Another finishing defect is uneven surface gloss. For example, a table top or a cupboard door that shines more on one side and less on the other. Find out why these problems occur below.
What is gloss
The degree of brightness of a lake shows how much of the light radiation is reflected and translates into how bright the lake is - bright, dim or not bright at all. Small variations in gloss are hardly visible to the naked eye. They can only be determined with the help of machines. But they're not what's annoying. The big problems arise when different degrees of gloss are visible on the finished piece of wood, or when the customer has ordered a matt piece of furniture and receives a glossy one, or vice versa.
Degree of gloss expresses the extent to which a finished surface reflects light. Depending on the amount of reflected radiation, surfaces can be divided into matt and glossy. This property is practically transferred to the finished surface by the applied topcoat, which has its gloss level specified in the product code and in the technical data sheet. The gloss is measured with a glossmeter.
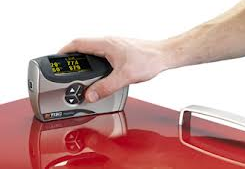
Why we have different gloss even if we used varnish from the same can
Differences in gloss can occur for several reasons.
Surface preparation before varnishing is one of the causes. The degree of gloss mentioned in the technical data sheet is determined on a sample of varnish applied on a piece of glass. To achieve the same gloss, the surface must be as flat as possible, without any unevenness or roughness. A sufficient amount of primer is needed to ensure that the sanding between coats is as smooth as possible. It is therefore recommended to apply at least two coats of primer. This amount of sanding will allow proper sanding, resulting in a flat surface which removes any unevenness and imperfections in the wood left after sanding. white grinding.
Gloss variations also occur if material is applied in different quantities. With spray applications, for example, spraying twice over the same area increases the amount of material applied to that spot and the surface will no longer be perfectly flat. The finished surface will have varying degrees of gloss, and for a glossy surface this means a distorted reflection of images.
Mix the material very well in the canister before use is another condition for no gloss variation. The gloss of a varnish is obtained by adding a quantity of very fine particles that reflect light to the base resin. The generic name for these particles is matting or matting agent and depending on the amount added, the varnish is glossier or matt. The matting agent is heavier than the resin and settles over time. If the can of varnish is not thoroughly mixed before application, then there will be a difference in gloss between the furniture to which the varnish has been applied at the beginning of the can and the furniture with the material at the bottom of the can.
Type of diluent used is very important when it comes to gloss. I was saying that in order to reflect the radiation well, the varnish needs to be as flat as possible. If the varnish doesn't spread out very well, it appears orange peelă and influence the gloss. Always use the thinner recommended for the type of varnish and the conditions in the application room (temperature, humidity). A thinner that evaporates quickly does not allow time for the varnish to set to reflect the light properly.
When using two-component products such as polyurethanes, use of another catalyst than recommended may result in a change in gloss. In general, if you add polyurethane catalyst over polyurethane varnish, the resulting mixture should harden. The proportion added and the formulation of each part influence the curing time, film hardness, film elasticity and gloss. There are catalysts that can also change gloss by 20-25 units.
Large temperature variations may lead to changes in gloss. Determination of the gloss level mentioned in the technical data sheet is done in the laboratory at a temperature of 20°C. At too low a temperature the varnish cannot relax, and at too high a temperature the varnish and primer become very fluid and do not provide the necessary loading for proper radiation reflection. In addition, the lake, the wood substrate and the environment must have approximately the same temperature.
Workspace dust can change the gloss, especially in the case of glossy varnishes. They should be applied in the cleanest possible rooms, preferably pressurized spray booths or stapled finishing lines.
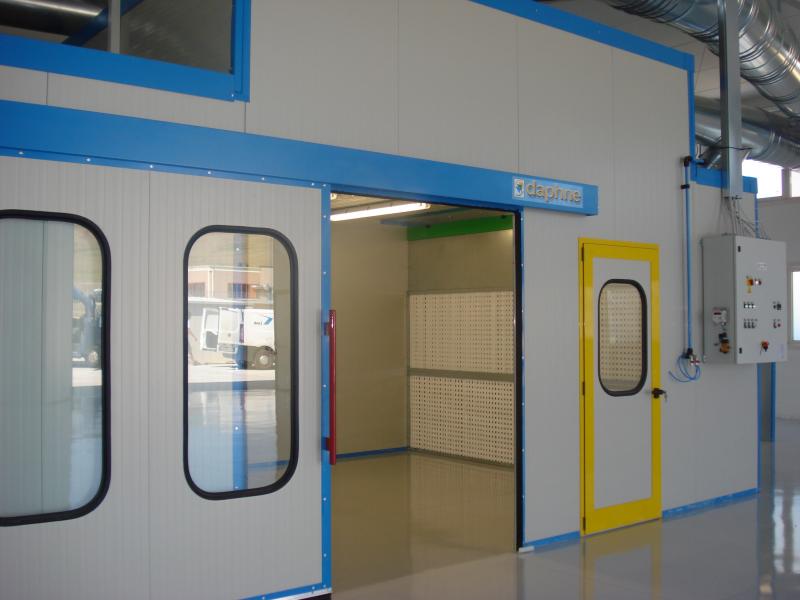
When variations in gloss are observed, it is advisable to first check that all of the above recommendations have been followed and then, if the defect persists, contact the manufacturer.
Cycle Finishing defects also presents other problems that occur on finished surfaces.
I hope you find the above information useful. As always, additions are welcome. And if you have any questions or queries, please leave them below in the space provided. I will be sure to reply
[...] used. If they are followed, quality finishes can be achieved. Omitting them leads to finishing defects, and remedying them means additional consumption of materials and labour, i.e. costs [...]