are choosing the right path - re-engineering - for both woodworking and furniture finishing. Finishing lines with automatic spray guns ensure consistent film quality, reduce waste and labor costs. But continued price pressure is also seen in negotiations for ancillary materials, with varnishes and paints directly targeted. And so some economical products are coming on the market to make equally beautiful and durable films. But spray guns on automatic lines break down much faster. Why? I try to answer this question below.
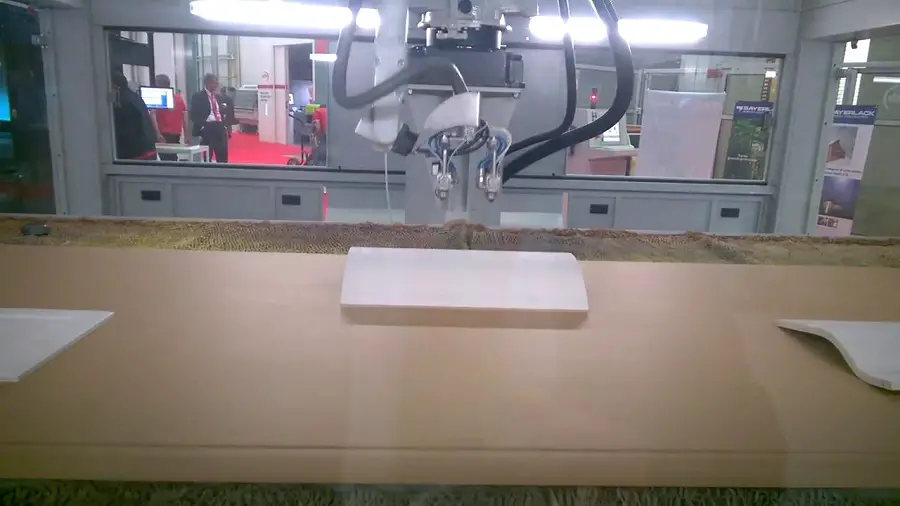
Finishing material changes affecting spray gun parameters
It's hard to understand what happens when all of a sudden gun nozzles and rods suddenly fail more often than at other times and need to be replaced for quality production. As nothing seems to have changed in the meantime, the conclusion is that the guns are to blame. Sometimes it can be the primer or lacquer used. Even if the product remains the same, the raw materials included can be changed.
Price pressure is driving varnish and paint manufacturers to find cheaper raw materials. In good faith, they want to preserve the final quality of the film and its mechanical and physico-chemical resistance. A finishing product is composed of resins which determine its basic properties (acrylic, ureic, ester), solvents, auxiliary materials which determine certain properties (stretching, thixotropy) and fillers. In order not to alter the basic properties of the product, the only materials that can be substituted or modified are the fillers.
Such modifications, which do not require changing the product name or code, are mostly made to white or colored waterborne primers and paints. Talc, chalk or other fillers can be replaced by similar, cheaper materials. The main qualities of the product do not change. But the granules of the new fillers may be harder, more abrasive. This leads to changes in the nozzle parameters of spray guns, especially those working in the Airmix system, and other component parts that come into direct contact with the finishing products.
As a result, the guns in use will suffer more if they are not made of durable materials. Spray gun and spray equipment manufacturers have adapted to the new conditions and are producing special, stronger guns for waterborne primers and white waterborne paints. Automatic airless spray guns ASI 24 and ASI 40 from Sames Kremlin are such products.
Sames Kremlin spray guns with increased resistance
ASI 24 and ASI 40 are spray guns recommended for the application of hard and/or abrasive materials. You can also find them in the country from the French company's distributor, Falk Consulting. The main advantages of these guns are:
- Simple construction with a small number of components;
- durability;
- low maintenance cost,
- compact and lightweight;
- clean and easy to change.
Works in Airless system making them very suitable for factories where high productivity is needed. Spray atomization is very fine and the material flow continuous and constant. The result is a good quality film even if the applied product is hard or abrasive.
The strength of the gun is given by the use of steel for the inner passages, nozzle and rods treated to resist abrasion. The rod tip that closes the nozzle orifice is made of nickel carbide, ensuring jet consistency even when using harsh products such as UV or waterborne primers with abrasive fillers. The nozzle is mounted directly on the gun diaphragm, without any other intermediate parts.
Such a spray gun, even if it may seem expensive at first, is a good investment because it ensures long use with consistent film quality. Gun nozzle failure at high flow rates and a finishing line travel speed of a few meters per minute means a large number of broken parts. And if this happens often, it means large losses of material and time. That's why I think the philosophy of the Englishman who says he's too poor to buy a cheap coat fits very well in industry. By approaching things in this way there is a real chance of being able to lower production costs and enter the foreign furniture market at competitive prices.
Add comment