Why doesn't the finish come out even though I use good finishing products? Because there are several aspects to consider to achieve a quality finish. For example, conditions in the working environment are very important. It's not enough just to use very good materials and follow the application technologies. You must also have the necessary working conditions to achieve quality finishes.
Dust, the enemy of a gloss finish
Finishing should be done in specially designated areas away from sources of dust. Praful in production and grinding areas is the enemy of the finish.
According to the working technologies, after application, film-forming materials need drying time to become a film. This drying time has several stages: drying to dust, drying to print, drying to sanding, drying for packaging.
The dust drying time is the time during which the film dries superficially. If there is dust in the area during this time, the dust will settle and become embedded in the film. The higher the gloss of the varnish, the more visible the impurities in the film. The dust embedded in the final varnish layer causes the film's texture to change and become rough.
Influence of temperature on film quality
Temperature is another factor to consider for a quality finish. Product data sheets recommend that the temperature in the finishing area should be 18-20°C. Slight variations from these temperatures are acceptable, but it is very difficult to achieve a perfect finish if, for example, working at 8-10°C in winter or 38-40°C in summer. If the temperature is very low, the viscosity of the varnish will increase. When applying, the varnish will be thinned with a higher percentage of solvent. When it dries, there will be less material left on the board, so a thinner film will result. Low temperature also leads to decreased adhesion to the substrate. If the temperature is high, the thinner will evaporate very quickly, the film will be rough with air bubbles embedded in it or will have the appearance of orange peel.
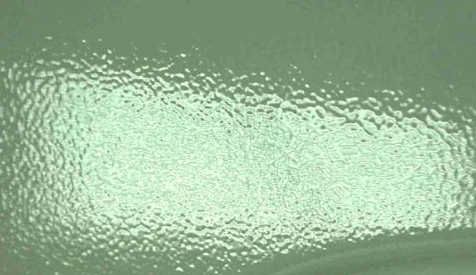
It is good practice to keep the ambient temperature, the temperature of the finishing materials and the temperature of the wood substrate the same or within a narrow range during the work.
Workspace ventilation
Other factors influencing the quality of the finish are ventilation in the finishing area and exhaustion. Ventilation is especially important when using water-based products. Lack of it leads to increased drying time and sometimes to a milky appearance of the film due to the inability of the water to evaporate completely. Dewatering ensures that the work is carried out in a clean and safe environment, with the effect of improving the quality of the finish.
Polishing needed to achieve a very high gloss
The influence of the working environment is best seen in the gloss finish. High-gloss or mirror-gloss finishis the one made with varnish with a gloss above 95. It is often necessary to polish afterwards to achieve the desired gloss (polishing) of the lacquer film. This is done with abrasive pastes. Polishing removes dust or other impurities trapped in the film, small bumps, scratches or orange peel. In this way, the reflection of light is perfect and the gloss is of the highest quality. Polishing can sometimes dramatically increase the gloss.
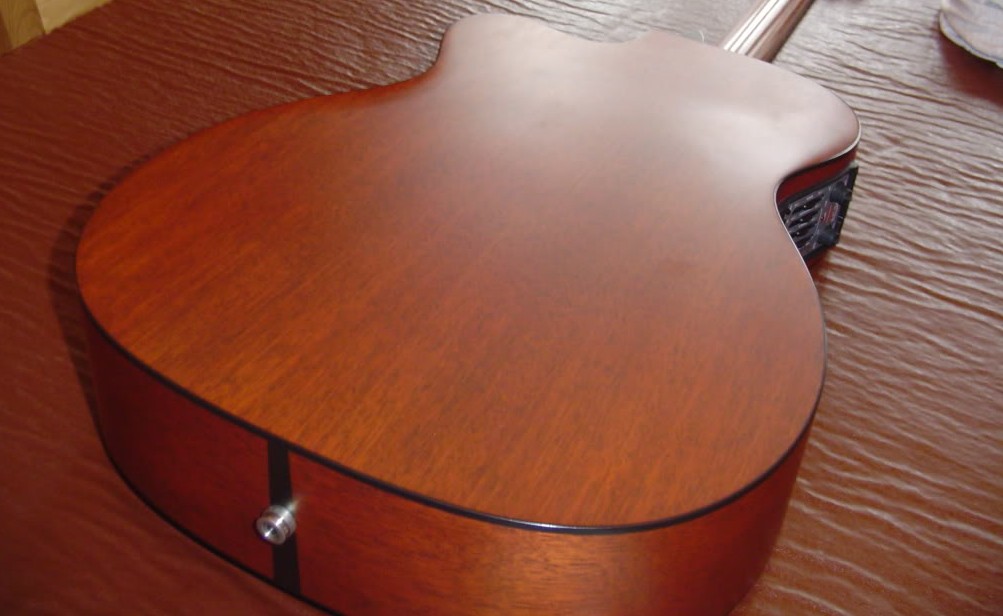
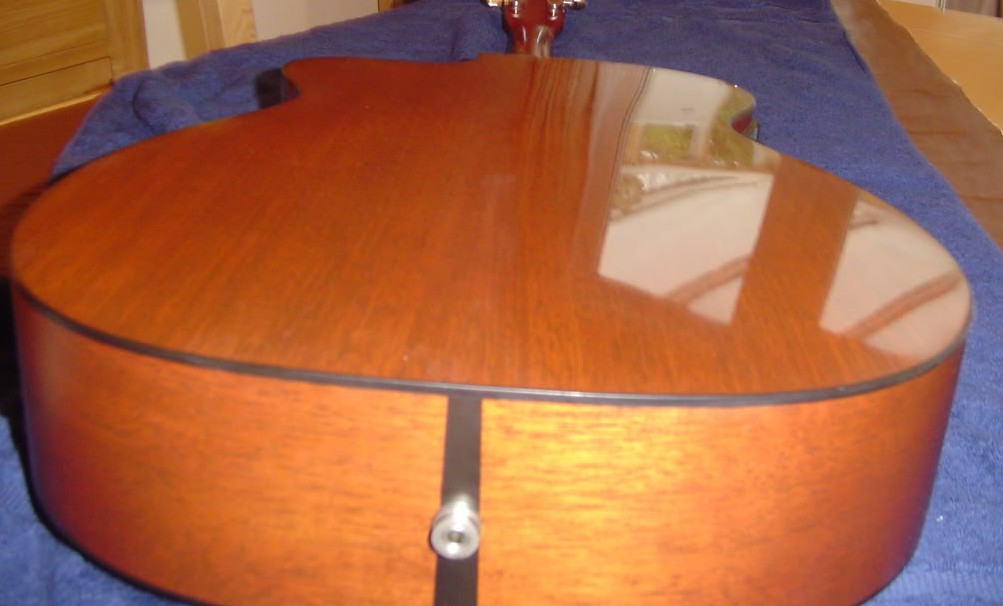
In connection with this operation, I learned from the technical director of a musical instrument factory that he was able to raise the luster of a guitar from 65-68 to 95 just by polishing.
It's all very well to use quality products, but don't expect them to work wonders. They are only part of the finishing process. For a quality finish, attention must also be paid to the working environment, the plant and machinery used and the way people do their jobs.
I would be glad if you could tell me what "unexplained" problems you had during the finishing. Maybe, together, we can find the explanations.
[...] Also good to read about ... https://revistadinlemn.ro/2016/03/15/situatii-cand-lacul-chiar-nu-are-nicio-vina/ [...]
[...] on the quality of the finish . More information on the influence of environmental factors can be found here. This time I want to draw attention to some defects that appear long before the [...]
Hello,
I varnished the parquet in a room following all the necessary steps, operation completed with the application of varnish in two coats with intermediate sanding. The first coat was applied with a brush and the second with a varnish trowel. Unfortunately the gloss is not as expected and in some places it has an orange peel appearance (where the trafaletti has overlapped). Please let me know how I can correct it and how - and with what - the surface can be polished for a higher gloss.
Thank you,
Sandu
Hello,
The degree of gloss is also influenced by this orange peel. This appearance of the film is due to too thick a layer of varnish. I think it should have been thinned more. All the more so as it is more visible where the coats have overlapped (I'm sure the varnish is a bit thickened in the areas where the coats haven't overlapped, but it's not so visible). To make it glossier you first need to remove the orange peel, then buff. Basically, you have to sand first with 600-800 grit paper, then polish with abrasive pastes with a grit larger than 1000 (2000-4000). There are several companies selling such pastes. (3M for example). Sanding and polishing should be done mechanically. It is impossible to obtain a constant gloss on the whole floor by hand.