Chair manufacturing is a special field of the furniture industry. The complexity of the product, its strength, design and comfort requirements, its particularities make it very difficult to combine the production of chairs with other pieces of furniture. As a result, there are factories where the machinery, flow and technologies are dedicated to manufacture of chairs and there are machine manufacturers who have perfected their machines. One of the best known is Bacci, represented in Romania by Ligna Dumi Techin Brasov. The specific technology developed by the Italian company over the years, the innovations and the international patents obtained have made Bacci a reference name in the field of seat manufacturing machinery.
A long-established name in industrial chair manufacturing
For those curious to find out who Bacci is, the firm introduces itself simply:
- 100% Italian company with 4 generations
- a world leader in the production of 5 and multi-axis CNCs
- over 50 international patents
- over 4000 CNCs sold worldwide.
It all began in 1918, after the First World War, when Paolino Bacci started the production of band saws to equip the workshops in the Cascina area (Pisa), where the company is still based. In 1950 Giuseppe, Paolino's son, took over the management of the company, which specialized in solid woodworking machinery, and started to manufacture machines for the production of chairs. This was the period when Italy was specializing in this field, becoming a major player on the international market. Constant contact with chair manufacturers enabled the development of high-performance technologies and the production of reliable, sturdy and precise machines.
In 1986 Bacci became the first Italian company to win the IWF USA (International Woodworking Fair, Atlanta) award, and in 1995 it produced the first 5-axis CNC with multiple outputs. From this point on, the company began to develop ever more complex and high-performance machines, continually perfecting CNCs for the chair manufacturing sector and other sectors of the furniture industry.
Innovations have taken CNC seat manufacturing to a new level
What makes the Bacci name a benchmark in woodworking machinery is continuous innovation. Machines capable of simultaneous machining with the same precision and safety have been developed from innovative ideas that have led to international patents. Perfection has also extended to other areas - machines for making sofas, sports equipment, musical instruments, stairs, door-windows - but chairs remain the reference area.
Modern chairs are not as simple as classic chairs. Moulded plywood allows the production of chairs with one-piece seat and backrest or atypical, flowing shapes. For continuous machining and to avoid moving the workpiece, the CNC has to have several machining axes and special clamping systems. Additional machining axes, in addition to the 5 axes of the spindle, are those provided by the worktable (in the X and Y axes) and by the rotation of the workpiece around its own axis. In this way, operations such as drilling, milling, planing, decorative milling, and making joints between elements can be carried out in a single step.
Multi-axis machining is not enough. You also need a fixture that is capable of both safety and mobility. Such a fixture is free jig device and is BACCI patented. The tweezers can move in space so that all machining can be carried out on all 6 sides of the wood piece. And when some machining cannot be done on one of the faces, the system allows the devices to hand over to each other the workpiece to be machined on all faces (360°).
Another Bacci patent - tool change on spindle. The manufacture of seat components is complex and requires a large number of tools to perform all operations. In 1995 Bacci patented the 5-axis CNC with multiple electrospindles on the same workhead, which allows the assembly of 2, 3 or 4 basic tools, machining without changing the tool. This reduced downtime while increasing productivity.
Another milestone in Bacci's journey was in 1998 when it became the first company in the world to produce a 5-axis CNC with two heads. With this type of CNC, both ends of a wooden part can be machined simultaneously. All these innovations were possible thanks to the anti-collision software PITAGORA which allows the management of working heads and movements of all independent axes (5) and interpolated axes (6-12). The program has special functions that allow reducing working times by up to 50%. But about Pitagora software and its performance, at length in another article.
Bacci classic machines for small and medium workshops and factories
Although Bacci means CNC technology and state-of-the-art machinery for young people working in the seating industry, the old-timers have not forgotten the machines for hollowing and chiseling, copy milling or tooth jointing that they were working with 40-50 years ago. The company has a special division that still produces classic machines for small and medium-sized workshops and factories. The sturdy, reliable and precise machines, with cast-iron beams and hardened steel drive elements as in the past, now have state-of-the-art electronics and pneumatics.
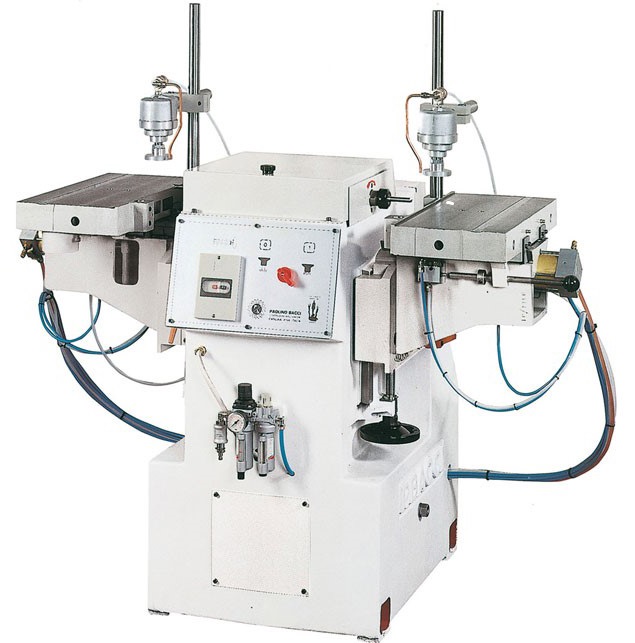
Bacci machines are not new to the Romanian market. Ligna Dumi Tech specialists still meet old craftsmen at trade fairs who fondly remember the Bacci machines they worked on. There are now over 350 new BACCI machines in the country, including 150 CNCs. Customers include Ligna Dumi Tech, Bacci's representative in Romania, include renowned names in the field of seating manufacturing: Plimob, Aviva, Becker, Sortilemn, Iris, ITA Production, Laguna.
We plan to return to Bacci machines and innovations in future articles. The important changes in the field of chair manufacturing made with their help deserve to be emphasized and deepened.
Add comment