In the early days of furniture finishing, the products used were only solvent-based. The first varnish used -shellac - was obtained by dissolving the resin secreted by the female Kerria lacca beetle in alcohol. Over time, natural products were replaced by more diverse, resistant and better performing industrially produced materials. But the solvents used have multiplied. Despite their very good quality, the environmental problems created by solvent emissions and the danger of fire mean that alternative solutions must be found. This has led to the development of water-soluble products with similar qualities and the gradual replacement of traditional solvent-based products.
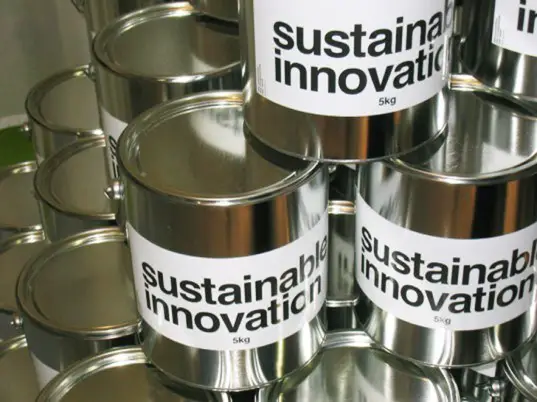
Research has led to high-performance water soluble products
As environmental concerns have become increasingly pressing, varnish and paint manufacturers have been forced to reduce production of solvent-based materials and increase production of water-based products. All users of such products have also been obliged to monitor solvent evaporation, i.e. the emission of volatile organic compounds (VOCs), and to reduce these emissions over time. Furniture manufacturers need to find solutions, one of which is to replace solvent-based materials with water-based (water-dilutable) ones.
What scares manufacturers the most when it comes to switching to waterborne finishes is the drying time and the fact that the water in the product lifts the wood grain, making the sanding process more difficult. It is no longer necessary to worry about this because the products have changed so much.
Manufacturers of such materials have stepped up their research by greatly reducing drying times. Thus, the drying of water-based products has in many cases become comparable to similar solvent-based products. Solutions have been found to reduce absorption into the wood so that less wood fibre is raised and sanding between layers is no longer a problem.
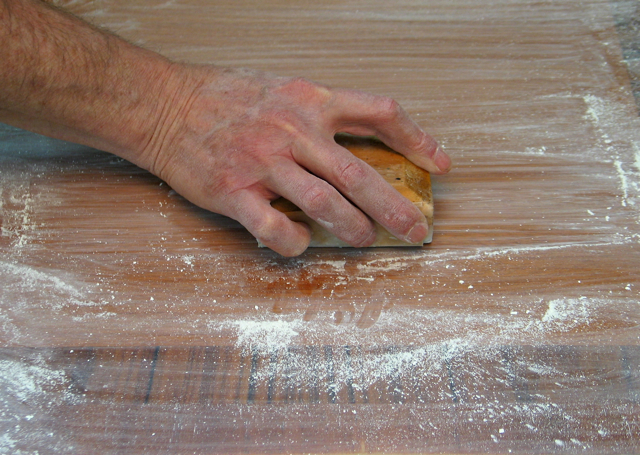
There are solutions for both baths and varnishes and paints
Both staining solutions and film-forming materials can be replaced. Water-based stains have long been used to stain wood. Originally they were powders of dyes dissolved in water. The varnishes were made in the factory before they were applied, so that there was no risk of spoilage from micro-organisms in the water. It was an unpleasant process (the powders flew through the air and were inhaled), and the stains dried quite slowly, with water as the only solvent.
Nowadays, there is a lot of use of baths made from concentrated solutions of dyes dissolved in mixtures of resins and water. The resins used prevent deep absorption and accelerate drying.
Film-forming materials (nitro, polyurethane, acrylic, etc.) can also be replaced by mono- or bi-component waterborne products. The application method is very similar to solvent-based products and the resulting films have a very good appearance and resistance.
Virtually all varnish and paint manufacturers can now offer waterborne versions for any finish. There are materials for finishing flooring, garden furniture or other outdoor furniture, there are water-thinnable oils and waxes, antiquing patinas, special effects, etc. Solid wood or veneered panels, MDF or HDF can be finished.
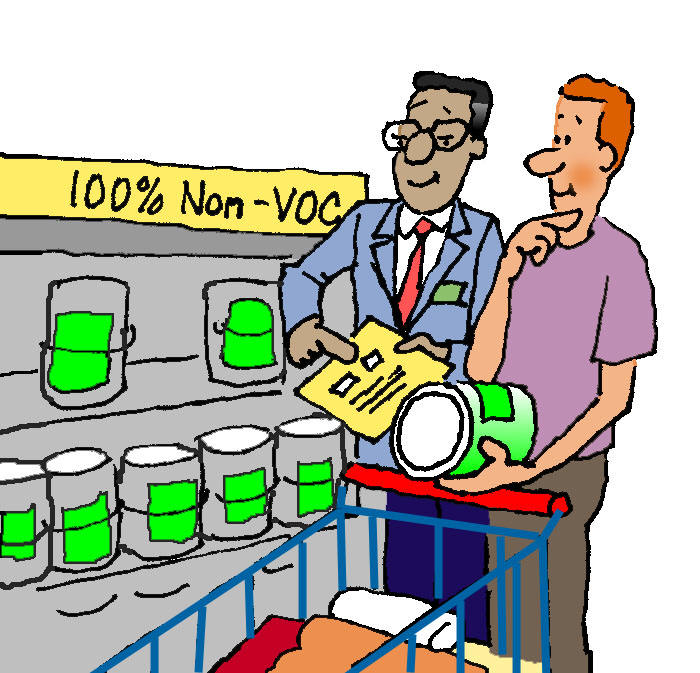
The application of waterborne products can be adapted to all technologies
Waterborne materials can be applied by spraying, pouring, pouring, flow-coating or by hand with a brush, sponge or roller.
When there are finishing lines, changing products is more complicated but not impossible. Often it is not possible to use the same finishing line and some adaptations or component changes are necessary. But together with the supplier of the finishing line and the supplier of varnishes and paints solutions can be identified.
In the case of manual finishing things are simpler. The first requirement is a stainless steel application gun or pump. There must also be a heated and well-ventilated drying area. Ventilation is a very important condition when finishing with waterborne products, even more important than a higher temperature.
The point to remember is that waterborne finishing doesn't always mean organic or ecological finishing. It solves the problem of fire protection and emissions of volatile organic compounds, but it does not necessarily solve other environmental or personal protection problems. For that, you need to study the safety data sheets of the products, which indicate the hazardous components and possible risks.
I hope you find the above information useful. As usual, additions are welcome. And if you have any questions or queries, please leave them in the space below. I'm sure I'll reply.
Add comment