Loss of material is one of the main problems of spray application of finishing materials. This loss is not only the actual cost of the varnish that no longer gets on the wood but also the cost of exhaustion to remove finishing materials and diluents from the working environment. As these costs are far from small, manufacturers of equipment and spray guns are continually improving their products so that losses are kept to a minimum.
Spraying systems with the best material transfer
Although one might think that only for very expensive pumps or automated spraying lines there are guns that have very good material transfer, this is not the case. There are also manual guns that reduce losses. What is important is how the gun works and the technology it is built for.
Spray guns known for low material loss are:
- HVLP
- electrostatic guns
- airless guns
For each of these types of spray guns there is a specific way of transferring material to the object to be finished so that losses are minimised. Let's take them one by one.
HVLP or High Volume Low Pressure
This type of spraying is actually a modified conventional spraying. In conventional spraying the material is pushed through the nozzle of the gun by compressed air with a pressure of 3-5 bar. As it leaves the gun, a cloud of fine particles is created, of which only a small part reaches the object, the rest being that "overspray" you have probably heard of, i.e. losses. The loss of material increases with increasing pressure, and below 2.5 bar pressure you no longer get uniform films. In conventional spraying losses can be as high as 75%.
HVLP gunsare modified so that the material can be sprayed at a low pressure of up to 0.7 bar. The applied material must have a lower viscosity than conventional spraying, which results in the use of a large amount of thinner. Losses are reduced, the film obtained is uniform and of good quality, but productivity is low.
It is a type of gun suitable for occasional finishing in a workshop where there is not a high volume of work. Note that you will need a larger quantity of thinner.
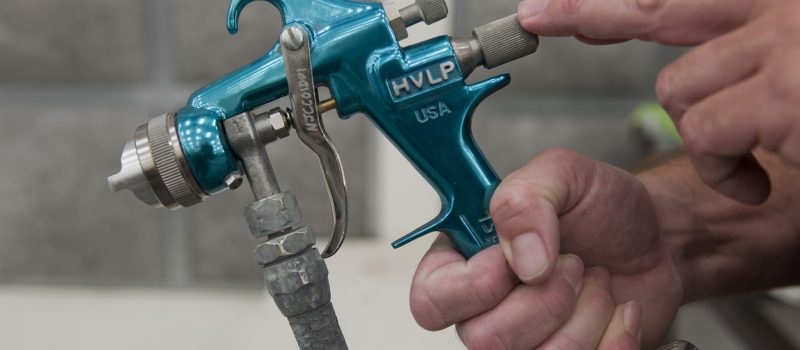
Electrostatic spraying
Electrostatic field spraying is based on the movement of fine lacquer particles along the lines of an electromagnetic field formed between the negatively charged gun and the positively charged wooden object. The electrically charged lacquer particles are attracted to the object along the lines of force of this field, yield the electric charge and are retained on the surface. The object is earthed so that the electric charge is discharged into the earth and there is no danger of electrocution.
For optimum electrostatic effect the wood humidity should be 10-12% and the air humidity no lower than 60-70%. It is known that wood is not a very good conductor of electricity. To increase its conductivity it can be treated with saline solutions or kept for a short period in special steam rooms.
When using electrostatic spray guns to apply finishing materials consumption is reduced by 50 to 80% compared to conventional spraying. Due to the electric charge, even if the spraying is done from the front of the object, the particles also settle on the back of the object and are attracted by the electromagnetic field formed.
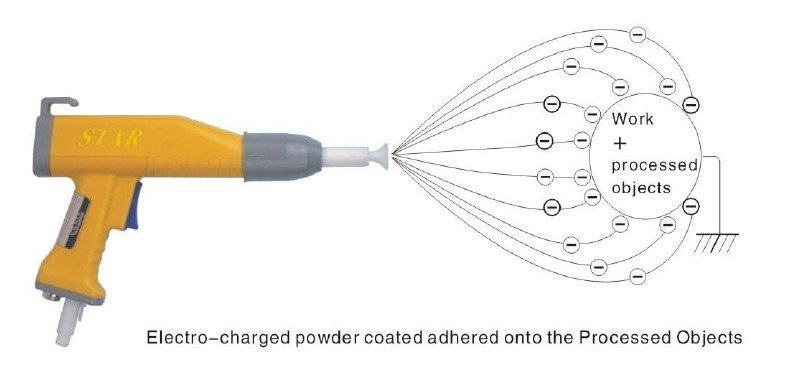
Airless spraying
Airless spraying is also called high-pressure spraying. The principle of operation is as follows: using a high-pressure pump, the material is pushed (without the aid of compressed air) and forced through a special nozzle. The pressure at the nozzle inlet reaches 90-360 bar. The nozzle atomises the spray to be sprayed and the jet exits without being forced by compressed air and unmixed with air.
It is a very suitable system for factories and comes with many advantages:
- high productivity,
- possibility to use high viscosity coating materials,
- reduction of material losses,
- material transfer efficiency
The disadvantage is that, as part of the system that makes airless spraying possible, the nozzle is fixed and the width of the jet cannot be adjusted. In order to change the spray pattern the nozzle has to be changed. For a spray line or for high throughput applications, where the parameters are fixed from the start and remain unchanged for a long time, this disadvantage is not very important.
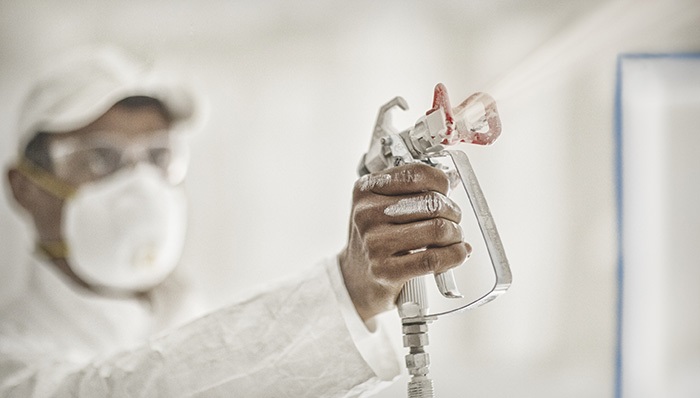
An airless gun you might be interested in
It is known that it is not possible to achieve a very high quality of finished surfaces with airless guns. However Sames Kremlin managed to overcome this problem with the airless gun SFLOW™ 275 & 450. The special nozzle atomises the material very well, resulting in very high quality finished surfaces. The gun also has a very good material transfer efficiency up to 81%.
In addition the gun is reliable and durable, with an ergonomic design that allows a very comfortable grip. Designed specifically for high productivity manual application, it is easy to handle and the trigger is not tiring for the finger, and can be operated with 2 or 4 fingers.
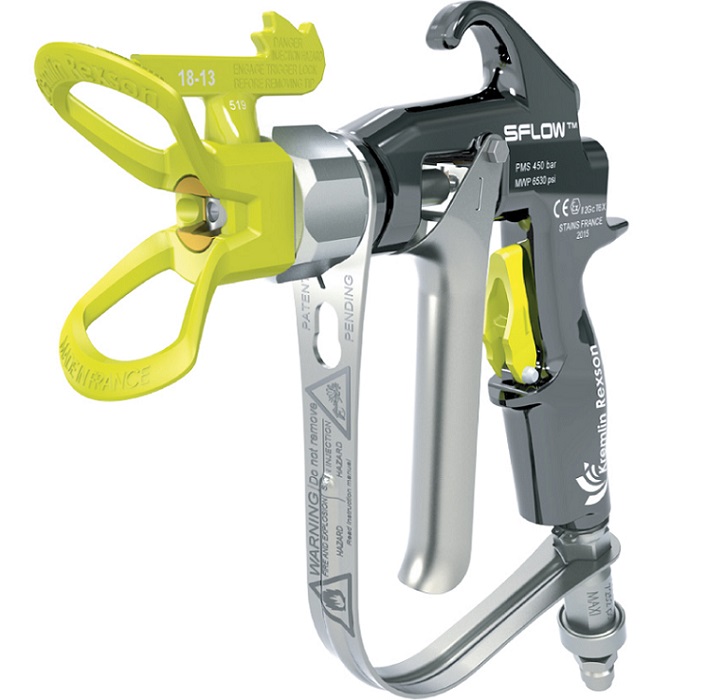
If you want to reduce material loss, get a quality film and have high productivity you can see the gun as an alternative. Find it at Falk Consulting, the distributor of Sames Kremlin in Romania.
Add comment